Question 6: Following an emergency shutdown that includes the loss of the recycle gas compressor, is it possible to quantify the effect on catalyst deactivation? What are the Best Practices to minimize catalyst deactivation?
ESTEBAN (Suncor Energy, Inc.)
This picture shows my favorite compressor at the refinery. She and I have a love/hate relationship. We installed a gas oil hydrotreater in 2006, a new unit with this compressor, and we have a great deal of experience with emergency shutdowns. In fact, the unit has shut down over 60 times in the last six years; so if you do the math, it is once a month. I have had the personal pleasure of being both an operator on the unit and an engineer for the unit, and then revamping it while still dealing with all of the compressor shutdowns. So, for us, that has offered some learnings and some struggles as well.
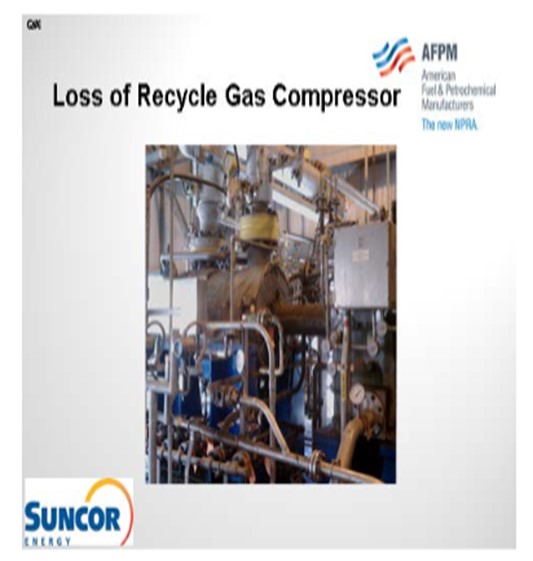
The primary impacts of loss of hydrogen circulation or flow. If you have a once-through unit are obviously loss of catalyst activity and increased reactor pressure drop. In some cases, you do not notice that these are occurring; so, at the start-of-run, you have excess void space and excess activity in the reactor. The same event may cause an increase in pressure drop, an increase in coke in the reactor, or a loss of active sites in the catalyst or access to active sites. You cannot really tell until you get closer to the end-of-run. As a result, we have experience seeing step changes in pressure drop and catalyst activity as a result.
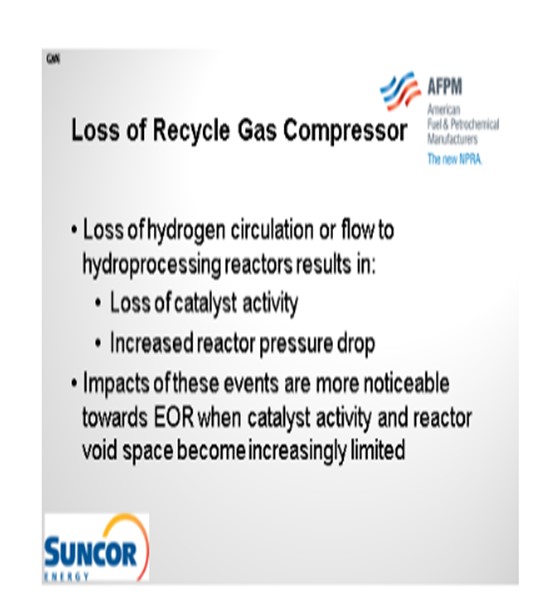
At Suncor, we have found several effective methods for minimizing the impact of loss on our hydrogen recycle gas compressor. First, we stop the flow of feed and depressure the reaction section. This action clears as much of the oil off of the hot catalyst as possible to avoid coking reactions that occur in low hydrogen partial pressure environments.
Secondly, we obviously attempt to restore hydrogen quickly to halt coking reaction in order to restore the circulation of hydrogen. For obvious reasons, this is the most advantageous action because it allows us to sweep the oil off of the catalyst and restore the hydrogen partial pressure; in addition, we can prevent liquid from pooling the reactor.
Third, we sweep reactors in extended outages and bottle up with nitrogen. So in the event that hydrogen cannot be restored quickly, the reactor should be swept by whatever means to the flare to clear as much oil from the catalyst as possible and then bottled up. At Denver, our high pressure units have integrated hydrogen circuits. While they are separate in operation, we also have an integration line between them. We just call it the ‘sweep gas line’, which is exactly how it is used: to sweep the reactor when it shuts down every month.
