Question 98: What catalyst changes can be made to minimize the negative effects of low delta coke that result from processing increased amounts of tight oil-derived FCC feed?
KOEBEL (Grace Catalysts Technologies)
The schematic on the slide shows the representation of the coke yield and the coke balance from the FCC. Of course, the total overall weight percent coke yield is set by heat balance, but the sources of the coke vary significantly from one feed to the next. Everyone talked thoroughly about how the coke precursors are just not there in these lighter feeds. The contaminant metals will be drastically lower, so your FCC catalyst will be called upon to provide a much larger percentage of the overall coke yield than it does in a normal operation. That can call on the unit to run a much higher catalyst circulation rate than it is physically able to do, so certainly you change the catalyst as warranted in these instances.

The next slide is a quick pilot plant representation of what happens in these cases. The darker blue represents a base VGO feed and the lighter blue: a shale oil type of feed. I will just pick a number here and say 2.5% coke yield in the pilot plant. In order to do that, we need about 5.5 cat-to-oil, which results in about 74% conversion in this operation on this catalyst. If we do nothing to the FCC catalyst and run the lighter feed, you can see that the required cat-to-oil to generate even that same 2.5% coke yield jumps up to 8%. So a full 50% increase in the catalyst circulation rate is required to keep the unit operating. We are talking about having to actually increase the coke yield, not hold it constant. That coke yield results in a little over 76% conversion. Clearly, a catalyst reformulation to a higher activity is in order here.
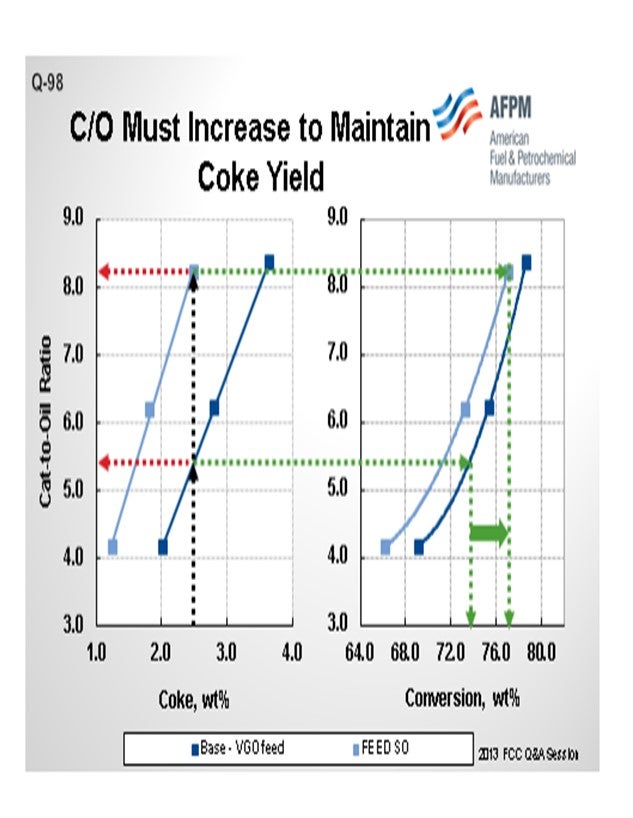
BULL (Valero Energy Corporation)
I am probably going to commit sacrilege here, from a catalyst vendor standpoint; but in many cases, a shift to a less-coke-selective catalyst can help process these increased amounts of tight oil-derived feeds. A catalyst with less zeolite and a higher quantity of non-active, non-coke-selective matrix can help you maintain a minimum regenerator temperature. We have actually done this at one or two sites.
JOE McLEAN (BASF Corporation)
I will go back to the previous question that we had before the break about the benefits of catalyst porosity. One thing you can do is reduce the porosity to reverse the delta coke benefits. We have a number of customers who have gone back to more old-style, lower porosity catalysts that are less coke-selective but just as active. These catalysts work quite well in this application. Because of the increase in conversion and, specifically, a big boost in LPG, we have seen at least one client take out ZSM-5 completely and still maintain the same light olefin yields that were in the previous operation with a fair amount of ZSM-5. So, in that case, the side benefit was the ability to save on the additive cost.
KEN BRUNO (Albemarle Corporation)
We agree, Jeff. There are cases where a lower coke selectivity is beneficial. But related to accessibility or the diffusion character with this kind of feed, quite often there is overcracking or secondary reactions that you do not want. So, it remains critical to have the right accessibility and porosity to minimize those secondary reactions.
