Question 29: What are the likely causes for temperature excursion events in a hydrogen plant?
EPSTEIN [Flint Hills Resources, LP (FHR)]
Hydrogen plant temperature excursions are possible in several of the catalyst vessels and are usually observed in association with the water/gas shift reaction. During normal operation, the high, medium, and low temperature shift reactors display an exothermic reaction. Changes to feed quality can increase this exotherm and cause the operating temperature to exceed the maximum allowable working temperature. A critical alarm on a high reactor discharge temperature is typically used to protect against this condition, with precursor alarms as needed. A similar exotherm is observed during the reverse water/gas shift reaction over the nickel catalyst in the methanator, which can increase under a change in feed quality. The exotherm generated by this reaction is significant enough that commonly occurring initiating events, such as the CO2 (carbon dioxide) removal system pump tripping, can cause the excursion. An SIL (safety integrity level)-rated system is typically used to isolate and depressurize the methanator if an excursion is detected.
I have personally observed an unexpected temperature excursion when starting up a combined feed pretreatment system. This catalyst combines the qualities of the hydrotreating and desulfurization beds into a single media and contains nickel, molybdenum, cobalt, and zinc oxide. That is what I am trying to show in this chart. Green is the top bed temperature; blue is the bottom bed temperature. We only had two TIs (temperature indicators). Yellow is our hydrogen recycle flow. So during startup, the natural gas feed was introduced, along with very high hydrogen recycle flow, at normal operating temperature and pressure. The unit operating procedure specified for the hydrogen recycle flow to be started at full expected flow rate, followed by ramping up the natural gas slowly. So we went to full-hydrogen rate right away. Under these conditions, it is believed that the hydrogen, CO2, and natural gas reacted exothermically through the reverse water/gas shift reaction similar to the methanator.
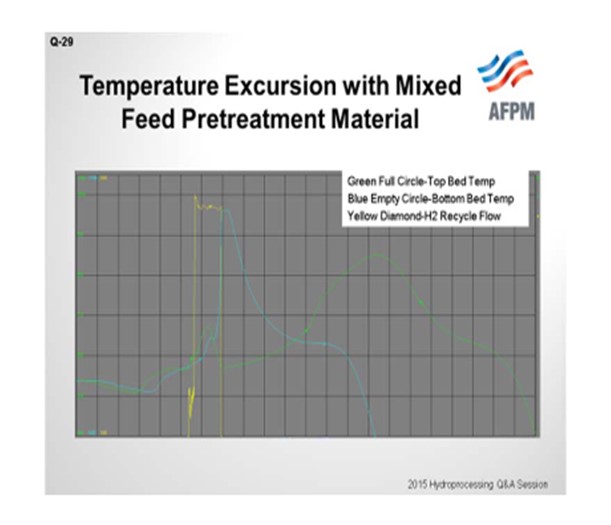
In addition, the catalyst was very dry after prolonged nitrogen circulation, and it is believed that the water generated by the reverse reaction was absorbed by the catalyst causing it to heat up, which initiated a reduction reaction that lead to the temperature excursion. Stopping the hydrogen flow discontinued all of this, and we are able to get back down to a safe level. According to the supplier, this was the first observation of such an issue with this material.
WRIGHT (Hunt Refining Company)
We approached the question from a different angle. We have recently had a temperature excursion which was caused by falling refractory in our transfer line. The transfer line is the pipe in between our reformer box and our first waste heat boiler. The line consists of a metal shell with refractory on the inside. The top portion of the refractory fell, allowing the hot syngas access to the metal shell; and soon, the line developed a fish mouth rupture resulting in what you see in the picture. Fortunately, no one was hurt. There were mainly cosmetic damages on the underside of the heater. So that was a recent event for us.
