Question 80: We have coke deposits in the plenum chamber and vapor line and are concerned the deposits may spall off or ignite during refractory dryout. What precautions should be taken to avoid re-igniting these coke deposits during the dryout?
INKIM (PETROTRIN)
We prevent hot air from entering into the reactor system during the regenerator dryout. Subsequently, we will use initial catalyst circulation for the reactor side dryout. Prior to lighting the DFAH (direct fire air heater) for the regenerator refractory dryout, we will introduce dry steam into the reactor, feed distributors, reactor riser, reactor dome, and stripper section. Temperatures in the reactor will be monitored during the dryout period to ensure that there are no excursions which indicate coke burning due to air leakage from the regenerator.
On completion of the regenerator dryout and catalyst loading to the regenerator, we transfer hot catalyst from the regenerator into the reactor to increase the temperature at a rate of 100°F per hour. The temperature in the reactor is monitored closely to ensure that there are no excursions. It is important to note that the reactor pressure should not increase to more than two psi above the regenerator pressure during the catalyst loading, as steam could enter into the regenerator via the regen cat slide valve, which is not a tight shut-off valve. This steam leakage, together with cool catalyst, can lead to mud formation which may be difficult to clear and may hinder catalyst circulation.
BULL (Valero Energy Corporation)
There is no guarantee that the coke will not spall off the refractory linings during startups. If you have any concerns at all, remove any significant coke buildup on the internals. On convex or relatively flat surfaces, there is a very good chance it will spall. In the case of concave surfaces, especially if you are looking at a reactor vapor line of any diameter less than 36 inches, we typically say that if the coke buildup is not very thick, you do not have to remove the coke.
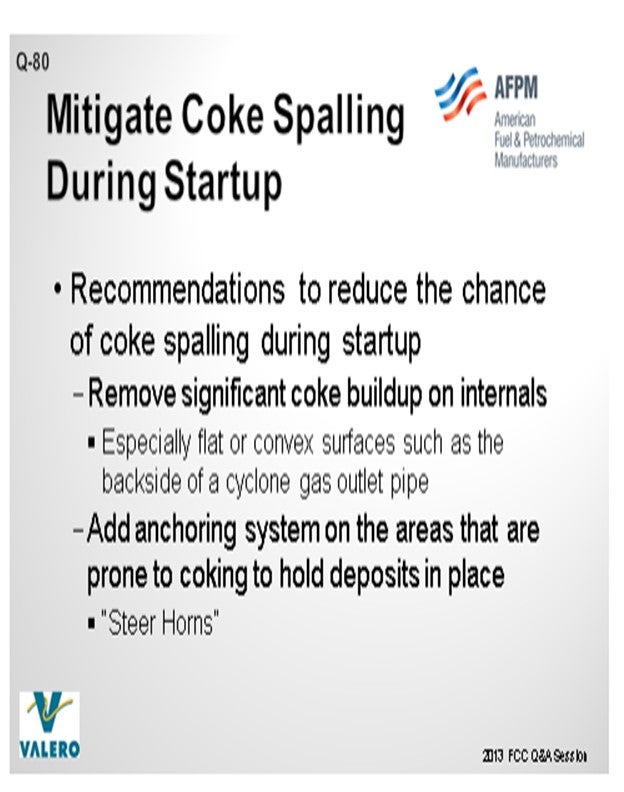
Our bottom line is that if we think there will be any operational issues, we will go through and remove the coke.
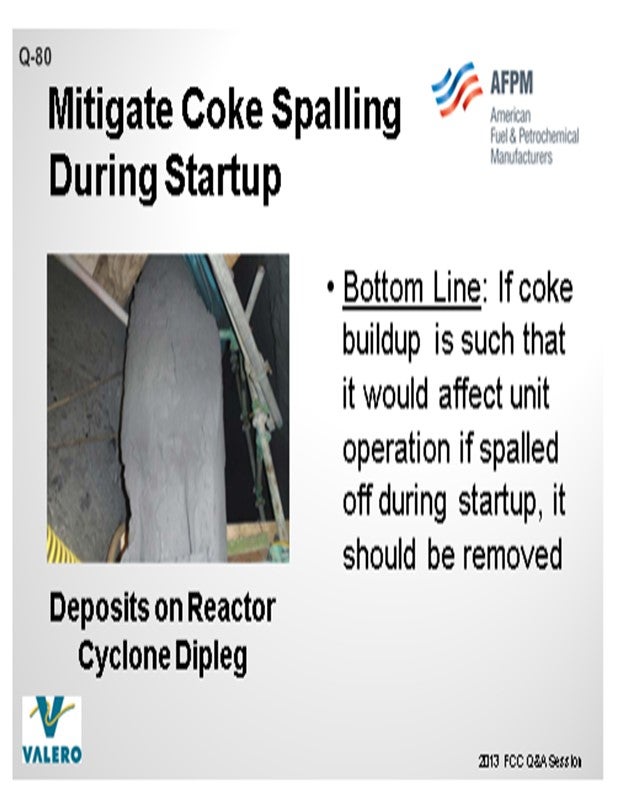
The second half of the question was about auto ignition. During our startups on the reactor side of the FCC, we keep the air temperature below 650°F. On some of our units, we actually have a sample point on the reactor vapor line outlet. As a backup check, we will actually sample for hydrocarbons at that point during the process.
