Question 18: What are the economic incentives to justify upgrading reactor internals? What techniques have been utilized to assess the performance of existing reactor internals?
BODOLUS (CVR Energy)
The primary incentive is catalyst life and the ability to meet turnaround intervals. Gas and liquid distribution improvement results in increased catalyst performance and potentially longer catalyst life. Reactor internal upgrades may consist of quench decks, mixing chambers, and improved liquid distributor trays. Reactor internals are expensive and can take considerable effort to install. Costs can be readily defined up front, but “hard dollar” economic benefits are more difficult to quantify.
Assessing performance can be done on temperature distribution within the bed where the ratio of radial distribution (across a bed level) is tracked with axial distribution (bed temperatures at increasing bed depth). The technique requires the existence of multiple thermocouples in the bed, which is typically an upgrade that is done when internals are changed out.. A typical guideline for good distribution within a reactor is for the radial differential temperature (DT) to be 10% to 15% of the axial DT. A radial-to-axial profile in excess of 20% may indicate inefficient distribution or bed channeling. Tracking the radial-to-axial profile with reactor rate will help define turn-down limits or indicate that better technology is needed for the particular operating scheme being used.
As reactor internals become mechanically complicated, maintaining cleanliness becomes important for continued performance. Modern internals provide efficient gas and liquid distribution in a minimum space, but cleaning them to maintain performance on subsequent outages is difficult and time consuming. Under inert conditions, manpower inside the reactor is limited and detailed inspections for cleanliness often depend on video cameras that only show what they are pointed at. If the reactor is exposed to normal atmospheric conditions of oxygen and moisture, it can cause normally adherent iron sulfide scale to curl and flake-off. The longer the reactor is exposed to atmospheric conditions, the higher the prospects that the initially adherent scale will curl and flake.
Pre-cleaning the reactor with chemicals at the start of the turnaround can be effective in hydrocarbon deposit removal, but the inorganic scale on the reactor internals needs mechanical force for removal. Cleaning with manual labor is highly dependent on the workforce and accessibility. Hydro blasting has been used with some success, but it has a lot of potential drawbacks. Solid carbon dioxide blasting has shown excellent results as it is very effective in dislodging scale and deposits from traditionally hard to reach places.