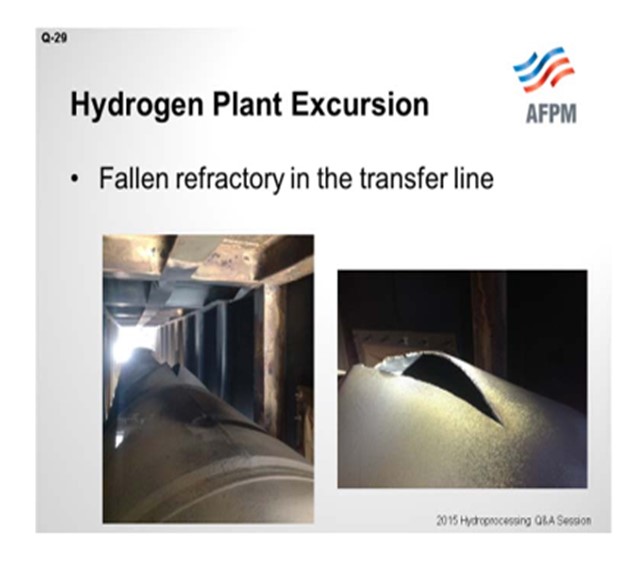
Other than that, in the past we have just had out-of-the-pipe issues: leaky flanges around some feed heat exchangers. We have had leaks around our PSA (pressure swing adsorber) valves, which caused fires. And one time, we had a fire caused by corrosion and erosion from attemperator water that was used to control the inlet temperature to a shift converter.
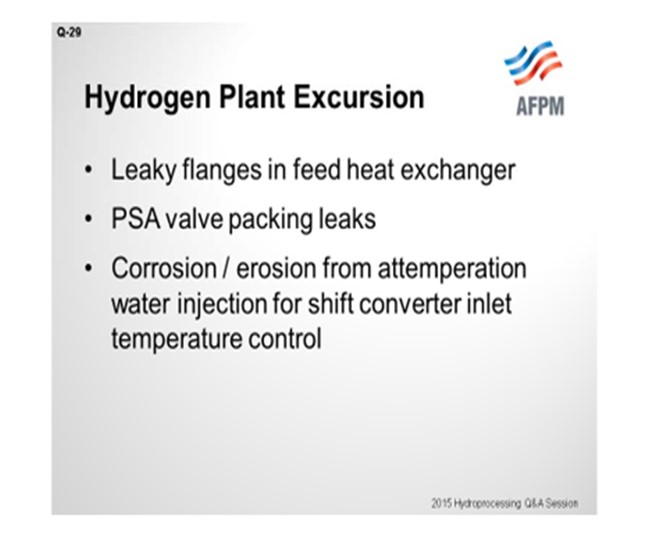
MORELAND (Valero Energy Corporation)
In Valero, we have experienced high bed temperatures in hydrogen plants in the high-temperature shift reactor due to failure of the control system or control valve in the upstream process gas boiler that resulted in high inlet temperatures. Additionally, the catalyst was very dry upon startup, and the heat of absorption caused temperatures of over 1200°F to be recorded. In the methanator, as Paul mentioned, we have also had an issue with a failure in the upstream CO2removal system. No catalyst damage was observed in that experience.
EPSTEIN [Flint Hills Resources, LP (FHR)]
We have not yet talked about pre-reforming catalyst. That catalyst is not used at Flint Hills Resources, so I would like to open that up, if anyone has any comments on pre-reformers.
MIKE ADKINS (KP Engineering, LP)
I know this is not directly related to excursions in the reactor. But as far as temperature excursions, in general, from the safety standpoint, it was kind of mentioned by Mr. Epstein on your cooling system looking at the steam generators. Obviously, in one particular plant I experienced. the failure of some of the safety systems. The Number 1 process steam generator blew out because it ran out of water. So definitely, keep in mind that you should be looking at the level instrumentation and safety practices.
JASON SCHMALTZ, NICK MUSICH, and RAJU NATARAJAN (Linde Engineering North America Inc.)
There are a few areas in the hydrogen plant where a temperature excursion is more likely and automated controls/shutdowns should be put in place to mitigate risk. The temperature excursion strategy should be confirmed during a HAZOP (Hazard and Operability) study with the proper risk matrix specific to the client’s site conditions and risk tolerance. The following is a summary of the likely causes for temperature excursion organized by plant area.
