Question 94: What is your experience using specially designed automated isolation valves on the reactor overhead line for your de-blinding operation during the start-up of the FCCU? Will they dependably provide positive isolation after being in operation? How did you justify the installation cost (e.g., safety and economics)?
SCHOEPE (Phillips 66)
We have quite a few units that use valves in the vapor line and others with just simple blocked valves in that service. Two more units now have a newer style: a double disc valve which relies, in part, on a steam purge to provide positive isolation. Because that valve was very successful, two more valves are going to be installed soon.
In terms of reliability, the blocked valves need to be replaced every single turnaround. They are coked-up after start-up and cannot be used again during the run. We have had good reliability with the newer type of valve. Some of those valves are now being refurbished after two runs.
Justifying the benefit of such a valve: You can save anywhere from 12- and 24-hours during start-up. After this slide, I have two more slides that drive home this point. Another advantage is that because the FCC gas plant is often used as a garbage dump for the rest of the refinery, if you do have an outage, you can actually isolate your catalyst section from the main fractionator and keep the recovery section online while doing repairs in your catalyst section. If your site had issues with safety while removing the vapor line blind, such a valve is easily justified. If safety is not deemed justifiable for undertaking this project, then it may be challenging to find another justification. The newer style, the double block and purge valve, is not considered a man-safe device because it relies on a steam purge for positive isolation. All of these newer valves are now being sold with a blank upstream of the valve, which you can then install to make the isolation man safe.
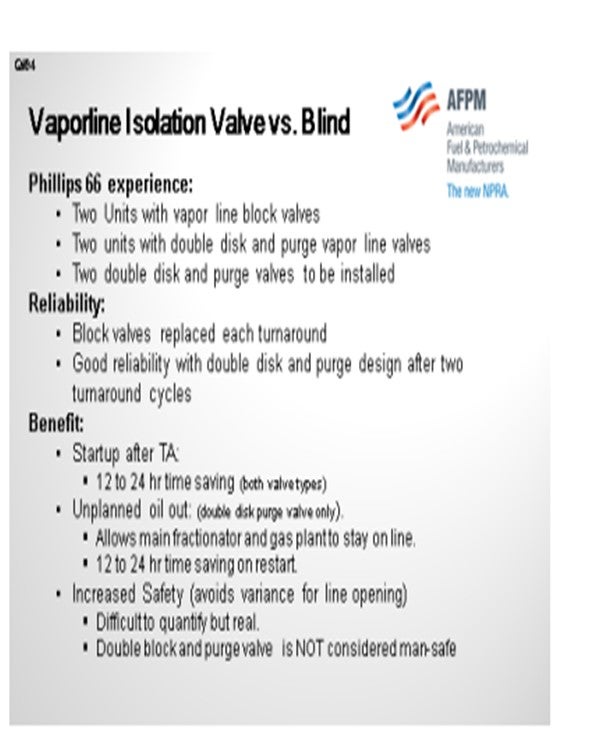
Going back to the justification: A good way to explain the benefit of this valve is to show an FCCU heat-up curve after turnaround. The red line represents regenerator temperature. The blue line is your reactor temperature, and the magenta line is your CO boiler temperature, if you have one. You start your air blower and then go into your first hold for refractory dryout. At some point, you will start your inline air heater; then, you will increase temperature to your next hold point. The heat-up reactor is lagging the regenerator by about 100ºF. First, the reactor and regenerator are being dried out with air. After the second hold period, the refractory dryout is finished.
In preparation to pull your vapor line blind, the reactor is air-freed, which takes about an hour or so. During that time, other equipment needs to be shut down. The CO boiler is usually shut down, in addition to the inline burner and main air blower. After that, the vapor line blind is pulled. With the vapor line blind taken out, the CO boiler, main air blower, and inline burner are restarted.
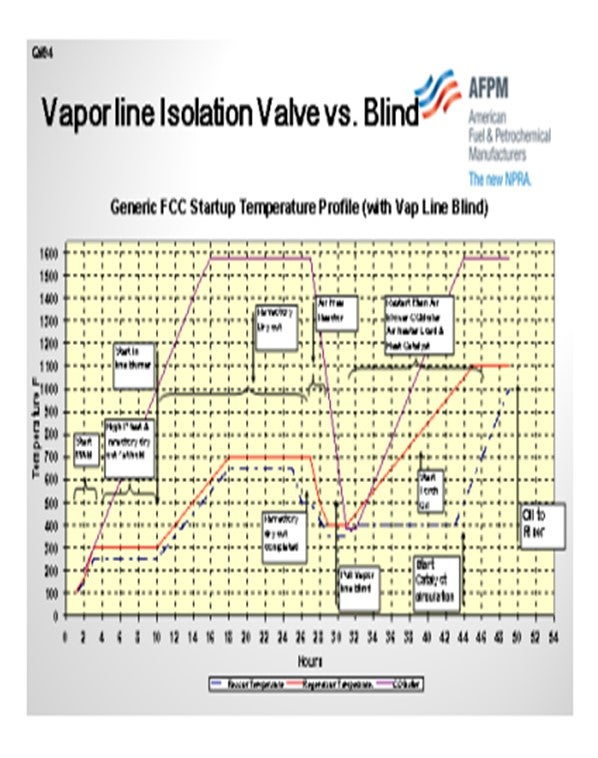
The next slide shows the time savings if you do have a vapor line valve. After the refractory dryout, you do not have to shut down anything. You keep your air blower and CO boiler running, and then proceed directly to catalyst loading.
