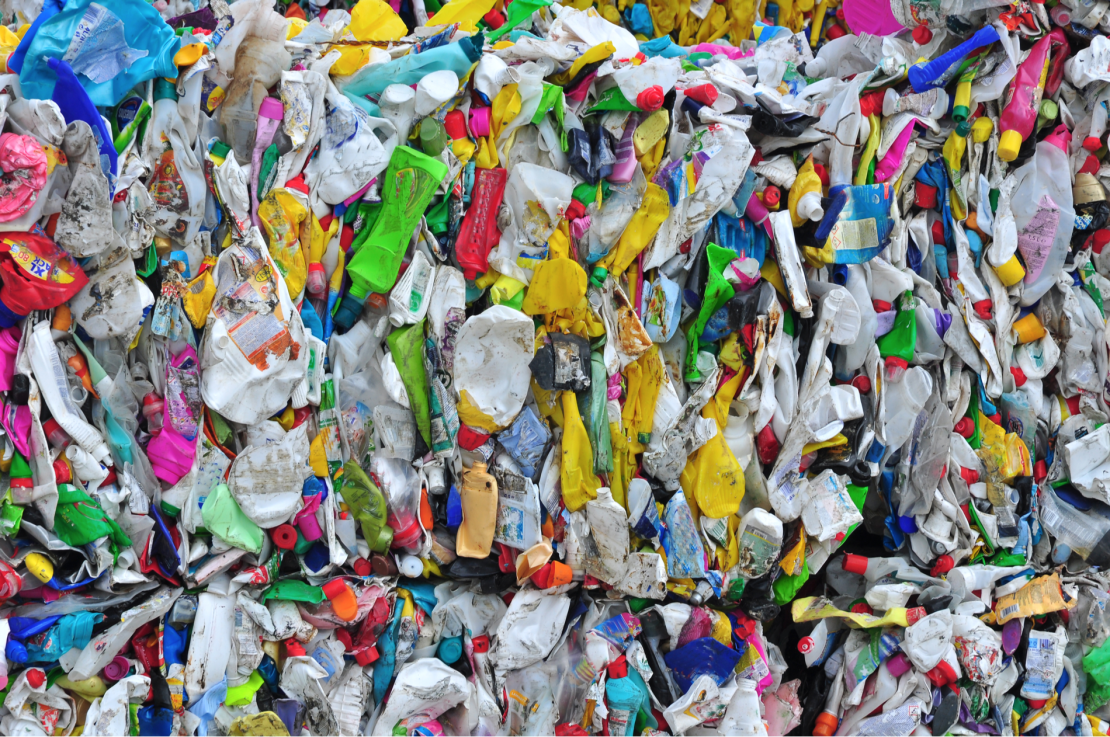
U.S. petrochemical manufacturers are at the forefront of research and development into cutting-edge solutions to give new life to used plastic products. Leveraging their in-depth understanding of plastics’ molecular composition and the manufacturing process itself, AFPM members are investing in recycling technology, infrastructure and partnerships that will reduce mismanaged plastic waste by applying unlocking its value as a feedstock.
Rob Benedict explains the science behind the advanced recycling of plastics.
A challenge with traditional mechanical recycling is that material properties degrade during the process – plastics can only be recycled a limited number of times before the material loses the required quality and durability for further use.
But in recent years AFPM members have been progressing advanced recycling processes that break used plastics all the way down to their original building blocks, known as a monomers. Used plastics can go through this advanced recycling process over and over again, while maintaining the same quality and strength offered by virgin plastics. This technology will enable society to successfully reuse the molecules of discarded packaging and other mixed plastics waste that might otherwise be sent to landfills.
AFPM members Dow, Chevron Phillips Chemical, Eastman, ExxonMobil and INEOS have all made major announcements about advanced recycling projects in recent months. Eastman, for example, plans to build “one of the world’s largest plastic-to-plastic molecular recycling facilities” in Kingsport, Tennessee. The company plans to invest $250 million in the facility that “will use over 100,000 metric tons of plastic waste that cannot be recycled by current mechanical methods to produce premium, high-quality specialty plastics made with recycled content.”
Learn more about the innovations, partnerships and policies AFPM members are advancing to enhance recycling and address mismanaged plastic waste here.