Question 95: What failure mechanisms have you observed in cyclone or cyclone support systems? What is the typical time to failure?
INKIM (PETROTRIN)
In the history of our unit, there have been no outright failures of cyclones or cyclone supports, just partial failures. In our experience, the major cause of failure in cyclones and cyclone supports has been erosion leading to thinning, cracks, and breakages. We have observed varying severities of erosion in the reactor and regenerator cyclones throughout the history of the unit. In the very early years, failures due to erosion were more frequent, and cyclone repair and replacement were required within five years or less. However, subsequent to the introduction of Resco AA-22 lining, replacement was required less frequently while some repairs were usually done at every turnaround.
Another failure type we have observed in the past is overstressing due to improperly designed cyclone supports. That was as a result of insufficient hanger rod clearance. We have also observed thermal fatigue associated with the use of quench steam to the cyclone outlets. For cyclone and hanger systems, excessive thermal cycling and temperature excursions above the design temperatures can lead to reduced life and subsequent failure.
Our design standard specifies that the minimum total design life must be at least 100,000 hours, which is about 11.4 years, accounting for short-term temperature excursions. We have been able to operate for lengths longer than 11.4 years based on our inspection. For our reactor, we have managed to operate with the cyclones for 29 years without replacement, but we did have to do minor repairs to them. Those cyclones were changed out as part of an upgrade because of the remaining life of the reactor at that time. The current cyclones in the reactor are now 17 years, and we have done some partial replacements on those. The regenerator cyclones also had longer run-lengths in the more recent past, with the last total replacements coming at 14- and 17- year intervals. The current cyclones in the regenerator are now over 12 years.
GIM (Technip Stone & Webster)
We have seen cyclones that have been torn apart during a campaign due to excessive high vapor velocities and catalyst velocity. We have also observed cyclones which operated for only a few years due to poor cyclone design. Additionally, failures in support systems are usually correlated with degradation of cyclones. Feedstock change from sweet to high sulfur content can affect some of the older carbon steel straps and hangers. Depending on the operation and cyclone design, the time to failure could be short; meaning, one campaign, part of another, or extended over a number of campaigns.
The biggest effect of cyclone life appears to be the amount of time the cyclone operates within the original design parameters. Multiple shutdowns with temperature excursions will obviously shorten the life of cyclones and their supports. Also, the high velocity will wear on the refractor protection and eventually on the cyclone metal itself. Cyclones running within design parameters can expect to operate between 16 and 20 years. Those which often run above the design parameters and have frequent shutdowns will obviously have a shorter number of campaigns.
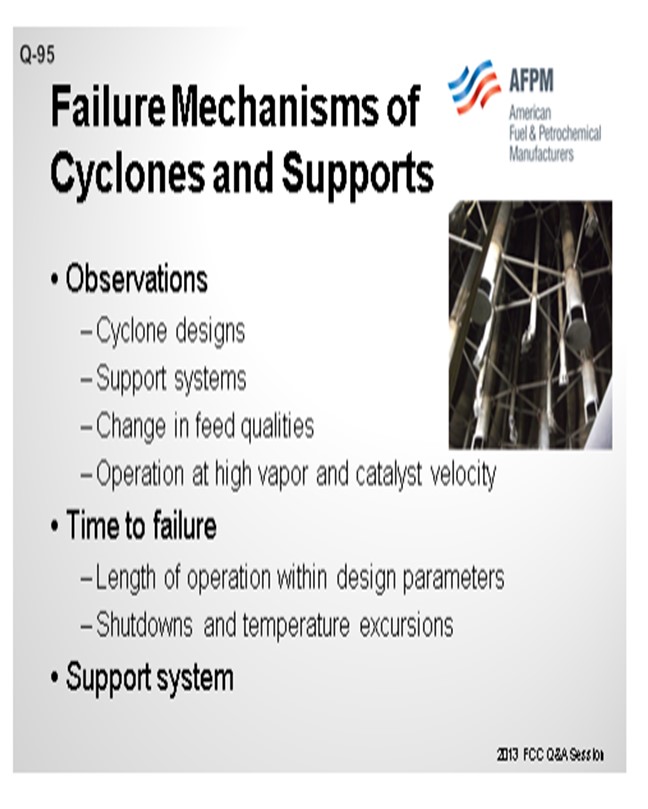
ROBERT “BOB” LUDOLPH [Shell Global Solutions (US) Inc.]
