Question 29: What is the impact of processing unconverted oil (UCO) from a high conversion hydrocracker on the following downstream units: FCC, coker, base-oil unit, and lubes hydrocracker?
PAPPAL (Valero)
This question is a handful to cover in three minutes, but here we go. This is a generic refinery processing sour crude. First of all, we add a coker to this generic refinery.
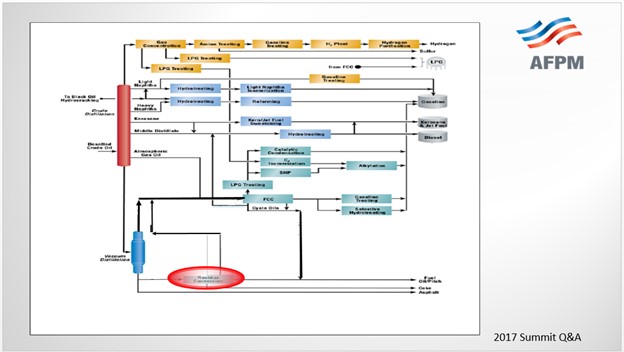
The heavy vacuum gasoil (HVGO) produced will be high in sulfur and nitrogen. The HVGO and the coker heavy gasoil (CHGO) are upgraded through the FCC. The CHGO, in this case, can be 14 gravities with 4,500 ppm of nitrogen. I want to acknowledge Jeff Bull, my colleague in San Antonio, who modelled these generic refinery configuration cases.
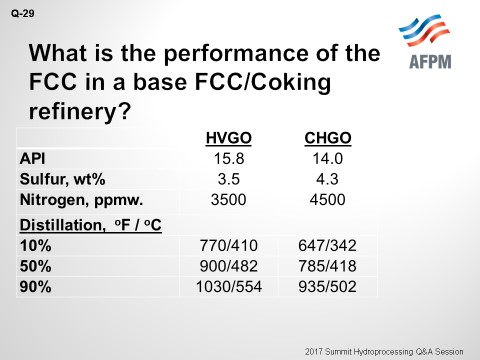
In an FCC/coking refinery, running this HVGO/CHGO blend results in a very low FCC conversion level of about 63%. The FCC produces a great deal of cycle oil and slurry. In addition, the volume swell for this case is not very high.
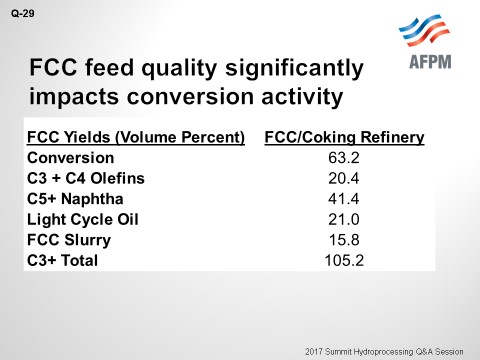
Now, we add a hydrocracker to this refinery configuration. Recall that we have the same crude slate, HVGO, and CHGO streams to upgrade. We add a reasonably powerful hydrocracker operating at 40 or 50% conversion.
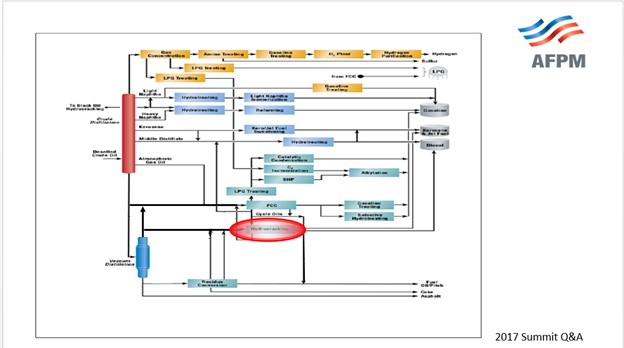
At this hydrocracker conversion level, many of the aromatics are converted and the sulfur and nitrogen are essentially completely removed. The unconverted oil from that hydrocracker operation is much improved at 35 gravity with virtually no sulfur or nitrogen, compared to the HVGO/CHGO feed to the hydrocracker. To stay in gasoil balance, the refinery would have to import HVGO or increase crude run. This scheme adds refinery G/D (gasoil/distillation) production ratio.
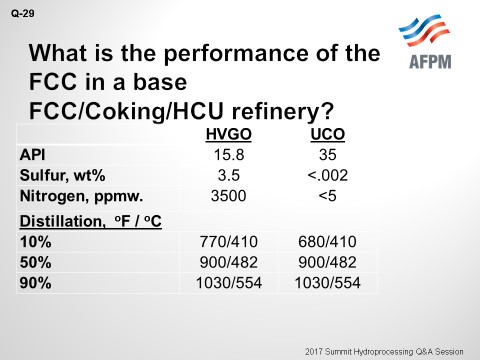
The FCC operation in this configuration is much improved as the cat cracker conversion is over 80% instead of the low 60s without the hydrocracker. There is significant light olefin yield to produce alkylate and lots of gasoline for blending. FCC cycle oil yields are significantly lower, and C3+ volume swell increases by 10%. Likely, this is a more economic operation than the previous operation. The message here is that adding a partial conversion hydrocracker to a coking refinery can have a large impact on the operation and can improve the overall economics of this refinery.