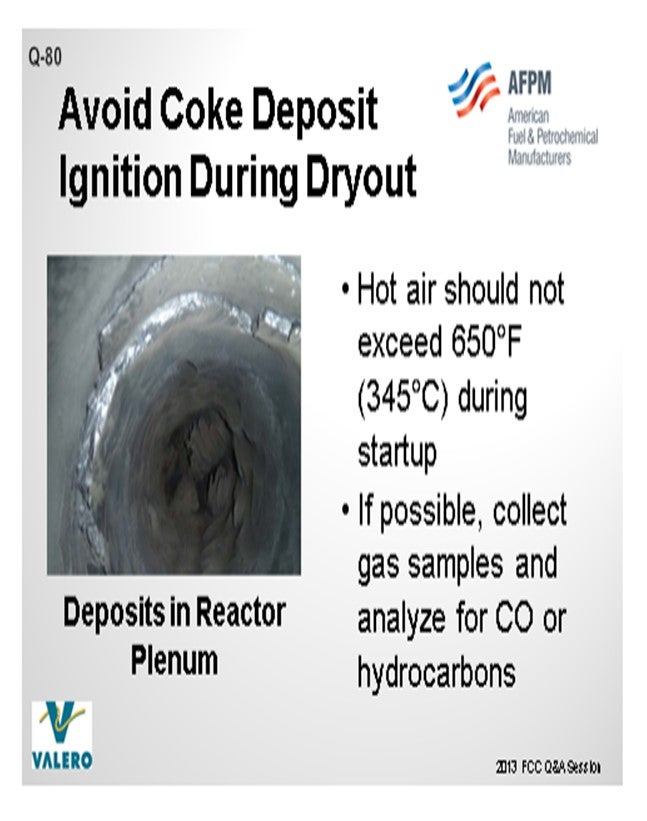
CATHERINE INKIM (PETROTRIN)
We prevent hot air from getting into the reactor system during regenerator dryout; and subsequently, we use the initial catalyst circulation for reactor side dryout.
Prior to lighting the direct-fired air heater for regenerator refractory dryout, dry steam is introduced on the reactor side at the reactor riser, feed distributors, reactor stripper and reactor dome at a controlled rate to prevent damage to feed distributors. Steam rates are adjusted to maintain the reactor pressure higher than the regenerator pressure for the entire regenerator refractory dryout period. Temperatures in the reactor are also monitored to ensure that there are no excursions which can indicate coke burning due to air leakage. The bleed upstream the spent catalyst slide valve is cracked open to remove any built-up condensate.
After the reactor vapor blind is removed and prior to catalyst loading, the reactor pressure is adjusted to circa 1 psi above the regenerator pressure to minimize steam leakage to the regenerator via the regenerated catalyst slide valve. The reactor system is dried out by transferring hot catalyst from the regenerator to increase the reactor riser temperature at a rate of 100°F per hour. The temperature in the reactor system is closely monitored to ensure there are no excursions.
It is important to ensure that the reactor pressure does not increase to above 2 psig higher than the regenerator during catalyst loading as steam can enter the regenerated catalyst standpipe since the slide valves are not tight shut-off valves. The combination of steam and “cold” catalyst can lead to mud formation which may be difficult to clear and can prevent catalyst circulation.
JEFFREY BULL (Valero Energy Corporation)
There are no guarantees that coke will not spall off the internals and refractory linings during refractory lining repair dryouts or unit startups. There is a good possibility that any coke deposited on the internals will spall, especially on convex or relatively flat surfaces such as on the back side of a cyclone gas outlet pipe. This deposit should either be removed before startup, or an anchoring system should be installed on the backside of the gas outlet pipe to hold coke deposits in place.
There should be no concern about coke buildup on concave surfaces such as vapor lines having diameters less than about 36” (914 mm). If the coke buildup causes an unacceptable pressure drop in the vapor line, then decoking should be performed prior to startup. Coke buildups in these lines are held in place by adhesion and by the arch affect caused by the curvature of the line.
Bottom line: If coke buildup is such that it would affect unit operation if spalled off during startup, it should be removed. To avoid coke burning in the reaction side of the FCCU, hot air entering the reactor either through the riser or the spent catalyst line should not exceed 650°F (345°C). It is standard procedure to monitor this temperature at our refineries as we go through dryout. In cases where it is possible to catch a gas sample, we will also analyze samples periodically to determine if we have any hydrocarbons in the vapor.