Lastly, where we have really gained a lot of experience and understanding is by using the flushes and sweeps recommended by catalyst manufacturers. Every manufacturer will have its own separate procedures on how to perform the flushes and sweeps. The hot strips – and then diesel and LCO (light cycle oil) flushes – are actually very effective in minimizing the impact of a loss of recycled gas event, although they do not completely mitigate the issue.
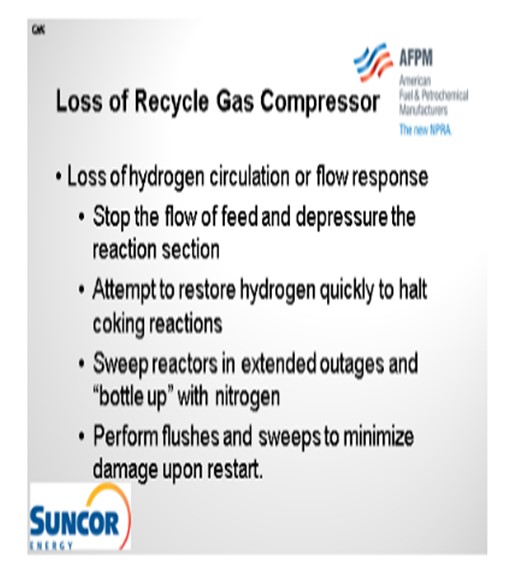
CARLSON (Criterion Catalysts & Technologies)
First of all, when discussing the response to an emergency situation like a recycle gas compressor, remember that not every unit or situation is the same. Care should be taken when applying any changes to existing procedures.
Following an event like a loss of the recycle compressor, it is, of course, important that the on-hand procedures provide a safe and reliable process for taking a potentially unsafe, undesired situation to a safe position. While consideration of HS&E (health, safety, and environmental) and equipment protection are key, a few additional steps in the procedures can minimize the potential of further lost opportunity due to any resultant catalyst damage.
Our response is a little bit different depending on whether it is a hydrotreating or hydrocracker application. For conventional hydrotreating applications (alumina-based catalyst systems), the first step is to remove heat from the reactors. This elimination involves tripping the furnace and removing any highly exothermic cracked stocks. By leaving the feed pumps on and maintaining makeup hydrogen, if possible, reactor temperatures will often begin to drop, thereby minimizing the incident. If the recycle compressor can be restarted within a short period of time, less than 15 minutes, then the impact on unit operation should be minimal. If exotherms continue to climb and do not show signs of stabilizing, then controlled depressurizing of the reactor will return the unit to a safe condition. Of course, this will trip the feed pumps and makeup compressor, initiating the sweeping of the reactants from the unit.
If the recycle compressor cannot be restarted within a short period, we recommend continuing cooldown to less than 400ºF and then following your procedures to depressure the unit to a safe holding condition.
Following the completion of any required maintenance, the start-up procedure should include steps to perform a warm diesel flush and possibly a hot hydrogen strip.
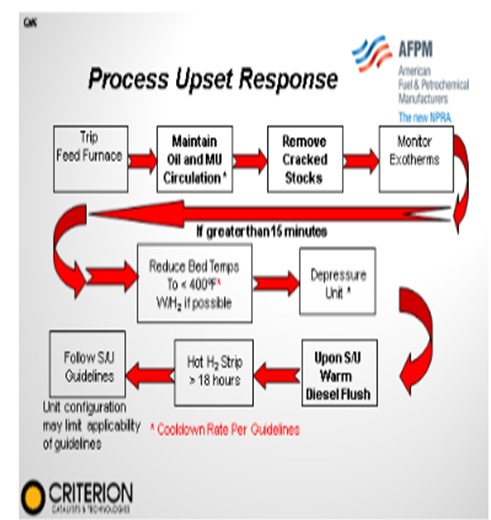
In the Answer Book, I have included a list of steps to consider when performing a restart after an extended unit trip. A key consideration during these types of unit responses is to take steps to minimize the exposure of the sulfide catalysts to a reducing environment. This means that when temperatures are above 450°F to 500°F, we need to ensure that H2S is present. Again, it is particularly important when doing the hot hydrogen strip that during the restart, you confirm that no pure hot hydrogen is being circulated. That, in and of itself, can have negative impacts on the catalyst.
