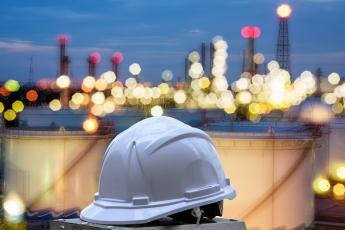
Nearly every gallon of gasoline sold in the United States contains a blendstock known as alkylate. Alkylate is essential in manufacturing the cleanest, high-octane motor gasoline and aviation gasoline capable of satisfying the world’s strictest environmental standards. If new barriers are put in front of alkylate production at U.S. refineries, the consequences could be severe, affecting consumers, U.S. fuel supplies and availability, the viability of U.S. some U.S. refineries, national energy security and prices at the pump.
Here’s what you need to know about alkylate, the catalysts refiners use to produce alkylate (hydrofluoric acid and sulfuric acid) and the steps our industry takes to manage alkylation-specific risks and keep employees, community neighbors and our facilities safe.
What is alkylate?
Alkylate is a blending additive that refiners have used for decades to make gasoline for cars and for small airplanes. Today, about 90% of U.S. refiners have alkylation units that produce alkylate.
Fuel alkylation rapidly expanded in the United States during World War II as the country needed more aviation gasoline to power military aircraft. As vehicle ownership became more common in the decade after the war, demand for alkylate as a component of motor gasoline grew as well.
Why do we need alkylate?
Alkylate is high in octane, low in sulfur and contains zero aromatics. Those characteristics allow refiners to produce gasoline that will help lower vehicle emissions. Alkylate also has low measures of fuel volatility and evaporative emissions (low Reid Vapor Pressure), a requirement in parts of the country where smog is a concern. In summary:
- There’s no way to meet California demand for reformulated gasoline (CARBOB) without alkylate.
- Low sulfur gasoline requires alkylate.
- Alkylate is central to manufacturing Clean Air Act Reid Vapor Pressure (RVP)-compliant fuel for parts of the country that fall under those seasonal regulations.
- Internal combustion engine vehicles in the coming years may rely more and more on gasoline that contains alkylate to hit corporate average fuel economy (CAFE) targets or octane standards for mileage efficiency and carbon reduction.
How is alkylate made?
Alkylate is produced in appropriately titled “alkylation units.” Except in a few specific cases, these units use one of two commercially tested and viable catalysts to initiate the chemical reaction that produces alkylate: hydrofluoric acid (HF) or sulfuric acid.
How safe is the alkylation process?
Alkylation can pose risks like any other industrial process, but refiners are able to operate these units safely because of our numerous risk reduction strategies. Refiners have managed alkylation units for decades and are taking steps all the time to implement new safety technologies and industry-recommended practices that will further mitigate risks, specifically, with HF catalyst. In fact, because of the extensive safety and mitigation investments refiners have made around HF alkylation units, the risks pale in comparison to those we assume every day when engaging in routine activities like riding a bike, driving a car and playing with pets. See for yourself.
Based on data from the National Safety Council, actual incident reports and mitigation surveys, the theoretical lifetime odds of sustaining a life-threatening injury from HF alkylation in the United States are roughly 1 in 52 million for the general public and 1 in 144,000 for those who live close to HF alkylation units. We regularly take part in much more “risky” activities.
How do refineries decide on an alkylation catalyst?
Both primary alkylation catalysts—HF and sulfuric acid—account for about half of U.S. alkylate production. The two catalyst technologies are different and present distinct challenges, risks and considerations for facilities which is why catalysts are decided upon in the design phase for each refinery. Refineries are essentially a giant chemistry set. Every part and every process unit needs to be considered in light of the whole facility. There are some refinery process units, such as fluid catalytic cracking (FCC) units, and logistical considerations, such as access to catalyst regeneration units or ability to accept frequent catalyst deliveries, available supply chains, that might make a facility lean toward HF as opposed to sulfuric acid at the outset.
Is hydrofluoric acid safe to use?
