Question 90: We are planning to purchase a new flue gas steam generator. What is your preferred configuration? What are the critical operating parameters you employ to ensure reliable operation? What is your sparing philosophy?
SINGH (Indian Oil Corporation Limited)
The configuration of the flue gas steam generator will be predominantly governed by FCC design. For a partial-combustion unit, it will be a CO boiler or a CO incinerator cum FGC (flue gas cooler) combination. For complete combustion, it will be a FGC or waste heat boiler alone. By CO boiler, typically we mean a boiler where the steam generating tubes are exposed to direct flame. On the other hand, in the case of a CO incinerator, CO is burned first to CO2 (carbon dioxide). These flue gases are then used to generate steam in the downstream FGC.
At Indian Oil, we have experience with all such boilers and flue gas coolers. Our experience is that the combination of a CO incinerator and FGC is much more reliable than a CO boiler by itself. All of our units have a bypass provision for an FGC. We do not have spare flue gas cooler in any of our units. Almost all of our units have a provision to put in blinds and spacers at the inlet and outlet of flue gas coolers to enable us to do maintenance without shutting down the FCC. The steam generation levels vary from 12 to 50 bars from unit to unit. Our experience is that the flue gas steam generators are more reliable at lower pressures of steam generation.
Preferred design of flue gas cooler is water-wall type in which the tubes are welded together to form the shell for the boiler with external insulation. Such designs have been found to be very robust and dependable. The common problems we have encountered include refractory and inlet bellow failures, boiler tube erosion, collection of catalyst at FGC bottom, and cold end corrosion due to condensed acid gas. Dry run of the tubes has been the leading cause of the tubes’ failure. Accumulated bed catalyst is acidic and highly corrosive. To overcome this, in most of our units we have modified the bottoms of these boilers to dump out the catalyst conveniently during the turnarounds, as well as during operation itself.
Going by the problems experienced in different CO boilers and FGC, the following can be considered for a new boiler design: The boiler design should have a provision for positive isolation to enable boiler maintenance. The boiler should be maintenance-friendly; that is, various pressure parts, economizers, and superheater coil bank tubes should be accessible. Soot blowers should be provided in high catalyst deposition zones and should be functional. We prefer to go for fabric bellows over the metallic bellows because of the frequent failure of metallic bellows in the flue gas line. The catalyst dump hoppers may be provided at the bottom of the economizer and superheater sections for regular and quick removal of the catalyst.
LARSEN [Marathon Petroleum Corporation (MPC)]
I think Sanjiv did a great job with the answer. I know that at Marathon, we only have one partial-burn unit with the CO boiler. Aside from that, we have several water-tube-style flue gas steam generators with shell-and-tube gauge exchanger design. In general, we have had good luck with them. We do not have provisions to take them off on the run, and they have not really caused us any reliability problems. We do have one unit with fire-tube-style flue gas steam generators. We are also satisfied with its reliability. So, there are definitely a lot of options: water- versus fire-tube and high pressure versus low pressure.
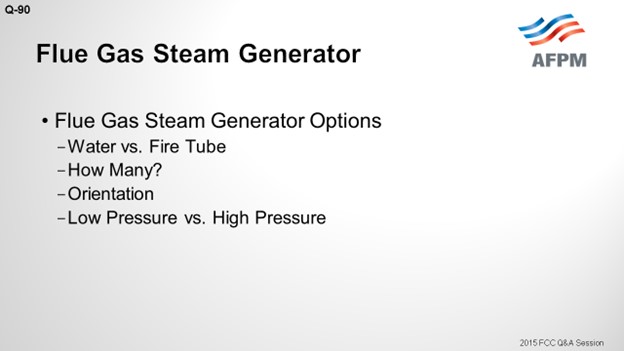
Maybe some of the licensors can comment. But if you are to trying to build a large new grassroots unit, perhaps the lowest-cost reliable option would be a low-pressure box-style boiler because you can possibly get away with just doing one of them. Making sure that the key point is to have reliable soot blowers. At Marathon, we did have a cause to evaluate replacing a couple of older designed waste-heat boilers with low pressure box-style. The unit did not have working soot blowers or anything. They were a significant cause of reliability problems for us, and replacing two old boilers with one newly designed unit was thought to be the best way to go. However, the fact is that when replacing equipment in a unit that was already designed with two boilers, the piping configuration, ducting, and structural loads made it more economical to go back with two new pieces of equipment instead of a single large boiler. At times, your hand is forced by what you currently have existing in your unit, in terms of replacement strategy.
