The U.S. fuel and petrochemical industries have a long history of stepping up and innovating to meet our country’s needs. In World War II refiners transformed production to create the high-octane aviation fuel that enabled the Allies’ air strikes, while the fledgling petrochemical industry produced the synthetic rubber and materials to keep the war effort rolling.
Now these industries are rallying, adapting and innovating to fight to new challenge: the COVID-19 pandemic.
Both the fuel and petrochemical industries are deemed critical by the Department of Homeland Security, since fuel is essential not only to first responders but to the entire economy and petrochemicals are crucial components to N95 masks, personal protective equipment (PPE), and many other public health necessities.
Applying industry expertise to COVID-19 challenges
Several companies are going beyond their existing operations to help meet emerging needs.
ExxonMobil has joined forces with the Global Center for Medical Innovation in a multi-sector effort to design and manufacture reusable PPE such as face shields and masks. ExxonMobil is applying its experience with polymer-based technologies to help facilitate the development and production of a reusable mask that can be sterilized and worn multiple times to alleviate supply shortages and protect frontline health care workers. Once approved by the U.S. Food and Drug Administration and the National Institute for Occupational Safety and Health, the reusable mask and replaceable filtration cartridge will quickly be put into production, with manufacturers expecting to be able to produce as many as 40,000 ready-to-use masks and filter cartridges per hour.
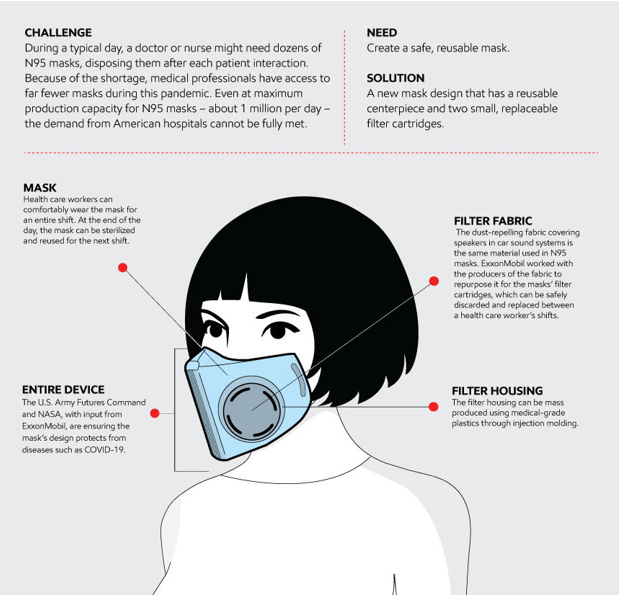
Image from ExxonMobil: Reusable PPE can be sterilized and worn multiple times to alleviate supply shortages and protect frontline health care workers.
A Koch Industries team from Advance Concepts Studios, meanwhile, is working with disinfecting company Violet Defense to rapidly develop a unique solution to destroy the deadly virus using ultraviolet (UV) light. The goal is to deploy mobile UV decontamination units to disinfect PPE at hospitals nationwide, reducing the need to dispose of these in-demand items while ensuring health care workers continue to be protected.
The units – which look like large shipping containers with metal storage racks inside – use pulsed xenon UV lights to disinfect masks, gowns, and eye gear in less than two hours. With the largest model able to disinfect up to 30,000 masks a day, these units have the potential to make a real impact on the PPE shortage while reducing medical waste.
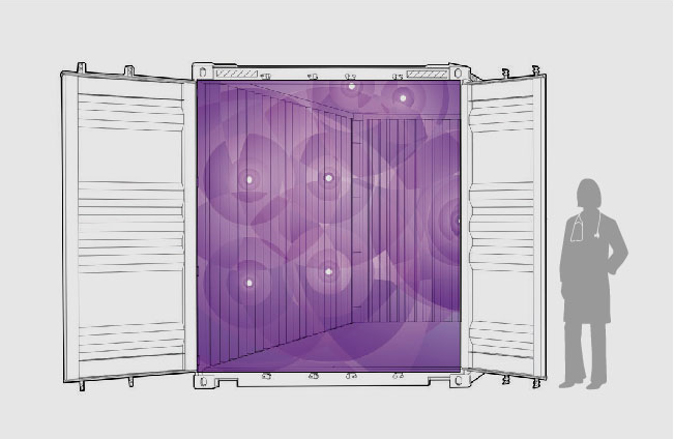
Image from Koch Industries: Mobile ultraviolet decontamination units are being developed for deployment to hospitals across the country.
“We’re helping design these units to be more easily manufacturable, more user-friendly, and more easily scalable across the country and beyond,” said Eric Peterson, leader of growth strategies with Advance Concepts. "To address the critical shortages in PPE right now, we have to look at more than just increasing production. We need to be able to safely re-use what we’ve already got.”
Meanwhile, Suncor is working with scientists to develop a more affordable and scalable COVID-19 antibody test. Suncor’s microalgae technology was originally developed to produce proteins that can break down bacteria in wastewater, but they realized that the technology could be adapted to produce COVID-19 antibodies for serology tests.
“We are using a microalgae that shows a lot of promise for not only producing the protein needed, but producing it with the correct modifications to mimic how it's made in humans,” said Daniel Giguere, PhD candidate at Western University’s Schulich School of Medicine & Dentistry.
