Question 70: With environmental regulations becoming more stringent on FCC stack emissions, what are your available options to achieve the required level of SOx (sulfur oxide) and NOx (nitrogen oxide) emissions?
FOSHEE (Shell Global Solutions - US)
From both the SOx and NOx perspective, there is a cat feed hydrotreater that will reduce both your sulfur and nitrogen compounds in the feed to your cat cracker, which will produce lower SOx and NOx emissions. It will reduce your metals in the feed and increase the hydrogen content of the feed, which will improve FCC unit conversion.
Regarding SOx specifically, other than the cat feed hydrotreater, there are SOx-reduction additives. These tend to be less effective in a partial-burn unit. There are also post-treatment options: either a non-regenerative type of option, like a wet gas scrubber, or a regenerative type of option such as Cansolv, THIOPAQ, and Labsorb. Shell has experience with cat feed hydrotreaters, SOx reduction additive, and wet gas scrubbers.
Regarding NOx reduction and cat feed hydrotreaters, you have NOx-reduction additives that fall under two categories: either NOx-destroying additives or non-platinum-based combustion promoters. There are regenerator hardware options, such as countercurrent regeneration, which help with NOx reduction. There are post-treatment options, including selective non-catalytic reduction (SNCR) and selective catalytic reduction (SCR), which are located after the CO boiler or waste heat boiler. In conjunction with the scrubber, you can have LoTOx™.
Regarding CO boiler hardware, there are low NOx burners that you can put into place to reduce thermal NOx. Shell has experience with cat feed hydrotreaters, platinum-based promoter, countercurrent regeneration, SNCRs, and SCRs.
LARSEN [Marathon Petroleum Corporation (MPC)]
In Marathon, we are lucky. We hydrotreat at least a portion of the feed for seven of our eight FCC units, so we start with an advantage. I will mention a couple other items related to NOx. First, we have not seen feed nitrogen be a really big influence around the NOx values on some units, with one exception: a unit that processes a batch sweet vacuum resid in it. We have seen that change NOx a good bit. We also have four scrubbers in our FCC units across the Marathon system and at least four units for which we use SOx additives to control SOx. In general, we have been pleased with the latest generation SOx additives and their pickup factors, as well as the ability to use them without significantly diluting catalyst activity in our FCCs.
Related to low NOx promoter, I put some of our experiences up on the slide. You can see that we are generally operating with low NOx promoter. We have been able to reach 30 to 50 ppm or so in different degrees of reduction compared to platinum promoters.
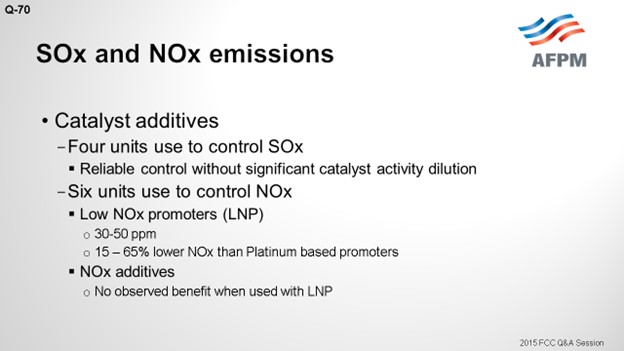
A lot of this information was covered in Questions 29, 31, and 32 during the FCC session of the 2009 AFPM Q&A. Some of Marathon’s information and data can be seen in that transcript, if anyone wants to look it up.
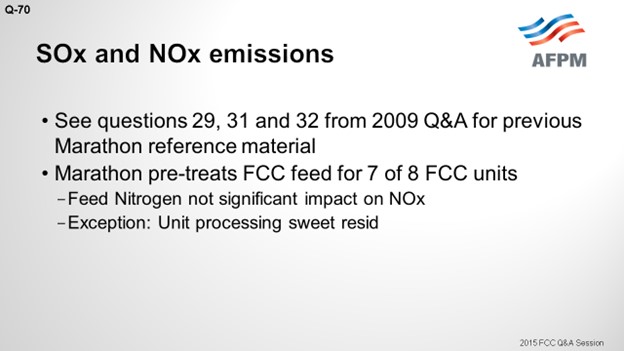
Other than that, we do have one SNCR and a couple of LoTOx™ units. We are pleased with the LoTOx™ performance. We are able to get under 10 ppm NOx on those units. They work very well. They use ozone injection. I am sure you know about ammonia injections for ESPs. We have seen them reduce NOx on one unit but not in another. It is not completely understood, although there are a few theories why that might be. Otherwise, there are a couple of interesting new technologies available now. Next-generation additives and who knows what will be next to come and help us get to the next level of reduction in emissions.
