Question 73: Octane may become an issue as refiners increase severity on the FCC gasoline post-treatment units. What are your options available to address octane debits?
DE GRAAF (Johnson Matthey Process Technologies)
When you want to reduce the sulfur in gasoline, one of the first options you can do is undercut the gasoline. The sulfur distribution in gasoline is typically exponential. If you reduce the cutpoint of your gasoline, you will reduce the amount of sulfur in your gasoline. Sulfur exhibits an exponential distribution. So, if you do not have a perfect distillation, the presence of a heavy tail will disproportionately add a lot of sulfur into your gasoline. A reduction in gasoline cutpoint will increase or decrease your octane, depending on your current cutpoint. As we have just discussed, the blending in of components that are low in sulfur but high in octane will also help like, again, increasing Reid vapor pressure and blending in ethanol alkylate reformate. You can also recycle the gasoline in the FCC. If you subject the gasoline to more hydro transfer that is just thrown back into the unit, you will see a reduction in sulfur and gasoline.
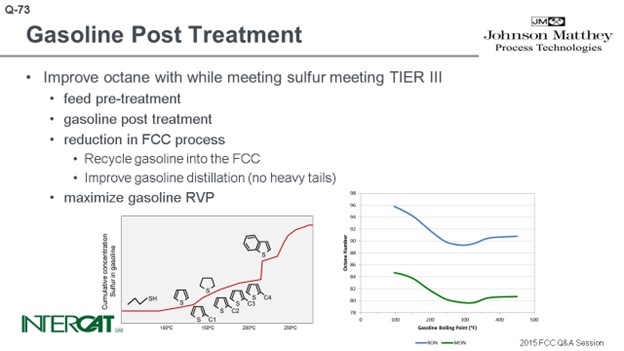
There are some options of catalyst optimization, including optimizing the amount of rare earth on zeolite. A higher concentration of rare earth on zeolite increases hydrogen transfer and typically helps to reduce sulfur in gasoline, but it comes at the expense of octane. So, optimizing the amount of rare earth is one option. Another option is increasing the amount of matrix in catalyst. Matrix has a limited affinity for cracking sulfur. It can reduce sulfur in gasoline slightly. You can optimize the octane by using ZSM-5 additives. Typically, ZSM-5 additives – both specialty and normal – will not affect the sulfur in gasoline.
There is, of course, the option of using LGS (low gasoline sulfur) additives, additives to reduce gasoline sulfur. As just was mentioned, LGS additives can typically reduce gasoline sulfur by about 20 to 35%. Contaminant metals on catalysts also have an effect; and especially, vanadium has some desulfurization tendency. Some refiners have used resid catalysts as a sulfur reduction additive because they contain high rare earth, high matrix, and typically high levels of vanadium. This addition of resid e-cat helped reduce gasoline sulfur but came at a severe penalty in coke and dry gas. Typically, sulfur reduction catalysts and additives use many of the components present in resid catalyst, but they are composed in such a way that they do not have an effect on coke or dry gas.
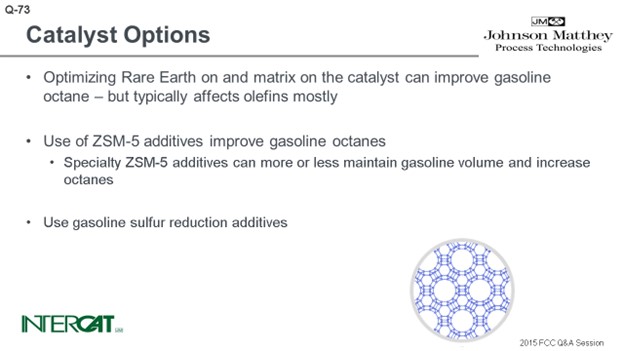
LARSEN [Marathon Petroleum Corporation (MPC)]
Bart covered a lot of the basics, in terms of how you can make more octane in the refinery; for example, you can turn up your cat feed hydrotreater unit. We also optimize our post-treater units making sure that we are only post-treating the material that actually needs post-treating, whether it is through gasoline separation or multistage post-treatment type units.