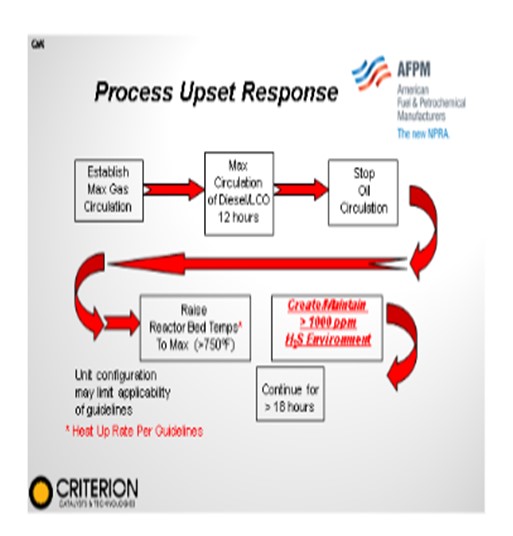
This next slide contains a lot of text that summarize the steps we recommend for hydrocracker operations. In the Answer Book, we cover the material in more detail. For hydrocracking applications, we have a further consideration for units with cracking catalysts. We advise that gas and liquid feeds be removed from the unit and that a low-rate depressurization be used to begin the sweep of reactants from the unit immediately following the trip.
After taking the unit to a safe condition, the obvious question arises about the impact on the catalyst. While the only way to evaluate and quantify catalyst condition is with a post-restart operational test run and pulse test, some qualitative indications of catalyst condition can be made prior to a restart, including:
•Time at temperature of the catalyst beds
•Hot spots observed during the event and subsequent cooldown
•H2S presence if temperature is greater than 500ºF
•Transient review of temperatures during cooldown
•review of procedure response
The other consideration is the point we are in the operational cycle. At SOR (start-of-run), the units tend to bounce back well; but if we are late in the cycle where the operating temperature is higher and contaminant loading has already elevated, then the impact of these trips tends to be felt more.
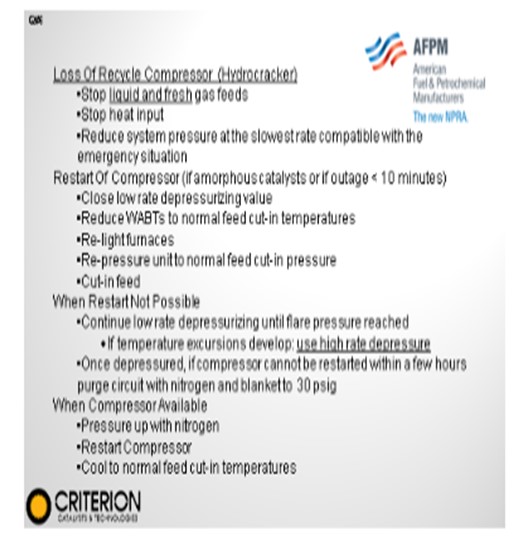
SERGIO PIMENTEL (CITGO Petroleum Corporation)
If feed is removed from the unit, it is recommended to immediately shut down the amine column, if you have amine circulations, to preserve H2S in the system. But if that trips the recycle compressor, then you might not want to do it because you would probably be depressurizing the unit quickly to a fuel gas system or to a flare. Hydrogen is not coming back to the reactor, so you should leave the amine column running.
CARLSON (Criterion Catalysts & Technologies)
That is correct. It is important to remember that if your beds are still at elevated temperatures upon unit restart, then we will again need to protect the catalysts from potential hydrogen reduction. In this case, we recommend that upon the restart of the recycle compressor, the amine system should be kept out of service to allow the H2S content to build up in the recycle circulating gas to prevent possible reduction.
SUBHASH SINGHAL (Kuwait National Petroleum Company)
We do it differently at KNPC. When there is loss of a recycle gas compressor, we keep the liquid feed going in and use this as a cooling media after reducing the hydrogen partial pressures and bringing down the temperatures. Liquid feed is used as a cooling media.