HYDROTREATING/DESULFURIZATION
Change in Feed Gas Composition: Increase in unsaturated bonds (e.g., olefins in refinery gases) or CO (carbon monoxide) levels can lead to a temperature spike in the feed gas as it passes through the desulfurization facilities.
Leading Cause: Unexpected change in feed composition is a more likely event at a facility that has multiple feeds from different sources that are constantly changing based on upstream plant performance. Upstream analytical tools can be used to determine if there is a potential feed composition issue and can set the plant to low fire prior to temperature excursion event. This does not necessarily need to be analyzer-based but can be based on a reactor temperature/pressure setting, for example. At a minimum, temperature should be monitored at the outlet of these facilities with proper alarm and/or shutdown systems in place. This does not mitigate the event. The proactive strategy will be mostly based on upstream product disposition criteria management.
New Phenomenon: Oxygen in natural gas from fracking can result in elevated levels of oxygen as compared to typical pipeline-quality natural gas. Although the levels are still relatively low, they can result in an exotherm across the hydrotreating catalyst.
REFORMING
Loss of Hydrocarbon Feed: Rapid loss of hydrocarbon feed can halt the endothermic reaction occurring in the reformer tubes faster than the temperature controls of the reformer are tuned to react. This will result in the steam flowing through the tubes to heat up rapidly and overheat the reformer tubes.
Leading Causes: 1) Loss of feed compression, 2) loss of supply natural gas supply, and 3) failed flow control, the most likely of which is loss of feed compression. Of course, the reformer should be equipped with high-temperature protection for both the process and firebox, but the proper strategy would include controls to mitigate the temperature excursion. Establishing strategies for shutting down preemptively on low flow or tying compressor suction pressure to a plant rate override are both viable with the most straight forward approach being to shut down the plant to low fire conditions on low hydrocarbon flow.
Poisoning/Coking can result in localized hot spots and eventual reformer tube rupture.
Leading Causes: 1) Sulfur or other poisoning, 2) low steam-to-carbon ratio, 3) change in hydrocarbon feed composition, 4) olefins, 5) localized high temperatures due to flame impingement or other furnace performance issues, and 6) deactivated catalyst due to aging are all likely causes of poisoning/coking. Temperatures and pressures around the reformer and furnace should be monitored with appropriate alarms and shutdowns implemented. The reformer should be regularly visually inspected for hot spots and burner operation.
WATER/GAS SHIFT REACTION
High Reaction Rate in Shift Reactor: Sudden increase in shift reaction rate can result in high-temperature excursions. The risks are greater in low and medium temperature shift converters.
Leading Causes: 1) Spike in CO composition, 2) high temperature at inlet, and 3) low steam-to-carbon ratio are the main culprits for high reaction rate in the shift reactor. Feed composition to the shift reactor is highly dependent on reformer operation stability and unit feed composition, especially for feeds other than natural gas. Regular feed sampling schedules should be part of operation practices and understanding of upstream units and when to preemptively reduce or cut feed completely should be understood. Additionally, inlet temperature should be managed based on CO slip indicated over long-term monitoring reports. This temperature should be set as low as possible based on expected methane slip versus actual. This strategy will reduce the chance of runaway reaction occurring. Additionally, alarms and shutdowns can be put in place based on inlet/outlet/delta temperature for the reactor to help mitigate the risk.
COOLING CIRCUIT
Loss of Integrated Cooling: Depending on how integrated the cooling system is with the rest of the plant, a fast reaction to an upset in one part of the plant could translate into significantly less heat sink available in an integrated exchanger. This could result in temperature excursion if the integrated exchanger accounts for a significant portion of the cooling duty.