As we get closer to Tier 3, I think more and more folks will be in a pretreater-FCC/ post-treater mode. Bob brought up the potential for gasoline sulfur reduction additives. At Marathon, we run a lot of our cat feed hydrotreater units in aromatic saturation mode. When you get to the point of reaching your budget curve, the choice will become a lot more important, in terms of 1) what you do to raise temperature and come off with aromatic saturation or let sulfur slip, and 2) what will be the impact of incremental sulfur in your post-treater. So, I think gasoline sulfur reduction with additives could play an important role in optimizing the cat feed hydrotreater FCC gasoline post-treater group of units in our refineries looking forward.
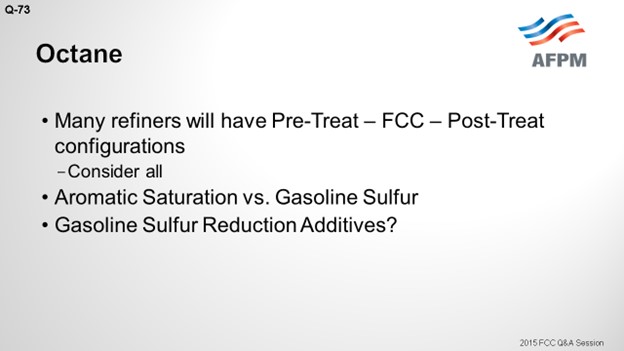
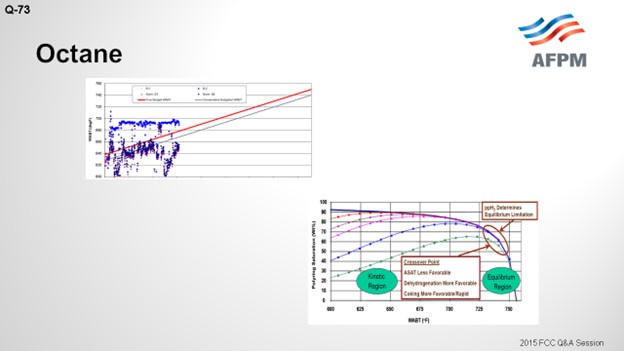
STUART FOSKETT (BASF Corporation)
Those were a lot of great ideas and options presented by the panel. I want to add just one more. One of the opportunities to reduce octane loss in hydrotreaters is to minimize the number of olefins in the gasoline since olefins are easily saturated to low octane paraffins. Most operating variables – and even a lot of catalyst variables – that affect olefins will also affect RON. So, the two works against each other to cancel out benefits. However, the one variable that can really give you a reduction in gasoline olefins without losing octane is catalyst activity simply by running the unit at a higher equilibrium activity. Equilibrium activity has a minimal effect upon octane, but the number of olefins in gasoline will be significantly reduced, which will, in turn, minimize the octane penalty from hydrotreating.
KENNETH BRUNO (Albemarle Corporation)
I just want to point out, again, that we have provided a rather detailed answer in the Answer Book which will be included in the final transcript. I encourage you to read our comments.
COLIN BAILLIE (Grace Catalysts Technologies)
Several direct catalytic options exist for the management of octane in the FCC. We will discuss the impact of ZSM-5 additives and changes to base catalyst with respect to hydrogen transfer. Additionally, we will address the ‘indirect’ use of Grace’s GSR® technologies to preserve refinery octane.
One way of increasing FCC gasoline octane is through the use of a ZSM-5-based additive. Figure 1 shows how RON can be boosted considerably by increasing the amount of additive in the inventory. The effect of ZSM-5 is more pronounced at lower initial conversion levels. Grace offers a variety of ZSM-5-based additives. OlefinsMax®, OlefinsUltra®, and OlefinsUltra® HZ FCC additives increase light olefins yield for petrochemical applications or alkylation feed while maximizing gasoline pool octane.
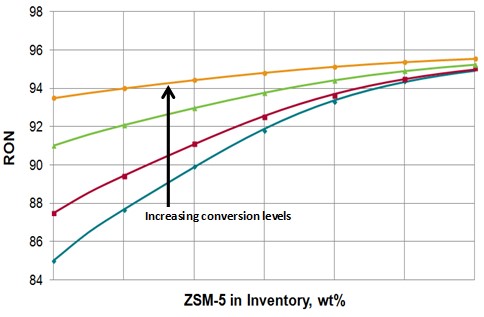
he FCC catalyst itself plays a significant role, with a lower unit cell size (UCS) typically providing higher gasoline octane though a reduction in hydrogen transfer reactions. As shown in Figure 2, RON and MON can be increased by 3 and 1 numbers, respectively, over a UCS range of 24.24 to 24.40 Å (ǻngström). The gain in gasoline octane comes at the expense of approximately 2 wt% gasoline, which is cracked into LPG olefins.
