Question 60: Please describe your experience with the occurrence of phosphorus and barium fouling in the distillate section of the crude tower. What steps have you taken to identify and mitigate the problem?
WATTS (LyondellBasell Industries)
This slide contains our legal disclaimer. I am really not going to cover it in a lot of detail. [Laughter] Just use your own judgment.
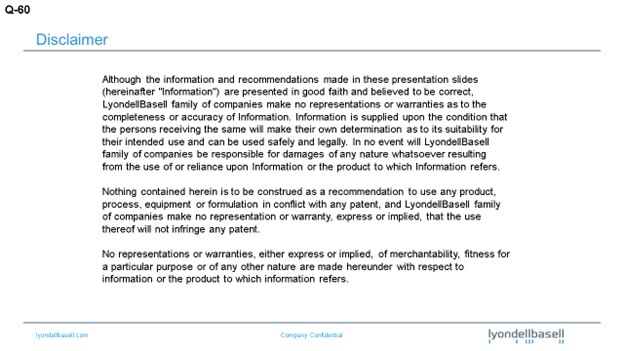
I know this topic generated a lot of discussion in our Hydrotreating session yesterday. I am mainly, obviously, going to focus on the crude side of it. I will start by saying that basically, it starts with a process to analyze processed crudes for impurities to manage and minimize fouling coming from salts, asphaltene precipitation, and other impurities.
Corrosion: Obviously, we look at TAN in the crude, organic chlorides, amines, and ammonia. We do not always do a full analysis of the crudes we are processing day in and day out, since we have a long history on those crudes. But when we are looking at new crudes, we do a more detailed analysis.
We also look for catalyst poisons mainly to make sure we do not have high levels of silica, phosphorus, arsenic, and other materials that would cause accelerated or loss of catalyst life. And then, we look at the downstream impacts on those units. But overall, our goal is obviously to manage equipment reliability and catalysts between turnaround cycles.
Last year, we took a short outage to replace a piece of equipment on one of our crude units. We were a little over five-and-a-half years into the run since the last turnaround cycle. When we started up after the outage, we saw that the top section of the crude tower dP (differential pressure) had increased to five pounds. Before the outage, it was two pounds, and that was for the top 20 trays of the crude tower. We had experience with trays fouling prior to this outage. When we would shut down the unit for turnarounds, we would see that the top six to eight trays had some fouling from salts that deposited on the trays.
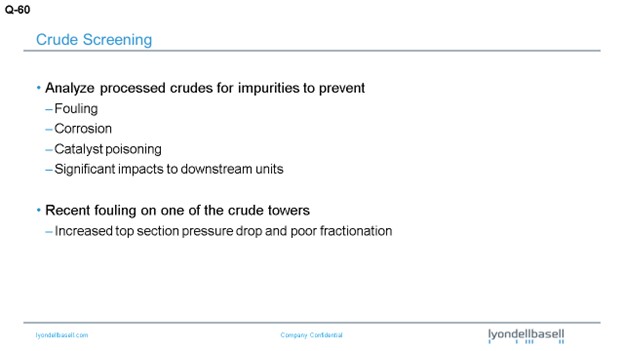
Next, we did a tower scan and also a more detailed pressure survey which showed that the liquid had started to back up in the tower just below the kerosene pumparound section. As I said, that is around Tray 20. So, as we were scanning the tower, we basically adjusted the liquid loading in the tower. We dropped the pumparound and the top reflux. Once we did that, we saw that the pressure drop returned to a normal range. The tower was no longer flooding.
Actually, prior to the outage, we had noticed an increase in fouling in our kerosene pumparound exchangers. We talked to some of the operators after we saw the increase in the tower top pressure drop. We also had some issues with valves closing when they were isolating the kerosene pumparound exchangers. So, we did an analysis of that stream; and basically, we saw a combination of corrosion products and hydrocarbons. We also saw trace levels of phosphorus as high as 800 ppm (parts per million). As I said, this occurred in April of 2014. We have continued to run the crude tower.
To manage this increased pressure drop and fouling, we have adjusted our kerosene pumparound. Before April of last year, we typically ran that pumparound at a rate of 1,300 barrels per hour or higher. Currently, we are running the pumparound at the minimum, which is 750 barrels per hour. So obviously, our kerosene production has dropped off. We have also lowered our top reflux in the tower and adjusted the heater outlet temperature and stripping steam to the tower to reduce the vapor load for certain crudes.