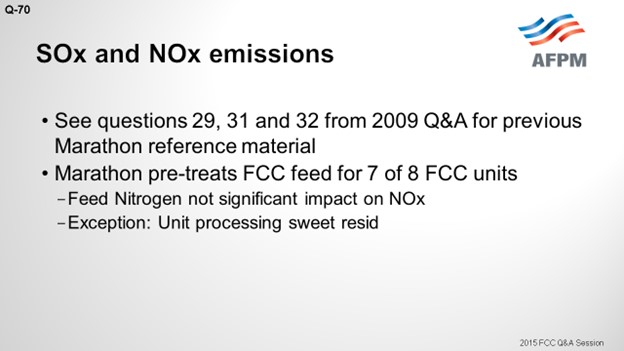
DE GRAAF (Johnson Matthey Process Technologies)
Our customers use SOx additives to reduce SOx. They can reduce SOx in full-burn up to 25 ppm, 10 ppm, or even below 5 ppm. For NOx reduction, typically, you would first try to reduce excess oxygen. If that is not enough, you would switch from a platinum to a non-platinum combustion promoter. Depending on the unit, you can reduce NOx by about 70 to 90%. We have also seen, in various trials, that you can reduce NOx further by 30 to 50% by using NOx additives. Please note the results are quite unit specific.
STEFANO RIVA (BASF Corporation, Europe)
We had a customer seminar last week, and I want to share the experience of one of our customers who actually presented their emissions reduction program. It is a refinery in Romania called Lukoil Petrotel. As you might know, Romania joined the EU (European Union) a few years ago. So as of January, of this year, the country had to comply with the SOx, NOx, and particulate emission. However, they were not initially in compliance with any of them. They investigated all options (feed pretreatment, FCC hardware modification, use of FCC additives, post-treatment with scrubber, ESP, filters, etc.); but given the limited time before the environmental limits would start, they had to go with the solution with the highest probability of success: a LoTOx™ scrubber.
However, while the LoTOx™ unit was under construction, and even after it started to operate, they investigated the use of additives. It quickly became clear that they could solve the NOx problem completely with the BASF COnquer, a Pd (palladium)-based CO promoter. Addressing SOx reduction required a couple of million dollars of capital investment in the scrubber, plus nearly $1.5 millions of OPEX (operating expenses). The use of EnviroSOx additive was easily justified by the reduction of consumption of caustic. This proves that, at least for this particular refinery, the use of additives is still a viable solution, even in combination with hardware solutions.
RYAN NICKELL (Albemarle Corporation)
I want to respond to the comment about use of SOx additives in partial burn. Albemarle has spent a lot of time on research and development looking at that situation, and we developed a product called SOxMASTER-2™. We have seen really impressive commercial results with it so far. This product is specifically geared for partial-burn applications, and it really overcomes a lot of the traditional problems with SOx additives in partial-burn.
When it comes to full burn, we offer two products: KDSOx® and DURASOx™. DURASOx™ is very effective for refiners who need the maximum amount of activity with really low attrition. I also agree with all of the comments about the use of combustion promoters. Definitely using a non-platinum promoter like ELIMINOx® is an optimal solution.
WADHA AL-KHATEEB [Kuwait National Petroleum Company (KNPC)]
At KNPC, we are just adding a SOx additive loader to our system. I want to know if there is any experience with safety precautions when adding that loader to the system.
