Question 17: Now that natural gas prices are low in North America, what options are available to increase refinery volume gain and product quality by exploiting low-cost hydrogen? Is the low hydrogen production cost impacting the economics between the selection of coking or hydrocracking?
CARLSON (Criterion Catalysts & Technologies)
There were a number of questions this year that requested information about how to effectively utilize low-cost hydrogen to increase refinery volume yields. To fully explore this theme, a Principles & Practices session will follow the Q&A and will cover the Strategies for Leveraging Low-Cost Hydrogen, including:
• Low-capital expense options (near-term),
• Product volume gain options,
• Optimizing H2 usage,
• Technology-based options for large capital projects (mid-long term), and
• Upgrading via H2-addition instead of carbon-rejection
Currently, as natural gas production hits unprecedented highs, we are fortunate that the cost of both natural gas fuel and hydrogen production has dropped to the lowest levels in the past decade. This cost-savings offers the opportunity to increase our utilization of low-cost hydrogen with the benefit of both higher liquid volume yields, as well as the capability of increasing the production of higher value products. Combined with the process efficiencies and capabilities gained in our facilities during the clean fuel's implementation, this current global advantage enables us to improve facility margins.
The chemistry available to us includes sulfur and nitrogen removal, aromatic saturation, selective ring opening, hydrocracking/conversion, and isomerization. With the implementation of clean fuels projects and continued catalyst development, many refiners are in the position of moving towards increased hydrogen uptake and reaping its benefits with minimal further investment.
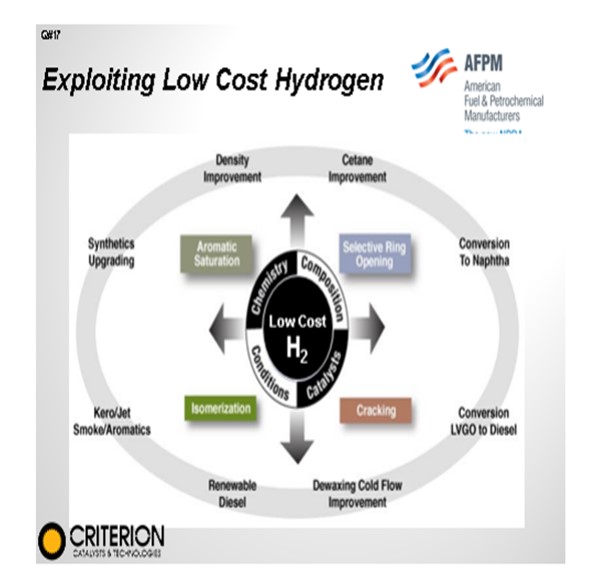
We have all spent a lot of time and energy increasing our hydroprocessing assets’ capabilities as we drive for clean fuels production. As we have done that development, advances in catalyst technology continue and have resulted in many “original” hydroprocessing unit designs now having additional underutilized capabilities. Many of these designs can be exploited with drop-in solutions during a catalyst changeout. By utilizing advances in catalyst capability, we can effectively provide additional reactor volume to provide further hydrogen utilization upgrades and extend days-on-stream or further increase unit capability by the application of additional upgrades utilizing the following technologies.
• Aromatic saturation can further enable density upgrades, smoke-point improvements, feed difficulty capability, and FCC yield gains.
• Selective ring opening will further improve density and volume swell while improving diesel cetane.
• Conversion via hydrocracking (distillate, VGO, resid) can minimize lower value fuels while increasing product quality and margins.