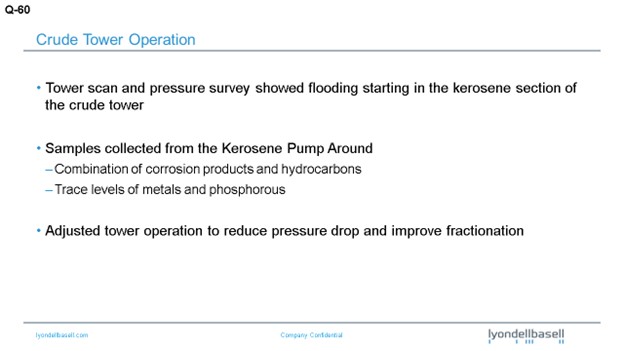
We have a planned outage for the first quarter of 2016 as it will have been a little over seven years since the last turnaround. We worked with a company to redesign the trays, so we plan to replace the trays. During the outage, we will also be able to verify the fouling.
BRADEN (NALCO Champion)
We have conducted deposit analysis on samples in the jet kero (kerosene) trays and found that the phosphorus component in the deposit, along with the iron and sulfur. The phosphorus usually comes from an upstream additive that is used in the fracking aspect of water-sensitive clay formations. They use a mono- and diphosphate ester to help with the fracking process that can be complexed with an inorganic material and removed from the crude oil. During the manufacturing of the mono- and diphosphate esters, a triphosphate ester is also formed which is oil-soluble and cannot be complexed. The triphosphate ester is the material coming in with the crude once it passes through the desalter. But once it gets into the heat exchangers into the towers, it starts decomposing. It starts hydrolyzing to phosphoric acid. So essentially, phosphoric acid distills up tower, deposits onto the tray, and then precipitates at the jet kero trays. When the phosphorus-containing deposits increase in size, the deposits then begin closing the holes in the trays.
Some refiners will replace the trays with trays containing larger holes, therefore allowing you to get more flow in the jet because the jet fuel has a phosphorus spec. Essentially, we try to mitigate the phosphorus from distilling up the tower by injecting a chemical additive that complexes the phosphorus to keep it into the resid fraction and does not distill up the tower. So, if you want to know a little more about that, contact your chemical vendor.
WEBER [Marathon Petroleum Corporation (MPC)]
We have had some practical experience. The picture here shows phosphorus fouling of one of our crude towers. This is in the kerosene section again. The first time we experienced it in 2011, we went into a tower for turnaround and found fouling in the kero section, with none above or below. It had not caused an operational problem, and we actually did not analyze foulant that was on the tray at that time.
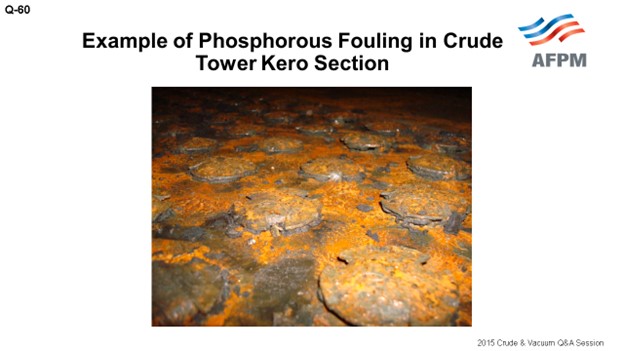
At another MPC refinery, the crude unit was reduced, for economics, for roughly a month. When an attempt was made to return the unit to full rate, flooding was observed in the kerosene section. We were referred to the Canadian Crude Quality Technical Association (CCQTA) which immediately said, “Oh yes, you have phosphorus issues.” After further discussion, it was discovered that CCQTA has extensive experience with phosphorus contamination. Their website indicates that since 1995, they have had a project on phosphorus fouling and have worked with some of their producers to help minimize it.
A similar incident occurred at a third refinery. One of the remedies we have implemented is the installation of fouling-resistant, fixed-valve trays in the kero section. In refineries that still have floating valve trays, we try to keep vapor traffic up in the kerosene section. We have found occasions where the valves were found stuck open; but fortunately, they did not cause an operational issue. It is when we got lower rates and lower velocities that the valves became stuck closed and caused flooding problems. We have also had experience with barium fouling in the wash section of the crude tower. This picture shows an example of that problem. The solution for this issue was also to install foul resistant, fixed-valve trays.
