Question 99: Are there any uncommon FCC metal contaminants showing up on equilibrium catalyst in addition to Ni, V, Fe, Na, and Ca? Are metals traps able to protect the catalyst by selectively capturing Fe, Na, Ca, or any of these uncommon contaminants?
Ray Fletcher (Intercat)
Typical Contaminants
Each of these catalyst poisons may have a significant impact on the FCC catalyst circulating inventory depending upon their concentration. Vanadium will form vanadic acid resulting in the sintering of the zeolite crystal thereby reducing activity. Nickel increases hydrogen yield potentially leading to wet gas compressor constraints and increases delta coke leading to main air blower &/or regenerator temperature constraints. Both iron and calcium deposit on the surface of the catalyst particle leading to possible pore blockage and loss of bottoms conversion. At higher concentrations iron will form nodules on the surface of the catalyst particle and reduce particle density. Calcium is observed to pass through a "cliff" in which the unit conversion is a observed to drop precipitously while the measured activity drops to a much lower degree. Sodium is a permanent poison neutralizing catalyst acid sites thereby resulting in lost activity.
The classic solution to most of these issues has been to dilute the metals using purchased equilibrium catalyst thereby minimizing their effect. Each catalyst and of course your favorite additive supplier has vanadium traps for absorbing excess vanadium. Each catalyst supplier is capable of incorporating crystalline alumina for the encapsulation of nickel thereby reducing its effect on selectivity's. Antimony is well established for passivation of nickel, but the benefits are reduced when good quality crystalline alumina systems are in place. The FCC process engineer is advised to closely monitor crude unit desalter operations for maximum sodium removal. Care is also advised in receiving purchased FCC feedstocks transported cross the oceans for sea water contamination.
Intercat has recently been asked to help deal with the consequences of processing a feed contaminated with molybdenum. The source of contamination was never made clear, but it is believed that it was related to treatments being made to an upstream FCC feed hydrotreater. In this case, Cat Aid was found to be very effective at dealing with the negative side effects from this feed which included hydrogen, dry gas and coke. Hydrogen was reduced by 50% while dry gas dropped by 15%. Coke yield was improved by 6% relative. The bottoms-to-coke ratio also showed a strong improvement.
Nitrogen
Cat-Aid has also been successful particularly in the trapping of nitrogen. Refiners utilizing this technology have in every instance observed an increase in conversion together with the capability of reducing fresh catalyst additions. Typical catalyst addition rate reductions range from 15% to 50% at constant conversion. In each of these operations the activity of the circulating inventory dropped as expected. Fortunately, FCC units are run for conversion and not for activity. Each application has been considered a success. Additionally, many of these units have been able to extend the feed slate to heavier more contaminated feeds thus improving both unit flexibility & profitability.
Mercury
Mercury has been observed in some FCC units. Mercury is present in some, not all, crudes. It is reported that a "belt" of mercury appears to be associated with the boundaries between existing or ancient tectonic plates. In particular, it is reported that the largest mercury deposits in the world are located above areas in which plate subduction has occurred in combination with a degree of volcanic activity. Therefore, mercury most commonly occurs in crude oil that is derived from walls which are located at or near current or historically active plate boundaries. When present the mercury is typically present at ppb levels - perhaps several hundreds of ppb in some cases. Mercury is present in different forms, metal, organomercury compounds, inorganic mercury compounds.
Mercury is toxic metal with a relatively high vapor pressure. Because of its high density and tendency to agglomerate and "bead" it can also be concentrated in drains and other low points of process plants. The potential exists for workers to be exposed to mercury upon opening or cutting any mercury containing pipe work. Hot work would be especially dangerous in this regard. Mercury has a tendency to contact and interact with steel surfaces of pipe work and other equipment and has been found at concentrations up to 10 g/m².
Mercury compounds within crude oil can be characterized into four broad classes including: hydrocarbon soluble, water-soluble, asphaltenes and sediments. Volatile hydrocarbon soluble mercury species tend to track through the refinery with the very lightest hydrocarbon product streams. It is therefore expected that most of these species will be found in and around the streams issuing from the top of the atmospheric column. However, some mercury will boil within the VGO and residue cuts and therefore may be found within FCC units.
One particular refiner found pools of mercury in the FCC flue gas line during a shutdown! This led to multiple employee lawsuits. So it can get clearly get into the FCC. Johnson Matthey has developed a range of mercury traps entitled, PURASPEC, which are able to capture mercury species. Refiners observing mercury within their units are recommended to consider this technology.