• Isomerization will improve distillate cold flow properties
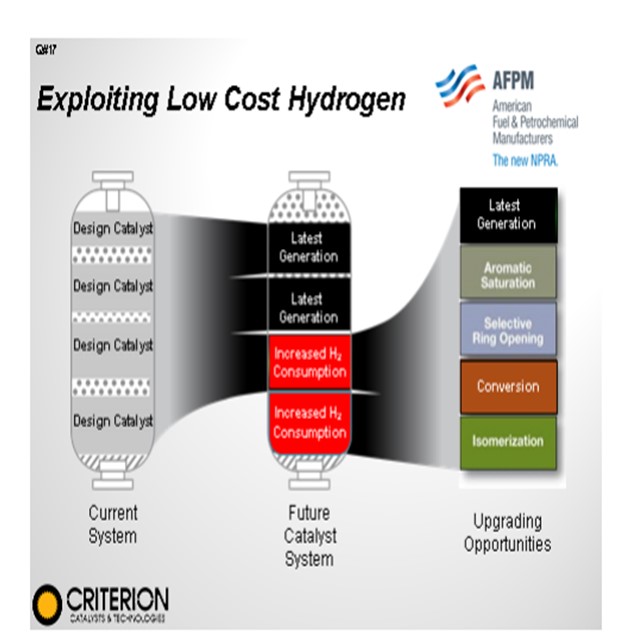
This graph highlights the impact of volume swell in distillate yield when applying some of the various technologies available. As you can see, the ultimate technology selection we choose for our own sites will really be dependent on the yield in volume gain for our facilities. We can really push the volume gain going to mild hydrocracking; however, we will start losing distillate selectivity. So, there is a wide range of options to evaluate when determining what is best for our facilities.
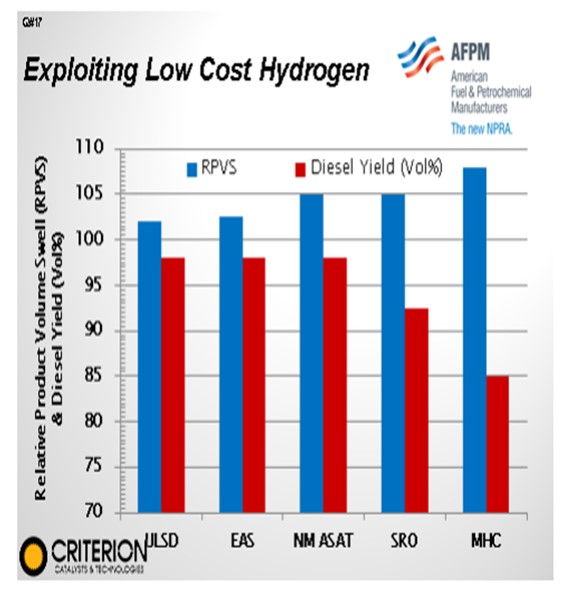
Beyond the gains we may be able to achieve with a drop-in solution, further capabilities can often be realized by combining these options with additional process improvements that can fit within a normal turnaround window. Improving reactor internals and instrumentation/control, as well as ensuring that the recovery and fractionation sections are in optimal condition, can all help push the level of performance while maintaining operational reliability and flexibility.
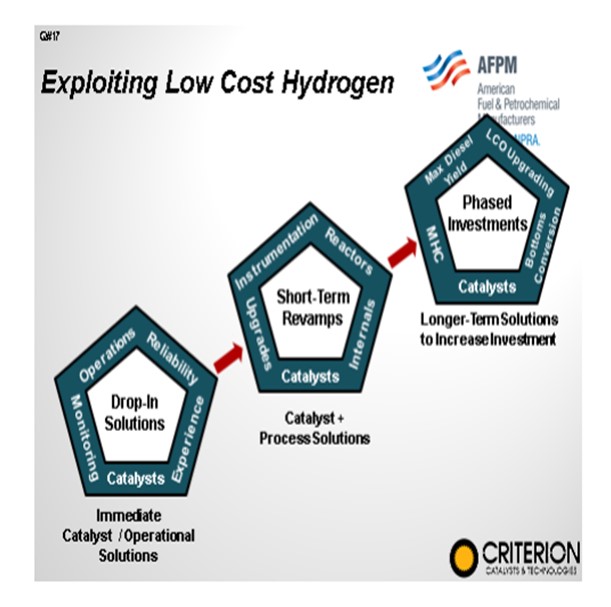
BODOLUS (CVR Energy)
Reactor internals have many benefits for you including increasing efficiency, extending turnaround intervals by improving gas to liquid distribution, and reducing hot spots. However, the tray hardware is often very expensive and difficult to install, so the costs need to be balanced by qualified economic benefits.