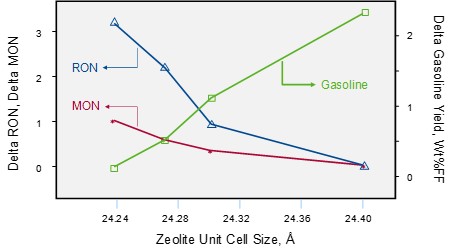
The impact that the FCC catalyst can have on gasoline octane is demonstrated through a recent Grace publication.6 The refinery switched from an alternate supplier to a Grace catalyst with an optimized UCS, which led to an increase in the FCC gasoline MON by 0.5 numbers that enabled the refinery to produce 5% more premium-grade gasoline.
In addition to increasing FCC unit octane, both the ZSM-5 additive option and the base catalyst UCS option have the added benefit of producing more olefinic yields, thus creating more alky feed for the refinery. This can provide a ‘double octane benefit’ to the refinery, presuming the refiner has the capability to alkylate the additionally produced light olefins.
The use of Grace’s GSR® technologies for gasoline sulfur reduction is also an option for maintaining or increasing gasoline octane. Decreasing the sulfur content of FCC gasoline in the cat cracker allows the severity of the post-treatment to be reduced, which will preserve gasoline octane. This is highlighted by the following example from a North American refinery (originally published in AFPM AM-07-06):7 A feed hydrotreater outage resulted in higher sulfur feeds being processed in the FCCU. The projected gasoline sulfur would have forced the refiner to hydrotreat approximately 5 mbpd (thousand barrels per day) of FCC gasoline to comply with emission specifications. The loss of octane from hydrotreating the FCC gasoline would have reduced the amount of low octane streams, such as light straight run and heavy cat naphtha, which could be blended into the pool. The sulfur reduction provided by Grace’s GSR® 5 additive allowed the refiner to avoid hydrotreating the 5 mbpd FCC gasoline stream, the value of which was calculated to be $0.25/bbl (barrel) or $1.7 million over the three-month period surrounding the outage.
GSR® technologies can be used simultaneously with ZSM-5 additives to achieve performance comparable to the use of each independently. Grace has co-authored an article with a refinery describing commercial experience when combining gasoline sulfur reduction technology with olefins additives.8 The refinery successfully used a SuRCA® catalyst to reduce their FCC gasoline sulfur by 20%. The refinery also used OlefinsMax® on an opportunity basis to make incremental refinery-grade propylene. The performance of SuRCA® was quantified both with and without the ZSM-5 additive. As Figure 3 indicates, the 20% reduction in gasoline sulfur was consistent whether or not ZSM-5 was present.
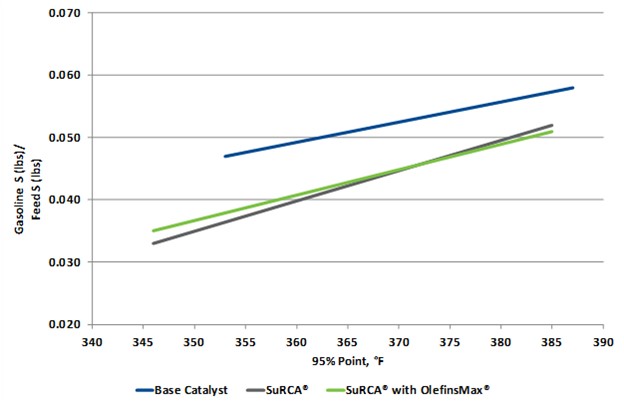
To summarize, there are several avenues in which gasoline octane can be increased, depending on the specific situation the refinery is facing. Refiners can consult their catalyst representative to find the current balance of products, as well as optimized UCS of the base catalyst to allow the refinery to meet the overall product performance goals.
BART DE GRAAF (Johnson Matthey Process Technologies)
Severe post-treatment of FCC gasoline reduces octane substantially. FCC gasoline meeting sulfur Tier 3 regulations requires feed pretreatment, gasoline post-treatment, sulfur reduction in the FCC process, or a combination of these options.
