Question 91: What are your top three causes of unit slowdowns, and what is the loss in onstream factor for each? Please provide the same information for your top three causes of unit shutdowns.
RUSSEFF (CVR Energy)
I get the fun one! For us, it has been the main column bottoms exchanger cleaning. We have a residuum oil supercritical extraction unit, or ROSE unit, upstream. We have been achieving some new recoveries there and are ending up with the high asphaltenes in our feed and in our slurry; so, slowdowns are the result of the combination of that polynuclear aromatic formation. Some people get excited over 15% asphaltenes in their slurry. When the ROSE is not online, we go from about 3% up to as high as 40%, which is very discouraging. A typical turndown for replacing a bundle in that service is about 75% max capacity. We have a spare steam generator online, so we could switch back and forth between the two units.
Feed availability: In our Wynnewood Refinery, we have competition for feed, depending upon the market conditions. In Coffeyville, we do not necessarily have a competitor for that feed within the refinery itself. But due to the kind of positioning and some of the prices we have seen, in terms of premium gasoline and diesel, we have changed some operations. So, we are just trying to make up for that price fluctuation in other areas for the gasoline crack. We have also been able to locate opportunity feed from some external sources. We have good synergy between the two refineries, and they are relatively close. So, when the northern one was going into a turnaround, we managed to turn through a lot of their gas and oil this year, too. So, the answer on turnaround is: It varies, depending upon the market.
Our Limitations on Our Wet Gas Machine: We have a dry screw machine in wet gas service. This is a first for me, and it has been a painful process. We have had a couple of outages because of problems with the dry screw machine in wet gas service, but we have a current rebuilding that has some losses in efficiency. We do have a backup machine: a reciprocating compressor. However, we have a considerable turndown; basically, down to 50%. Additionally, for upstream unit recoveries, such as the ROSE I mentioned earlier, we are turning up the knob on recoveries and the asphaltenes. Conradson carbon residue (CCR) leads to metals taking capacity in the wet gas machine with a higher hydrogen and methane ratio. We have been aggressively flushing the additional metals in the catalyst. I have also switched over to a nickel trap catalyst, which is working well.
Also, in our Oklahoma and Kansas facilities, with the lack of condensing and cooling capacities they have during the summertime, the loss in capacity is really directly dependent on the ambient conditions outside. So that turndown depending upon how hot it is outside at each moment.
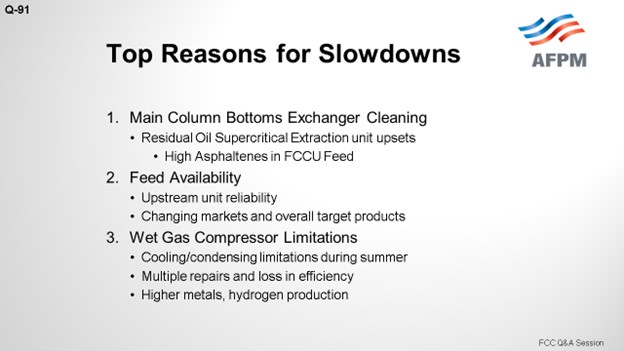
As far as the top three shutdowns, I have to say that the rotating equipment reliability, especially with the dry screw machine, has been difficult. We have a spare machine. It is a reciprocating wet gas machine, but it just does not have the capacity. We do not actually have a full shutdown. You would think that some of the parts on that dry screw machine were made of fresh panda blood because it is very difficult to get parts for it.
We have also had some other problems as we have gone through a rigorous pump rebuild program where we sent pumps out to have complete rebuilds so we could start a new benchmark, in terms of reliability. That does take more time. The pump availability for the spares has not been there during this revamp of our reliability program, so we have had some issues there.
Finally, the other main reason for shutdowns is probably the catalyst. It is a very sensitive subject, but it is more of a catalyst issue. We had the opportunity to run some what I would call opportunity e-cat. Right now, I want to say that we are really happy with our long-time vendor, but running the opportunity e-cat from somewhere else was not such a good opportunity. The shutdown gave us a chance to prove that our current vendors are probably the best out there. It also gave us a chance to communicate wonderful experiences about paying attention to your e-cat, no matter where you get it from, to the additives, activity, metals, particulate size, yield projections, and required addition rates. So, those are our top three reasons for shutdowns.