RAMA RAO MARRI (CB&I Lummus Technology)
Nik and Sanjiv had summarized the answer nicely. I think, configuration-wise, that the horizontal type is better than the vertical, as Sanjiv recommended. It is a packaged item. As a licensor, we have some specified conditions and criteria that we establish. But mostly, the horizontal type is what we are seeing being used because it is accessible and easy to maintain and repair. So, we recommend the horizontal type.
SANJIV SINGH [Indian Oil Corp Ltd. (IOCL)]
For an FGC (flue gas cooler), the configuration will be predominantly governed by FCC design. For a partial-combustion unit, it will be CO boiler or CO incinerator and FGC combination; and for a complete-combustion unit, it would be FGC/WHB (waste heat boiler) alone. At IOCL, we have experience with all such boiler/FGC combinations. Our experience with a CO incinerator/FGC combination had been better in comparison to a CO boiler. Though all of our units have bypass provisions for FGC, none of the units has a spare FGC. Almost all the units have provisions to put blinds at FGC inlet and outlet to carryout maintenance while the FCC remains onstream. The steam generation level in FGC varies from unit to unit depending upon the overall steam balance of the refinery. We have steam generation levels ranging from medium pressure (12 bar) to high pressure (50 bar).
The preferred design for an FGC is a ‘water wall’ in which tubes are welded together to form the shell for the boiler with external insulation. Such designs have been very robust and dependable. Common problems encountered with the FGC include refractory failure, inlet below failure, boiler tubes’ erosion due to catalyst content of flue gas, collection of catalyst at FGC bottom, and cold end corrosion due to condensed acid gas. Dry run of the tubes leading to tubes failure had been one of the most common causes of failure. Accumulated wet catalyst is acidic and highly corrosive. To overcome this, we have made provisions to take out catalyst from the FGC bottoms even while the plant remains onstream.
Based on problems experienced in different COB/FGC, the following shall be considered in the new boiler:
-
The boiler design should have provisions for positive isolation to enable boiler maintenance even when the FCC unit is in operation. The main CO-flue gas duct should have isolation and blinding provisions with a similar arrangement at the stack end to ensure positive isolation of the equipment.
-
The boiler should be maintenance friendly; i.e., various pressure parts like economizers, superheater/bank tubes, etc. should be accessible. The catalyst and soot deposit can be easily cleaned during maintenance turnaround.
-
Soot blowers should be provided in high catalyst deposition zones and be functional. Catalyst carryover shall be monitored upstream of the boiler so that damage to the tubes and deposition can be minimized.
-
Metallic bellows have a history of cracking/failure, so fabric bellows shall be provided as far as possible over the metallic bellows.
-
Catalyst hoppers may be provided in the bottom of the economizer/superheater sections for regular and quick removal of catalyst.
NIKOLAS LARSEN [Marathon Petroleum Company (MPC)]
Flue gas steam generators can be a significant reliability concern for FCC units. However, if properly designed, operated, and maintained, they can also be an afterthought. In typical new grassroots units, a common design is that of a single, low pressure (downstream of flue gas slide valve) ‘box-type’ water tube flue gas steam generator (FGSG)/waste heat boiler. Unfortunately, we are infrequently handed a blank sheet of paper, and reliability improvements associated with current unit design, configuration, and plot space are desired. Still, improved reliability and increased heat transfer capability can be achieved by installing new FGSG equipment. There are a number of options to consider such as type (water tube versus fire tube), number (spared versus unspared), orientation (horizontal, vertical, box, etc.), and location of flue gas steam generator (high pressure versus low pressure).
Water tube FGSGs are generally more reliable than fire tube FGSGs. A water tube FGSG would be a preferred option if catalyst losses from the regenerator are low and flue gas velocities are also low (about 90 fps) as this type of exchanger is susceptible to erosion in highly loaded systems. MPC has several of these types of FGSG designs. There are a number of design features that can improve reliability in these designs, but they result in the need for additional exchanger length. These features include upgraded metallurgy of the fins and vapor belts on the inlet and outlet of the FGSG. Fin tip temperatures can exceed 1000°F so metallurgies like 1¼ chrome or 409 SS (stainless steel) should be investigated. We have found that using 1¼ chrome versus carbon steel fins has no significant impact on the overall heat transfer rate. A heat transfer coefficient of about 6 BTU/h.ft2.°F is adequate for a new FGSG of this design; a fouling factor of 0.03 ft2.h.°F/BTU for design is consistent with the operating data for a fouled FGSG of this type. It is also important to be cognizant of acid dew point concerns with all FGSG designs.
