Question 51: What are some steps that can be taken to minimize re-foaming while steaming to the fractionator? Are there ways to predict re-foaming tendencies of different crudes or coker feed properties?
Rajkumar Ghosh (Indian Oil Corporation)
After a Coke drum is taken offline, it is steam stripped with ‘little’ steam @ 2.5 t/hr for 30 minutes (28 ft drum) to main fractionator to recover volatile hydrocarbon material. During this period, following conditions exist in the offline coke drum:
a. As the coke drum is filled to near its maximum allowable level, there is less vapor space available in the drum.
b. Presence of 8 – 10 ft high foam front
c. Reduced system pressure, as the fresh coke drum is yet to achieve its normal Coke drum outlet temperatures
Under these conditions, sudden drop in pressure of the off-line Coke drum results in re-foaming phenomenon. This can happen due to:
a. Switch over being done to a relatively cold Coke drum. Because of the changeover at a lower temperature and very less vapour generation, the overall system pressure comes down till the fresh Coke drum has achieved the overhead temperature of at least 420o C.
b. Very quick changeover in less than 30 minutes in a Coker having 4 or less drums would result in lower system pressure immediately after switching over.
c. If there is condensate carryover into the Coke drum along with ‘little’ steam, it results in immediate pressure surge and subsequent abrupt lowering of pressure. This also enhances chances of refoaming.
The steps taken at our cokers to minimize re-foaming while steaming to the fractionators are:
a. Proper heating of the drum is ensured to avoid switching to the cold drum. We monitor the Coke
drum Skin temperatures and our standard is to maintain these temperatures in the range of 260 –
280 degrees C
b. Condensate draining is done religiously prior to putting in steam to the offline coke drum.
c. The quantity of steam being put into the Coke Drum, to be done in-line with Licensors’. recommendations or based on firm procedures based on experience. Lower steam rate can cause faster rate of pressure decline in the drum and also blockage of channels in the coke bed while higher steam rate can lift the foam front of the filled drum towards fractionator.
d. Antifoam injection is started approx. 4 hrs before switchover and is continued in the off-line coke drum till it is lined up to blowdown. If frequent problems of refoaming are being faced, the rate of antifoam injection can be increased during switch over.
e. In case high system pressure drop is observed during and after the drum switch, we have a practice of increasing the set point for Wet Gas compressor suction pressure thereby reducing the RPM of Compressor.
Generally, we ensure that rate of pressure fall in the offline coke drum is in the range of 0.22 to 0.25 psi/ min immediately after switching over. This ensures that refoaming doesn’t take place. (Trend of coke drum pressures during a typical switch over is attached)
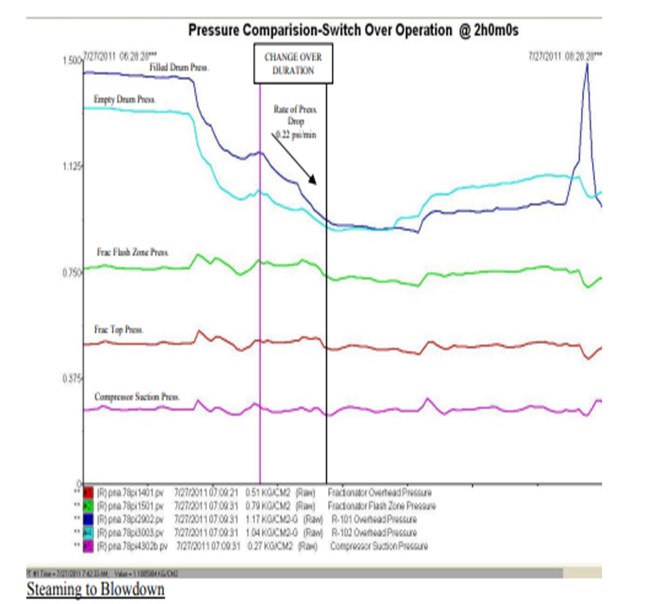
Once steaming towards fractionator is over, the steam and residual vapour from the drum overhead is routed to the blowdown system and steaming is ramped up to 16-18 t/hr (28 ft Coke Drum) and continued for 1.0 hr. If this switch to blowdown is performed too fast, it might again cause a sudden pressure drop in the drum which might uplift the foam bed. In some instances, foam and other material have been sucked in the drum vapour line and caused severe fouling and plugging.