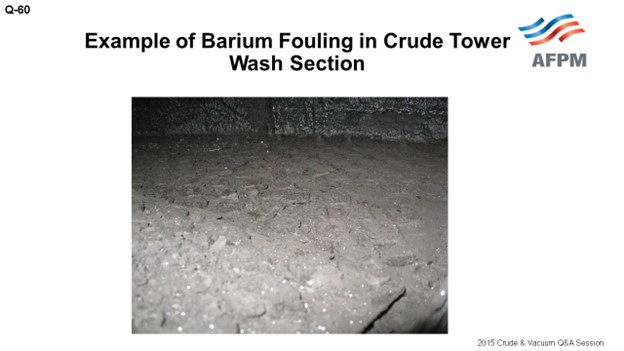
NAGASHYAM APPALLA (Reliance Industries Ltd.)
Is there an industry-accepted limit of monitoring the phosphorus in the crude oil? If so, does anyone distinguish the differences between volatile and non-volatile phosphorus?
WATTS (LyondellBasell Industries)
I want to echo some of what John said. I did quite a bit of research on this and know that it is not a new issue. I think the slides I found were from the mid-1990s, and the specification levels I saw were 1 to 1.5 ppm. But based on our working with our lab, we have not seen a detectable level of phosphorus on the crudes we have analyzed. We have not traced it back to a crude source.
BRADEN (NALCO Champion)
In our experience, the phosphorus compounds enter the refinery via the crude and normally come in slugs because of the fracking issue; and therefore, it can be up to 50 parts per million when you get a slug of phosphorous material. But in our measurements of it, it is normally 1 to 3 ppm. We have run that by ICP (inductively coupled plasma) analysis. So it is normally very, very low if it is in there. But sometimes, you do get slugs. Then when do you catch a slug? When do you see that? You just see the results of the slug coming through. It is hard to pick up.
NAGASHYAM APPALLA (Reliance Industries Ltd.)
What is the industry’s experience on the cause of this fouling when using high temperature corrosion inhibitors in atmospheric tower?
SAMUEL LORDO (NALCO Champion)
The inhibitors that are used for high temperature treatment are not really part of that particular description. As Mike indicated, those are triester compounds which come in with some of the fracking gels that are used in Western Canada or in clay formation-type crudes where they are water-sensitive. In the lower 48 though, there is no fracking with phosphorus-based gels. Now we are targeting to look at phosphate esters being used for scale control and corrosion inhibitors.
I looked at one complete year of a refinery’s crude tracking where they analyzed for phosphorus the entire year on each batch that came in. Most of it was in the 1 to 3 ppm range; except in November, it shot up to about 10 to 15 for a one-month period. And then, it came right back down. During that timeframe, their tower had some issues which have not yet been resolved. So they will have to come down and clean it. But as far as the inhibitors go, most of them do not cause a problem. If you overtreat, then yes, you can have some issues.
PRICE (Fluor Corporation)
Just a comment to the Mr. Appalla from Reliance: If you have not visited the CCQTA website, I recommend that you do because it contains is a lot of information about lab methods that might be helpful.
NAGASHYAM APPALLA (Reliance Industries Ltd.)
Yes, but the CCQTA only talks about the phosphorus coming from the Canadian crudes. Suppose you are not processing Canadian crudes. What are the other sources of it?
HAROLD EGGERT (Athlon Solutions)
It is an odd question when you say barium and phosphorus in the same sentence. Why would you pick those two particular elements to examine? Like Sam, and I think the panel, have mentioned, not all phosphorus is going to end up fouling your trays. It is always coming in at a low level. Some of it is benign phosphorus, and some of it will contribute to tower fouling. What is currently being used – and the reason the barium came up – is that the phosphorus causing some of these problems is injected to prevent barium sulfate scale upstream. It is a scale inhibitor. If you see barium and phosphorus, chances are it is from the production chemicals. The barium used to be called NORM: Normally Occurring Radioactive Material. That is why we are looking for phosphorus and barium. It is the combination of the two that sends up a red flag.