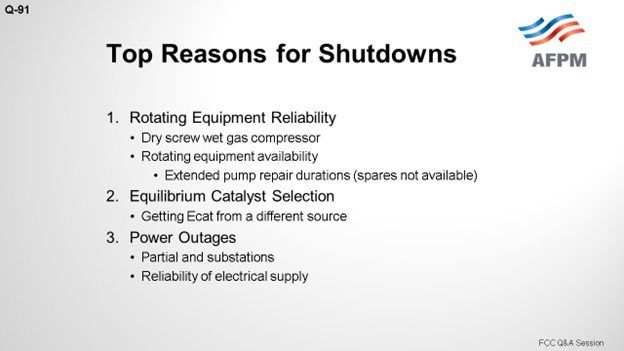
SINGH (Indian Oil Corporation Limited)
The cat crackers are one of the major secondary units for all of our refineries. Irrespective of demand and condition, our units are always required to operate at high capacities. All of our refineries have been participating in benchmarking studies done by Solomon. I tried to compile the Solomon studies results for 2014, which are shown on the slide. They are based on more than 300 cat crackers worldwide. As can be seen, the last one is for Indian Oil Refineries. We have eight cat crackers. You can see the slowdown percentage for our units is much lower than the global numbers. Our refineries are focused on consistent high-capacity performance of the FCC units.
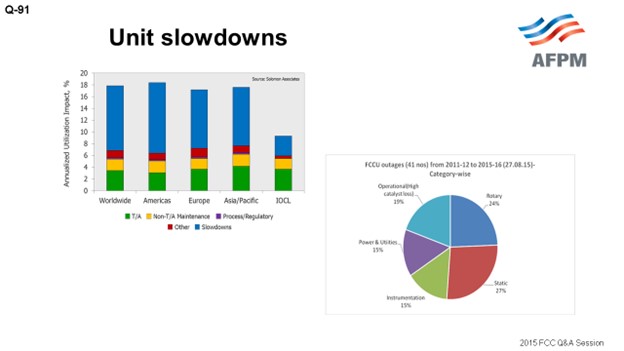
Referring to the FCC outage pie chart for IOCL refineries, it can be noticed that there is no single reason for unplanned outages on our units. Our youngest unit is 13 years old. Typically, most of the units are between 17 and 32 years old. All these units have been revamped to capacities more than 25% to about 50% of the original design capacities.
The pie chart presents the distribution of the different reasons for our plant interruptions. I have tried to compile data for the last five years. There are a total of 41 incidents, and I cannot figure out a single reason that has been predominant. We operate our units based on our captive power plants. So, this power and utilities interruption of 15% is based on our own power plant. The catalyst loss issues are predominantly because of reactor/regenerator internals and the aging of these internals, not because of any other issue. The rotary equipment issues are predominantly WGC failures. None of the refineries have a spare WGC. And similarly, the static and instrumentation issues have shown 27% and 15% of total outages, respectively.
It needs to be noted that while presenting the interruption data for our FCC units, all interruptions – irrespective of the duration – have been included in the evaluation. Any incident that leads to a feed out has been accounted for in these statistics.
LARSEN [Marathon Petroleum Corporation (MPC)]
I tracked internal problems associated with our FCCs and the reliability impact of these for all of our Marathon FCCs. I highlighted a couple of our top three. Because the question mentioned onstream factor, our three biggest ones for the first two entries are from 2014; the last one was 2015. The flue gas steam generator leaking caused 0.7% loss in our total Marathon FCC reliability. That is basically due, as was Sanjiv’s experience, to the old cyclones on this site. We chose to operate it at higher velocities than our normal operating guidelines, which resulted in higher catalyst losses and impacts on this flue gas steam generator.
The second one is the waste heat boiler situation I mentioned before: previous old CO boilers converted to just normal waste heat boilers now. An improper quench design where the boiler feed water is injected too close to a geometry change in the flue gas line resulted in significant erosion and corrosion problems. That resulted in a low of 3% total Marathon FCC mechanical liability in 2014, and the correction there is for installing our new waste heat boilers on this unit in the future.