As far as the performance assessment, unit engineers can use techniques to track radial profiles versus axial profiles. There are many other examples of pulse technology in the Answer Book. I know Kevin included good examples in his response, in addition to tracer studies. Also, outside vendors will help you prove that you need new trays and provide justification for them. One issue I have come across in the last 10 or so years is having new generation trays that show a significant decline in performance in use. You cannot really justify a whole new set of trays, primarily due to the fact that these trays have gotten fouled out and dirty. Also, it is often very, very, very difficult to clean them during the short window of a turnaround outage.
I have a case study with a couple of photos that are worth a thousand words. The case study was on solid CO2 (carbon dioxide) blasting. Shown are the innards of a typical hydrotreating reactor. This is the catalyst support bed. The catalyst pellets get embedded in that Johnson screen down at the bottom. The wedge wire is very difficult to clean. It could take a guy a couple hours to clean this.
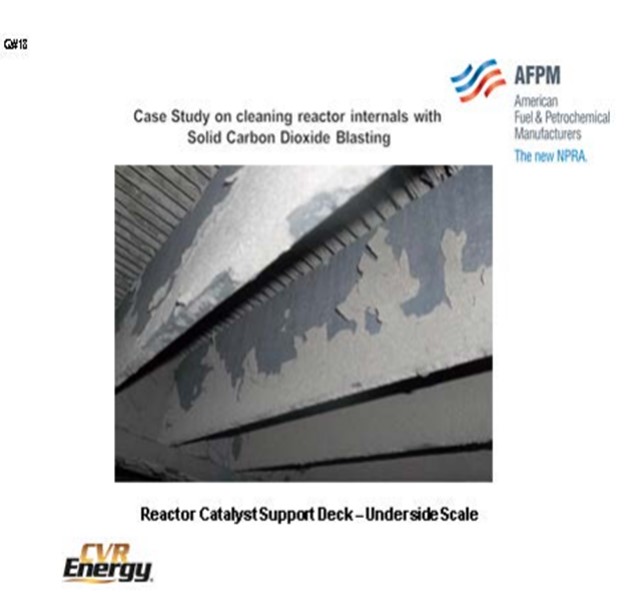
The next photo shows you underneath the hood and the tray support. As I mentioned a little earlier, you will find iron sulfide scale there. And if you look up into the nooks and crannies, you will see all of these sheet-like deposits that can break off later. If you do not clean them out, they might break off later and cause you liabilities of pressure drop in your bed and maldistribution of flow.
The next slide shows the liquid distributor. It accumulates debris on the deck of these things. And if you look closely, you can see the iron sulfide scale all over the place. Historically, I have tried a lot of different techniques; hydroblasting done in with Tanner K hydroblasters. Two or three days later, the turnaround guys are all over you because you are still cleaning up the mess.
The next slide shows some of our success. From a distance, it might not look like it, but the wedge wire here is 80% to 95% better than it was when we started. If we zoom in on the picture, you can see the lights underneath. This picture shows that same distributor tray after it was been cleaned up with solid CO2 blasting, which is good because the CO2 just sublimes away. There is nothing to brush up or clean up, with the exception of just the dust that has formed.
This slide shows that same situation. This solid CO2 blasting gets into all of the little nooks and crannies and cleans things out. I want to tell you, it was a long shift. These tray pictures were taken after one 16-hour shift inside the reactor, which would have normally taken multiple shifts to do this level of cleaning with mechanical hand tools and vacuums.