CARLSON (Criterion Catalysts & Technologies)
Right. That was what I mentioned on the first slide. For conventional hydrotreating applications, if it is just alumina-based catalysts, we recommend that you leave in your straight run feed. You will want to pull your cracked feeds; but yes, you can cool down your reactors on a conventional hydrotreating unit with straight run feeds. It is just in hydrocrackers that we suggest removing all feeds.
SUBHASH SINGHAL (Kuwait National Petroleum Company)
I think a lot of those hydrocrackers are not straight run feed. The hydrotreated feed from it mostly exists at desulfurization. We still keep in the liquid feed, and that has been quite effective.
CARLSON (Criterion Catalysts & Technologies)
Exactly, and you will see a lot of variations on the practices within the industry.
LEICHTY (Chevron USA, Inc.)
At Chevron, we have concluded that it is always better to leave feed in the reactor upon loss of recycle hydrogen, regardless of whether it is a hydrotreater or hydrocracker. The basic premise is that without recycle hydrogen or feed, there is almost no flow through the reactor to carry away heat. Also, reactor temperature indication is stagnant, and there is a higher probability of undetected localized hot spots that could lead to a temperature excursion. If feed is left in the unit, excess heat in the reactor has a medium to be carried away, thereby minimizing the potential for de-methylation-type hydrocracking reactions and temperature excursions. In addition, with the flow in the unit, operators have a better picture of what is thermally happening in the reactor, which enables them to quickly respond to a temperature excursion by depressuring the reactor.
ESTEBAN (Suncor Energy, Inc.)
For units equipped with a recycle gas compressor, it is one of the most critical pieces of equipment; and as such, an emergency shutdown of this critical piece of rotating equipment can result in significant adverse impacts to unit operation and catalyst performance. Similarly for units without recycle streams that operate in once-through fashion, the loss of hydrogen flow to the reactor can have the same detrimental impacts. The primary concern with the loss of recycle gas or the loss of hydrogen flow to the reactor in general is the potential for coking due to the presence of oil on hot catalyst with significantly reduced hydrogen availability partial pressures. The result of coking can be seen both in a loss of catalyst activity and ultimately an increase in reactor pressure drops. Given the nature of the emergency and the state of the unit before and after a shutdown, it is possible to determine the impact on catalyst activity once the unit is brought back online and is in stable operation.
The Suncor Energy, Inc. Denver Refinery has a great deal of experience with loss of recycle gas compressor events on a gas oil hydrotreater. The recycle gas compressor has seen very poor reliability primarily due to electrical issues related to the variable frequency drive unit that is used as the driver for the compressor motor. On average once a month this machine and subsequently the entire unit experience a complete shutdown. While some efforts have been successful in improving the compressor’s performance it remains one of our big rocks. However, on a positive note the experience gained from these events has provided us with supporting data to confirm our Best Practices. Typically, most trips early in a catalyst run do not appear to be as detrimental to reactor performance as those later in the run due to the excess void space and catalyst activity available. It is possible to see the impact from these events on catalyst activity simply by comparing the normalized reactor weighted average bed temperature (WABT) prior to and post shutdown, but it is our experience that noticeable step changes in WABT are more pronounced and noticeable towards the end of run. In conjunction with catalyst activity the effect on reactor pressure drop is also more noticeable towards the end of run. Both catalyst activity and reactor pressure drop are related here because loss of activity is a direct function of the formation of pressure drop due to coking and sloughing of materials from upstream equipment.
In order to minimize the impacts of loss of hydrogen events our experience has shown that the following Best Practices are effective:
1. During a loss of hydrogen event immediately stop the flow of feed oil to the reactor and depressure the high-pressure circuit to aid in sweeping oil from the reactor. It is critical to depressure quickly and at an adequate rate to sweep the oil off the catalyst and with a properly designed system it is possible to sustain minimal catalyst activity loss.
2. Attempt to restore the flow of hydrogen first following the event to provide cooling to the reactor, as well as increase hydrogen availability halting coke formation.
3. Given extended outages sweep the reactor as best as possible without stripping catalyst, potentially with the use of makeup hydrogen or integrated hydrogen streams from other units. The most effective way to sweep the reactor while minimizing catalyst stripping is to pressure up and depressure the high-pressure circuit a few times. Following a sweep, the reactor should be “bottled up” with a nitrogen blanket.
