From the wings and fuselage to the seats and overhead bins, petrochemicals have been increasingly relied upon to make passenger aircraft lighter and stronger, cutting fuel use and costs and making air travel more sustainable at a time when more people are flying than ever before.
A modern transatlantic flight requires more than just spruce wood — the Wright Brothers’ material of choice when they made aviation history at Kitty Hawk — and the aluminum designs that dominated many subsequent decades of aircraft. Instead, petrochemicals are increasingly being used as the building blocks for lighter and more durable aircraft parts made from advanced plastics — also known as “composite materials.”
In Boeing’s groundbreaking 787 Dreamliner, you will find composites made from ethylene, propylene, benzene and other petrochemicals on nearly all exterior surfaces, including throughout the fuselage, wings, tail and doors.
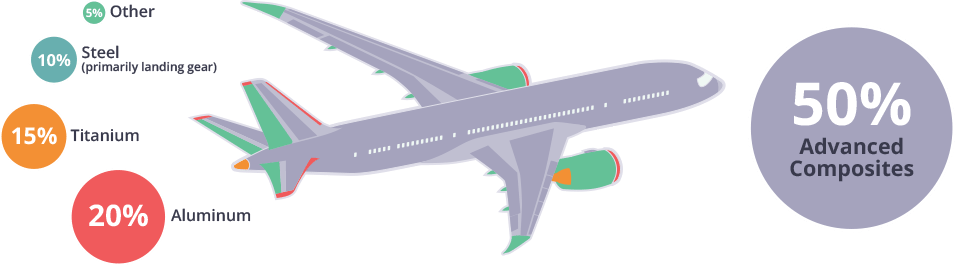
They also dominate the plane’s interior, including overhead stowage bins and sidewall panels made from fiber-reinforced plastic in a honeycomb pattern with a sheet of phenolic resin facing. The honeycomb configuration and fiber reinforcement give the aramid plastic strength, durability and fire resistance while providing for lighter weight and easy cleaning.
Airplane seats have also evolved. Seats were commonly constructed using a simple polyurethane foam cushion covered by a fire-resistant fabric, all under a wool and polyester blend seat cover. Modern seats now use a combination of polyurethane and polychloroprene, which preserves fire resistance and comfort but also reduces overall seat weight.
Even the floors you walk on in an aircraft are made of these petrochemicals. This galley floor is typically polyvinyl chloride (PVC), which is able to withstand harsh environments. During more than a decade of service, not a single composite floor beam has had to be replaced in the Boeing 777 aircraft.
By putting all these pieces together, more than half of the Boeing 787 airframe is made up of a variation of petrochemicals, resulting in a 20 percent reduction in the weight of the aircraft compared to conventional aluminum designs.
Indeed, increasingly one of the biggest upsides to petrochemicals is the fuel efficiency and sustainability benefits they enable. The heavier the plane, the more fuel it takes to get from takeoff to touchdown. This additional fuel means more costs to airlines.
Each pound of weight on a plane, either interior or exterior, equates to about $10,000 in fuel costs annually, according to Huntsman. Even cutting an ounce of weight from United’s planes saved nearly $300,000 per year.
By 2050, these composite planes could reduce emissions from the global fleet by about 15 percent compared to a fleet that maintains its existing aluminum-based configuration. To provide a better picture, transitioning to a composite-based fleet could avoid 500 million metric tons of carbon dioxide emissions in 2050 alone, a value that roughly corresponds to current emission levels.
The importance of this innovation is heightened further amid ever-increasing air travel. Last year, U.S. and foreign airlines serving the U.S. for the first time carried 1 billion passengers systemwide — a nearly 5-percent increase from 2017.
As air travel continues to get people and goods where they need to go, petrochemicals and the advanced plastics they enable are making the process more efficient than ever.