Leading Cause: Compensation for level fluctuation in steam drum or deaerator is the most common cause. The best mitigation for this is to pay special attention when tuning level controllers that are tied to the cooling circuit water flows. The level controllers should react very slowly so as not to reduce flows significantly during some sort of level upset (there are many root causes for this). It will take operating the plant for a few weeks to determine what tuning parameters make sense long-term. Additionally, overdesigning the cooling section for higher design temperatures can provide some additional assurance that a temperature excursion will have minimal consequence to the equipment. This is typically at a marginal cost increase since this section is already cool enough where stress values for material of construction are only minimally impacted, if at all. Obviously, temperature measurement/alarms/shutdowns should be implemented on the syngas product.
METHANATOR
Feed Contamination: It is common to have a methanator in the old-style, pre-PSA hydrogen plants to convert the low levels of CO (up to 0.3%) and CO2 [up to 200 ppmv (parts per million by volume)] to methane. Methanation is an exothermic reaction and could run away if excessive CO (due to malfunction/misoperation of the low temperature shift reactor) and/or CO2 (due to malfunction/misoperation of the CO2 removal system).
Leading Causes: High CO and/or CO2 in the methanator feed usually create the problem. Typically, a shutoff valve and a vent valve are provided in the feed line with a temperature probe in the first one-third of the section of the bed to detect a rate in temperature rise. A rapid temperature rise will shut the feed valve and vent the syngas to the flare.
TURNAROUND/MAINTENANCE
Oxygen Ingress into Piping/Equipment: Exothermic reaction with hydrogen or hydrocarbons can result in equipment failure due to temperature excursion.
Leading Causes: Improper purging and purge contamination may occur, so proper procedures must be followed.
LOSS OF HYDROCARBON FEED
Rapid loss of hydrocarbon feed can halt the endothermic reaction occurring in the reformer tubes faster than the temperature controls of the reformer are tuned to react. This will result in the steam flowing through the tubes to heat up rapidly and overheat the reformer tubes.
GOPI SIVASUBRAMANIAN (Amec Foster Wheeler)
Temperature excursion events could occur in the HDS (hydrodesulfurization) reactor or in the methanator reactor. Processing higher olefins than the unit is designed for can cause temperature excursions. Less frequent causes are CO2, CO, and oxygen, in that order. Higher CO slip/inlet temperature will cause the methanator reactor to have temperature excursions.
SUE SIMPSON (Johnson Matthey) Temperature excursions can occur in each section of the hydrogen plant for a variety of reasons. Operating issues that can cause temperature increases in the purification, reformer, and shift sections should be avoided as costly damage can occur.
First, in the purification section, a temperature excursion can occur if olefins are present in the feed. The HDS catalyst is also an effective olefin hydrogenation catalyst. The olefin hydrogenation reaction is significantly exothermic and should be considered in the HDS design. If the olefin level will cause the HDS bed to exceed the maximum recommended catalyst temperature, a more active catalyst that reacts at lower temperatures and increases the operating temperature window should be utilized.
Hydrocracking, a very exothermic reaction, has also been observed over HDS catalysts. The risk of hydrocracking increases when the HDS bed temperature exceeds the maximum recommended level for a specified feed, the feed has a very low total sulfur level, or the catalyst has been exposed to high levels of hydrogen. In situations with increased risk, presulfiding the HDS catalyst may be necessary.
In addition, CO and CO2 can methanate on HDS catalysts if the operating conditions and state of the catalyst are conducive. The consequences of the resulting exotherm can be severe, and conditions under which methanation can occur should be avoided. This is achieved by selecting the appropriate catalyst type, depending on the level of carbon oxides in the feed gas. CoMo (cobalt molybdenum) HDS catalysts have a greater tendency to promote methanation reactions whether sulfided or not; however, NiMo (nickel molybdenum) HDS catalysts do not promote methanation when sulfided.
Second, in the reformer, the steam reforming reaction is highly endothermic. If less reforming occurs, the temperature will increase. Feedstock purification is key to ensuring an active reforming catalyst. Sulfur, chlorides, or other heavy metals can poison the catalyst resulting in less reforming and increased temperatures. This can then lead to carbon formation which further reduces catalyst activity. Carbon formation can also be effected by low steam, heavy feed, and burner flame impingement.