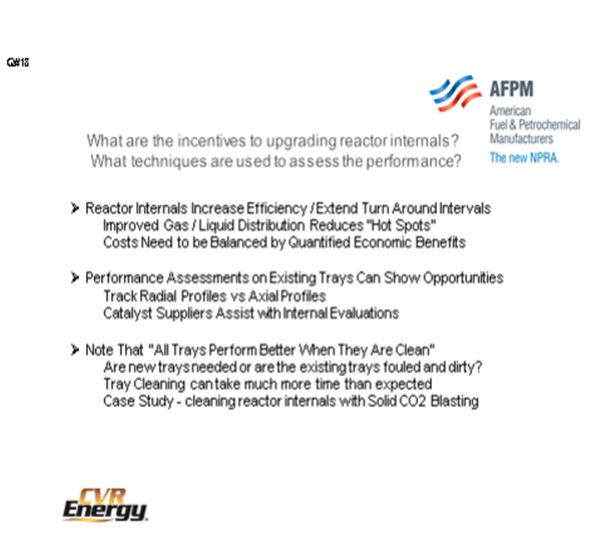
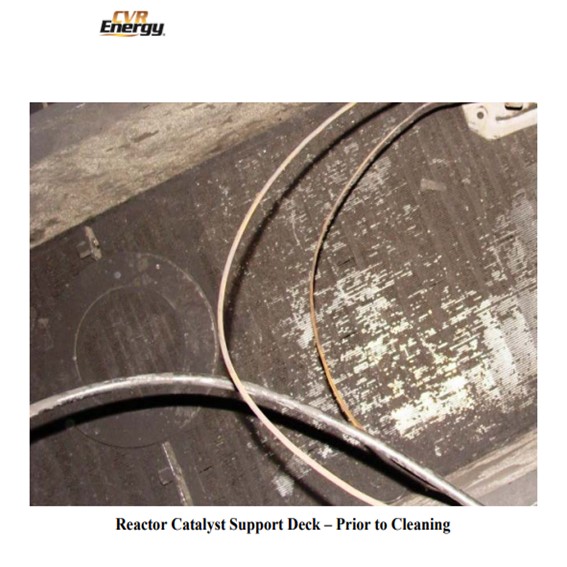
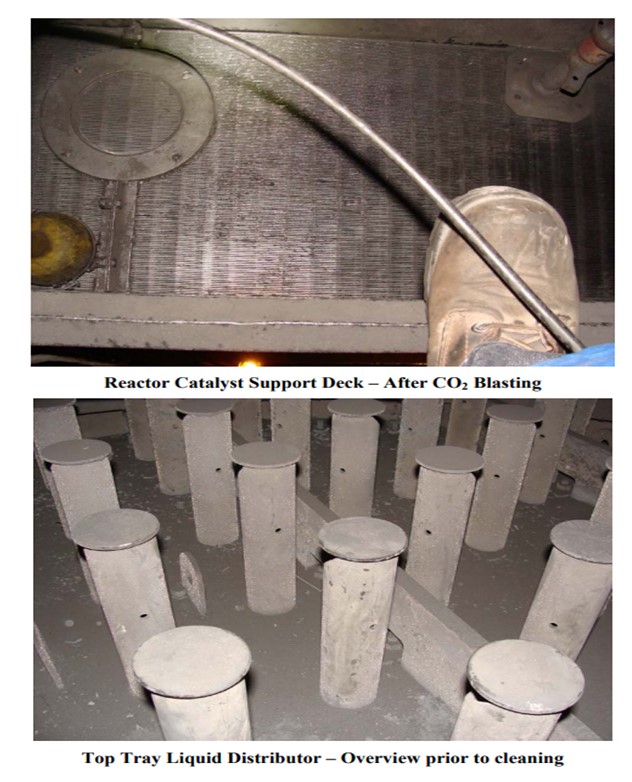
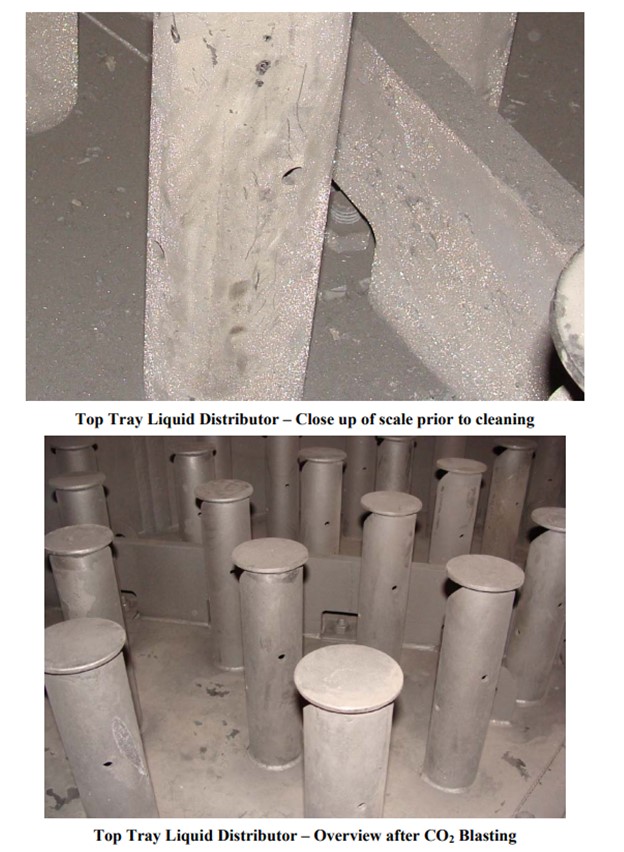
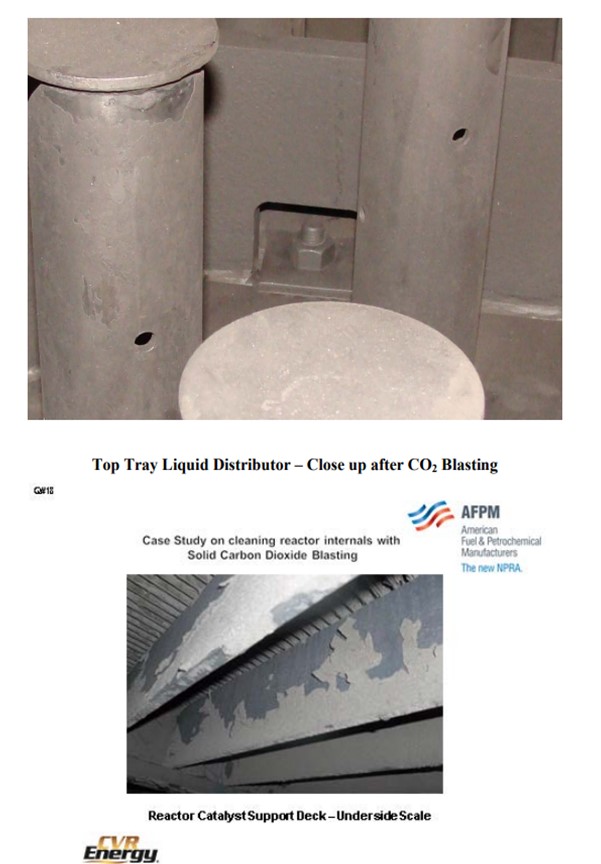
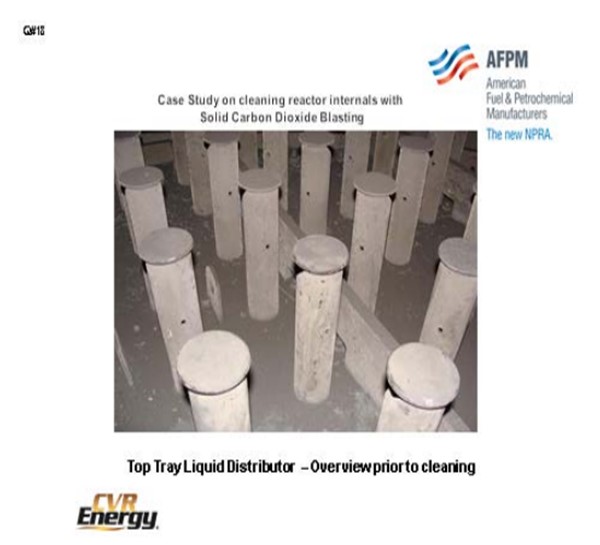
CARLSON (Criterion Catalysts & Technologies)
Catalytic hydroprocessing technology has been applied for many years in the upgrading of refinery hydroprocessing streams. The reactions are typically carried out in co-current adiabatic fixed-bed reactors.
The performance of such reactors is determined by the loaded catalyst and also, to a large extent, by the design of its internals. In the last 15 years, there has been considerable attention for the issue of maldistribution in vapor/liquid hydroprocessing applications: insufficient distribution of gas and liquid inside the reactor leads to underutilization of the catalyst and local hot spot formation. This has detrimental effects on catalyst cycle length, product quality, unit reliability and process safety. In a number of articles published, successful revamps have been presented, showing how installation of state-of-the-art internals had positive effects on these parameters, as well as provide an economic way to debottleneck units for refiners everywhere in the world.