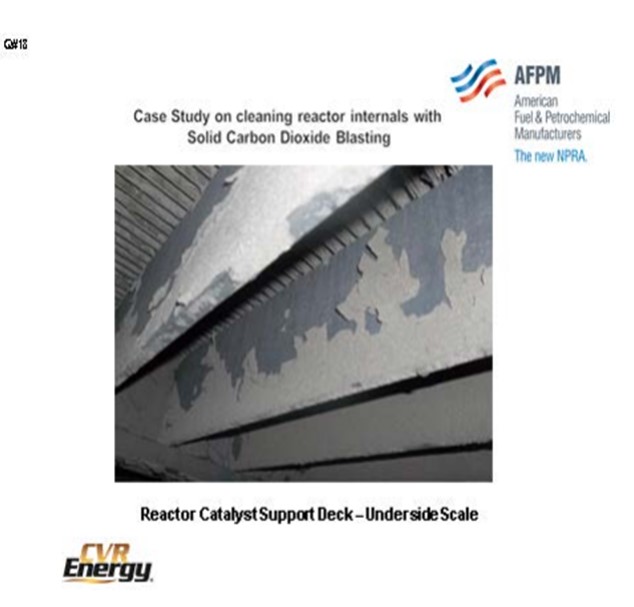
ROBERTSON (AFPM)
That is the response from the panel. Kevin and James have responses in the Answer Book.
PUI-NANG LIN (Flint Hill Resources, LP)
Very impressive pictures on the CO2 blasting performance! Are you doing this blasting under inert atmosphere, or do you have a concern about the confined space situation with CO2?
BODOLUS (CVR Energy)
This reactor was turned over to air, but the CO2 blasters do have the same inert atmosphere headgear. They have all of the requirements of an inert atmosphere entry. Even though the reactor is under air or under inert, it does qualify for all of the inert entry procedures. So yes, they operate as if the unit was inert.
PUI-NANG LIN (Flint Hill Resources, LP)
Do you use a specialized company to do this, or did your company personnel do this blasting in-house?
BODOLUS (CVR Energy)
It is a specialized skill that requires specific equipment, as I understand, and there are a number of folks who offer this service. I do not want to advertise any of them, so just contact someone who does solid CO2 blasting and can demonstrate it with a track record at refineries. We have also used convective section tubes in heaters, and the results are amazing.
CARLSON (Criterion Catalysts & Technologies)
There were a number of questions this year requesting information to how we can effectively utilize low-cost hydrogen to increase our refinery volume yields. To fully explore this theme a Principles & Practices session will follow the Q&A covering the strategies for leveraging low-cost hydrogen including:
• low-capital expense options (near-term) including product volume gain options and optimizing H2 usage,
• technology-based options for large capital projects (mid-long-term), and
• upgrading via H2-addition instead of carbon-rejection.
We are currently fortunate that with natural gas production hitting unprecedented highs that the cost of both natural gas fuel and hydrogen production have dropped to the lowest levels in the past decade. This offers the opportunity to increase our utilization of low cost hydrogen with the benefit of both higher liquid volume yields, as well as the capability to increase the production of higher value products. Combined with the process efficiencies and capabilities gained in our facilities during the clean fuels implementation, this current global advantage enables us to improve facility margins. According to a recent Hart Energy report, U.S. refiners have a greater than $6 per barrel advantage over Asian competitors.
The chemistry available to us is sulfur and nitrogen removal, aromatic saturation, selective ring opening, hydrocracking/conversion, and isomerization. With the implementation of clean fuels projects and continued catalyst development, many are in the position to move towards increased hydrogen uptake and its benefits with minimal further investment.
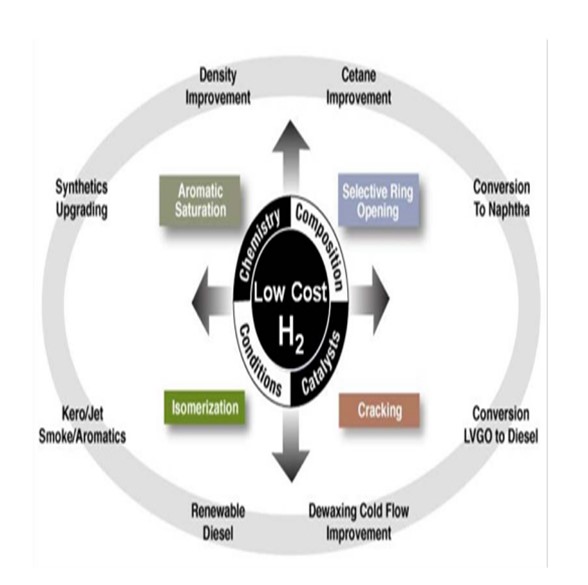
Looking at the existing applications in our refineries that can potentially increase hydrogen utilization we have a wide range of upgrade potential across the boiling range. To facilitate an accelerated implementation of this current opportunity we would first focus on what can we do with our existing distillate and heavy gas oil units to maximize volume gain and product quality benefits with “drop-in” solutions.
