Question 99: We are struggling with high afterburn in the regenerator. What hardware changes (spent catalyst distributor, air distributor, etc.) have you implemented to improve afterburn? What commercial experience exists using computational fluid dynamics (CFD) to resolve such issues?
Peter Blaser (CPFD Software, LLC)
CFD has been successfully used to predict afterburn in FCC regenerators. A published example was presented as part of the CFD Case Studies workshop at the 2012 AFPM Cat Cracker Seminar (session CAT-12-101) as well as at the 2012 AIChE annual meeting. For more information see: 'Clark, S., Snider, D., and Fletcher, R, "Multiphase Simulation of a Commercial Fluidized Catalytic Cracking Regenerator",Presented at the AIChE 2012 Annual Meeting, Pittsburgh, Pennsylvania, (2012)'.
In that example, the CFD model accurately predicted the magnitude of the afterburn (approximately 100 degrees F as shown in the attached image) as well as the non-uniformity of cyclone temperature distribution. Once validated, the model was used to rule out the distribution of spent catalyst as the primary cause of the afterburn for that case. Instead, the afterburn was attributed to poor mixing of the multiple air sources with the catalyst in the shallow bed, leading to some undesirable dilute phase combustion. An animation of the results can be found at http://cpfd-software.com/resources/videos/cfd-simulation-of-a-full-scale-commercial-fcc-regenerator.
However, other unpublished CFD studies have reached different conclusions for other FCC regenerators. Recent analysis of a regenerator at a US refiner showed asymmetric afterburn was directly related to the mixing of the spent catalyst in the bed as directly influenced by the spent catalyst distributor. Based on this, it's not likely that a single hardware change will be effective in all cases. Instead, CFD can be used as a tool to understand the root cause of the phenomena resulting in the afterburn for a particular regenerator operating under a particular set of process conditions. Using the CFD models, proposed modifications can be evaluated and compared prior to shut down and installation.
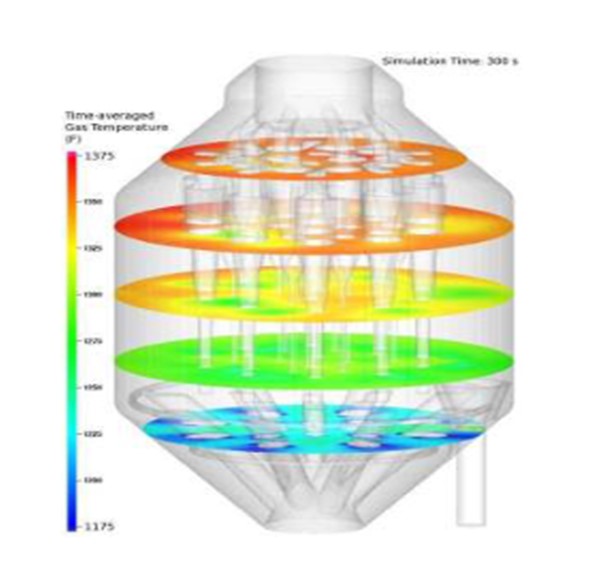