Suncor is donating both its technology and the research facilities needed to develop the serology kids, as well as providing funding for the scientists working on the project.
Shifting production to meet emerging needs
Their sophisticated facilities and highly trained workforce are also allowing fuel and petrochemical companies to quickly retool their efforts and produce needed goods such as hand sanitizer.
Valero was able to quickly transform its ethanol plant in Hartley, Iowa, to produce hand sanitizer to help alleviate the supply shortages for health care organizations and first responders. The hand sanitizer, which began being produced in early April, will be used not only in Valero facilities to help protect the health of its workforce but also in local hospitals and emergency care providers.
Similarly, Dow Chemical — which does not usually produce hand sanitizer — is using its expertise and existing supply chains to convert operations in Auburn, Michigan, and South Charleston, West Virginia, to manufacture hand sanitizer. Once at full production, the company expects each facility to produce about 30,000 8-ounce bottles each week. The hand sanitizer will be donated to the State of Michigan, the State of West Virginia, and Great Lakes Bay Region area hospitals and first responders, among others.
BASF is also temporarily producing hand sanitizer at its facilities in Wyandotte and Washington, New Jersey. A team BASF scientists and engineers worked on a compressed timeline to develop and begin production of hand sanitizer at these locations starting in early April. To date, the facilities have produced and donated more than 9,500 gallons of hand sanitizer to New York, New Jersey, Michigan, Texas, Louisiana, Ohio and California.
Exxon’s Baton Rouge and Port Allen facilities have also mobilized to produce and donate up to 160,000 gallons of hand sanitizer, while Honeywell’s Muskegon, Michigan, plant has begun production of hand sanitizer for donation to the Federal Emergency Management Agency (FEMA).
And Chevron-funded Fab Labs — suites of digital fabrication and rapid prototyping machines, including 3-D printers, that are usually used to encourage STEM learning — have found a new purpose. They are now producing PPE for first responders and health organizations in communities near Chevron’s U.S. facilities, with a goal of producing over 20,000 face shields for local hospitals, nursing homes and first responders.
Expanding production to protect health care workers
In addition to working on the creation and production of reusable PPE, ExxonMobil is also ramping up production of key raw materials to protect health care workers. The company increased the production of specialized polypropylene by about 1,000 tonnes per month — enough to make to 200 million medical masks or 20 million gowns. They’ve also increased the production of isopropyl alcohol by 3,000 tonnes per month, which is enough to produce up to 50 million four-ounce bottles of medical-grade hand sanitizer.
INEOS brought its significant engineering expertise and resources to bear in a tremendous logistical accomplishment: in less than 10 days INEOS built two new hand sanitizer plants in Jacksonville, Arkansas and Neville Island, Pennsylvania to provide hand sanitizers to hospitals for free. Each facility will produce 1 million bottles of hand sanitizer each month to help meet the nationwide shortage and protect consumers.
Honeywell is also stepping up to protect health care workers by dramatically expanding its production of N95 face masks. In mid-April, Honeywell announced it had begun production of N95 face masks at its Smithfield, Rhode Island, facility. The masks will go to the U.S. Department of Health and Human Services for the Strategic National Stockpile to support health, safety and emergency response workers. This is in addition to the new Phoenix facility that Honeywell announced will begin producing N95 masks in mid-May. Once both facilities are fully operational, they will produce more than 20 million masks each month.
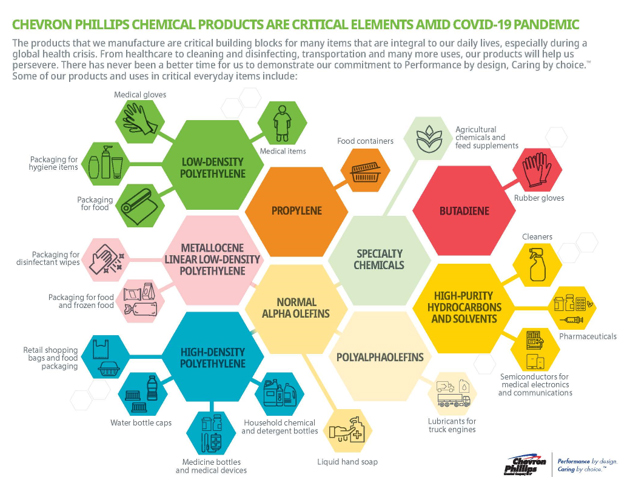
Image from Chevron Phillips Chemical: Chemicals are integral to a range of critical products from medical cleaning solvents to packaging that keeps food protected.
And several petrochemical companies have been increasing production to meet COVID-related needs. For instance, Chevron Phillips Chemical has been working hard to provide in-demand products such as specialty chemicals that go into medical cleaning solvents, the a pharmaceutical intermediate for the Tamiflu medication, polyethylene films and sheeting used to cordon off hospitals and public areas, and resins that create packaging for bleach and hand sanitizer.
Flint Hills Resources employees are producing medical-grade polypropylene for COVID-19 testing kids as well as the expandable polystyrene used to transport the testing kits and other critical therapies to health care professionals.
Once again, the U.S. fuel and petrochemical industries are stepping up, adapting and innovating to meet our country’s needs. COVID-19 will not deter this commitment; on the contrary, it is another opportunity for these industries to continue to make progress.