ROBERT (BOB) RILEY, III (Grace Catalysts Technologies)
I want to share a couple of experiences specifically about SOx additives. SOx additives have a higher level of acute toxicity than a typical FCC catalyst, so you want to make sure that you do not have any operator exposure. You want SOx additives to be delivered in a contained system and used in a manner that does not expose operators to them during the loading process. Also, although it tends to be taken for granted, it is critically important to ensure that the system you install is electrically grounded. This is an important factor, especially in systems that are procured from vendors; i.e., skid mounted or standalone units. In some systems, an area of concern can be any plastic vacuum hosing or PVC piping fixtures. These should be traced with copper line to ground them properly. I have seen several examples of refiners who vacuum additives out of containers without this safeguard, and one can see electric arcing as they vacuum. Grounding should be a primary design consideration for these systems.
MARTIN EVANS (Johnson Matthey Process Technologies)
I agree with the last speaker 100%. I also will add that it is important, when choosing the addition system, to make sure that the filtration system you have on it when you are refilling it is one which will take the dust out of the atmosphere. We have now standardized sintered metal filters for this purpose. Like I said, we want to minimize operator exposure to dust at all times. That is a very important part of the process with the addition systems.
COLIN BAILLIE (Grace Catalysts Technologies)
Grace has a portfolio of additives to help refiners reduce the number of SOx and NOx produced in the FCC unit.
SOX Reduction Additives: SOx reduction additives offered by Grace are Super DESOX® and Super DESOX® OCI, which have been used to control SOx emission levels to below 25 ppmv (parts per million by volume) SOx. These SOx reduction additives are microspheroidal powders that have similar physical characteristics to those of FCC catalysts and are typically used at dosing rates of 5 to 10 wt% (weight percent) of fresh catalyst additions. Figure 1 shows a back-to-back comparison of the two additives at comparable usage rates, excess oxygen, and feed sulfur levels in which flue gas SOx levels were maintained below 25 ppmv for both periods.
Super DESOX® and Super DESOX® OCI reduce flue gas SOx emissions through a three-part mechanism:
-
Sulfur bound in coke is oxidized to SO2 in the FCC unit regenerator. Grace’s SOx reduction additives subsequently promote the oxidation of SO2 to SO3, which is often the rate-limiting step.
-
The resulting SO3 is subsequently captured by the additive and converted into magnesium sulfate, which is facilitated through the incorporation of a patented magnesium spinel in the product.
-
The SOx additive is then transferred to the riser/stripper section where the magnesium sulfate is ultimately reduced back to its active state regenerating the additive and releasing the sulfur as H2S.
Properly balancing the additive’s ability to promote each of the above three steps is necessary for achieving the best SOx reduction performance. Grace’s SOx reduction additives have been used in more than 100 commercial applications worldwide.
Figure 1: Both Super DESOX® and Super DESOX® OCI additives-controlled SOx to <25 ppmv
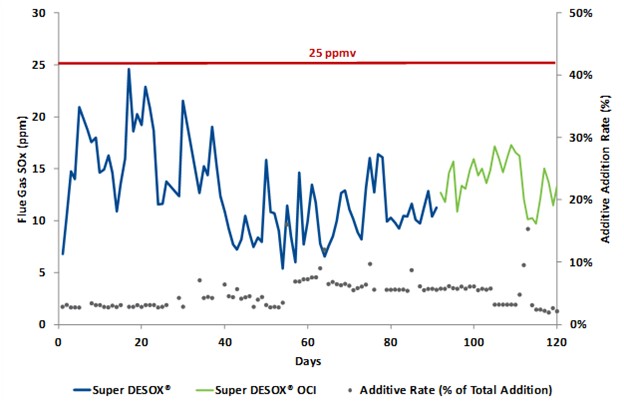
Another case study for Super DESOX® was published in a joint article with the BP Castellon refinery in Spain.2 Based on a commitment to reduce emissions, as well as increasingly stringent emissions standards, the refinery trialed the Super DESOX® additive. Figure 2 shows the SOx emissions observed using the Super DESOX® additive compared to the correlated uncontrolled SOx levels that would have been obtained without additive. The refinery achieved its trial targets and observed SOx reductions of approximately 70%.