In addition, increased temperatures may be the result of reduced flow. Tube blockage or scale can reduce flow causing less reforming and increased temperatures. During transient conditions, flow is typically lower than normal operation making the reformer more vulnerable to temperature excursions. At low flows, less heat load is required which can result in overfiring. Compositions and flows used for instrument calibration may vary during transient conditions resulting in inaccurate measurements. In addition, the heat leak from the temperature measuring point to the tube exit will increase at low flow rates. Typically only inlet and outlet temperatures can be measured, and there is not sufficient manpower available during startup to visually inspect the reformer tubes. These factors can result in temperature increases in a reformer.
A useful tool to monitor the reformer is a multipoint thermocouple called a CatTracker™. This device measures the process gas temperature throughout the tube. The measuring points are individually specified and uniquely designed for a specific plant. The CatTracker™ provides continuous online monitoring with tube temperature profiles available in real time. Determination of the tube temperature profile provides a more accurate prediction of the carbon formation zone. This increases the ability to avoid catalyst steaming and lost production as a result of carbon formation. The installation of trips based on these process gas temperatures can also prevent costly reformer damage. The CatTracker™ is a tool that can aid in the optimization of reformer operation and help determine when catalyst changeout is required.
Finally, in the shift section of the hydrogen plant, temperature excursions can be observed. If a high-temperature shift (HTS) catalyst is exposed to dry nitrogen circulation prior to startup for an extended period, possibly due to refractory curing or a delayed startup, the catalyst surface can be dehydrated. The subsequent rehydration with steam addition is very exothermic.
Medium temperature shift (MTS) and low temperature shift (LTS) catalysts must be reduced prior to plant operation. The reduction is completed with hydrogen and is exothermic. The concentration of hydrogen must be controlled to prevent temperature excursions. When the reduction appears to be complete, a soak period is initiated at a substantially higher hydrogen level. A temperature increase may be observed if unreduced catalyst is still present.
Temperature excursions can occur for a variety of reasons in a hydrogen plant. Understanding the causes can optimize performance and avoid costly damage.
CHAD TAYLOR (Haldor Topsoe, Inc., Inc.)
The main causes for high-temperature excursion events in a hydrogen plant are hydrocracking over the HDS catalyst, runaway during an LTS reduction, and runaway in a methanator from CO2 absorber carryover/failure.
Hydrocracking over HDS Catalyst: Hydrocracking in an HDS reactor can take place in situations where a fresh CoMo/NiMo catalyst is exposed to a hydrogen-rich off gas, with little or no sulfur, at an operating temperature of 600°F or higher. This occurs when the unsulfided CoMo/NiMo oxides are reduced to base metals after being operated for an extended period of time in the hydrogen-rich gas. The resulting reduced catalyst is active for hydrocracking, which is an exothermic reaction. The risk of hydrocracking increases with higher temperature, carbon number, hydrogen partial pressure, and the duration of time of exposure to these conditions. Hydrocracking results in an uncontrollable temperature runaway because the heat produced from the cracking leads to further cracking and even more heat, and so on. This will damage the catalyst and possibly even the HDS vessel. The graph below shows how quickly and how hot an HDS runaway reaction can get.
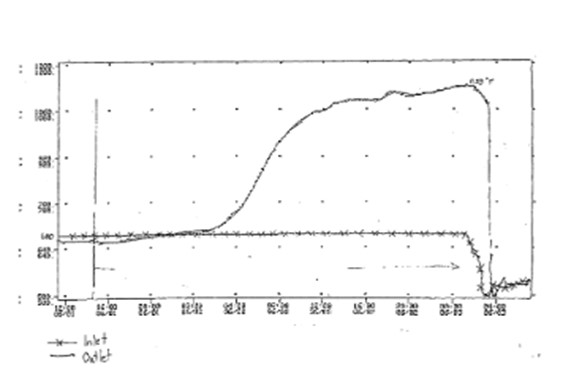
It should be noted that once a catalyst with hydrotreating functionality has been exposed to ppm levels of sulfur; it is very difficult to reduce the metal sulfides to base metals and create a hydrocracking functionality. In other words, we have never seen an issue during operation, only in connection with fresh catalyst during the initial startup phase.