When considering upgrading reactor internals in an existing hydroprocessing application, the economic gains can be realized from a number of operational capability improvements:
• Increased operational cycle life, reducing both long-term maintenance and catalyst costs,
• Improved product qualities and yields,
• Reduced capital expenditures for revamps to meet process improvement requirements, and
• Increased safety and reliably
When reviewing the benefits, the first step is to understand what operational limitations currently constrain the overall economic value of the unit’s performance, such as
• A pressure drop resulting in early unit shutdowns,
• A high radial delta T resulting in a limited EOR operating temperature,
• Unit activity limitations resulting in either lower-than-desired feed rates or shorter-than-desired operation cycles, and/or
• An inability to meet product specifications with current performance.
In many hydroprocessing units, utilizing upgraded internals can relieve these constraints.
via:
• Removal of foulants and contaminants with a scale catching or filter tray,
• Improved catalyst utilization due to a homogenous distribution with a high dispersion tray,
• Thermal uniformity and quench injection with an ultra-flat quench mixer, and/or
• Increased active catalyst loading via reduced need for hold down material, quench zone “straight wall”, and bottoms inerts.
In one of many examples, the figure below highlights the improvement in flow distribution in a hydrocracker as indicated by the reduction in radial temperature deviations. This improvement had the benefit of opening the operating window of the unit and extending the cycle life, as well as increasing performance due to improved catalyst utilization.
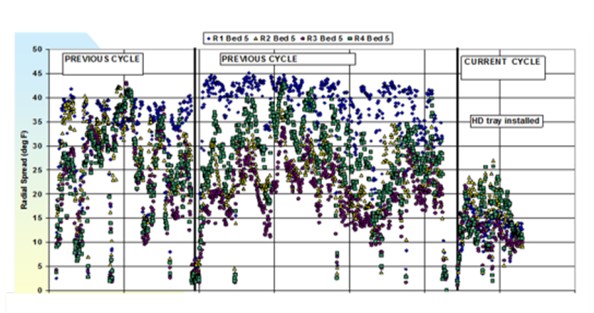
As many existing hydroprocessing units can take advantage of improved internals, combining advanced reactor internals with recent catalyst developments can significantly increase process capability. In the example summarized below, and recently presented at another industry conference, this approach was used to revamp an LSD unit into ULSD service while minimizing the cost and complexity of the required revamp.
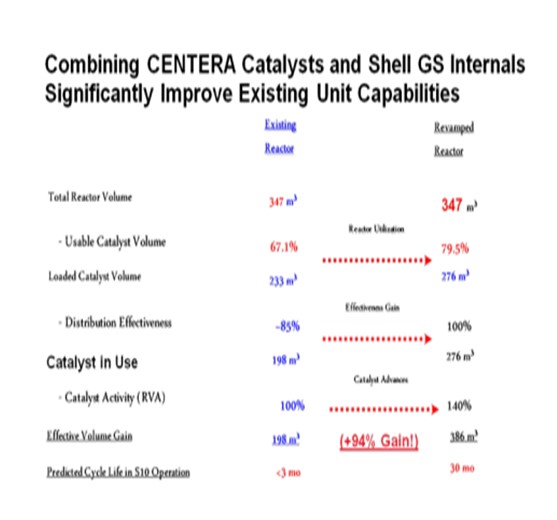
Diagnosing existing operations can be accomplished by a number of approaches.
• Day-to-day radial temperature spreads
• Evaluation of radial to axial temperature spread ratios
• Kinetic response test
• Radio-Isotope tracer studies
• Pulse test: transient temperature change response study
Often current performance has been preliminarily evaluated by the review of the day-to-day temperature reading. While this can indicate potential issues in the reactor, a snapshot of temperature deviations does not provide sufficient information to accurately judge performance as many things can lead to these observations such as catalyst fouling or loading problems, as well as in some sections of reactor beds poor operation may masked due to low axial temperature changes. A pulse test in which a small temperature change is introduced into the reactor sections is a very easy way to qualitatively diagnose potential distribution, fouling, or mixing issues in the reactor beds. In addition, Shell Global Solutions has a detailed analytical approach that utilized pulse test data to provide a quantitative evaluation of current performance. and providing a measurement of potential performance.
ESTEBAN (Suncor Energy, Inc.)
