Question 15: As hydrotreating catalyst development continues with the emphasis on activity and saturation, how has this changed optimization strategies for the entire hydrocracker?
NEIL HOWARD (Chevron Lummus Global)
Advances in hydrotreating catalyst technology continue to produce steadily increasing performance for hydrocracking pretreat service. These improvements result in increased HDN and aromatics saturation performance which are key to optimizing overall hydrocracker performance.
There are many ways this improved performance can be utilized:
-
Processing lower cost, more difficult to treat feedstocks
-
Targeting deeper HDN to install lower activity, more distillate-selective hydrocracking catalysts
-
Taking advantage of lower start-of-run temperatures to target longer cycle length
Processing more difficult feedstocks
Improvements in pretreat catalyst activity has steadily continued over the last several years, which has made it possible to send more profitable feedstocks to the hydrocracker. This can be through more refractory feed selection, or simply increasing the boiling range of the hydrocracker feedstock by cutting deeper in the vacuum distillation unit.
Below is an example which shows an increasingly heavier feedstock with each progressing catalyst cycle made possible by more active pretreat, as well as a more nitrogen tolerant cracking catalyst system. In this case, the refiner’s crude source has been reasonably constant, but advances in the pretreat and the cracking catalyst systems have allowed them to progressively process heavier feeds with each subsequent cycle by going up in feed endpoint.
Table 1: Feed Basis Over Subsequent Cycles


Increased options for cracking catalyst selection
More active pretreat systems also allow for more flexibility in cracking catalyst selection. For example, by going to a more active pretreat system, it is possible to trade off this activity gain with the use of a more middle distillate selective catalyst in the cracking system. Below is an example of a typical progression of this nature. In this case, the refiner is targeting maximum middle distillate within the constraints of a minimum 30-month cycle length. By installing a more active pretreat system, the refiner can make use of a more middle distillate selective cracking catalyst in one or more beds of the hydrocracking reactor. The impact of going to a more distillate selective catalyst in the last bed of such a system is significant, as the selectivity improvement in this highest conversion regime of the hydrocracking reactor is most pronounced.
Figure 2: Increasing the Pretreat Activity with Newer Generation Hydrotreating Catalyst
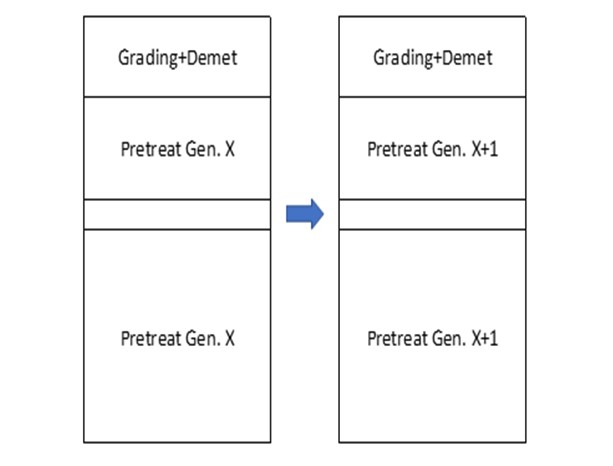
The increased activity of the pretreat system changes shown above enable the replacement of one bed of hydrocracking catalyst in the bottom bed of the hydrocracking reactor with a more middle-distillate cracking catalyst as shown below:
Figure 3: Increased Pretreat Activity Allows More Distillate Selective Cracking Catalyst
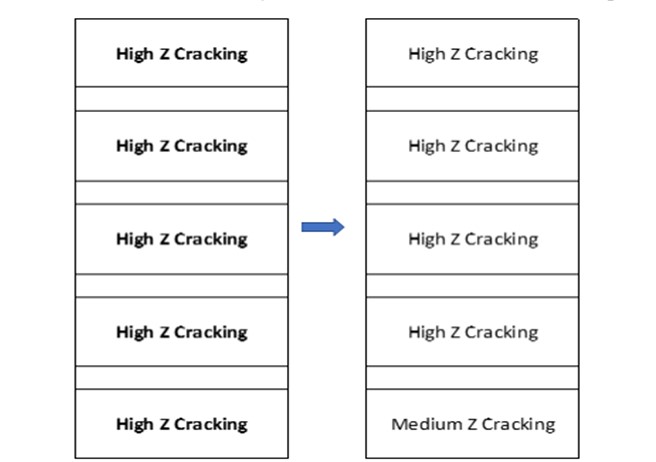
This one bed of more mid-distillate selective catalyst buys a significant improvement in middle distillate yield by virtue of its placement in the highest conversion environment in the reactor. It can be seen from the following comparison that the selectivity advantage of going to a somewhat lower activity, more mid-distillate selective catalyst, in the bottom bed results in a large boost in the marginal increase in middle distillate in this range of 60-70 lv% conversion.