WARREN LETZSCH (Technip USA)
I want to remind people that the pilot plant data is quite accurate. But when you start increasing catalyst circulation rate like this, chances are that the stripper performance may well deteriorate. You will have a much shorter residence time; and basically, you may end up pulling a lot more hydrocarbons through. It will be different for every unit, depending upon where you are operating and the type of equipment you have in it. I think if you have what I would call conventional a disk-and-donut type of stripper, then these types of circulation rates will almost guarantee that you will need to have much higher hydrogen on cokes because the flux rate will be very, very high. So, every situation is really different.
JEFF KOEBEL (Grace Catalysts Technologies)
Delta coke is the difference between carbon on spent catalyst as it leaves the stripper and carbon on regenerated catalyst. Delta coke is the primary variable that determines the regenerator bed temperature.
There are four primary sources of coke in the FCC process. They are: feed Conradson carbon, contaminant metals, stripping coke, and the catalytic coke produced by the FCC catalyst. The sum total of these four components adds up to the total coke yield in the FCC. Since the FCC heat balance determines the overall weight percent coke yield in the FCC process, a reduction in the contribution of one of these four coke sources must typically be offset by an increase in one of the other sources. For example, let us consider an extreme case, which is represented in Figure 1, of a unit that experiences a change in feedstock from resid feed to a light shale oil feed. When the unit shifts from heavy or resid feed to lighter feed, the total weight percent coke requirement does not necessarily change; however, the contribution of coke from each source will shift. Assuming stripping coke stays relatively constant, the feed contributes less to the required coke (feed carbon and contaminant); thus, the catalyst must make up the difference.
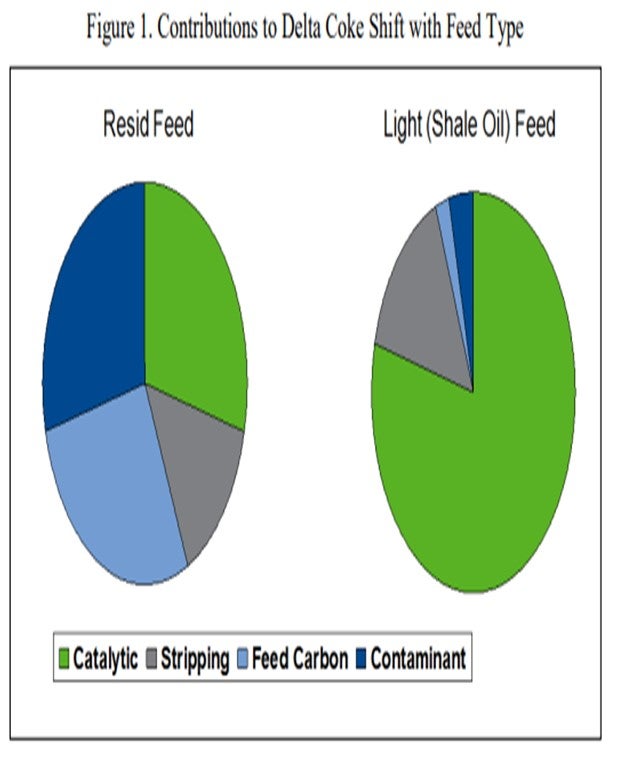
That means that the FCC catalyst will contribute a larger percentage of the overall heat required for the process. If the catalyst is not active enough, the catalyst circulation rate must increase so that conversion, and thus the coke yield from the catalyst, can increase to satisfy the FCC heat balance. This will lower the delta coke and the regenerator temperature. For a set riser outlet temperature, the lighter feed will require much higher catalyst circulation rates to satisfy the FCC heat balance. If the FCC catalyst section cannot physically circulate enough catalyst, it will be necessary to either reduce the unit charge rate or the reaction severity to stay within the FCC catalyst circulation limit.
In the pilot plant example below (Figure 2), an FCC unit operating on standard VGO is contemplating a move to lighter shale oil feed type. The base case catalytic coke of 2.5 wt% requires a cat/oil ratio of about 5.5 and results in 74% conversion. In order to keep the 2.5% coke yield with the lighter shale oil feed, a cat/oil ratio of over 8.0 is necessary with an increase in conversion to about 77%. Most FCC units are not capable of this dramatic increase in the catalyst circulation rate, and the catalyst circulation hydraulics will likely limit the unit severity or throughput.