JEFFREY ZURLO (GE Water & Process Technologies)
Just to clarify, you are right. The CCQTA talks about phosphate esters from Canadian crudes. One of the test methods they have on their website specifically identifies volatile phosphates. The CCQTA test separates the volatile phosphorus components from just the general phosphate components by performing a distillation on the whole crude and analyzing the middle distillate cuts. Although the CCQTA work is done on Canadian crudes, the source of the crude oil really does not matter. What is important is if phosphate is in the crude; if it is volatile; and, if it can hydrolyze, complex, and form this fouling material. So, it is not necessarily the source but more the effect of what type of phosphate is in the system.
BILLS CATES (Hunt Refining Company)
If I understood the question, what Mr. Appalla is really asking is: Other than light tight oils, where are they finding crudes containing phosphorus? He just really wants to know what crude; he does not want to buy. [Laughter]
WATTS (LyondellBasell Industries)
I mentioned earlier that we have not traced it back to its source, at least in our refinery.
BRADEN (NALCO Champion)
The phosphate esters for the fracking are mainly coming from the Canadian side, the north coast of North America, and the south coast of Canada.
JESSICA NAQUIN (Valero Energy Corporation)
I have heard rumblings that the fouling would have less affinity for metallurgies. For example, if you have carbon steel or different variations of stainless trays or parts in the tower, sometimes the phosphorus fouling will not have the same affinity; so then, you will not have the same accumulation of the fouling in the tower. Does anyone have experience with those observations and any Best Practices?
WATTS (LyondellBasell Industries)
I do not have experience on the metallurgy. I would say that what we are doing is similar to what John said in that we redesign the trays to go to a fixed valve. So, we avoid the potential – if you turn down, increase, or shut down a unit – of your valve getting locked in place; that is, if you have a floating valve. Obviously, that changes your flexibility on how you can run the crude unit when you turn down rates.
PRICE (Fluor Corporation)
Once again, I am not an expert on this subject. Based on the experience of our clients, I think the jury is still out on the subject of phosphate fouling. People are finding, in some cases, that when they solve the fouling problem in their crude tower, the fouling problem migrates downstream to the exchanger. While exchanger fouling is not a good problem, it is solvable. If you can then install a bypass and if you have the ability to do online cleaning of that exchanger, it will help to mitigate the impact on your unit throughput.
RALPH WAGNER (Dorf Ketal)
Fouling in the distillate section of the crude tower due to phosphorus is rising globally. A primary likely cause is the result of phosphorus-containing chemicals used in oil exploration and production. However, in recent surveys, several of the fouled towers have employed naphthenic acid corrosion inhibitors which have contributed to the problem.
The corrosion inhibitors contain phosphorus, and most products are thermally unstable and contribute foulants to the system. A Best Practice is to use a thermally stable inhibitor containing a phosphate triester. This type of corrosion inhibitor can withstand processing temperatures and does not contribute to phosphorus fouling. By comparison, mono and diphosphate esters are prone to thermal degradation; products of decomposition contribute to phosphate fouling.
For barium, we have observed issues in desalters, preheat exchangers, and towers due to presence of barium in the crude. The presence of barium appears to depend on geographic location and how the well has been fractured. Bentonite clay used in oil well fracturing contains barium, and poorly fractured wells may allow this clay into the crude. Barium is not soluble in oil or water, and the small particle size leads to accumulation in the rag layer in the desalter. Steps to mitigate barium accumulation include the reduction of pH and the optimum selection of desalting chemicals and mechanical adjustments for minimizing rag layer.
JOHN WEBER [Marathon Petroleum Corporation (MPC)]
MPC has experienced fouling in the kerosene section of crude units at multiple refineries which has been attributed to phosphorous. The first documented occurrence was found in 2011 during inspection of the tower during a unit turnaround. A light crusty scale was found on the trays in the kerosene section with no fouling in the sections above or below. Although this scale was not analyzed, subsequent incidents support phosphorous as the culprit.
A second occurrence followed an extended rate reduction at another refinery. When the refinery attempted to return to maximum rates, they were limited by flooding in the kerosene section. The MPC Crude Quality Manager at the time had heard of similar issues and referred the crude technologist to the Canadian Crude Quality Technical Association (CCQTA). The CCQTA representative suggested phosphorous fouling as the potential problem based on experience with other refineries. An attempt to remove phosphorous with online chemical treatment showed some effectiveness, but the unit was ultimately taken down to clean out the fractionator concurrent with a planned turnaround. The valves on several trays in the kerosene section were found to be stuck closed, which caused the flooding issues in the tower (See Figure 1). Analysis confirmed phosphorous as a major component of the foulant. Similar fouling has been found in one other refinery on inspection, however the valves were stuck open versus closed and did not impact operation.
