In advance of the AFPM Summit, AFPM Vice President of Technical and Safety Programs Lara Swett and Technical Operations Program Leader Alyse Keller talk about one of AFPM’s premier safety programs, Walk the Line.
What is Walk the Line and how did it get started?
Lara Swett: Walk the Line (WTL) is a process safety practice sharing program AFPM launched in 2015 to help prevent open-ended lines and line-up errors at industrial facilities like refineries and petrochemical plants (e.g. instances where accidental product releases may occur because valves and pipes aren't properly sealed or closed within a unit). Industry metrics at the time showed that about 30 percent of process safety events occurred for one of the following reasons: valves or “bleeders” being left open during equipment commissioning, draining, and loading/unloading activities; lapses in operational readiness; and line-up errors. Those mistakes can be avoided, so we took it upon ourselves to address the industry-wide challenge together.
Alyse Keller: At its core, the program reinforces the fundamental responsibility of operators to know with 100 percent certainty where a material will flow between any two points in a process unit. If they don’t, they need to “walk the line.” Through its resource library and industry-wide practice sharing, Walk the Line upholds a culture of consistency where errors are reduced and operators and front-line supervisors are supported in operational discipline and readiness.
Can you walk us through how Walk the Line works?
AK: Walk the Line was developed for industry by industry, which means that all of the tools have been used by a site or company. Even the program itself is based on an initiative spearheaded by Jerry Forest, senior director of process safety at Celanese. We were able to take the basics from that program and add insights and practices from other companies to create a comprehensive toolbox of resources. To date, there are over 94 practices, trainings, exercises, presentations and videos available to Walk the Line participants. And soon, the toolbox will expand to include micro-learning videos on topics like shift handovers, and practice-sharing posters so that regardless of where employees are on site, they’ll see reminders to “walk the line.” When we all share, we all improve.
LS: Through our digital safety portal, members can browse blinded data to evaluate how their process safety record compares with industry peers, and then identify areas for improvement and potential resources to help address their specific needs. A site new to Walk the Line would first evaluate their metrics and identify opportunities for improvement. Then they would look to the Walk the Line toolbox to help fill those gaps. In addition, there is a Walk the Line community where members share their programs and how they got started with others looking to get a program off the ground. In return, many sites add their own tools to the Walk the Line toolbox allowing it to build.
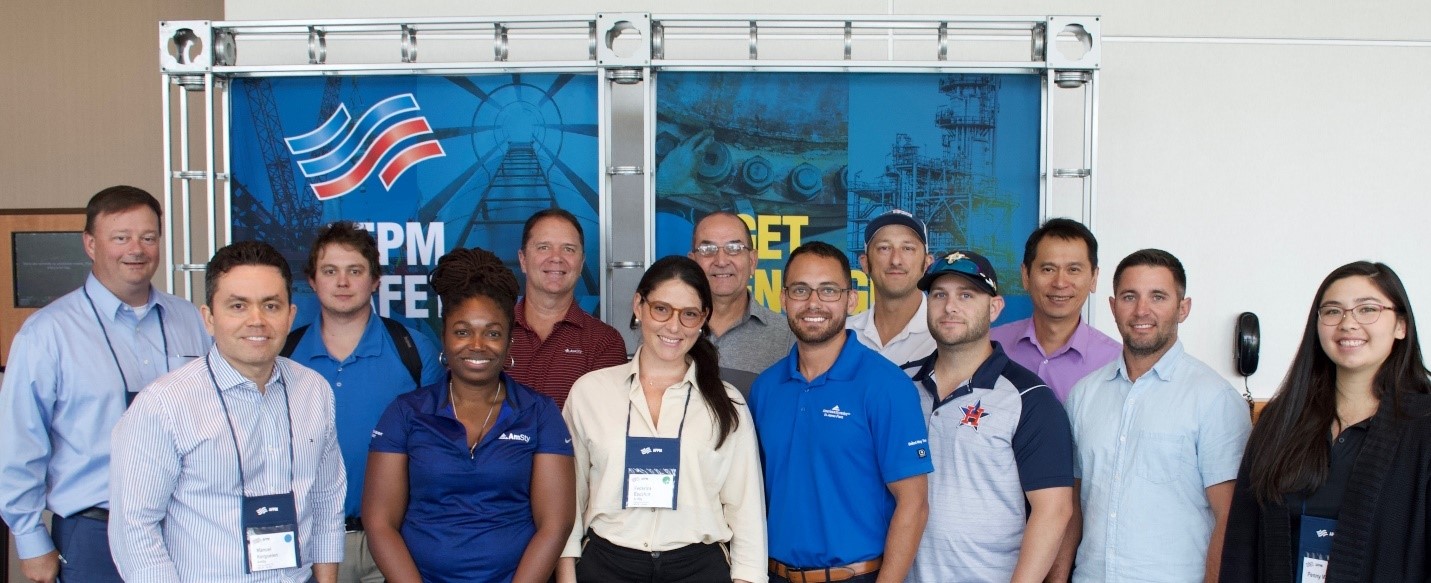
Where would we see Walk the Line recommendations being implemented at a facility?
