Question 63: Please explain the phenomenon known as “coke ratcheting” in the FCC reactor where equipment exposed to coking services elongates over time and heat cycles. Please provide details of actual examples of where this occurred and the impact to equipment operations and reliability.
MALLER (TechnipFMC Process Technology)
Coke ratcheting is a phenomenon that occurs in hot wall refractory line equipment in the FCC reactor service. It impacts refractory linings with hex steel-type anchors and can occur with a variety of base metals, including carbon steel and alloy steel. The basic mechanism is illustrated here with some pictures. The differential expansion causes some cracks in the refractory, and that provides a pathway for hydrocarbons to get back underneath the refractory. Then, coke sets up in that annular space between the hex and the base steel, all while the unit is running in ‘hot’ position. When you go through a thermal cycle, the coke setup in that space restricts the base material from contracting all the way back to its normal cold position.
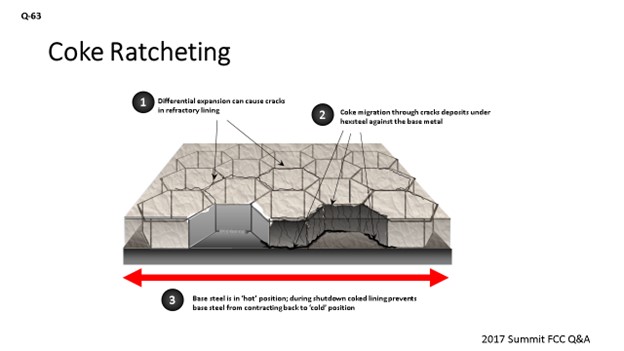
During your next thermal cycle, when the material returns to the ‘hot’ position, it may be slightly longer. The stresses there between the hex and the base metal then get worse, as do the cracks. Over many, many thermal cycles like this, you can eventually actually extend the base material. We have seen it in riser termination devices and in some areas of cyclones, such as in the crossover areas. What may also happen before you even see the elongation of the base material is that the coke will separate the hex from the base metal. You might see refractory biscuits popping out; and where there is bare metal exposed, you will then see some severe erosion.
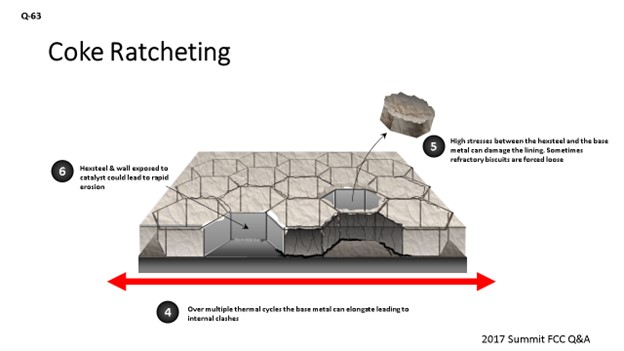
At TechnipFMC, we recommend that all hex in the reactor service be 100% welded pattern to the base material to minimize the amount of annular space available for the coke to settle. We also recommend the type of hex steel that has punched tabs to help hold the biscuits in place.
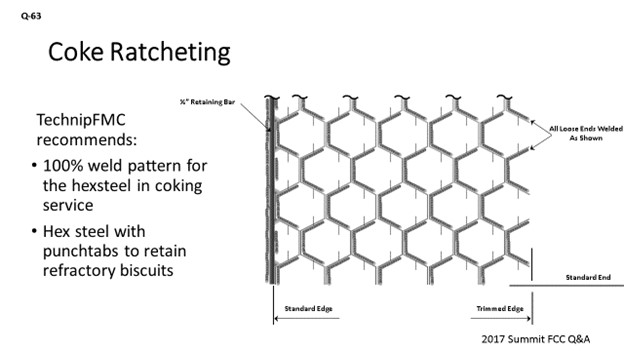
FOOTE (CHS Inc.)
I will just add that for carbon steel and 1¼ chrome as risers, we typically require some type of corrective action between 25 and 30 thermal cycles, which is where you elongate past the point that your expansion joints can handle it. We do see some coke ratcheting in our systems, but we have not had to make a replacement as a result of coke ratcheting; because typically, we only run about 60 thermal cycles on our risers and 15 to 20 thermal cycles on our reactors and stripper systems.