Iron
While not a new contaminant, we have observed some interesting and unexpected side effects from high levels of iron contamination recently. It has been observed in several FCC units that as iron concentration on the equilibrium catalyst increases the uncontrolled SO2 emissions also increase. The half-life of this iron appears to be very short on the order of approximately 2 days. These increased emissions can be controlled by utilizing a SOx reducing additive, but large amounts are required as iron is very effective at increasing Sox emissions.
Rosann Schiller and Sudhakar Jale
(Grace Davison Refining Technologies) Appearance of an unconventional metal on your equilibrium report can be cause for alarm, but not all metals require action on the part of the refiner. Alkali metals such as sodium and potassium are naturally occurring in crude oil and their concentration is reduced by desalting processes. However, desalter upsets can cause carry over into the FCC feedstock and result in deactivation of the FCC catalyst, particularly under the oxidizing, high temperature conditions in the regenerator. Use of alkali metal contaminated water or steam around an FCC unit can also contribute added contaminants to the catalyst. Alkali metals cause a loss in activity due to neutralization of acid sites. The result is a loss of unit conversion, but not a change in selectivity as observed with iron, nickel, vanadium, or calcium. Flushing of the metal out of the inventory with additional catalyst additions will restore catalytic activity. Typically, only low levels of potassium oxide are observed in equilibrium catalyst [Figure 1].
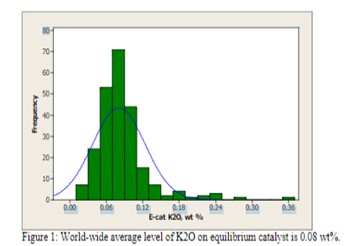
Magnesium is not of concern at low levels (<0.5 wt%), but at higher levels, it has a tendency to react with silica from the zeolite to form forsterite (Mg2SIO4), which will decrease zeolite stability and adversely affect unit conversion. Most of the MgO observed in equilibrium catalyst is due to the presence of SOx reducing additives and not feed contamination [Figure 2].
Lead is well known to cause the deactivation of combustion promoter. However in large enough concentrations on Ecat, Pb can also cause a loss in catalyst activity and conversion. Historical data reports a loss of as much as 1% conversion per 0.1 wt% Pb on Ecat. However, there are no units operating at these levels of Pb in the industry today [Figure 3].
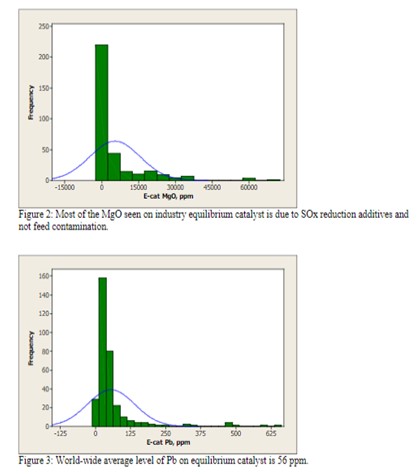
Crude can contain significant calcium naphthenate that may not be removed by conventional desalting and will find its way to the FCC. Calcium poisoning of the FCC unit can be a serious problem, reducing bottoms cracking and catalyst activity. The severity of the impact of calcium on FCC selectivities depends mainly on the amount of incremental calcium that is deposited on the catalyst and the rate of deposition. When the incremental calcium lays down on the FCC catalyst rapidly, the apparent effects of calcium on the unit performance can be more pronounced because there is less time for the unit operator to realize what is happening, identify the root cause of the problem, and take corrective actions. Very few FCC’s operate at high levels of CaO on equilibrium catalyst [Figure 4]; however, poisoning can be evident even at lower levels of contaminant if deposition occurs rapidly.
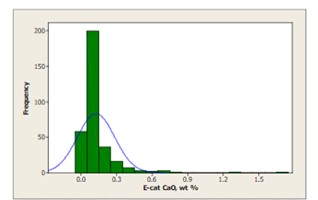
Figure 4: Less than 10 FCC's operate at levels of CaO over 0.75 wt%. The world-wide average level of CaO on equilibrium catalyst is 0.13 wt%, however, CaO poisoning can be evident even at low levels if deposition occurs rapidly.