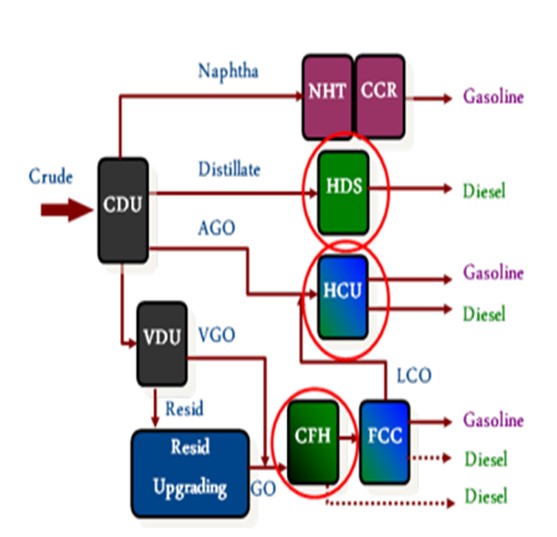
Development and advances in catalyst technology continue following the significant R&D efforts employed during the global clean fuel's initiatives. This has resulted in many “original” hydroprocessing unit designs now having additional underutilized capabilities, many of which can be exploited with drop-in solutions during a catalyst change out. By utilizing advances in catalyst capability, we can effectively provide additional reactor volume for further hydrogen utilization upgrades and the extension of days onstream. Examples of the benefits available through catalyst advances are described below.
• Aromatic saturation can further enable density upgrades, smoke point improvements, feed difficulty capability, and FCC yield gains
• Selective ring opening will further improve density and volume swell while improving diesel cetane.
• Conversion via hydrocracking (distillate, VGO, resid) can minimize lower value fuels while increasing product quality and margins.
• Isomerization will improve distillate cold flow properties.
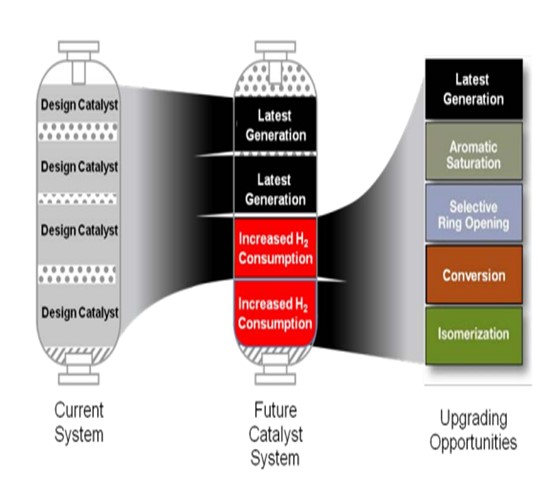
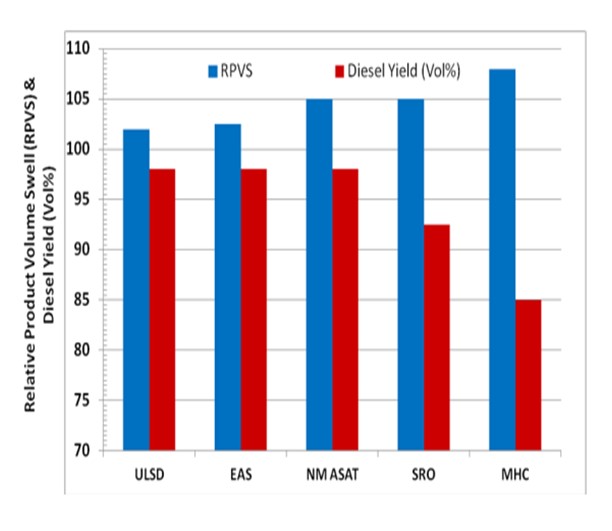
Beyond the gains we may be able to achieve with a drop-in solution, further capabilities can often be realized by combining these options with further process improvements that can fit within a normal turnaround window. Improving reactor internals and instrumentation/control and ensuring the recovery and fractionation sections are in optimal conditions can enable pushing the level of performance while maintaining operational reliability and flexibility.