LS: Let’s talk about line-ups since they’re one of the core operator responsibilities. At a refinery, this basically means adjusting pipes and rerouting feedstocks to introduce different inputs and change product outputs.
Our toolbox contains a variety of resources to help operators know with 100 percent certainty that their line-up is correct and no valves or bleeders have been left open. These tools include practices for a good shift turnover, completing a piping and instrumentation design (P&ID) walkdown, line labeling, and templates for line break tape, management of change (MOC) tags and open bleeder tags to name a few.
AK: Then there’s the operational readiness component that gets to the heart of Walk the Line: the need for clear and concise communication when you are shutting down or starting up a piece of equipment or unit.
Let’s say I’m an operator and you’re a craftsman coming in to conduct maintenance on a piece of equipment in my unit. For you to do your job, I need to prepare the equipment to a state of energy isolation so it’s safe to work on. And then when you’re done, you need to get the equipment back to a state where it’s safe for me to return it to service.
Walk the Line would give us both the tools, communications touchpoints and practices to help ensure that we are in alignment and know with 100 percent certainty where material in the unit is flowing.
What makes Walk the Line different from other safety programs?
LS: Walk the Line is a culture-shift program for fuel and petrochemical manufacturers, and we recognized early on that to have the greatest impact, it needed to be operator-centric and customizable at the company and even site levels. Walk the Line gives participants flexibility along with access to industry data insights and proven educational resources.
AK: This program reflects lessons learned at refining and petrochemical companies across the country. Many of the tools go back to basic disciplines and purpose, training operators how to do certain things and also why those recommendations exist. At the core of Walk the Line is a “Plan, Do, Check, Act” cycle that helps ensure work is done consistently and corrects deviations from intention. The fact that we have boots-on-the-ground operators involved and driving this program really sets it apart. At our workshops, you’ll find operators leading the conversation with their peers, which is a lot more impactful than hearing from a manager or corporate person.
What have you heard from companies using Walk the Line? Does it work?
LS: I can’t stress enough how valuable data sharing is in the manufacturing sector. When we first started Walk the Line and provided members access to our database, one of our members said they would never have been able to develop something like this on their own, with such extensive tools for everyday application. Walk the Line gave them a menu of proven solutions on day one along with a community of industry peer support.
Walk the Line is a tool that not only helps prevent process safety events, it helps companies with product quality control and emissions reductions. Process safety event data shows line-up error events (in yellow below) declined 90 percent from 2014 to 2018. Incidents related to operational readiness and open lines and valves went down 9 percent and 20 percent, respectively.
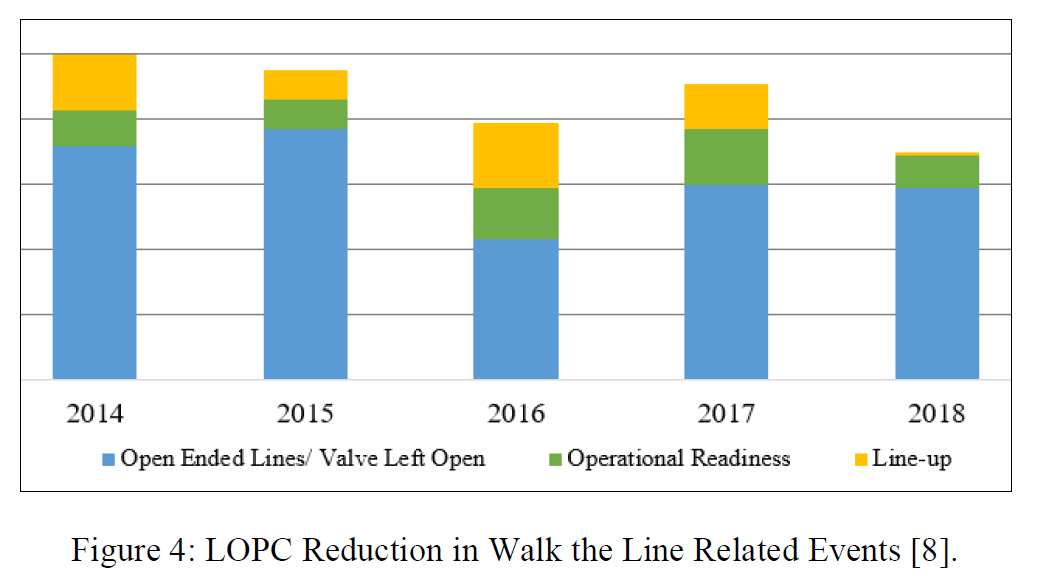
AK: Our industries have very strong safety cultures already and Walk the Line has helped brand that commitment and provide a shared language around process safety. One of our newest Walk the Line sites told us after their introduction to the program that operators on the radio were already reminding each other to “walk the line.”
Walk the Line is also having an impact beyond the downstream refining and petrochemical sectors. Some pipeline and fertilizer companies have joined AFPM specifically because of Walk the Line. Even the upstream International Association of Oil & Gas Producers (IOGP) included Walk the Line as one of its process safety fundamentals after learning about it from a shared member company.
Bottom line: If it wasn’t effective, this many companies would not be using it.
If a company is interested in using Walk the Line, what’s the best way to get started?
Contact Alyse Keller to learn more.