With proper management, it can be. HF is a very common industrial chemical, but it requires extremely careful handling by very well-trained teams operating in well-maintained and well-equipped facilities. If those criteria are met, then HF risks can be safely managed.
Beyond its use at fuel refineries, HF is part of the manufacturing process for aluminum cans, soap, zero emission vehicle fuel cells, fluorescent lightbulbs and a wide range of other consumer products. In fact, refiners are responsible for just 2% of HF demand globally while fluorocarbon production for refrigerants and air conditioners accounts for roughly 60%.
Every industry in the United States that uses HF is subject to regulatory oversight from these and other agencies, depending on facility location:
- Environmental Protection Agency (EPA)
- Occupational Safety and Health Administration (OSHA)
- Department of Transportation (DOT)
- Department of Homeland Security (DHS)
- Various state agencies
What specific steps do refiners take to manage hydrofluoric acid safely?
Refiners take safe, reliable operations of HF alkylation units very seriously. In addition to following all government regulations for HF, we’ve developed extensive industry-specific guidance for managing HF in refinery settings. Our engineers and process safety teams are the world’s experts in fuel alkylation. We think a complete understanding of the science behind HF alkylation is essential for safely and effectively managing HF catalyst and alkylation process units.
Since 1992, AFPM members with HF alkylation units have contributed to and followed API Recommended Practice 751 (RP 751). RP 751 is the collaborative product of an industry working group comprising nearly 100 of the top global leaders in HF alkylation science and process safety. The most recent edition of RP 751—its 5th—was released in August 2021 and reflets the newest data, real-world learnings and available safety technologies. It is the most rigorous and exhaustive policy for HF management in existence.
RP 751 provides guidance on incident prevention, detection and containment that is applicable and adaptable for every refinery with an HF unit. It is recognized by OSHA and the U.S. Chemical Safety Board as providing effective guidance for the safe operation of HF alkylation units and management of HF catalyst, for the ultimate purpose of protecting people and the environment.
It is because of RP 751 and its requirements for regular audits and oversight that risk from this HF alkylation is so well managed. There have never been any life-threatening injuries to people in surrounding communities stemming from HF-related incidents at refineries. Wherever incidents have occurred, and emergency procedures have been followed, multiple layers of mitigation technologies have kept people safe. Learnings from those and other incidents are shared and considered for future RP 751 editions—even incidents where HF was not the cause, but rather was present on site when another incident occurred.
Safety is always the number one job at every refinery, and it extends well beyond our own employees and contractors to include our neighbors outside the fence line. It is because of our safe, reliable operations—achieved by adhering to RP 751 and all government regulatory and performance standards for HF and chemical safety—that refiners and American consumers are able to fully enjoy the benefits of alkylate in cleaner, higher octane fuels.
Why can’t refineries switch from HF to sulfuric acid?
Once a refinery chooses a catalyst and builds its alkylation unit for that technology, it cannot quickly or easily swap to the other. HF and sulfuric acid technology are not interchangeable. HF and sulfuric units have completely different designs, footprints and technological requirements.
A study looking at a specific Southern California refinery found the cost to replace its HF unit with a significantly larger sulfuric acid alkylation unit (because more sulfuric catalyst is required to produce the same volume of alkylate) and brand-new sulfuric acid regeneration unit (a requirement for sulfuric alkylation, but not HF alkylation) would approach $1 billion—significantly more than what this facility was valued at in its last sale. This study also concluded that a regional loss of alkylate production and the resulting need to import alkylate would add an additional 26-cents to the price of finished gasoline for Southern California consumers.
Any loss of U.S. alkylate production and potential loss of U.S. refining capacity stemming from prohibitions on the use of HF would likely result in more expensive gasoline and the potential depletion of already-tight U.S. fuel supplies. Alkylate demand wouldn’t go away. But instead of making it ourselves, we’d likely have to import alkylate from other countries that also use HF or sulfuric acid to produce alkylate. This expensive and un-strategic move would have potential to impact U.S. energy and economic security.