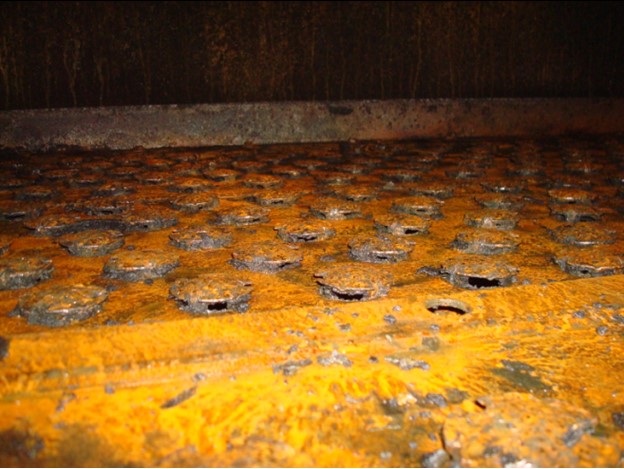
Figure 1. Example of phosphorous-induced tray fouling in crude unit kerosene section
The CCQTA website indicates that the group initiated a project in 1995 because of phosphorous-related fouling at three Canadian refineries. The source of the phosphorous was traced back to additives used in the production industry.
MPC has switched to fouling-resistant, fixed-valve trays in crude towers where phosphorous fouling is thought to be an issue. In addition, at a refinery where we have not been able to replace trays yet, efforts are made to keep traffic high in the kerosene section in the event of a rate reduction.
MPC has also experienced fouling attributed to barium at one refinery in the wash section of the crude tower (Figure 2). Fouling-resistant trays were installed to minimize fouling rate and extend time between cleanouts.
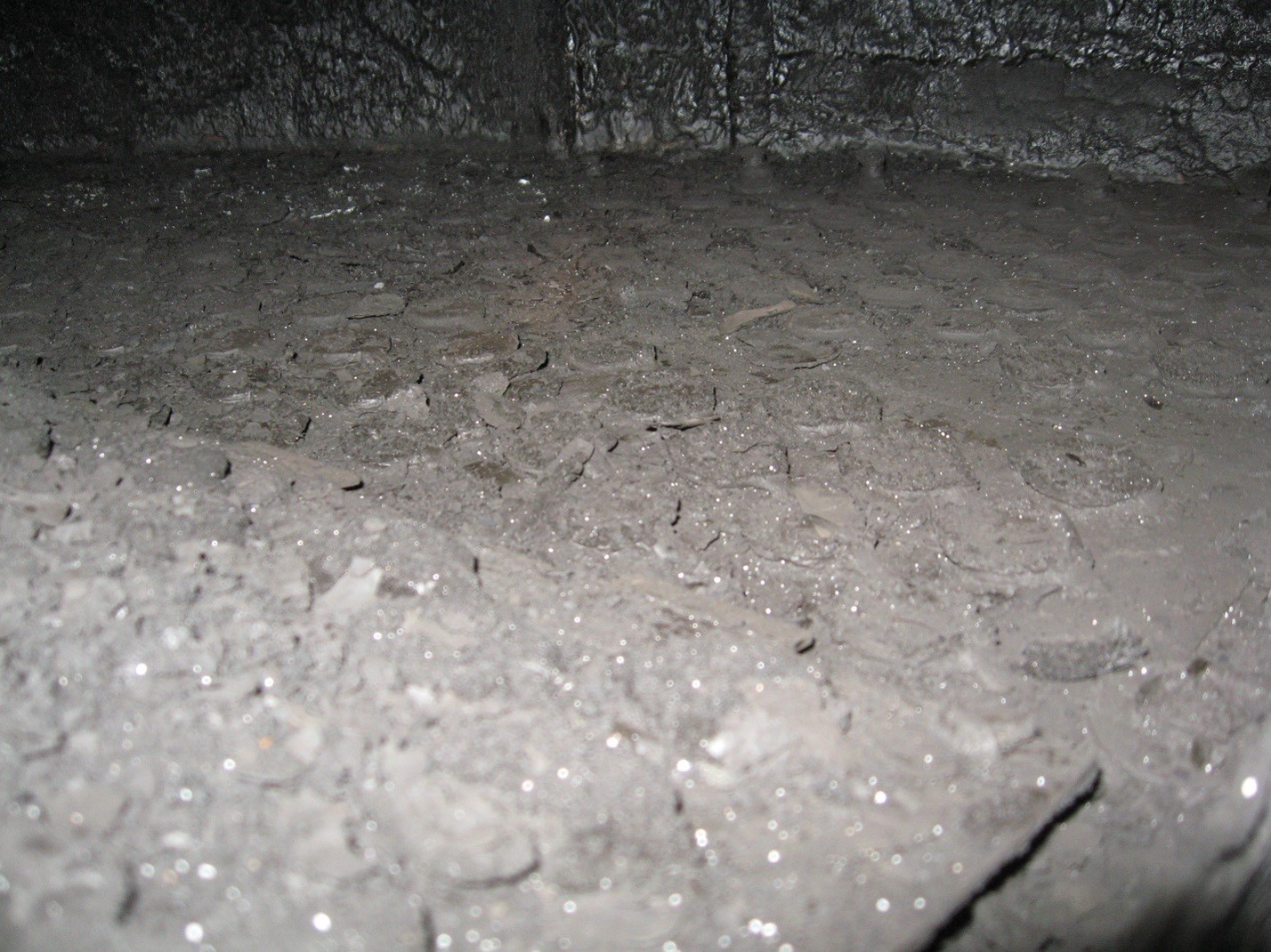
Figure 2. Barium fouling in wash section of atmospheric crude tower
MICHAEL BRADEN (NALCO Champion)
Deposit analysis of the jet/kerosene trays in the distillation towers has shown that phosphorus can be a component in association with sulfur and iron. The phosphorus usually results in the use of a chemical additive in upstream applications, such as a part of a corrosion inhibitor, or present in downhole fracking fluids. Phosphorus-containing additives are also used as fouling inhibitors for barium sulfate.
The downhole applications use mono- and diphosphate esters that can be removed by coagulation via inorganic chemicals. Unfortunately in the manufacturing process, triphosphate esters are also formed, are oil-soluble, and cannot be removed by the coagulation mechanism. Thus, the triphosphate esters move through the refinery’s desalters and are in the crude entering the distillation towers. At this point, the higher temperatures begin to hydrolyze the triphosphate esters converting to it to phosphoric acid, which then distills up the tower and condenses at the jet or kerosene sections. The acid reacts with the iron and sulfur causing corrosion to occur. Overtime, the deposit is large enough to block the holes in the trays. At this point, the tower needs to be shutdown to remove the deposit.