Figure 4: Incremental Selectivity to Middle Distillate
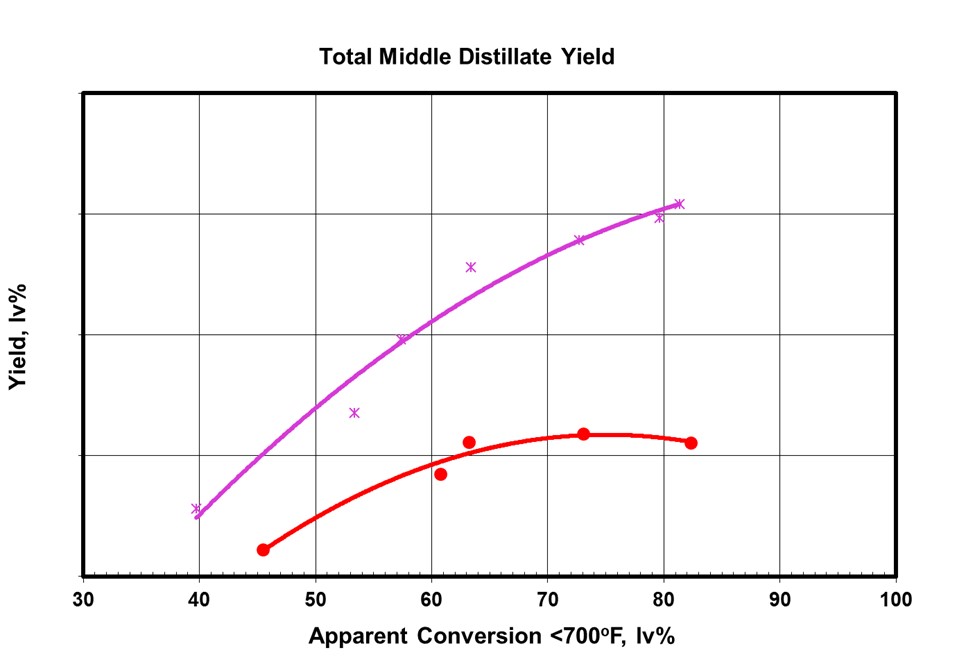
Self-Supported very-high activity catalyst options
Many catalyst vendors now offer very-high activity hydrotreating catalysts that are more often finding use in hydrocracking pretreat systems. These catalysts have much stronger aromatics saturation, HDN and HDS activities than conventional alumina-based catalysts. As discussed above, this activity improvement can be used to process more difficult feedstocks or take advantage of more catalyst flexibility because of the activity improvement in the pretreat section of the hydrocracker. Or some refiners find an economic payout in the form of longer cycle length afforded by such catalysts.
Below is an example of this concept in which a very-high activity self-supported catalyst is used to enhance the activity of the pretreat system to extend cycle length of the entire hydrocracker. The key to this sort of optimization is to appropriately size and place the self-supported catalyst to extract the maximum benefit. Because of the very high aromatics saturation activity, placement of such catalysts too high up in the pretreat system will result in excessive coking, which can prematurely deactivate the catalyst, and in some cases, make the catalyst difficult to unload due to hard coke ball formation. The sizing and placement will depend upon the feedstock and processing objectives.
To extend our example above, here is a case in which a portion of the pretreat system is replaced with a very-high activity self-supported hydrotreating catalyst.
Figure 5: Very-high Activity Self-supported Pretreat Catalyst System
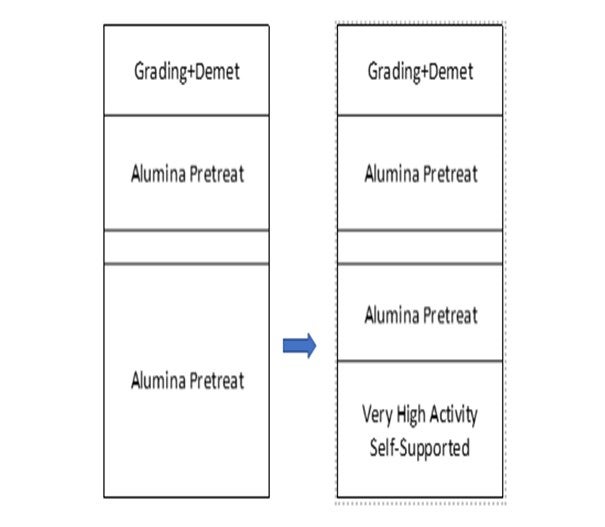
In this case, the resulting activity improvement allows a cycle length increase from 30 months to 36 months on the overall hydrocracker.