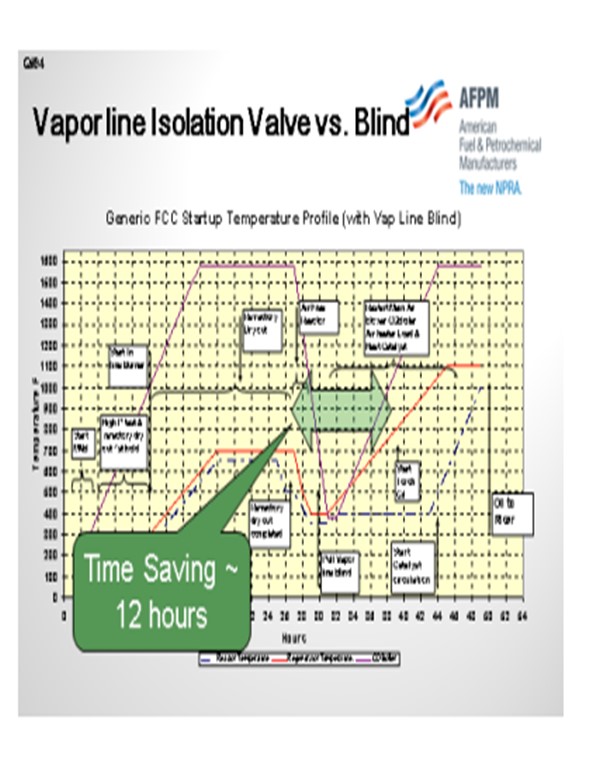
In summary, it is very difficult to justify such a valve if you are not allowed to consider safety and only allowed to consider scheduled plant turnaround intervals. If, however, you consider one unplanned event during each run, it will be very easy to justify that type of device.
LALL (UOP, A Honeywell Company)
Christian covered this very well. UOP also does not consider the isolation valve to be man-safe for vessel entry. Therefore, an isolation blind will need to be installed whether the valve is installed or not.
WILLIAMS (KBR)
I have nothing more to add.
MICHAEL LEMESHEV (Zimmerman & Jansen)
With regard to these valves, here is some statistical data. In North America, there are about 99 cat crackers. Not including refineries, FCCs and Flexicrackers total 140 units, plus 11 in Mexico. There are probably 22 to 23 cats with these types of valves ranging in size from 24 inches to 66 inches. In addition, speaking from the safety side, which UOP has addressed very well, the valves are installed with manual actuation. They are not using any kind of automated actuation, and that addresses some of the safety aspects of the installation. In this way, the automated line blank can be compared to a regular line blank, in terms of an accidentally swinging blank. Now this obviously would not happen. Additionally, the valves can be fitted with a safety mechanism that would prevent them from being stroked or, even in the event of stem failure, the gate slamming shut on its own due to gravity. These are some of the considerations when evaluating the configuration of the valve. These points help address the safety aspect and also give some basic numbers about how many refineries have these valves installed.
LALL (UOP, A Honeywell Company)
We do have a number of customers that use these and contemplating their use. The benefit depends on the type of start-up procedure that the refiner follows. If a "blind out" procedure is normally followed where the entire unit is cold when the blind is removed, the addition of the valve can save a few days of downtime, especially for a new unit. If a "blind in" procedure is normally adopted where the equipment is hot and under steam purge, there are the added benefits of personnel protection and safety. UOP views the reaction vapor line isolation valve as a safety-oriented valve more so than a production saving valve. However, one needs to bear in mind that the valves are expensive. Also, this is a judgment call by the refiner who will assess its merits on safety grounds and/or production time gains.
In our experience, the isolation valve does operate without any problems following turnarounds (i.e., when the valves are cleaned and overhauled); however, whether the valve works dependably after exposure to hydrocarbon is another matter. Feedback from customers has generally cited problems with coke lodging in the cavities of the housing, securing a tight closure during the previous shutdown, and purging the valve. UOP believes the valve vendors are working to enhance the reliability/availability of the valves.
UOP does not, however, consider the isolation valve to be man-safe for vessel entry. The isolation valve typically requires an internal purge to keep the inner housing cavity free of hydrocarbon and this cannot be considered to be safe for vessel entry. Therefore, an isolation blind will need to be installed no matter if they install the valve or not. This may limit the usefulness of the valve.
SCHOEPE (Phillips 66)
Phillips 66 FCC units use two types of valves in the vapor line from the reactor to the main fractionator, a simple block valve and, in recent times, a double disc steam purged isolation valve. Block valves can only be used once during start-up. During the run, these valves coke up and need to be cleaned and/or replaced during each shutdown. Maintaining such a valve is justified by shortening the start-up time between refractory dryout and catalyst loading. An overhead vapor blind allows the refiner to proceed directly from air-freeing the reactor to catalyst loading, units without an overhead vapor valve have to prepare for pulling the overhead blind by shutting down the main air blower, the in-line air heater and the CO boiler (if applicable). After the blind has been pulled, the unit has cooled down significantly and all previously named equipment has to be restarted in order to continue with the start-up process. Depending on the site and the reliability of the equipment, an overhead valve saves one to two shifts during unit start-up.
A newer style double disc and purge valve has all the advantages of a simple block valve, but it can also be used during a run and at the end of each run. Overall reliability for these valves has been good within the Phillips 66 organization. Some valves are now being refurbished after two turnaround cycles.
The economic justification for such a valve is difficult if only planed turnaround intervals are considered. If one or two unplanned outages are used in the economic evaluation, the Lost Profit Opportunity (LPO) is usually high enough to justify such an investment. Line opening during the removal and installation of a vapor line blind can be hazardous and has to be managed very carefully. The increased safety during FCC start-up often contributes the justification of a vapor line valve. Because the double disc and purge design relies in part on a steam purge to provide positive isolation, most sites do not consider this isolation device “man safe”. All newer double disc and purge valves are, therefore, sold with an additional blind/spacer, which is located upstream of the valve.