As there is a significant pressure difference between the offline drum (1.1 kg/cm2 g) and the blowdown system (0.3 kg/cm2 g), care is to be taken by the operator to perform the switch to the blowdown system smoothly. We advice our operators to fully close one of the Vapour valves prior to opening the Blowdown valve. Further, the blowdown valve opening is to be manipulated through ‘inching’ control for slowing depressurizing the Coke drum pressure to Blow down.
As a best practice, we have configured the layout of Vapour valves, Blowdown valves and the Coke Drum pressure local indication in such a way that the valves can be operated with an eye to the pressure indication.
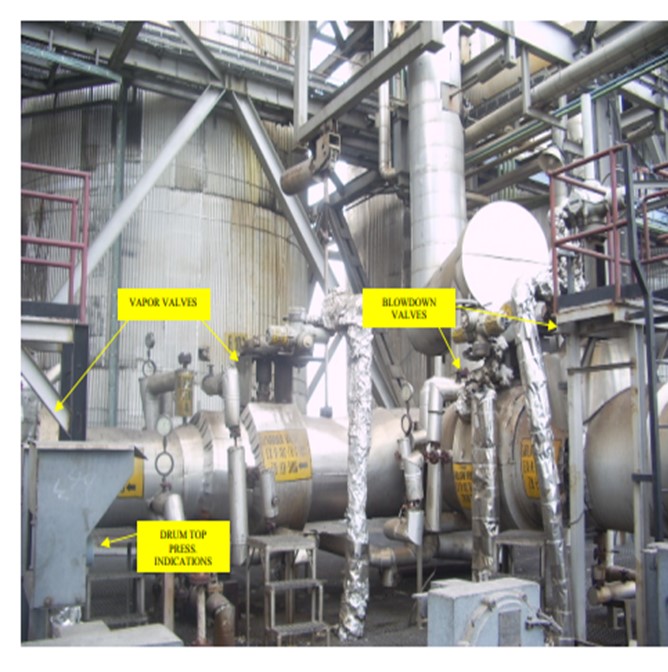
Prediction for refoaming
Data for predicting refoaming tendencies based on Coker feed properties is not available with us. However, it’s understood that Coke drums experiencing the following aspects may end up having tendency to refoam :
a. Sharp variations in feed quality w.r.t. API gravity
b. Light oil ingress in Coker feed through slop route
Jeff Lewellen (HollyFrontier)
I concur with the primary answer, and would like to highlight two additional events when foaming can be a significant issue:
o Establishing steam (or re-establishing feed) to a drum following a charge heater upset may result in a sudden foaming event. Typically, this occurs following loss of charge heater firing, or during startup and shutdown activities.
o Our experience indicates heavier unit feeds allow us to operate at lower heater outlet and drum outlet temperatures while maintaining same coke qualities. However, the lower drum outlet temperature tends to form a shorter, denser, and more stable foam layer that is more difficult to collapse. Higher antifoam rates are required to prevent a foaming event.
Eberhard Lucke (Commonwealth E&C)
Foaming during the steam stripping step can occur for different reasons. The most typical mechanism I know of is foam entrainment when depressurizing the drum from fractionator to blowdown pressure. This can be controlled by the speed of depressurization (slow opening of blowdown valve). In general, to see foaming during the steam stripping step there has to be significant amount of hydrocarbon liquid sitting on top of the coke bed. Not going into all the details of what feed properties influence this behavior, all residues that coke relatively slowly (typically high aromatic coke content, low asphaltenic coke content) will leave more liquid on top of the coke bed after switching the coke drum. This liquid layer can foam up if for example the steam stripping flow rate is ramped up too fast, or if there is condensate entering the drum with the steam that spontaneously vaporizes and causes a peak in steam flow through the coke drum. One idea to think about: ramp up the coil outlet temperature for 15-30 minutes at the end of the drum cycle to boil off more of the liquid from the coke bed.