Optimization of Pretreat vs. Cracking LHSV
In addition to the examples above, many refiners will achieve more profitable operation by shifting the ratio of pretreat to cracking catalyst volumes with changes in process conditions or objectives. For example, it isn’t uncommon to trade out pretreat volume for cracking volume in cases where cracking activity is limiting. This type of adjustment is made possible by higher activity pretreat catalysts maintaining performance at higher LHSV. This can allow a refiner to maintain a more distillate selective catalyst system than would otherwise be possible with limitations in cracking catalyst volume due to capacity increases, or feedstock changes, over the life of the hydrocracking unit.
There are several considerations in implementing this type of adjustment. Typically, small layers of cracking catalyst can be accommodated at the bottom of the last pretreat bed. However, as this cracking layer is increased it is necessary to be aware of temperature control issues in the bed. To get around this concern it may be feasible to place the cracking layer at the top of the pretreat bed so that the temperature control at the bed inlet directly controls the temperature rise across the cracking catalyst portion of the bed. Alternatively, one can use a co-extrudate catalyst system with combined hydrotreating/hydrocracking functions to uniformly distribute the temperature rise across the entire bed.
The converse of this shifting of pretreat volume to cracking volume is also common for units in which increased capacity, or more difficult feed, necessitates more hydrotreating activity. In these cases, similar considerations come into play with respect to temperature control on a partial bed of pretreat and cracking catalyst. Placing a layer of pretreat atop the first cracking catalyst bed is most common; however, for very deep catalyst beds, a co-extrudate system will provide more stable temperature control.
JEFF CATON (Axens)
In addition to the points already discussed, a higher relative volume activity (RVA) pretreat catalyst can allow for a reduction in pretreat catalyst volume thus freeing up reactor volume for additional top bed grading and/or guard catalyst. For units that have historically had end-of-cycle either dictated by dP or contaminants, this additional grading and/or guard volume can allow for increased cycle length and better monetization of the pretreat and hydrocracking catalyst systems.
There have also been advancements in the area of increased nitrogen tolerance of hydrocracking catalysts (Refer to Figure 1 - Nitrogen Tolerance of New Generation Hydrocracking Catalyst). If there is enough temperature to drive conversion in the hydrocracking system, the temperature of the pretreat system does not have to be increased to maintain a very low nitrogen slip over the entire cycle. By allowing nitrogen slip to drift up towards the end of the cycle, this can provide benefits in terms of maximizing cycle length and/or by optimizing the pretreat system temperature profile in a maximum aromatics saturation mode.
Figure 1 - Nitrogen Tolerance of New Generation Hydrocracking Catalyst
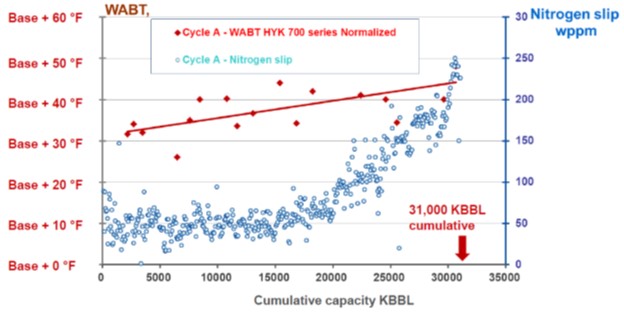
Alternatively, with this increased nitrogen tolerance, the pretreat catalyst volume could potentially be decreased as HDN activity requirement is reduced. Coupling this with current generation higher relative volume activity (RVA) pretreat catalysts, there can be an even more substantial reduction in required pretreat catalyst volume. As discussed previously, this decrease in pretreat catalyst volume can allow for an increased volume of grading, guard, and hydrocracking catalysts.
WENDY WILDENBERG (Flint Hills Resources)
A choice to install catalyst with higher aromatic saturation has allowed the shutdown of a small Jet Aromatic Saturation unit. The Hydrocracker is now able to achieve in the same unit what both units together were accomplishing.