Figure 2: SOx levels obtained using Super DESOX® compared to uncontrolled SOx emissions
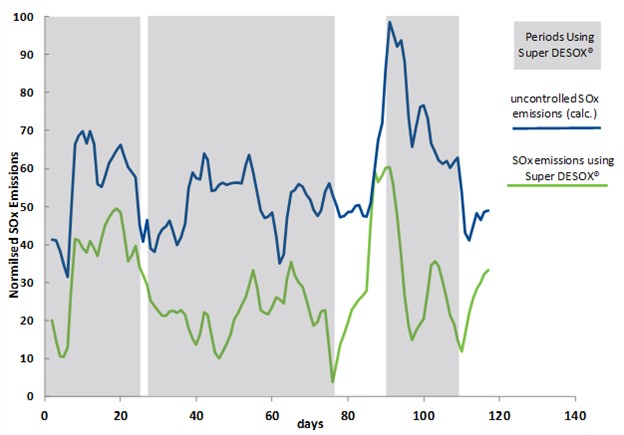
While SOx chemistry is well-understood, the chemistry of NOx formation within the FCCU regenerator is extremely complicated and typically unit specific. Early experiments by Grace showed that the source of NOx is the nitrogen bound to heavy molecules in the FCCU feed, which are ultimately burned as coke in the regenerator.3 About 50% of the nitrogen in FCCU feed typically enters the regenerator, however less than 10% of this nitrogen is usually emitted as NOx. Coke-bound nitrogen can take one of three paths: It can be reduced to N2 (nitrogen gas), oxidized to NO (nitric oxide) and NO2 (nitrogen dioxide), or remain in an intermediate stage such as NH3 (ammonia) or HCN (hydrogen cyanide). These intermediate-stage nitrogen species have the potential to oxidize to N2 or NOx, and there are several unit factors which can play a role in the direction they take. For example, high dosing rate of a CO promoter can cause these species to be oxidized to NO, increasing overall emissions. Use of CO promoters will also reduce the amounts of various reductants present in the regenerator, thereby further exacerbating NOx emissions in the flue gas. The simplified mechanism of NOx formation is shown in Figure 3.4
Figure 3: NOx Formation Mechanism in the FCC Unit
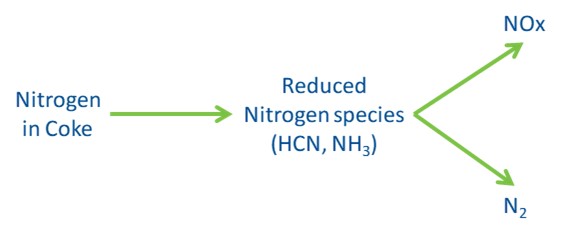
Grace offers two types of catalytic additive technologies for reducing NOx levels in the FCC unit: low NOx combustion promoters and standalone catalytic NOx reduction additives.
Low NOx Combustion Promoters: CP® P is Grace’s third-generation, non-platinum-based, low-NOx combustion promoter. CP® P is designed to catalytically promote CO combustion with a similar efficiency of a traditional platinum-formulated CO promoter, yet it has a reduced propensity to generate NOx emissions. CP® P combustion promoter was recently used in a refinery trial, as an alternative to a platinum-based promoter, with the objective of reducing NOx emissions while maintaining CO promotion activity. Factors affecting NOx formation are mainly feed nitrogen, e-cat platinum content, regenerator air distribution, excess oxygen, dense bed temperature, and dense bed level. Correlation models are important to determine catalytic additive performance in a dynamic environment, such as an FCC regenerator. Figure 4 shows the correlation made before the trial to calculate the predicted NOx emissions. From the data available, the best correlation found was related to excess oxygen.
