Navigating our current health crisis offers frequent reminders of the critical role petrochemicals, particularly plastics, play in daily life — whether in the masks and gloves that protect our frontline health care providers, the containers that hold our takeout food, or the wrapping that keeps our groceries fresh and clean.
Much of the value of these and other similar products is derived from the fact that they significantly lessen contamination concerns, since they can be discarded after use. However, petrochemical manufacturers are working on novel “molecular” recycling solutions to give new life to plastic products — including many single-use plastics — so they can safely provide value over and over again.
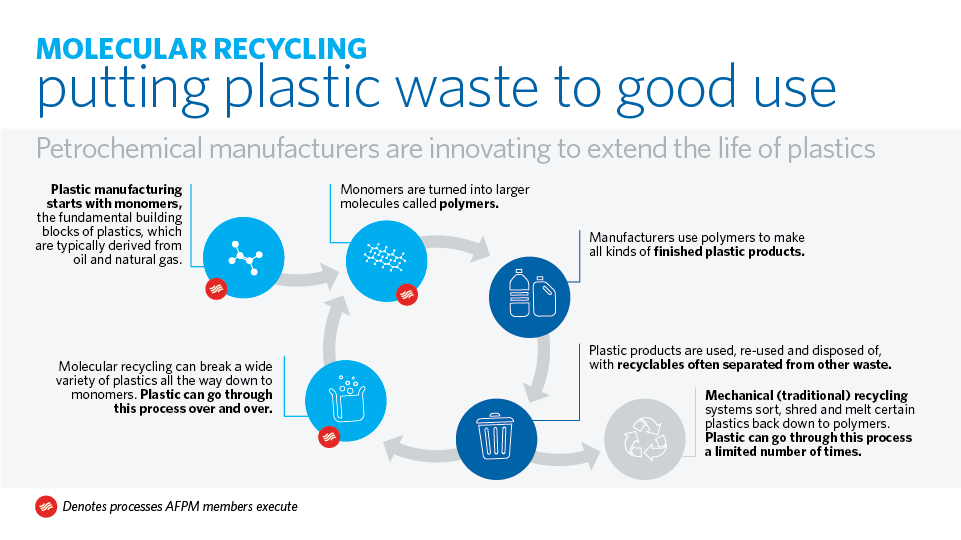
Plastic products are made from big, long-chained molecules called polymers. Polymers are made up of many individual units of repeating smaller molecules called monomers. These monomers are made from a small number of building block molecules called base petrochemicals. Six of the most important base petrochemicals are ethylene, propylene, butylenes, benzene, toluene and xylenes. In other words, petrochemicals make monomers that make polymers that make plastic products.
Traditional “mechanical” recycling systems sort, shred and melt certain plastics down to their polymer level — a process that can be repeated only a limited number of times before polymer chain degrades and the recycled plastic loses strength. But in recent years, petrochemical manufacturers have been advancing molecular recycling, also known as chemical recycling, which can break a wider variety of plastics all the way down into their smaller monomers — and plastics can go through this process over and over again. Breaking used plastics all the way down to their fundamental monomer units offers a wider range of possibilities for re-use — whether the monomers go into fuel products, chemicals or new plastic products.
The U.S. petrochemical industry, with the full force of its engineering expertise and creative problem-solving, is driving molecular recycling advancements for a more sustainable future. Here are just a few examples of how:
-
Eastman has developed carbon renewal technology, or CRT, which breaks down waste plastic feedstocks into carbon molecules, like a 3-D printer in reverse. Then, just like carbon in a 3-D printer, that former waste material can become an infinite number of new products. Through this process there is no degradation of quality so it can be repeated over and over again. In addition, Eastman is pushing its polyester renewal technology, or PRT, which involves taking waste polyesters from landfills and other waste streams and transforming them back into a raw material that is indistinguishable from traditional polyester.
-
In February, SABIC supplied Avery Dennison, the label design and manufacturing company, with a material for label-making that was made, for the first time, from recycled polypropylene. “We have come a very long way with adding recycled- and sustainably sourced products to our portfolio and polypropylene is a very important addition,” said an Avery Dennison representative.
-
In January, Dow signed a deal to buy recycled polyethylene pellets from Avangard Innovative, a Houston-based waste-optimization specialist. The move enables Dow to provide recycled content plastic to its North American customers. “This collaboration combines AI's waste collection and sortation technology with Dow's materials science expertise, application expertise, and operational scale,” said a Dow representative. "We’re giving our customers the tools they need to supply consumers with products made from recycled plastic, like the liners they place into their waste bins and the shrink wrap they use to bundle and ship packaged goods.”
-
Some petrochemical makers operating in the U.S. are also progressing molecular recycling technology elsewhere across the globe. INEOS and Plastic Energy are building a new chemical recycling plant to come on stream at the end of 2023. “It is very important to us to constantly increase amount of plastic which is recycled in line with the INEOS pledge: By 2025, we will incorporate at least 325,000 tonnes/year of recycled material into products,” said an INEOS representative.