The mechanism by which calcium deactivates FCC catalyst is similar to that of iron deactivation (Yaluris et al, NPRA 2001). The distribution of Fe levels on Ecat is shown in Figure 5. Both metals poison the catalyst by depositing on the exterior surface and over time, will build up on the surface of the catalyst forming rings typically 1-5 μm thick. As the rings form [Figure 6], Fe, and Ca combine with silica, sodium and other contaminants to form low melting temperature phases, which collapse the pore structure of the exterior surface, blocking feed molecules from entering the catalyst particle and reducing conversion. The diffusion of the large molecules inside the particle is the first to be affected by this phenomenon, therefore, the ability of the catalyst to crack bottoms decreases first with a corresponding decrease in cracking activity following.
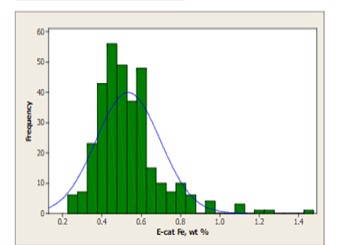
Figure 5: World-wide average level of Fe on equilibrium catalyst is 0.5wt%. The contribution from catalyst is included in this distribution. Approximately 10% of the refiners sampled operate at levels regarded as high.
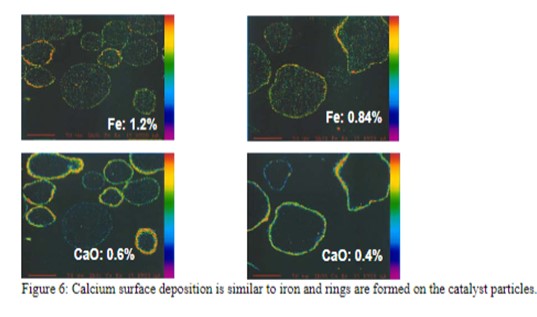
As the calcium or iron builds up on the catalyst surface and the exterior surface of the particle becomes compromised, the coke selectivity of the catalyst declines due to increased mass transfer limitations, which increase residence time of cracked products inside the catalytic particle and result in higher rates of secondary reactions such as coke. The combination of the loss of coke selectivity, combined with the loss of activity, results in further loss of in-unit conversion.
Figure 7 demonstrates the impact on conversion due to calcium poisoning from a refiner who experienced a doubling of CaO on Ecat in a short period of time due to a change in both crude source and desalter operation. Other contaminants such as sodium also increased in the same time period. In this example, laboratory ACE testing of Ecat demonstrates that the incremental calcium caused a loss of approximately 5 wt% conversion.
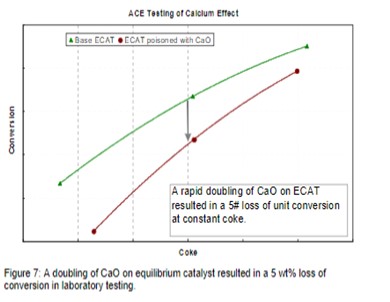
The refiner first observed an increase in bottoms and LCO yields on the unit along with a loss in coke selectivity. Increased catalyst additions were used to flush out contaminated particles and catalyst formulation was optimized to better handle future metals excursions.
Since Fe and Ca are not mobile species in the FCC unit regenerator, the usual trapping technologies, especially those based on separate additive particles are not effective for preventing cracking catalyst poisoning by Fe or Ca.
Several catalytic approaches are recommended to manage calcium issues. Optimization of the pore structure eliminates diffusion limitations. Maximization of the catalyst pore volume in the 100-600 Å range is the best for conversion of bottoms without compromising coke selectivity. Improving coke selectivity of the catalyst will improve performance by offsetting the increased coke make caused by contaminant calcium. High alumina catalysts, especially catalysts with alumina-based binder and matrices, are best suited for operations where high Fe or Ca feeds are commonly processed because they are more resistant to the formation of low melting temperature phases that can destroy the surface pore structure.
In summary, if the increase in contaminant level is temporary, an increase in fresh catalyst addition rate will improve the performance of the catalyst. If high metals feeds will remain a component of the FCC feed, the refiner should minimize the amount of deposition on the Ecat and utilize a catalyst system appropriately designed to handle the potential surface destruction. Such catalyst should contain the appropriate amount of pores in the optimum size of 100-600 Å to overcome diffusion limits. High alumina catalysts such as Grace Davison’s MIDAS® catalyst technology are ideally suited for such applications.