4. Upon restart of the unit it is effective and advantageous to perform the flush and hot sweep procedures recommended by many catalyst manufacturers to reduce pressure drop accumulation. Our experience has shown that performing a diesel/ light cycle oil (LCO) flush upon restart of our gas oil hydrotreater has resulted in smaller step changes in both reactor pressure drops and catalyst activity following shutdown events. (It is important to note that caution should be taken prior to reintroduction of feeds to monitor reactor temperatures closely identifying hot spots and non-uniform profiles which may indicate the potential for reactor walk/ run away.)
CARLSON (Criterion Catalysts & Technologies)
When considering a response to an emergency shutdown it must be mentioned that not all situations or units are alike, and care should be taken when applying any changes to existing procedures.
Following an emergency event such as a loss of recycle compressor it is of course important that the procedures on hand provide a safe and reliable process for taking a potentially unsafe undesired situation to a safe position. While HS&E consideration and equipment protection are key; and while all circumstances are not the same, a few additional steps in the procedures can minimize the potential lost opportunity due to catalyst damage. For conventional hydrotreating applications, Criterion suggests the following approach be incorporated into existing operating procedures for conventional hydrotreaters to mitigate the loss of a recycle compressor.
For conventional hydrotreating applications (alumina-based catalyst systems) the first step is to remove heat from the reactors. This involves tripping the furnace, and removing high exothermic cracked stocks. By leaving the feed pumps on and maintaining makeup hydrogen, if possible, reactor temperatures will often begin to drop.
If the recycle compressor can be restarted within a short period of time (less than 15 minutes), impact on unit operation should be minimal. If exotherms continue to climb and do not show signs of stabilizing, then controlled depressurizing of the reactor will return unit to safe condition. This will of course trip the feed pumps and makeup compressor, sweeping the reactants from the unit. If the recycle compressor cannot be restarted within a short period, we recommend continuing cooldown to less than 400°F and following your procedures to depressure unit to a safe holding condition.
Following completion of any required maintenance, the start-up procedure should include steps to perform a warm diesel flush and possibly a hot hydrogen strip.
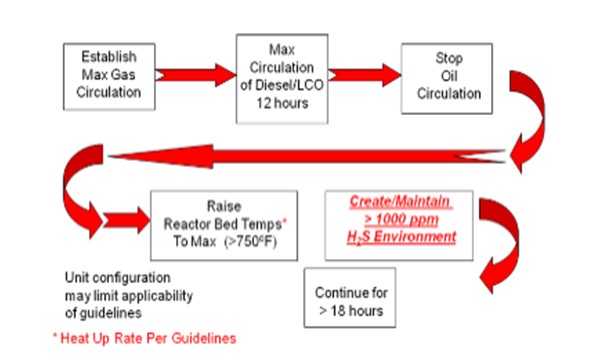
A hot hydrogen strip can be beneficial in minimizing impact on the catalyst by removing soft coke/coke precursors that may have thermally condensed on the catalyst due to elevated temperatures and low hydrogen partial pressures.
For hydrocracking applications, we have further considerations. For units with cracking catalysts, we advise that gas and liquid feeds be removed from the unit and that a low-rate depressurization be used to begin the sweep of reactants from the unit.
Loss of Recycle Compressor:
•Stop liquid and fresh gas feeds.
•Stop heat input.
•Reduce system pressure at the slowest rate compatible with the emergency situation.
Restart of Compressor (if amorphous catalysts or if outage less than 10 minutes
•Close low-rate depressurizing value
•Reduce WABTs to normal feed cut-in temperatures
•Re-light furnaces
•Re-pressure unit to normal feed cut-in pressure
•Cut in feed
When Restart Not Possible:
•Continue low-rate depressurizing until flare pressure reached
•If temperature excursions develop, use high rate depressure
•Once depressured, if compressor cannot be restarted within a few hours purge circuit with nitrogen and blanket to 30 psig (pounds per square inch gauge)
When Compressor Available:
•Pressure up with nitrogen
•Restart compressor
•Cool to normal feed cut-in temperatures
Following the taking of the unit to a safe condition the obvious question of the impact on the catalyst arises to help in planning the return to normal operations. While the only way to evaluate and quantify catalyst condition is with a post-restart operational test run and pulse test, some qualitative indications of catalyst condition can be made prior to a restart, including:
•Time at temperature of the catalyst beds,
•Hot spots observed during the event and subsequent cooldown,
•H2S presence, if temperature greater than 500°F,
•Transient review of temperatures during cooldown,
•Review of procedure response, and/or
•Evaluation of unit condition prior to event.
