Question 24: How do you manage reactor maldistribution once identified?
PATRICK GRIPKA (Criterion Catalysts & Technologies)
Once maldistribution is identified, safely managing it depends on the unit, feedstock, and unit objectives. If the extent of maldistribution is not impacting safety, then it is an economic decision whether to:
*Manage to the end of the cycle,
*Manage to a convenient turnaround point, o.
*Shut down and correct immediately. The decision and the mitigation actions will also depend on how the maldistribution is observed.
*Differential pressure (dP; ∆P; delta P) issues can be handled by adjusting feed rate and gas rate to keep dP below the maximum until a unit skim or changeout can be taken. Use of chemicals to reduce dP can work for short times if the dP is due to FeS (iron sulfide) particulate agglomeration.
*Radial thermocouple spreads can be an issue if the radial exceeds the accepted Best Practice or if it leads to a peak thermocouple being reached at a much lower overall bed temperature than expected. In both cases, feed management (i.e., removal of most reactive feeds) and/or adjustment of feed and gas rates are items which can be adjusted. If product quality is impacted, then feed management may get the unit back on-spec (on specification). If feed management does not resolve the issue and the product spec cannot be relaxed, then the unit will have to be shut down.
In any of these circumstances, understanding the cause of the maldistribution is critical; and if the cause is undetermined or uncertain, a careful observation and review should be completed during unloading.
JEFFREY MUELLER (Marathon Petroleum Company)
Reactor maldistribution is a phenomenon that is typically caused by inadequately designed or installed reactor internals, improperly/unevenly loaded catalyst bed, catalyst migration from an upstream bed, or process fouling. The main problems generated by flow maldistribution are the overuse of part of a catalyst inventory and the formation of hot spots, which can create a process safety risk, as well as limit the performance of the cycle. In a hydrocracker, hot spots present a serious process safety concern, as well as contributing to over cracking which can lead to reduced liquid product selectivity.
Reactor maldistribution can be recognized by an increase in the radial temperature spread, an increase in the measured bed dP, or both. Once maldistribution is identified, the most important items to understand are the safety implications and set limits accordingly. A refiner should be monitoring all radial bed temperatures and honor any peak temperature limitations. It is also important to consider that your temperature indicators (TIs) are only a snapshot of the bed. As your spread increases, you should consider being more conservative on your peak temperature limit, considering the logic that you may have hot spots that are non-detected due to the spacing of the TIs. Additional monitoring of the reactor walls, either by IR scan or installing temporary TIs should be considered in the bed where maldistribution is occurring. In addition, monitoring individual reactor bed dP versus loading limits is important, as maldistribution can be tied to pressure drop if catalyst migration is a causal factor or if the maldistribution has caused coke balls to form within the reactor bed.
There is little or nothing that can be done, on the run, to manage maldistribution issues caused by distribution tray issues. This type of maldistribution is typically recognizable because it is near the top of the bed. The obvious answer here is to replace or repair the damaged tray at the next catalyst change.
Depending on the source of the maldistribution, an immediate outage may be required to remedy a process safety risk. Recently, on an MPC hydrocracker, an impromptu mid-cycle outage was taken to screen and reload the top few beds of the hydrocracker reactor after maldistribution was detected due to a loss in catalyst containment from one bed into the redistribution tray. This catalyst migration issue was diagnosed from an increase in bed radial distribution spread corresponding to an increase in reactor pressure drop (see Figures 1 and 2).
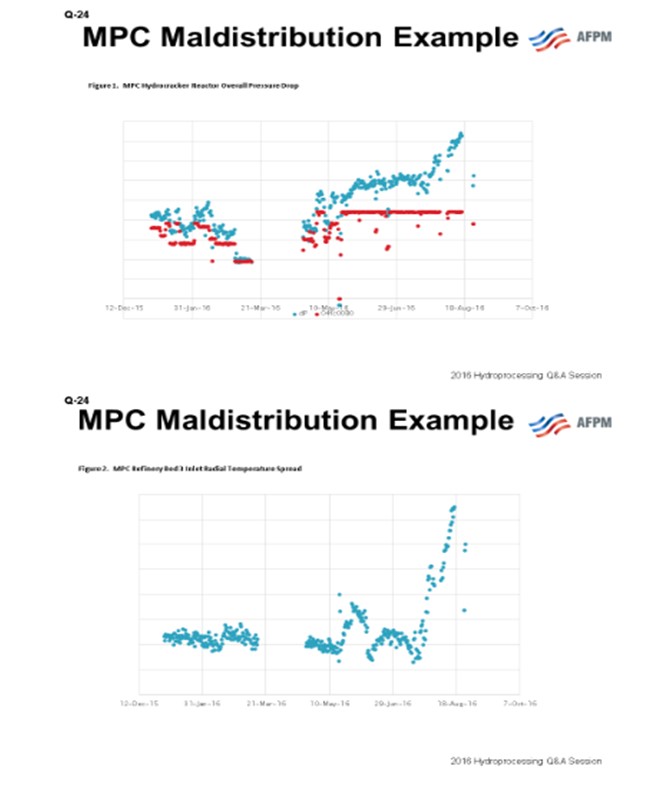
The data pinpointed the issue to an initiating event: an unplanned unit shutdown due to a refinery hydrogen upset. Figure 3 is a photo taken from inside the reactor during the catalyst removal showing the migrated catalyst on the redistribution tray.
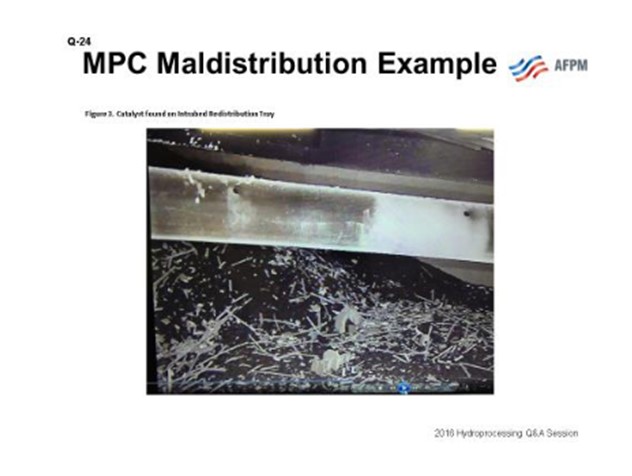
JACOB BRIX (Haldor Topsoe A/S)
When reactor underperformance has been confirmed to be caused by maldistribution, two separate tracks are normally started in parallel. The first is to limit the impact on the current cycle length by following the pressure drop, deactivation, and product specifications. Depending on the observations, small modifications –such as a calculated change in gas/quench rate or a small change in feedstock properties –can help to extend the cycle.
The second track is to investigate the cause. Maldistribution can either be caused by internals malperformance or by channeling initiated in the bed. If there is evidence of internals malperformance, the refiner should ask Haldor Topsoe to evaluate the benefit of installing new Topsoe distribution VLTs (vapor lift trays) and a Torus™ mixer which can, in most cases, be paid back in a matter of months due to better performance and reduced downtime. Maldistribution in the bed can both be initiated after an upset, which caused coking, or at the start-of-run if the loading was not ideal.