Question 94: What is your experience regarding corrosion of hexmesh anchorage in regenerators using non-phosphate bonded abrasion resistant lining materials?
Tom Lorsbach (UOP)
This is an issue which is continuing to be studied. Since there is no clear link between the lining’s phosphate content and the corrosion rate, the question should be restated to say, “What is your experience using Alternate abrasion resistant lining materials?” In this discussion “Alternate” refers to all abrasion resistant materials being used in FCC regenerators other than Rescobond AA-22 or AA-22S.
The fact that a significant number of full burn regenerators have suffered severe abrasion resistant lining failures in recent years due to under-lining corrosion is not in dispute. The open question is; what is the initiating step that causes destruction of the protective chromium oxide layer of the 304H stainless steel hexmesh anchorage? Once the protective chromium oxide layer of the stainless steel is disrupted other forms of corrosion proceed to rapidly destroy the hexmesh, hexmesh welds and, to varying extents, the underlying base metal.
For the purpose of discussion of under-lining corrosion in FCC regenerators there are two categories of abrasion resistant lining materials used, i.e., Rescobond AA-22S and Alternate abrasion resistant lining materials. AA-22 (and later AA-22S) was the dominant material being used 20+ years ago. Over the past 10-15 years Alternate abrasion resistant lining materials have gained increasing market share and have become the dominant materials used in FCC abrasion resistant linings. This is because some Alternate materials are easier to apply and have better abrasion resistance.
Beginning about 8 years ago there were a couple of cases of catastrophic regenerator lining failures. These were investigated and metallurgical testing was conducted, but no firm conclusions regarding the failure mechanism were reached. The 304H hexmesh corrosion is characterized by its occurrence between the base metal and the underside of the abrasion resistant lining. In many areas where this under-lining corrosion is present the process face of the lining looks unaffected while the hexmesh adjacent to the base metal is badly corroded. In the last several years the frequency of these lining failures seems to be increasing. UOP is aware of at least a dozen instances of this type of regenerator abrasion resistant lining failure. Common factors in these regenerator abrasion resistant lining failures appear to be:
1. use of Alternate refractory materials
2. full burn regeneration
3. elevated feed sulfur - time to failure appears to decrease with increasing feed sulfur (increasing flue gas SOx concentration)
The slide on screen shows both categories of abrasion resistant materials side by side in a new full burn FCC unit. This FCC unit started up in February 2008 and processes virgin HVGO feed containing about 2.5 wt% sulfur. The pictures shown were taken in July 2011 after about 2.5 years of operation. The pictures show Rescobond AA-22S on the exterior of the regenerator combustor riser right next to an Alternate refractory material installed on the exterior of a regenerator second stage cyclone dipleg. The internal refractory linings of the cyclones were also in very poor condition as shown in the second picture.
On the basis of the strong empirical correlation between lining failures and use of Alternate refractory materials and the lack of a clear solution to the problem, UOP has revised its abrasion resistant lining project specifications and now lists only Rescobond AA-22S for use in regenerator abrasion resistant linings. This under-lining corrosion has not been seen at the lower temperature reducing conditions in the reactor and several Alternate materials are cited as approved for use in FCC reactor abrasion resistant linings.
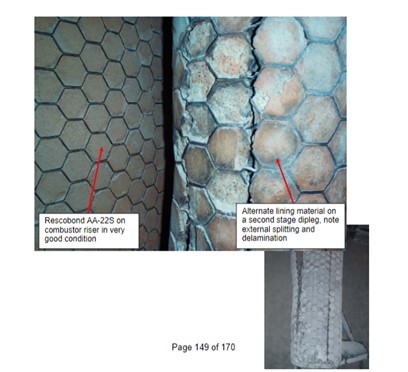
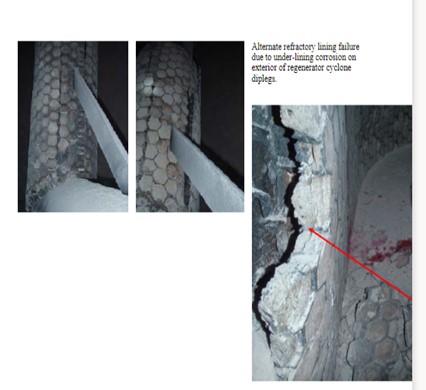
Mike Teders (Valero)
Valero has experienced corrosion of the hex mesh liner in several FCC unit regenerators. We concur with UOP that the flue gas sulfur is a common factor in the hex mesh failures. Valero has active litigation against the makers of refractory that results in the corrosion of hex mesh and I cannot comment on this topic any further.