Question 98 What measures have you taken to minimize catalyst expenses due to rare earth price inflation? Please include an economic comparison of using a high rare earth catalyst at a lower catalyst addition rate versus using a low rare earth catalyst at a higher catalyst addition rate. Are there alternatives to replace rare earth in FCC catalyst? Are there any negative yield shifts with these new technologies?
Ray Fletcher (Intercat)
Rare earth is an integral component of today's FCC catalyst. Rare earth adds catalyst stability and activity, functions as a vanadium trap and is the oxidizing agent within most SOx additives. Rare earth has also increased in price by over 1500% in the last 18 months. Rare earth has a direct impact on the split between LPG and gasoline in the FCC unit. As rare earth concentration is decreased LPG yield will increase potentially leading to wet gas compressor limitations.
It is suggested that the refiner wishing to minimize catalyst based operating costs consider achieving conversion via operating parameters rather than catalyst activity consistent with unit constraints. These variables include: increasing riser outlet temperature, decreasing feed preheat temperature, recycling an intermediate cut cycle oil or slurry, etc. This strategy is typically more effective during non-summer operations given the fact that most FCC units are limited in main air blower &/or wet gas compressor capacity. An additional strategy for the refiner possessing excess main air blower & catalyst circulation capacity is to consider recycling naphtha or light LCO to the riser. Neither stream will support itself in coke thereby reducing delta coke and increasing catalyst circulation rate for deeper conversion.
Intercat has commercialized a vanadium & nitrogen trap which has in every application resulted in a substantial increase in conversion and also reductions in fresh catalyst additions. This technology enables a refiner to reduce rare earth costs directly via a reduction in rare earth on catalyst concentration at constant conversion or indirectly via a reduction in fresh catalyst addition rate. This additive based technology presents a significant advantage to the refiner in that the effect is cumulative with the improvements made to the catalyst via the catalyst supplier.
The second part of this question is difficult to answer in absolute terms. There are several factors which determine catalyst costs on a daily basis. These include the base catalyst cost which is a function of zeolite content, alumina content, rare earth content plus other factors. Few catalyst suppliers would hold the zeolite content constant while reducing rare earth composition. In order to supply an answer to this question I have assumed that the zeolite-to-matrix ratio remains constant. This implies no changes in zeolite content. Additionally, the required additive injection rate will be primarily a function of the base catalyst intrinsic activity, equilibrium metals concentration and the deactivation rate. As the rare earth concentration on the catalyst decreases the impact of the hydrothermal conditions within the regenerator will result in an increased deactivation rate. The deactivation rate will likely vary between catalyst suppliers.
I have assumed that my typical FCC unit has the following characteristics: charge rate = 41,000 BPD, equilibrium V & Ni = 1500 ppm, target equilibrium activity = 70, fresh catalyst z/m = 3.5, RE/cat: 4.2 - 0. The catalyst cost is assumed to be $3000/ton at zero rare earth. Rare earth costs are estimated assuming variable pricing in $/mTon beginning at $8000 up to $150,000. This data shows that at historical rare earth pricing of two years ago the optimal rare earth concentration (when considering only catalyst costs and not product slate selectivities) was likely greater than 3.0 wt%. At rare earth costs of $100,000 and greater the optimum appears to be less than 1.5 wt%. The last portion of this question addresses new technologies to replace rare earth. We are aware that at least one catalyst supplier is commercializing a new catalyst technology containing a rare earth replacement. We expect that after the panel has provided answers that one or more catalyst supplier representatives will update us with their particular technology. We have reviewed no commercial data defining the stability of this technology and its applicability for heavy oil crackers. We understand that these catalysts have been targeted primarily for VGO operations.
Sudhakar Jale (Grace Davison Refining Technologies)
Grace Davison Refining Technologies has responded quickly to the issues of rare earth price and availability by developing new zero or low rare earth catalysts and additives. Early in 2011, Grace commercialized a family of these catalysts, called REpLaCeR™, for both hydrotreated and resid feed processing. The family of REpLaCeR™ catalysts includes REBEL™, REACTOR™, REMEDY™ and REDUCER™. The REpLaCeR™ family of catalysts utilizes proprietary zeolites and state-of-the-art stabilization methods to deliver performance similar to current rare earth-based FCC technologies. Simply removing the rare earth from a FCC catalyst lowers the Ecat activity significantly. Unit performance will suffer, in most operations, despite higher catalyst circulation rate which results with lower Ecat activity. Catalyst additions of a low rare-earth catalyst must be increased in order to preserve Ecat activity for those units that operate at a catalyst circulation constraint.
Table 1 summarizes a scenario comparing the base catalyst, base catalyst with low rare earth content and REMEDY™ technology where zeolite is stabilized with proprietary metals. The REMEDY™ technology provides the same activity as the rare earth containing zeolite and hence has the same catalyst additions. Table 1: Simply lowering the RE content will result in increased catalyst additions to hold Ecat activity.

The performance data and the resulting profitability for these three scenarios are summarized in Table 2. Unit constraints for the low rare earth catalyst and REMEDY™ case are air blower, catalyst circulation and wet gas compressor. The low rare earth option where the RE content of base catalyst is lowered is less economically attractive mainly because of higher catalyst additions and the need to reduce conversion due to a wet gas compressor constraint and a catalyst that is more LPG selective. REMEDY™ technology has good activity and selectivity retention vs. the base catalyst thus providing the economic savings of $0.5/B.
The economic advantage of using REMEDY™ catalyst is plotted in Figure 1. The RE2O3 content in low rare earth catalyst is reduced by 75%. This results in a lower catalyst price, but the daily cost increases by about 30% due to higher catalyst additions. REMEDY™ catalyst has 90% lower rare earth as compared to the base case catalyst and maintained same activity and catalyst addition rate as the base case resulting in 30% daily operating cost. A refinery with 50,000 bpd operation increased the profitability by $9 mm/yr (using recent Gulf Coast Economics).
In summary, the REpLaCeR™ family of catalysts introduced by Grace reduces the RE content significantly while maintaining the activity and catalyst additions resulting in a decrease of daily costs by 30%.
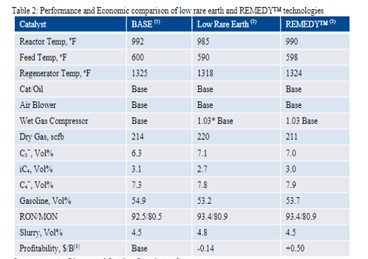
Operating at Air Blower and Catalyst Circulation Constraint
Operating at Air Blower, Catalyst Circulation and Wet Gas Compressor Constraint
Profitability includes total catalyst cost
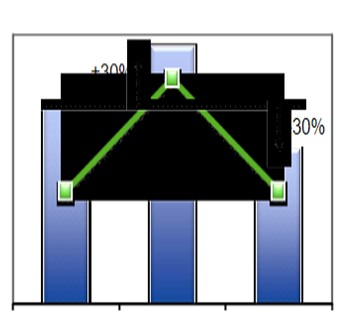
Figure 1: Economics of using REMEDY™ vs. simply reducing the RE content