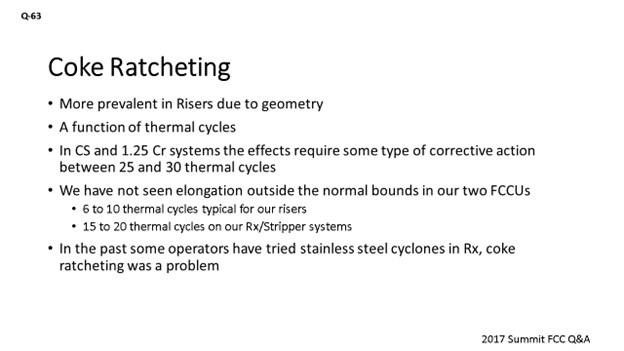
Since 2005, we have gone to the standard where we weld every hex mesh. Prior to that, we did see some lining failures due to the stresses in the cold condition. Since we started welding everything, we have had good performance.

PHILLIP NICCUM (KP Engineering, LP)
I have seen this before, and I think the proposed solution or mitigation of welding the hex steel is the right answer. However, I think that the ratcheting is really a metaphor for what, at times, is a different mechanism: vapors of light olefins – such as propylene – diffusing down into the material and forming coke. And then, it is the growth of the coke and the coke expanding that breaks off the metal. So, it does not really require thermal cycling to cause extreme damage. I have seen instances where units that have run without thermal cycling for short periods of time completely break the metal, rip off the hex steel, and break full penetration welds. It is analogous to the force that you might see with rust between two steel plates that will break the rivets or water freeze in a crack. The amount of force that can be generated by the chemical reaction of the coke forming in a spot and the diffusion of material into those areas can be tremendous.
DARIN FOOTE (CHS Inc.)
When the system is cooled down, the coke impregnated lining does not return to its original shape causing the parent metal to yield and elongate. In the cold condition, high stresses are present in the attachment welds between the hex mesh and the parent metal. This situation can lead to lining failures.
Coke ratcheting is a function of thermal cycles. In CS (carbon steel) and 1.25 Cr (chrome) base metal systems, the effects of coke ratcheting typically require some type of corrective action at 25 to 30 thermal cycles. The riser is the most prone to elongation because of its geometric configuration. However, coke ratcheting can occur in any coking environment. At CHS, we monitor for riser elongation but have not seen elongation outside the normal range of expansion for our counterweights and expansion joints. Nevertheless, we typically only run six to 10 thermal cycles between riser replacement and 15 to 20 thermal cycles between reactor/stripper replacements. In the past, some operators have tried stainless steel cyclones in the reactor. These stainless reactor cyclones were very prone to coke ratcheting.
We have seen some liner failures due to coke ratcheting in our reactor/riser systems. For this reason, on abrasion resistant linings in coking service, our standard is to weld the full length of every hex mesh bar, as shown in Figure 1. By welding the same three sides in each hex, every bar receives an attachment weld to the base metal. Since we implemented this practice in 2005, we have had good lining performance in coking service.
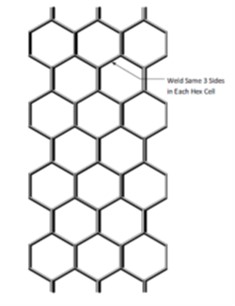
Figure 1: Hex Mesh Welding Diagram in Severe (Coking) Service
ALEX MALLER (TechnipFMC Process Technology)
Coke ratcheting occurs on hotwall refractory-lined equipment in FCCU reactor service. It impacts refractory linings with hex [hexagonal] steel anchors and can occur with a variety of base metals, including carbon and alloy steel. Whilst in the hot condition, differential expansion can loosen the refractor biscuits and provide a pathway for hydrocarbons to migrate beneath the lining and form coke in the annular space between the base metal and the hex steel. During a shutdown, this coke can prevent the base metal from contracting back to its cold position. This process, when repeated over multiple thermal cycles, can cause the effective lengthening of reactor internals. Further evidence of what is occurring is often seen as the premature failure of the lining on this equipment. As the coke is built up overtime on the surface of the steel, it will separate the lining system away from the base metal often seen as the loosening and loss of the refractor biscuits. One method used to prevent coke ratcheting is to utilize a 100% anchor weld of the hex steel to the base steel, which reduces the area beneath the anchor for coke formation to occur. Carbon diffusion into the base metal grain structure is not believed to be a significantly contributing factor. Although this phenomenon is a possibility, it only occurs in environments with temperature greater than 1100°F, and the result is the embrittlement of the base metal.