Figure 4: Correlation model had good agreement with actual FCCU NOx Emissions
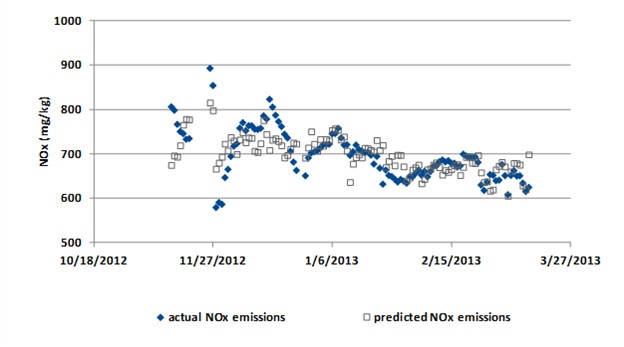
Figure 5 shows how the NOx emissions decreased when switching from the platinum-based promoter to CP® P.
Figure 5: Application of CP® P reduced NOx levels by 80% without compromising CO combustion promotion activity
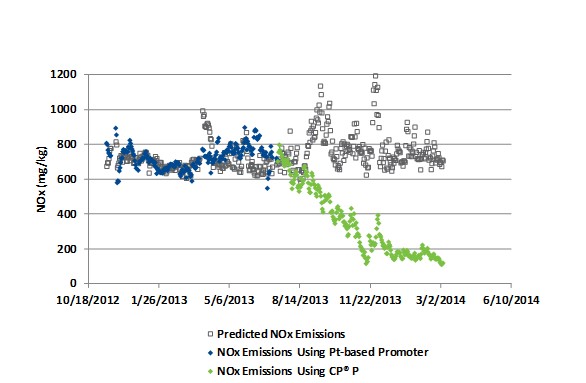
Standalone Catalytic NOx Reduction Additives: Grace’s portfolio includes DENOX®, which is a standalone NOx reduction additive without combustion promotion activity. Since its introduction in 1997, DENOX® has been successfully evaluated in a wide range of FCCUs. DENOX® is typically used at dosage rates of between 0.15 to 2.5 wt% of fresh catalyst additions and has provided a range of NOx reductions from 15 to 60+% (Figure 6).
Figure 6: Frequency of Observed NOx Reduction Bands in FCCU Applications
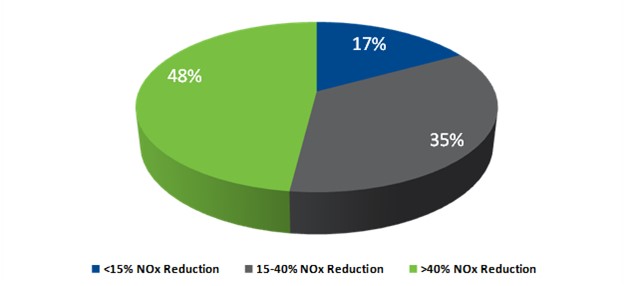
DENOX® has been used to reach as low as 26 ppm NOx, as shown in Figure 7. In this FCC unit, DENOX® was used at 1 wt% of fresh catalyst additions and demonstrated 75% NOx reduction.
Figure 7: DENOX® has achieved as much as 75% NOx Reduction.
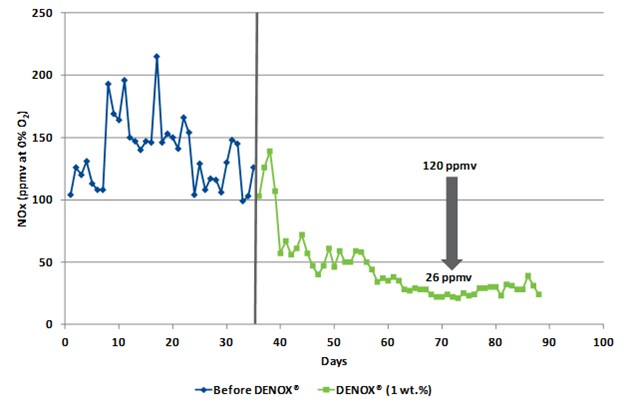
NIKOLAS LARSEN [Marathon Petroleum Company (MPC)]
MPC pretreats its FCC feed (at least a portion) for seven of its eight FCC units. Obviously, this is an effective way to manage SOx. We also have four units with flue gas scrubbers. MPC has presented significant data in previous AFPM meetings (2009, etc.) but will summarize here since it has been several years. See Questions 29, 31 and 32 from 2009 AFPM Q&A for additional reference material.