SUBHASH SINGHAL (Kuwait National Petroleum Company)
The catalyst may coke up if the temperature run away is not controlled. In many severe cases, the reactor internals may get damaged. In a high pressure unit like the hydrocracker, if the recycle gas compressor trips, you must ensure that the heaters are cut off and feed is maximized to cool the catalyst beds before you start reducing system pressure to control reactions.
GEORGE ANDERSON (Albemarle Corporation)
It is possible to precisely quantify the effects of an emergency shutdown on catalyst deactivation after restarting the unit, but it is not possible to accurately predict the quantified effects prior to restart. At best, some directional assessments can be made based on the conditions in the unit before, during and after the shutdown. To quantify the effects of the emergency shutdown on catalyst deactivation, you need to have a reliable baseline on catalyst activity and deactivation profile prior to the shutdown and you need to assess the lined out unit performance (preferably with the same feed and operating conditions) giving the same product properties after restarting the unit. Normalization techniques can be used to make corrections back to the baseline operating conditions if necessary. The HDS, HDN, HDA (hydrodealkylation), HDM (hydrodemetallization), and conversion functions can all be affected differently by an emergency shutdown.
Best Practices for minimizing catalyst deactivation in hydrotreaters is usually not appropriate for use in hydrocrackers due to safety considerations. The discussion below ONLY applies to hydrotreaters operated without any conversion (hydrocracking) catalyst. Hydrocracker shutdowns require special considerations. Consult your hydrocracker licensor and hydrocracking catalyst supplier.
To minimize catalyst deactivation, you would like to avoid emergency shutdowns altogether. However, to the extent that this is not possible, the best alternative is to manage a controlled shutdown. In general, to minimize deactivation, you want to minimize coke creation conditions in the hydrotreater. Depending on the circumstances of the shutdown, the actual response will vary, but maximizing hydrogen partial pressure, minimizing temperature, and removing coke precursors are directionally the correct course of action. Feed should be stopped. Furnaces should be turned off. To maximize partial pressure, makeup hydrogen should be added to the extent possible. If hydrogen flow is completely lost, minimizing loss of hydrogen already in the unit is important. If temperatures rise or hot spots develop, it may be necessary to depressure. If possible, when reactor temperatures reach about 570°F (300°C), a lighter feed should be used to remove any condensed aromatic species (soft coke) from the catalyst. When 480°F (250°C) is reached liquid feed can be stopped and the reactor can be further cooled with makeup gas. After the minimum unit temperature is reached, the unit can be depressured.
When restarting the unit, whether from a controlled or uncontrolled shutdown, it can be helpful to basically reverse the controlled shutdown procedures noted above. The reason is to start up the unit with a lighter feed and then run the treat gas at maximum rate to react as much soft coke as possible. Once the unit has begun running on typical feed, standard unit monitoring procedures can be applied to assess the impacts of the shutdown on catalyst activity and stability. If activity loss from the shutdown is excessive, a hot hydrogen strip may be able restore some performance.
One final note to keep in mind is that the amount of deactivation a catalyst will incur from an emergency shutdown is highly variable and depends on the process application, the feed being processed, the operating conditions, product specifications/targets, the specific details of what occurs during the shutdown and restart, the catalyst properties, and where the unit/catalyst were in their life cycle.
ROBERT WADE (Advanced Refining Technologies, Worms, Germany)
Reducing reactor temperature and sweeping with H2 will help minimize deactivation due to coke formation. ART recommends that for loss of the recycle gas compressor cold feed should be used to reduce reactor temperature below 400°F. In addition, make up hydrogen should be used to sweep the reactors. If the recycle gas compressor cannot be recovered within an acceptable period, then the feed should be pulled once the reactor temperatures are reduced below 400°F, and the reactor should be swept with make up H2 to remove residual liquid. This sweep should continue until the recycle gas compressor is recovered and feed is reintroduced. If the shutdown will be prolonged, then the reactor may be parked under N2 (nitrogen gas) below200°F.