LTS Reduction: LTS catalyst is delivered in oxides form and needs to be reduced with hydrogen in a carrier gas to be activated according to the following reaction:
CuO + H2 Cu + H2O + HEAT
This reaction is highly exothermic. The reduction is carried out at a specific inlet temperature, and the hotspot temperature is carefully controlled by adjusting the hydrogen concentration in the carrier gas. There is only a small risk of a runaway when using nitrogen as the carrier gas. However, it can happen if too much hydrogen is injected to the reduction loop or if hydrogen or CO- containing gases leak into the reduction loop. Many plants will, however, use once-through natural gas where there is a potential for a runaway reaction due to cracking of the methane or higher hydrocarbons at temperature above 450°F. The hydrogen released from cracking the hydrocarbons will further reduce the catalyst resulting in even more heat, cracking, and hydrogen. The result is a runaway reaction.
As mentioned, a runaway can occur if the hydrogen is increased too quickly and/or not monitored closely or if process gas is leaking in, which increases the hotspot temperature to the point where the cracking begins. The factors affecting the cracking temperature include the amount and type of higher hydrocarbons in the natural gas stream and the pressure of the LTS reactor. A runaway during an LTS reduction will cause damage to the catalyst resulting in shorter run-lengths and/or catalyst replacement and could possibly damage the vessel as well.
If the hydrogen is carefully increased and all of the parameters and procedures are closely followed, then the risk for a runaway is extremely low. Haldor Topsoe, Inc. uses our proprietary TopsafeTM portable hydrogen analyzer. This analyzer provides real-time continuous display of the hydrogen concentration in the carrier gas. Real-time monitoring allows us to bring the concentration up quickly and safely without having to rely on the local lab or a portable GC (gas chromatography) machine, which can require up to 30 minutes or longer to obtain results. You will notice the compact setup in the picture of the TopsafeTM analyzer and setup below:
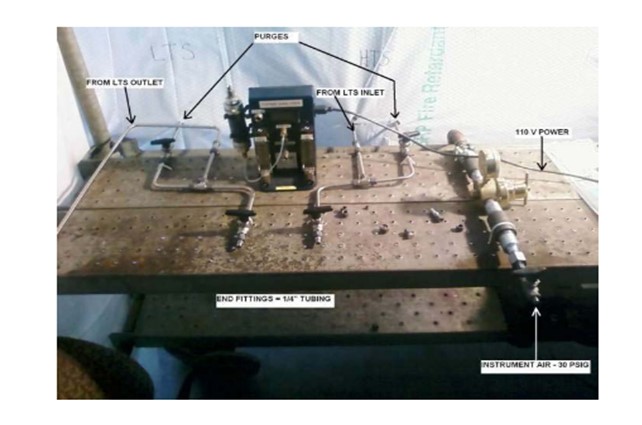
The TopsafeTM analyzer is very reliable and easy to use, and its accuracy is extremely high. The TopsafeTM analyzer is the only online analyzer in the market place for this use.
Methanator CO2 Excursion: The purpose of the methanator is to convert CO and CO2 to methane (reverse reactions of the steam methane reformer). The reactions are:
CO +3 H2 CH4 + H2O + HEAT
CO2 +4 H2 CH4 +2 H2O + HEAT
For every 1 vol% (volume percent) of CO2 converted, there is an increase in temperature of approximately 108°F. At the exit of the LTS vessel, the process gas will have between 15 and 19 vol% CO2, which would result in an exotherm of 1600 to 2050°F. This is obviously unacceptable, so the CO2 is removed in an amine liquid absorption process. If the absorber is underperforming, then it can lead to an increased exotherm across the methanator. If the absorber is not adequately removing the CO2, it will lead to a rapid temperature excursion which is usually not stopped until equilibrium is established around 1500°F. To avoid catalyst and/or vessel damage, most plants have both a high temperature, and a high rate of temperature increase trip which reroutes the process gas to a flare or vent.