We have not seen significant impact from feed nitrogen on NOx emissions; the one exception being a unit that processes sweet vacuum resid at times.
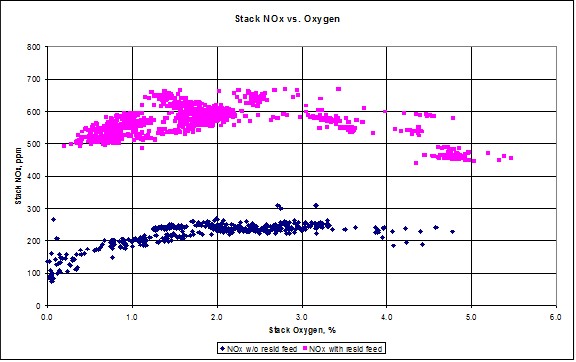
MPC uses catalyst additives on four units to control SOx and on six units to control NOx. MPC has been satisfied with the performance of next generation “Super” SOx additives. The pickup factor has improved significantly since the additives were introduced and has allowed for reliable control of SOx emissions, without significant catalyst activity dilution. Low NOx CO promoters (LNP) also performed well. However, outside of rare earth replacement technology, these two additive markets are ready for the next technological advance.
Additionally, MPC still sees very limited value in NOx reducing additives. Although these additives have been effective when used with Pt COP (platinum combustion promoter), MPC has not seen any incremental benefit when used with LNP. This remains an opportunity for industry to find a product that can incrementally reduce NOx. The majority of units using LNP have been able to control NOx at 30 to 50 ppm. During Consent Decree trials, our percent reduction from baseline NOx when switching to LNP from Pt promoter ranged from about 15 to 65%. Below is a trend showing conversion from mid-grade Pt to LNP and reduction in overall NOx and variability.
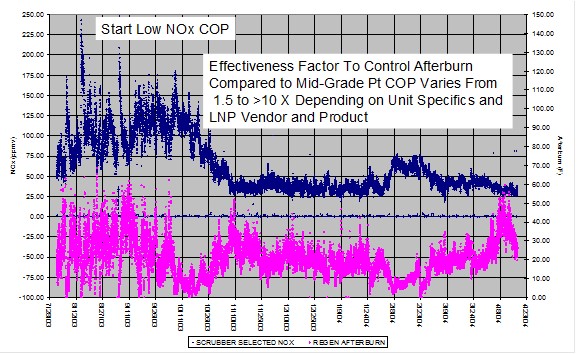
Given further decreases in NOx emissions limits, additional controls (or advancements in technology) are needed. Although MPC does not have SCR technology in its FCC units, we do have one SNCR and operate two LoTOx™ units and we have been pleased with the technology. NOx levels less than 10 ppm are achievable with LoTOx™. MPC has also conducted trial testing of next generation NOx additives to help drive technology advances. Another interesting technology currently in use in industry is Praxair’s CONOx.
Ammonia injection into an ESP can also have a large impact on NOx emissions. We have seen this in one unit and not in another. Possible theories for the difference include the use of SOx additives. The unit that sees a NOx reduction uses SOx additives; the MgO (magnesium oxide) and vanadium could be catalyzing the NOx reduction with NH3. See below for MPC testing experience.