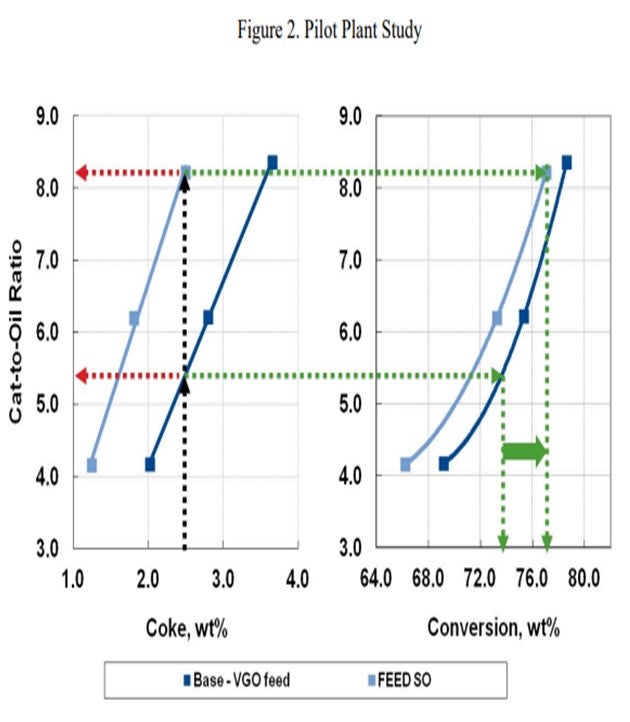
In this same example, we consider a catalyst reformulation to a more active catalyst with a different coke to conversion relationship (Figure 3). Here, Catalyst A is applied, and a much more modest cat/oil ratio of 6.5 is necessary to satisfy the coke yield. This is due to the inherent catalyst activity of Catalyst A. Because of the coke to conversion relationship of Catalyst A, higher conversion is achieved.
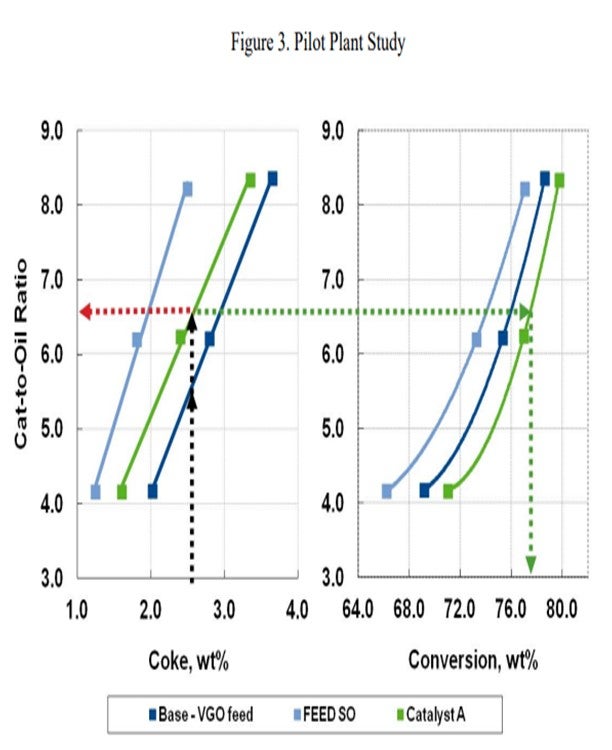
Grace has had multiple experiences with reformulations such as these for processing lighter feeds from shale oil or traditional hydrotreated FCC feed. Using a high activity catalyst is required to counter the effects of low delta coke, but it is important to select a catalyst with the proper coke selectivity (coke-to-conversion relationship).
Lastly, another issue with processing shale oil is the possibility of Fe and Ca contamination. To minimize the effect of Fe and Ca poisoning, a high porosity, high diffusivity catalyst should be considered. Since processing shale oils will often result in both issues (lower delta coke and high Fe/Ca), a high activity and Fe/Ca tolerant catalyst should be considered.
RAUL ARRIAGA and KEN BRUNO (Albemarle Corporation)
From a catalyst formulation point of view, it is recommended to increase catalyst activity and tune the selectivity's, including delta coke, to the desired targets while keeping the FCCU against its constraints. When optimizing the catalyst formulation, it is important to maintain or improve the mass transfer character of the catalyst. The objective is to prevent increased pore mouth blockage rates due to the higher amount of iron and calcium often observed in tight oil (TO)-derived feeds.
It is better to achieve higher catalyst activity with the use of high accessibility technology than with additional active ingredients, particularly zeolite, in order to maximize catalyst tolerance to iron and calcium. If the catalyst applied does not have the optimal pore and surface architecture, the result could be increased slurry yields and additional bottlenecks. Albemarle’s AMBER™ and UPGRADER™ are proven catalysts for use with tight oil.
One tactic to increase activity is to raise the amount of rare earth on zeolite for increased delta coke. While case-dependent, another approach for consideration is to reduce the use of vanadium traps or nickel-selective matrices which would enhance the metals contribution to delta coke. By the same token, if a refiner is consuming a flushing catalyst of any kind, it is recommended to re-think that strategy and evaluate reducing its utilization because lower use of a flushing medium may be desired to let metals concentrate on the catalyst. It is recommended to consult with various catalyst suppliers to compare the merits of each manufacturing technology and for commercial references with this new type of feedstock.