First, limit gasoline sulfur intake. Feed with sulfur content or which contains less aromatic sulfur species will typically result in lower sulfur in gasoline. When a feed pretreater is used, its severity can be balanced with the severity of the post-treatment to optimize gasoline octane while meeting regulations. Reducing gasoline hydrotreater severity helps preserve octane, but the FCC gasoline octane depends on the severity of the pretreat.
The distribution of gasoline sulfur species versus boiling point is nearly exponential: the higher the gasoline cutpoint, the higher the gasoline sulfur. Reducing gasoline cutpoint reduces the gasoline sulfur content and, therefore, the severity of post-treatment required. Reducing gasoline cutpoint comes at the expense of gasoline volume and can improve or reduce gasoline octane, depending on the cutpoint (for low gasoline cutpoints, it typically improves gasoline octanes). Another effect of the exponential sulfur distribution is that gasoline sulfur content depends strongly on the quality of distillation. A heavy tail in the gasoline fraction will increase sulfur content disproportionally.
Gasoline recycle into the FCC unit decreases gasoline sulfur, as the gasoline sulfur species are exposed to more hydrogen transfer reactions. Where possible, it is advantageous to maximize gasoline Reid vapor pressure to maximize octanes. Blending in (or increase the ratio of) high octane streams with no- or low sulfur content will help as well: ethanol, alkylate, and reformate. If there is room, ZSM-5 additives can be used to produce more feed for the alky unit, and medium cracked naphtha streams can be diverted to the reformer to improve octane.
There are various catalytic options to reduce gasoline sulfur. Optimizing catalyst rare earth content will reduce gasoline sulfur, but it decreases gasoline octane (typically affecting gasoline olefins mostly). High matrix catalysts can reduce gasoline sulfur as well, without [causing?] a detrimental effect on gasoline octane. Its effects are limited though. Use of ZSM-5 additives improves gasoline octanes. Standard ZSM-5 additives concentrate gasoline aromatics and isoparaffins but decrease gasoline volume. Specialty ZSM-5 additives can more or less maintain gasoline volume and increase octanes. Use of gasoline sulfur reduction additives can effectively lower gasoline sulfur and, therefore, reduce severity of post-treatment, which allows for conservation of gasoline octanes.
Each of the options above, or combinations thereof, can help improve gasoline octane after post-treatment. The most efficient solutions are unit specific as each unit will be maximized against its own set of operational limits.
NIKOLAS LARSEN [Marathon Petroleum Company (MPC)]
MPC has seen a large increase in the value of octane coming from FCC gasoline in recent years following the expansion of tight oils into the marketplace and the swell of light straight run material in refineries. This, along with the value of alkylate and LPG, continues to drive FCC economics to maximize production of wet barrels. Options to address octane debits can be grouped into two buckets:
-
Make more
-
Other refinery units: reformer, isomerization, alkylation, etc.
-
FCC: catalyst, additives, operating conditions, etc.
-
Blending: ethanol, etc.
-
Lose less
-
Increase CFH severity to decrease severity in gasoline post-treater
-
Post-treater optimization: SHU, separation, etc.