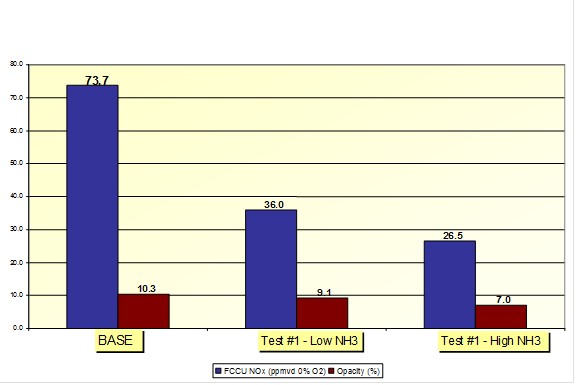
SCOTT EAGLESON (DuPont™ BELCO® Wet Scrubbing Technologies)
Wet scrubbings systems have been used for many years to control FCCU flue gas emissions. The BELCO® EDV® Wet Scrubbing technology is used primarily for control of particulate and SOx emissions to meet the most stringent standards. Where needed, NOx emissions are also controlled using a patented oxidation process by Linde LLC during which flue gas NOx is oxidized to nitric acid and easily scrubbed from the flue gas in the BELCO® EDV® Wet Scrubbing process. There are over 100 EDV® Wet Scrubbing systems in use on FCCUs worldwide. Recent EDV® advancements support meeting lower and lower outlet emissions requirements. These advancements can be applied to upgrade and improve the performance of existing BELCO® EDV® Wet Scrubbing systems with some of these advancements applicable to improving performance of other wet scrubbing technologies.
LYNN TAN XIN LIN and ALEXIS SHACKLEFORD (BASF Corporation)
Increasing environmental awareness at a global level is driving enforcement of stringent regulations to limit emissions of sulfur- and nitrogen-containing gases to the atmosphere. The use of catalytic additives is a convenient solution to help FCC operators achieve the required level of SOx and NOx emissions without capital investment. These additives can be added directly to the FCC catalyst inventory for immediate effects. In the case of controlling SOx emission, SOx reduction additives reduce sulfur oxides in regenerator to hydrogen sulfide where it is released in the riser for further recovery. Cerium is commonly used in the additives to oxidize SO2 to SO3, and vanadium will further reduce it to H2S in the reactor/riser. BASF’s EnviroSOx is specially designed with the optimal content of such metals to maximize SOx removal per unit additive addition rate (i.e., pickup factor). In a recent back-to-back trial with four suppliers in a R2R FCC unit in Asia, EnviroSOx outperformed the three competitors by reducing uncontrolled SOx emission to less than 700 ppm with a pickup factor of 15.5. NOx reduction is extremely unit- specific and can vary depending on type of feed and process parameters. For example, under full-burn conditions, NOx correlates well with excess oxygen in flue gas; whereas under partial-burn conditions, nitrogen in coke is only partially combusted to reduced species which go to form NOx in CO boiler. This requires the consideration of NOx reduction additive in the regenerator, as well as low NOx CO promoter for better afterburn control. BASF offers CLEANOx which is a NOx sorbent with optimized contact area to allow conversion of nitrous oxide to N2. At an addition rate of 1.4 wt% of fresh catalyst addition, CLEANOx had been shown to reduce NOx by more than 70% with no increase in hydrogen and dry gas. In addition, BASF also offers a Palladium-based CO Promoter, COnquer, which can promote CO with lower NOx formation compared to the conventional Platinum-based CO Promoter. Both CLEANOx and COnquer are effective for use in partial-burn as well as full-burn units.
CHRIS STEVES (Norton Engineering)
There are many options available for SOx and NOx emissions reductions from FCC units. The best option for each unit will depend on the existing configuration of the unit, current emissions and new limits, and desired capital versus operating costs. Some options include:
-
Flue Gas Scrubbing: FCC Gas Scrubbers [such as the VSS (Venturi Scrubbing System)] offered by Norton Engineering) can reduce both particulates and SOx emissions from FCC stacks in a reliable and cost-effective manner.
-
Grassroots and Retrofit Designs take into account available flue gas pressure drop, available plot space, sources and quality of available makeup water and reagent, and purge effluent quality limits in order to maximize reliability and minimize ongoing operating costs. New wet scrubbers can be designed, and existing wet scrubbers retrofit to include NOx control technologies such as LoTOx™, WGS+, and Sodium Chlorite/Hypochlorite Scrubbing.