A comparison of reactor temperature at the same conditions and severity using the same feed should be performed to quantify the amount of catalyst deactivation. If this is not possible, then previously established normalization parameters may be used to make a reasonable comparison of reactor temperatures before and after the emergency shutdown.
A hot H2 strip may also be performed once the recycle gas compressor is restarted to recover activity; however, this has a limited ability to recover all of the catalyst activity and is highly dependent on the current and prior operation conditions and stability.
BRIAN WATKINS (Advanced Refining Technologies)
There are two main types of acidic renewable “distillates” available. Triglyceride-based (animal fats or vegetable oils) or pyrolysis oils to be considered when co-processing is an option at the refinery. Grace is leading development of technologies to be utilized for the process of either of these types of oils in a petroleum refining environment.
Triglyceride-based oils derive their acidity mainly from free fatty acids in the oils. The level of impact of corrosion on processing equipment will depend on the type of feedstocks (animal fats or vegetable oils) and their level in the overall blend going to the refinery processes. To evaluate co-processing of these oils in a hydrotreater, several other factors must be understood as well:
•Triglyceride-based oils have a new suite of metals contaminants. They are typically lean in nickel and vanadium but very rich in calcium, magnesium, phosphorous, and other transition metals. Left unchecked, these metals can have a strong detrimental effect on the catalyst bed. Advanced Refining Technologies has studied the treating of these oils extensively and recommends a pretreatment system to remove metals. Guard beds have been suggested, but the suitability of a guard bed depends on its size and the amount of oil to be processed; it is likely to require bed replacement much sooner than a typical VGO hydrotreating guard bed. The combination of a separate pretreatment system and an in-situ guard bed is typically the approach preferred for commercial operation.
•Triglyceride oils also typically contain between 10 wt% and 15 wt% oxygen. The removal of this oxygen creates a high level of water, carbon dioxide, and carbon monoxide, and due to the higher oxygen concentration, releases heat at a much higher rate than desulfurization of VGO. Care must be taken to ensure that the hydrotreating unit can handle additional heat release.
•Triglyceride oils release higher than typical amounts of water, carbon dioxide, carbon monoxide, and propane when hydrotreated. One must review the downstream gas system to ensure that higher volumes of these products will be appropriately handled by the existing equipment.
•In this type of system, production of carbon monoxide happens via the decarbonylation route. To minimize the production of carbon monoxide, some process conditions can be changed, including increasing the available hydrogen, and selecting a catalyst system that is designed for deoxygenation. However, if co-processing renewable stocks, these moves are likely to have an impact on the non-bio-based portion of the feedstock and must be evaluated against the reduction in carbon monoxide.
Pyrolysis oils are a wide class of oils that are produced via cooking biomass in an oxygen free environment. The level of acidity and other properties ultimately depends on the production process with a typical pH range from 2.0 to 4.0. These oils are newer to commercial markets, and experience is limited in being processed in existing refining equipment. It is safe to say that the points below do not apply to all commercially available oils; however, the following points should be considered:
•These oils are typically very hydrogen deficient, and the average molecular weight can be quite large. They easily lay down on the surface of an extruded catalyst to condense (form coke), and thus coking and pressure drop increases in a hydrotreater is an important concern. Catalyst activity could be manipulated degree to compensate, but the range of compensation may not be wide enough, depending on the quality of the pyrolysis oil.
•There are often miscibility concerns when co-processing with standard VGO material. Phase separation could also ultimately lead to unintended coking in the unit, including the clogging of feeding equipment.
•These oils often have extremely high metals levels and may need to be pretreated in some fashion to remove those metals.
•Another option is to consider processing these oils in other units in the refinery (FCC or coker). Though not without issues, these units may be more suitable to handle the metals levels and the coking tendency of pyrolysis oils.
In all cases, one should closely examine the blending percentage of the renewable oil to be co-processed as a key variable. Minimizing this percentage will minimize disruption to an existing unit. In addition, one should also closely examine the regulatory environment to determine if there are benefits to co-processing or if standalone processing (100% renewable) adds additional benefits in the form of tax credits.