The last one occurred in 2015 and was an unforced error from leaving blast steam open on the guides on the spent slide valves, resulting in the loss of control on the reactor level. We have shown the damage that that can do in a fairly short period of time.
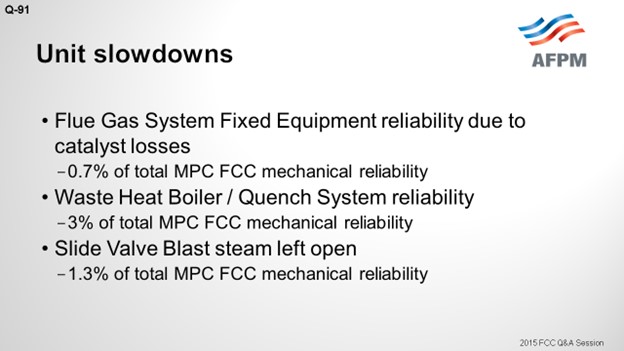
In terms of slowdowns, I just want to add one interesting example. We have one unit that is challenged in the fractionator, in terms of coking. It required the reduction in throughput to manage this coking, but you can see that we tracked the densities. In the packing, you can see that the green trend is the tracking of the density in the top layer. The other two are in the bottom layer of the pack. You can see the densities creep up over time.
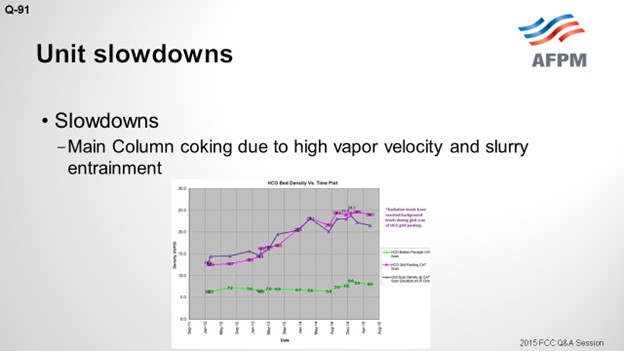
So, this is a strategy we use to manage getting to the next turnaround where we can properly swap some of the fractionation beds. This unit has high inlet velocities to the fractionator and high slurry entrainment, combined with the fractionation section being located right above the slurry section, with the resulting low liquid rates contributing to the coking problem. So ultimately, we are swapping the beds around in the fractionator to eliminate that concern.
JAMES (JIM) PROROK (Husky Energy, Inc.)
I was not going to say anything on the last question; but on this one, you again brought up the waste heat boilers that sometimes reduce liability. On our unit, the mud drum hangs on the bottom of the tubes inside the flue gas duct, so you cannot get to it very easily. Regarding the gaskets, we had the manway gaskets on the mud drum. You could tell it was happening by the water balance on the boiler. So yes, not that it is a bad design, it is just that when you do maintenance of your unit and have startup and shutdown, the thermal cycling of the system may cause the gaskets to leak. It may have stretched bolts and leaked where the gaskets were crushed and then cooled off, ending in failure.
SANJIV SINGH [Indian Oil Corp Ltd. (IOCL)]
FCC/RFCC units are the one of the major secondary units in almost all of IOCL’s refineries. Irrespective of demand positions, these units are always required to operate at high capacities. All of our refineries had been participating in the benchmarking surveys conducted by Solomon Associates, and the results comparing IOCL FCC units with rest of the world (2014 study) are indicated below. The chart shows the factors impacting FCC unit capacity utilization. This chart considers the data reported for approximately 300 FCC units in recent Solomon Fuels Refinery Performance Analyses (Fuels Studies).