-
Selective Non-Catalytic Reduction (SNCR) is a highly temperature-dependent NOx control technology which is not usually as effective as selective catalytic reduction (SCR) technology. However, an SNCR installation is usually much less complex and much less expensive than SCR. SCNR is most effective when installed on partial-burn FCCs which have CO boilers with adiabatic combustors. These systems can be operated in an optimum temperature range and provide sufficient residence time to achieve high levels of NOx reduction. SNCR installed on partial-burn FCCs with water tube CO boilers will be less effective than adiabatic combustor units due to limitations in controlling flue gas temperature and temperature variation, and residence time. SNCR installations for full-burn FCCs require staged reagent and “catalyst” (hydrogen) injection in the regenerator plenum and along the regenerator flue gas outlet line to achieve even low levels of NOx removal due to low flue gas temperatures (<1350°F).
-
Catalyst Additives, for reductions in both SOx and NOx, are available from multiple suppliers. These additives can be added quickly to the unit with low capital expenditure but may add significant operating expenses to the refinery and have had varying degrees of success (depending on unit configuration, type of sulfur species, and operating conditions). The steady move to cleaner feedstocks has, in most cases, reduced FCC feed sulfur and nitrogen levels. This fundamental change from the heavy feeds more typical prior to 2008 has opened the window of opportunity for refiners to use additives for both SOx and NOx control.
-
Feed Hydrotreating: Installation of a new feed hydrotreater upstream of the FCC can reduce SOx emissions from the FCC stack, but it will require a fairly significant capital investment and may not be suitable if the FCC is processing resid type feedstocks. It is also important to remember that stack SOx emissions will increase if the hydrotreater has an unplanned shutdown with the FCC remaining in operation.
-
Selective Catalytic Reduction (SCR): This technology is the gold standard in NOx reduction, proven in many successful FCC applications. It can be designed for very high levels of NOx removal (95+% is typical) and can achieve very low NOx emissions (<10 ppmv @ 3% O2). SCR installations consist of a steel box with two to three fixed catalyst beds, ammonia injection facilities, and cleaning facilities installed downstream of the FCC. Operating temperature is critical to achieving reliable SCR performance over the course of an FCC run, and many FCCs will require modification to CO boilers and/or waste heat recovery units to ensure that flue gas temperatures are in the range for proper SCR operation. SCR installations are much more expensive than other options with the exception, perhaps, of a LoTOx™ system. In general, the “Gold Standard” costs a lot of gold.
-
Regenerator Design: For full-burn FCC units, operation at low flue gas O2 is essential in order to minimize NOx emissions but may be difficult in units with non-optimum catalyst and/or air distribution. Upgrading regenerator internals to improve catalyst and air distribution has been proven to reduce NOx emissions but will typically involve significant capital expenditures. Refiners should consider regenerator modifications (technologies are available from FCC technology suppliers and consultants) when they have identified a need to modify regenerator internals (existing equipment is at its end-of-life). In this circumstance, the cost of emission control will be roughly equal to the incremental cost of the new technology only.
RYAN NICKELL (Albemarle Corporation)
Compliance with SOx and NOx limits can be met with additives, hardware, or a combination thereof. Effective additives are available, and the economics should be compared with capital options or the operating cost (i.e., caustic) of existing hardware. A key factor affecting additive choice is the mode of operation, i.e., partial- or full-burn. NOx additives are simply not effective under partial-burn. The performance under full-burn is highly variable with the average being near 26%.5 If starting NOx is below 100 ppm, experience suggests that NOx additives may not work at all, or reduction will likely be less than 26%. Regarding SOx additives, Albemarle offers proven solutions for both partial- and full-burn operation. In partial-burn, the optimal choice is an additive containing zero cerium, such as SOxMASTER-2™. Its unique technology effectively catalyzes the critical SOx reduction reactions without cerium’s negative effect of promoting combustion in a partial-burn environment. For full-burn applications, most refiners should opt for DuraSOx™ or KDSOx™. Albemarle’s KDSOx™ is a proven workhorse while DuraSOx™ fulfills demanding applications requiring extremely low attrition and/or maximum activity. A final comment should be made regarding FCC units using platinum-based combustion promoter. While highly effective, this class of promoters inherently produces higher NOx emissions. A non-platinum promoter such as ELIMINOx™ can provide equal afterburn control with significantly lower NOx emissions. Albemarle prepares comprehensive proposals with performance estimates for these additive solutions following a technical review of each FCC unit.