There are chemical additives which are used to complex the phosphoric acid generated and keep the phosphorus in the resid. Please consult your chemical supplier.
Another method to mitigate the fouling is to install trays with larger holes; although this will not decrease the fouling, it will lengthen the run time for the tower.
EDWIN WATTS (LyondellBasell Houston Refining)
It is important for refineries to have a rigorous program to analyze crudes, particularly new crudes, for impurities that will cause issues on the crude or downstream units. Recently, we experienced fouling in the kerosene section of one of the crude units. A sample from the kerosene pumparound exchangers showed a combination of hydrocarbons and corrosion products. There were trace levels of metals and phosphorous. We have made adjustments to unload the top section of the tower to minimize flooding, reduce pressure drop, and improve fractionation. We will verify the fouling mechanism during an upcoming turnaround.
MAUREEN PRICE (FLUOR)
Phosphorus originates mostly from secondary recovery processes and causes severe fouling in the jet pumparound (both trays and exchangers), jet product route (exchangers), and in the jet-diesel fractionation section. There have been problems with some Canadian and fracked crudes, as well. Fouling-resistant trays, such as PROVALVES, have been effective (at least in some cases) in alleviating the problem in the tower but have aggravated the problem in the exchangers. Bypasses permitting cleaning exchangers when the plant is running have been very useful, but beware of design conditions. It is difficult to predict the offending crudes as the amount of phosphorus is usually small in them. The deposits often show 10 to 50% phosphorus. However, one Southern California refiner who runs 20% Canadian crudes has no evidence of any phosphorus fouling. Barium fouling has been experienced by another client.
CCQTA has established a limit of maximum of 1.5 ppm volatile phosphorus after conducting research. Their website has a large amount of information available, including test methods.