We found that in regenerator service, cracking in the welds is by far more common for systems that are properly designed for thermal expansion. Older systems have shown creep. The key to design is allowance for upset conditions that you anticipate during the campaigns. In the reactor service, distress, distortion, and even cracking has been observed if coke builds up and prevents free thermal expansion of the system. Key to success is to design for minimum or no sliding parts. In designs where relative movement of adjacent pieces cannot be eliminated, the design accommodates a “breaking force” for the coke. In some cases, materials are used which have shown that coke adhesion is not as strong.
Where galling is a concern, stainless steel with Stellite® surfacing has been used. For carbon steel cyclones that operate with moderate sulfur in feed, carburization and sulfidation take place. In a number of cases, the hanger itself is not necessarily the weak link; but rather, the attachment to the cyclone body. For maximum life, Shell uses a mix of carbon steel and chrome-molybdenum alloys. Carbon steel is economical and easy to repair, but the chrome-molybdenum will extend the service life, especially in high stress applications.
J.W. “BILL” WILSON (BP Products North America Inc.)
You have a few options. From my experience, unfortunately they are not particularly universal. From the standpoint of time to failure, if the failing problem is related to erosion, you can usually develop a tracking mechanism using cumulative velocities over time. We actually use velocity to the cyclone. But as I said, the answer of how far that curve can go seems to be unique to each unit; so, you have to use unit’s maintenance history to figure out your actual limits.
Bob talked about coke buildup. What can also happen is that you can get a coke ratcheting effect where the coke can build up causing you to shut down the unit. Coke and the steel have different expansion coefficients, so there is usually a little space for coke to build up again. So gradually over time, this coke deposition just pulls part the system. That is another reason why repeated shutdowns and startups are not good.
I would like to discourage the idea of there being a defined maximum life to the cyclone. For years, I have been hearing people say it is 20 years. There are currently lots of cyclones older than 20 years that are working fine, so it is really matter of the condition of the cyclone and the metallurgy. For regenerator cyclones, sigma formation that usually shows up is from an inability to actually repair them. You can have thermal stresses that cause distortion to a cyclone. These stresses are usually related to improperly designed hanger systems or other support systems. Other reasons are repeated operation well above where it should operate or repeated thermal cyclings of the cyclone: getting hotter and colder, hotter and colder.
CATHERINE INKIM (PETROTRIN)
In the history of our unit, there has been no outright failure of all the cyclones, or all the cyclone supports, but there have been several partial failures. In our experience, the major cause of failure in cyclones and cyclone supports has been erosion leading to thinning, gouging, deformation, holes, cracks, and breakages. The cyclones are usually inspected at four-year intervals, and the cyclones are assessed by visual, hammer, dye penetrant, and ultrasonic testing.
We have observed varying severity of erosion in reactor and regenerator cyclones throughout the history of the unit. In the very early years, failures due to erosion were more frequent and cyclone repair/replacement was required within five years or less. Subsequent to the introduction of Resco AA-22 lining, replacement was required less frequently, while some repairs are usually done at every turnaround for both regenerator and reactor cyclones. The majority of repairs include repairs to Resco liner and hex mesh, removal and renewal of cracked welds, weld buildup on areas of eroded metal, and partial replacement of dustbowls and/or diplegs as necessary.
Other types of failures observed in the past include:
• Overstressing due to improperly designed cyclone supports: On one occasion, there were several cracks on the gas outlet tube weld attachment to the plenum and the hanger rods and stiffening bars showed signs of distortion and cracking. Reappraisal of the design by the fabricators indicated that there was insufficient hanger rod clearance.
• Thermal fatigue associated with the use of quench steam/water (both intentional/unintentional) to cyclone outlets and to the plenum resulted in several cracks in the gas outlet tube weld and severe distortion and failure of the plenum.
For cyclone and hanger systems, excessive thermal cycling and temperature excursions above design temperatures can also lead to reduced life and subsequent failure. In one instance, we had to replace cyclone supports prematurely owing to the expiration date of the creep life being before the next scheduled turnaround.
For the reactor, we have managed to operate with cyclones for 29 years without replacement and with only minor repairs at each turnaround before the entire reactor was replaced as part of an upgrade, in addition to the vessel reaching its end of life. The current reactor cyclones, which were installed at that upgrade, have been in service for approximately 17 years with partial (dustbowl) replacements done at the last turnaround and full cyclone replacement recommended for the next turnaround.