The major economic incentives to justify upgrading reactor internals are increased catalyst utilization and minimization of hot spots resulting in increased catalyst life cycles (unit availability), increased capability to process more feed or more difficult feed, improved product quality, and in some cases improved yields. The performance of reactor internals can play a huge role in the overall performance of a catalyst system because catalyst life cycles are optimized by proper reactor flow distribution, good mixing with quench streams, and minimization of reactor weighted average bed temperatures (WABT). In cases where the metallurgical design temperature limitations of the reactor and heat exchange equipment determine end of a catalyst cycle, minimizing hot spots can extend catalyst life cycles by permitting operation to higher maximum WABTs. When product quality dictates catalyst life cycles, the improvement in product quality due to improved flow distribution can also extend cycle life by permitting operation to higher maximum WABTs. Unfortunately, in some cases catalyst life cycles are limited by overall reactor pressure drop which can reduce unit feed rates to less than desirable levels and/or heat transfer equipment limitations that will not permit on-specification operation at higher rates, both, impacting overall refinery throughput. In these cases high performance reactor internals have the potential to improve catalyst life cycle performance extending run lengths which relates to both reduced catalyst costs and increased refinery throughput. In addition to improved unit availability, upgrades to reactor internals can provide improvements in product yields, which are more evident operating at high WABT at the end of cycle or high conversion rate when considering modifications to hydrocracking units.
The two key benefits to high performance internals are even distribution and improved quench mixing. Improvements in reactor distribution and quench mixing result in a more even use and deactivation of catalyst lowering the severity required to meet product specifications. As well these improvements can reduce the potential for formation of pressure drop depending on the contributing causes for excessive pressure drop and assuming proper catalyst loading. In some cases the current performance of reactor internals can be implied by comparing the average final reactor bed outlet temperature to the combined temperature of the stream in the piping downstream. A large difference in these values can indicate poor distribution.
In order to provide a better measure of improvements in distribution and quench mixing, one simple method using existing equipment Suncor Energy, Inc. has employed to evaluate reactor internals performance is the statistical analysis of data provided from temperature pulses. The method of analysis is based on the principle that if the distribution in a catalyst bed were perfect, a temperature pulse initiated at the top of the bed would travel down and reach each point in any horizontal plane simultaneously. In addition, if the uniformity of catalyst activity and catalyst loading were perfect, the temperature difference between each point in any horizontal plane and the bed inlet temperature would be the same. This concept of perfect distribution is used to evaluate the performance of the old internals versus the new internals, as well as provide information regarding the gap between perfect distribution and actual performance to determine the potential benefits of upgrading internals. The following describes the test method previously used by Suncor Energy, Inc. sites:
Test Method: During a test run or several runs, the temperature at the inlet of each bed is reduced by approximately 5°F and then increased back to its original setting. Data from every available bed temperature indication (TI) is then collected. Using all available temperature data, three variables are calculated for each temperature signal.
1. Delay time: The amount of time that it takes for a temperature pulse to reach a TI.
2. ∆T: The temperature difference between each TI and the average bed inlet temperature.
3. Gain: The derivative of each TI with respect to the average bed inlet temperature. For example, if the bed inlet temperature was increased by 1°F and the TI increased by 0.5°F as a result, the gain would be 0.5.
With perfect distribution, a plot of ∆T versus delay time would show a near-linear correlation with a coefficient of determination, R2, equal to one. The R2 of the ∆T versus delay time correlation for each bed is used to determine the nearness to perfect distribution.
Using the previously described method several Suncor sites have been able to determine the performance improvements resulting from tray modifications and have been able to achieve distribution results in the 0.9 to 0.95 range. The following figure displays the improvements from a project in our Edmonton Refinery in 2005.