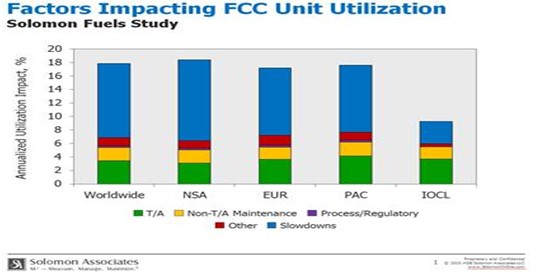
IOCL refineries are focused on achieving consistently high-capacity performance of its FCC units. Regarding unplanned outages, there is no single reason for the same. The age profile of operating FCC units varies from over 30 years to little over 10 years, and failures mainly with reactor/regenerator had been due to aging equipment. Unplanned outages of FCC units during the past five years are indicated below.
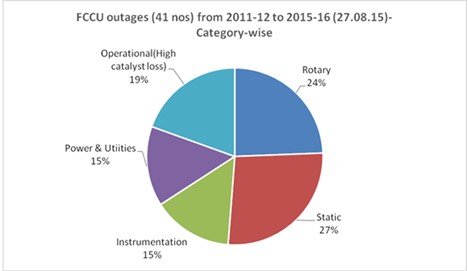
NIKOLAS LARSEN [Marathon Petroleum Company (MPC)]
Rationalization of U.S. refining assets has placed significant focus on doing more with less while meeting tougher environmental and regulatory requirements. This has created incentives for improving FCC reliability: The unit needs to run to make a profit. MPC’s take on this is captured in our FCC business plan, which is based upon the following pillars:
- Build it right. Invest in the right hardware to modernize and capture the latest technological and reliability improvements.
- Optimize and debottleneck. Continuously focus on operating up against multiple constraints and completing small tests/projects to creep limits.
- Run it to last. Stay inside the box with regard to procedures, limits, and KPIs (key performance indicators).
Using this model has (historically) resulted in greater than 98% mechanical availability for MPC FCC units. However, there is always room for improvement. In general, MPC seeks to lower cyclone velocities in order to minimize erosion without sacrificing efficiency. This, along with longer L/D (length over diameter), has improved dustbowl erosion. However, in situations where dipleg length is limited, MPC will be installing new cyclones with vortex stabilizers to avoid extending the regenerator vessel to accommodate larger cyclones. Cyclone reliability was responsible for reducing overall FCC mechanical reliability by about 0.7% in 2014.
Likewise, cyclone L/D ratio can affect waste heat boiler reliability. To minimize flue gas and tube leaks going forward, new waste heat boilers will be installed, and new cyclone technology (vortex stabilizers) will be evaluated as driven by unit configuration/design. Waste heat boiler reliability was responsible for reducing overall FCC mechanical reliability by about 3% in 2014. Third, proper blast steam operation minimizes slide valve guide erosion. Slide valve erosion reliability was responsible for reducing overall FCC mechanical reliability by about 1.3% 2015.
Lastly, main column coking in the fractionator section can be caused by high vapor velocity and slurry entrainment combined with low liquid rates in the fractionation section above the slurry pumparound bed. Reducing fractionator inlet velocity and redesigning fractionator bed placement to eliminate a fractionation bed between slurry and HCO pumparound streams is expected to reduce coke formation.
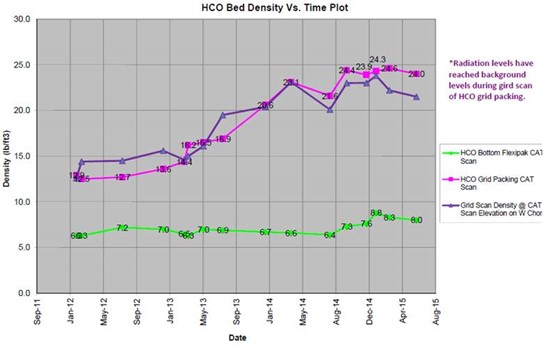
GARY HAWKINS (Emerson Process Management)
We have seen increased interest in monitoring any rotating equipment, such as process pumps and air-cooled exchangers, which can allow early detection of potential problems that could cause a shutdown or upset. The major equipment, like the air blower and wet gas compressor, is typically supplied with shutdown systems, but the air blower and wet gas compressor do not necessarily have all the measurements to calculate performance, such as efficiency and alert when efficiency deteriorates, which can be an early indication of a potential shutdown.