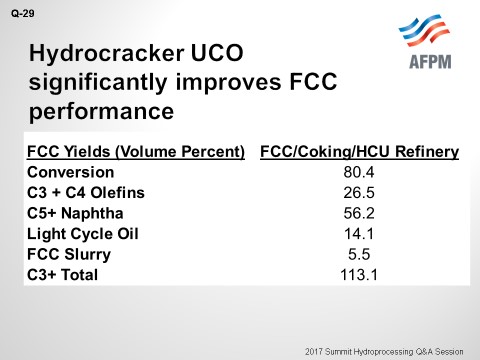
To summarize, the FCC and coker operation can be decoupled as the hydrocracker converts aromatics. Potentially, the coker could produce a more difficult coker heavy gasoil; the hydrocracker would protect the FCC from that difficult feed. Our volumetrics in the coker and cat are decoupled a step further. If we were to add a deasphalter, our ability to run heavy crude would increase while staying within coking and FCC capacity limits. Adjustments to FCC and coking operation are likely needed. There is further opportunity to optimize crude.
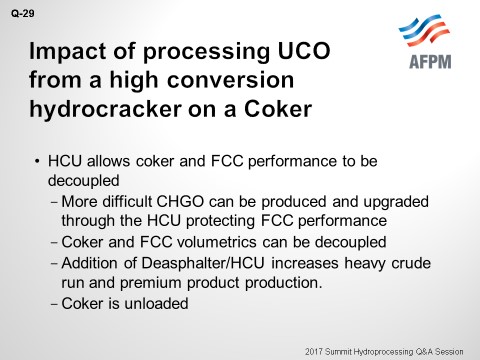
What is the impact of the hydrocracker on the lube block?
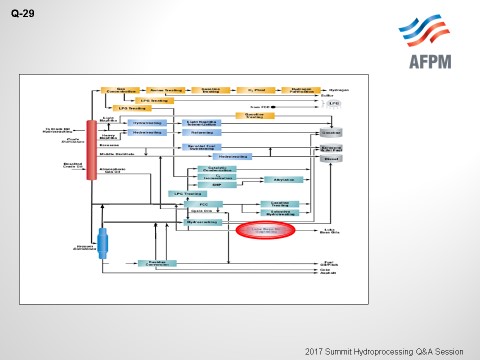
The UCO, as feed to the conventional base oil plant, increases the VI (viscosity index) potential of the product mix. The VI boost is decoupled from crude source. The hydrocracker is a great homogenizer of feedstock. Hydrocracking selectively cracks out aromatics, concentrating paraffins. Paraffins are the preferred component in the lube block. The conventional lube oil block would benefit from increased base oil yield from that plant. In addition, non-traditional crudes could be upgraded to produce premium lubricants.
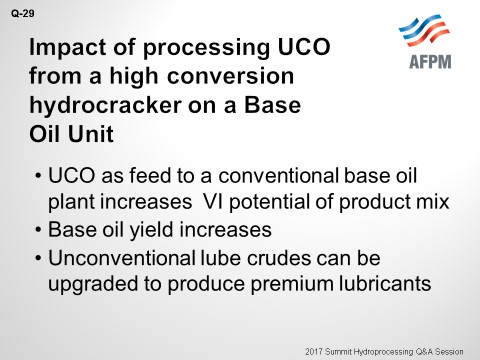
If a catalytic lube configuration is producing Group 2 and Group 3 lubes, using the fuel’s hydrocracker UCO as feed increases the high-quality base oil yield. The benefit is reduction of the lube hydrocracker conversion target required to meet the given VI target. Directionally, lube oil yield increases at lower tube hydrocracker conversion. Overall, the yield of premium quality base oil from that plant will increase.
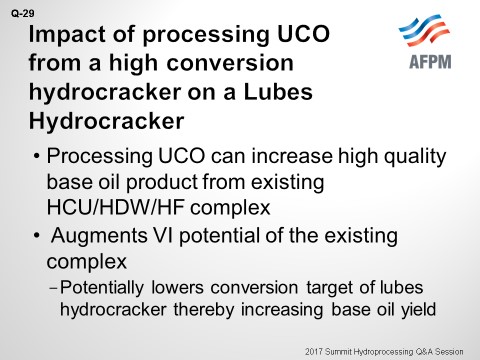