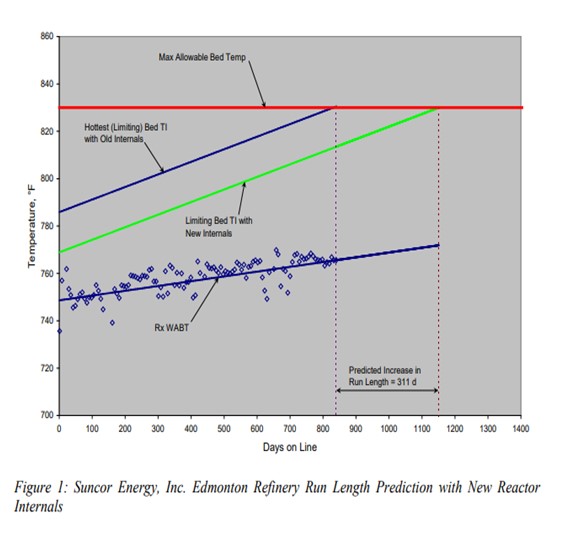
In addition to the benefits mentioned above, the installation of new trays in hydroprocessing reactor vessels can provide additional reactor volume for catalyst and provide ease for maintenance personnel, increasing cycle length and reducing shutdown timing respectively.
SUBHASH SINGHAL (Kuwait National Petroleum Company)
Increased catalyst cycle length, more selective yield pattern, and reduced temperature mal distribution are some of incentives to justify reactor internals upgrade. For units facing temperature mal distribution and product selectivity, upgrading internals may prove a quick win. Test run on product pattern SOR to EOR and temperature spread across catalyst beds are some performance measures of internals.
ANDRE SCHAAP (Albemarle Corporation)
With product specifications becoming tighter and feedstocks becoming more difficult to process, maximum catalyst performance is needed. It is, therefore, of the utmost importance that there is no loss of catalyst performance or efficiency due to improper reactor internals. Reactor internals should make sure that all catalyst is fully utilized. The distribution throughout the reactor should be as close to perfection as possible and maldistribution should be avoided at all times. Any form of imperfect distribution will lead to losses in overall performance and efficiency.
Upgrading reactor internals to achieve a better distribution will lead to a higher efficiency of the catalyst system. This will, in turn, lead to higher catalyst performance. A system with a higher performance can:
• Run longer cycles,
• Run with lower product S/N,
• Run with higher aromatic saturation (more density/cetane uplift),
• Process higher throughput, and
• Process more difficult feedstocks.
As economic incentives cannot be linked directly to reactor internals, one should assess the economics of above parameters when evaluating reactor internal upgrades. This is particularly important for units that operate at high severity and require the highest catalyst performance, as shown in the figure below.
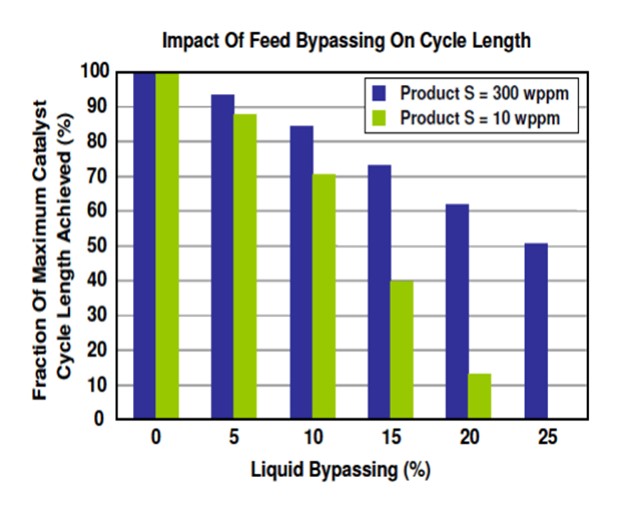
When shorter cycles than expected are encountered, it is worthwhile to evaluate the unit’s susceptibility to maldistribution from old or outdated distributor trays. Consistently high radial ΔT is one indication of maldistribution as is very limited turndown. Older trays can be more susceptible to directed flow from slightly off-level installation. If inspection indicates warping or leak points, these are also good indications that a new tray will significantly improve cycle length.