Most in the industry are familiar with basic FCC handles to manipulate gasoline octane: fresh catalyst/rare earth, severity, ZSM-5, etc. Most plants are also set up on paper to have a successful operating strategy under new Tier 3 conditions when considering octane and other blending targets and requirements. However, around the edges, it can get more interesting, especially when dealing with three different refinery units: CFH, FCC, and gasoline post-treaters. There are several instances where a gasoline sulfur-reducing (GSR) additive may be a successful strategy. First, most units with CFH units realize the economic benefits of H2 addition to FCC feed. However, as sulfur regulations tighten, the amount of aromatic saturation could be impacted if you move past the ‘knee’:
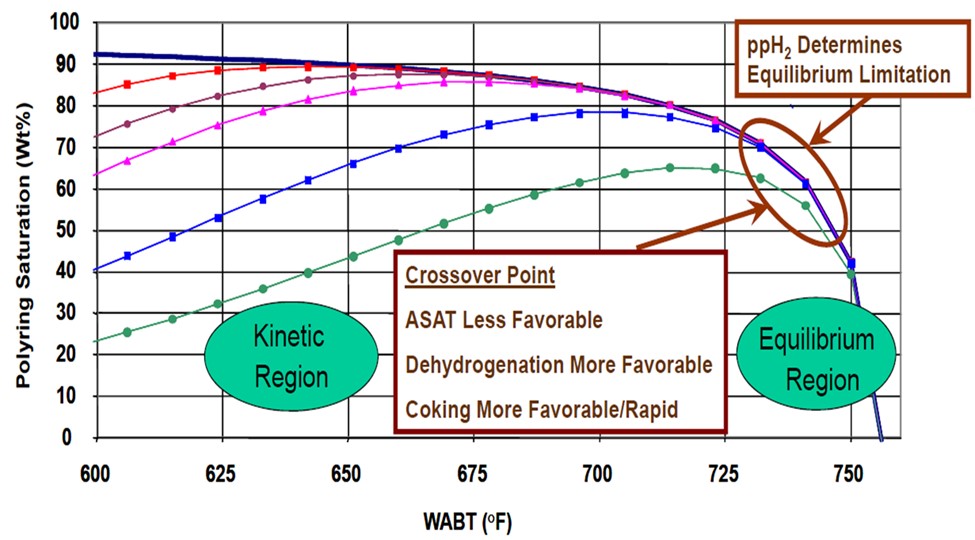
Given the significant economic incentive to maximize H2 addition to FCC Feed, MPC is ready to use GSR additives as a tool to optimize operations under Tier 3 environments in order to stay in aromatic saturation mode longer while either limiting octane loss across a post-treater or maximizing CFH run-length within gasoline sulfur constraints. This benefit of GSR – to reduce severity in the post-treater and/or, depending on gasoline distillation capabilities, possibly routing lighter streams straight to blending instead of having to be processed – can be significant given strong refinery octane-barrel values. There can also be options for units with two-stage post-treaters to minimize octane loss of specific streams.
LYNNE TAN XIN LIN (BASF Corporation)
To meet Tier 3 quality FCC gasoline (lowered sulfur content of gasoline from 30 to 10 ppm), many refiners will add FCC gasoline post-treatment or increase severity of current post-treatment units. Such treatment does invariably result in octane loss due to saturation of some of the olefins. To counter such octane debits, FCC catalyst technology can be used to not only enhance octane level but also to minimize product sulfur to reduce the need for further post-treatment. It is important for the refiner to actively manage e-cat activity. A low e-cat activity will result in gasoline with higher olefins content without a significant increase in octane. A higher olefins-content gasoline will experience greater octane loss in post-treating. Therefore, it is important to maintain a higher e-cat activity in the unit. Gasoline sulfur additives, such as BASF's Low Sulfur Additive (LSA) is a way to trim gasoline sulfur which may avoid the need for capital investment. For units with post-treatment, LSA will allow the unit to run at a lower severity for a lower octane penalty to achieve the target product sulfur. A lower severity operation will also extend the catalyst life and reduce H2 consumption.
RYAN NICKELL (Albemarle Corporation)
Both catalyst and additive options exist for refiners facing an octane deficit. Refiners with room on the wet gas compressor and favorable pricing for propylene should consider an additive like Albemarle’s DuraZOOM™. This additive contains ZSM-5 zeolite which cracks low-octane gasoline-range olefins into propylene and butylenes. The remaining high-octane molecules increase in concentration; thus, the observed naphtha octane also increases. DuraZOOM™ exhibits high activity and can be used at modest concentrations to minimize dilution of the base catalyst’s activity. For refiners preferring no dilution whatsoever, Albemarle’s PROvantage™ may be recommended. Since PROvantage™ contains both matrix and zeolite technologies, it efficiently cracks bottoms while also providing the aforementioned benefits for octane enhancement. A third alternative being adopted by many North American refiners is a switch to Albemarle’s ACTION catalyst. The matrix in ACTION provides excellent bottoms cracking while the novel zeolite technology (ADZT-100) promotes both octane enhancement and the production of butylenes. These butylenes can, of course, be fed to an alkylation unit for further production of high-octane gasoline blendstock. The optimal choice between DuraZOOM™, PROvantage™, and ACTION depends on each refiner’s unique FCC unit configuration and product values. Albemarle’s technical service representatives can forecast the optimal solution.