The regenerator cyclones have also had longer run-lengths in the more recent past, the last two total replacements coming at 14-year and 17-year intervals. The current regenerator cyclones have been installed for 12 years thus far.
Generally, we have found that some degree of weld buildup is anticipated at every turnaround (four-year cycle). Some breakages in cyclone supports and renewals in diplegs dust bowls are anticipated every eight years in the first instance after replacement and then every four years. While our design standard specifies that the minimum total design life must be 100,000 hours with accountability for short-term temperature excursions accounted for, we have managed to get longer run lengths based on inspection of our cyclones.
STEVE GIM (Technip Stone & Webster)
Observations: We have seen cyclones that have been torn apart during a campaign due to operation at very high vapor and catalyst velocity, and we have seen cyclones operating for only two years due to a poor cyclone design. Failures in support systems are usually correlated with the degradation of the cyclone. High internal reactor vapor and catalyst velocity can erode the cyclone supports over time. Feedstock change from sweet to higher sulfur content can affect older carbon steel straps and hangers.
Time to Failure
Depending on the operation and the cyclone design, the “Time to Failure” could be short – one campaign or a portion of it) or extend over a number of campaigns. The biggest effect on cyclone life appears to be the amount of time it operates within its design parameters. Multiple shutdowns or temperature excursions can shorten the life of both the cyclones and their cyclone supports. High and very high velocities wear on the refractory protection, and eventually on the cyclone metal itself, shortens lifespan. Cyclones that run within their design parameters can be expected to operate for 16 to 20 years. Cyclones that run often above their design parameters or have frequent shutdown of temperature excursions probably last for two campaigns and maybe a third with risk of failure during the campaign.
Support System is a Key
The support system is a key component of the cyclone system and needs to be considered when purchasing a cyclone system. A properly designed support system will adequately accommodate the differential expansion between the hot internals and the relatively cool vessel, which is further exasperated in larger diameter vessels. Furthermore, maximizing the load supported directly by the vessel minimizes the loads imposed into the plenum, which further extends the life of the cyclone system.
A poorly designed support system imposes additional stresses into the cyclones and/or plenum, which will not only greatly reduce the live of the cyclone system but also result in significantly greater maintenance costs and turnaround time.
A few tips for proper support systems:
1. With no bracing, the cyclones will dance and be fatigued.
2. Lateral bracings that are not free to expand from the shell.
3. Add pivot points with slots if bracings are mounted to shell.
4. Set in midpoint at the startup to move freely
CHRIS STEVES (Norton Engineering)
Failures due to erosion are very common in FCC cyclone systems. Cyclone age, flue gas velocities, and repair techniques all play into the erosion failure time. A new, properly designed regenerator cyclone will last a five year run without failure. As long as good inspections are done, repairs are identified, and the correct repairs are made, the cyclones can last 20 to 30 years without failure. Pay close attention to the catalyst losses during the run, especially if the cyclone velocities are not within the design guidelines of the OEM (original equipment manufacturer).
Case Study: A 50,000 bpd FCC unit has air rate was increased by adding a smaller air blower. The flue gas rate increased 14%, with a corresponding increase in regenerator cyclone velocity. Within two and half years, the cyclone barrels and transition ducts started to wear away. Catalyst loses increased from 1. to 20 7 tons per day (tpd) within a month. One month later, the losses were over 40 tpd. When the regenerator was first opened, a trickle valve was seen on the regenerator floor, and this was quickly assumed to be the problem. Only after repeated discussions was the decision made to build the scaffolding needed to properly inspect the cyclone barrels and transition ducts. Many holes, ranging in size from pinholes to holes large enough to fit an arm through, were found. These cyclones were 20 years old and had never had this extensive amount of damage in prior runs. Subsequent review of inspection records revealed that the repairs completed during the prior outage may have been less than adequate. A combination of age, prior substandard repairs, and increased cyclone velocities all played a role in the eventual failure mechanism.
Take into account the cyclone age, prior repairs, and current and anticipated cyclone velocity when evaluating the cyclone damage. All three aspects are part of the failure time. Start the paperwork for new cyclones when the refractory hex mesh telltale signs start showing, and pay closer attention to the catalyst losses when the cyclone velocities go above the OEM’s recommended max.