The assets and economic situation of each refinery are unique, but new projects large and small can enable survival and even thriving in difficult economic times by including reliable and flexible technology selection. Taking advantage of the current low hydrogen and fuel costs to increase and upgrade our transportation fuels can be done with a combined effort of utilizing immediately available drop-in solutions, short-term revamps that increase capabilities of assets, and longer-term projects for taking advantage of global market fluctuations.
Today, advances in hydroprocessing technologies and reactor design are providing refiners the ability to meet these challenges, enabling reliable, successful operations into tomorrow.
STEFANO MELIS (Albemarle Corporation)
Hydrogen addition is one of best ways to increase refinery volume gain considering the current low cost for hydrogen. The easiest solution is to resort to more active hydrogenation catalyst in distillate or VGO hydrotreaters.
Regarding ULSD units, application of very active hydrogenation catalyst is recommended only if unit pressure is on the high side. At low pressure, additional aromatic saturation is often limited by thermodynamic equilibrium so that application of active hydrogenation catalyst is much less effective and may even reduce cycle length. In these units it is preferable to operate with the most active desulfurization catalyst. To maximize hydrogen uptake, the unit is operated close to its maximum aromatic saturation point right from start-up,
allowing sulfur giveaway. Operating temperature is kept constant until the S (sulfur) specification is hit and then progressively increased to compensate for catalyst aging. Such a strategy provides an average density gain by 0.5 g/l (grams per liter) to 1.0 g/l over the course of the cycle.
At higher pressure levels (i.e., hydrogen partial pressure at reactor outlet above 600 psi to 700 psi) use of catalyst with high hydrogenation power may lead to a significant volume gain of up to 5 g/l depending on unit specific conditions. However, application is not always straightforward. Extremely active hydrogenation catalysts have a tendency to coke due to local hydrogen deficiency, at the top of the reactor, for instance. In general, an optimal catalyst design technology (such as Albemarle’s STAX® technology) is recommended in which catalysts are sequenced according to the reaction chemistry of a particular location in the reactor. Very active hydrogenation catalysts are placed where they are most effective.
Evaluation of hydrogen addition in VGO hydrotreaters is more complex since economics is related to the modification in the yield structure of the downstream FCC unit. Also for this case, hydrogen addition can be achieved through dedicated catalytic solution coupled with dedicated operating strategies. Once again, if hydrogen pressure of the unit is on the high side, there are more possibilities to improve the density gain. In general, better density gain in the VGO hydrotreater corresponds to higher conversion and better product quality (with particular reference to light cycle oil) in the FCC unit. However, coke formation in the FCC tends to decrease and this might become limiting.
Another approach to improve the density of the VGO hydrotreater (particularly those operating at high pressure) consists in the increase of severity, with particular reference to the operating temperature. In this way, the main result is the increase in the conversion to middle distillate which is anyway balanced by a reduction in cycle length. Such severity increase also leads to a decrease of bottoms density (with related modifications in FCC yield structure) and always to an increase in hydrogen consumption. Of course, a reduction of bottoms throughput is consequential.
One way to improve refinery volume gain is to modify the operation of the conversion units; for example, shifting some feed from coking/visbreaking units to hydrocrackers (i.e., cutting the VGO deeper). Such an approach may be favored by the low hydrogen cost; but since it affects refinery yield structure, other market specific factors may overrule