Another option to consider is a fire tube type of exchanger. In this exchanger, the flue gas is cooled on the tube side and the water/steam is on the shell side. There are certain critical design features that are essential for reliable operation in this type of FGSG, such as the upper tube sheet design and the water/steam outlet design. The critical hot top tube sheet is protected with six to 10 inches of insulating refractory. Inlet tube ferrules (typically ceramic or stainless steel) extend through the refractory and into the tubes. For a vertical design, the flue gas enters the top of the exchanger. This can be a positive feature of this type of exchanger depending on inlet piping configuration as the potential for erosion is lessened if there are no changes in direction of the flue gas.
A downside to this design is that the tube bundle is non-removable and that all inspection and maintenance must be done in place. MPC does not have any vertical fire tube FGSG designs. However, we do have a unit operating with a horizontal fire tube-type FGSGs and have had good operating experience. Horizontal fire tube exchangers have good cooling of the hot tube sheet. The tube sheet is self-venting, which prevents the accumulation of noncondensables that can collect under the tube sheet in a vertically oriented fire tube exchanger. Piping arrangement and scouring may be more challenging for horizontal fire tubes (compared to vertical fire tubes). Heat transfer coefficients are comparatively higher than water tube designs (11+ BTU/h.ft2.°F), and hot side fouling factors are slightly lower (0.02 ft2.h.°F/BTU).
Depending on the size of the unit and amount of heat recovery desired, a single piece of equipment in the above designs can be large – often too large, which can lead to consideration of a low pressure ‘box type’ FGSG/waste heat boiler; these are unlike the previous designs that are closer to a shell-and-tube heat exchanger. The type of FGSG being replaced can often be a deciding factor as well due to the surrounding piping/duct, foundation, and plot space. MPC recently encountered this while deciding on a replacement strategy for a large unit with two old low-pressure box-style waste heat boilers. In the end, installing two newly designed low-pressure box-style waste heat boilers were the most cost-effective option. In large part, this was due to unit piping configuration, plot space, and ability to install equipment while the unit was in operation. Critical factors for successful future operation on this unit included soot blower design/reliability and ability to operate without waste heat boilers (quench system).
PATRICK BERNHAGEN (Amec Foster Wheeler)
Larger FCC units have basically two types of steam generation methods: forced circulation and natural circulation. In both of these designs, the regenerator flue gas is on the outside of the heat transfer tubes. Amec Foster Wheeler offers both designs.
Our natural circulation design has vertical tube bundles for the various services with the steam drum above them. The flue gas flows across these bundles horizontally similar to an HRSG (heat recovery steam generator). Hoppers are below the bundles to collect any catalyst dust that drops out of the flue gas stream. Various levels of soot blowers are placed along the flue gas path and vertically along the tube bundles to keep the heat transfer surface free of fines. The circulation ratio is carefully selected to accommodate the required steam pressure level and tube bundle design. Economizer, steam generation, and steam superheat are typically the services in the unit.
Our forced circulation design has horizontal tubes very similar to fired-heater convection sections stacked on top of each other for the various services. Circulation of the BFW (boiler feed water) through the steam generator coils is provided by circulation pumps (typically spared). This design has a higher flue gas velocity through the heat transfer coils and entrains the catalyst fines such that hoppers are not necessary. Again, various levels of soot blowers aid in moving the dust through the unit while keeping the tubes free of deposits. This design has successfully used low density finning with proper soot blower arrangements.
General conditions of the flue gas steam generator to consider include the following:
Operating and design pressure of the casing (enclosure) needs to consider the back pressure of the system. This is typically in the range of 25” WC (water column); but if wet scrubbers are in the system, this number can increase substantially. Units up to 5 psig (pounds per square inch gauge) design pressure have been built, but there is a premium for higher pressures.
Catalyst loading and deposition must be addressed. Our natural circulation systems are designed with hoppers to collect any catalyst fines and must be periodically cleaned out. Our forced circulation designs with higher flue gas velocities do not need hoppers. Retractable soot blowers (no rotary) should be selected for their robustness. Another key component is the wall boxes/valves on the casing for soot blower entry and sealing when soot blower retracted. Poor designs allow leakage and can affect operations.
Plot Space is critical on a retrofit installation in most cases. The natural circulation style can require a larger plot space as it is horizontally arranged coils with design constraints on lengths and widths. The forced circulation design is vertically oriented, thereby reducing the plot space requirements. The circulation pumps do not necessarily need to be adjacent to the unit thereby allowing another degree of plot space flexibility.
Steam quality/purity/superheat is another topic requiring your specification. Our steam drum design can address the superheated steam at any pressure level. Our drums have primary and secondary separation devices or more depending on your requirements.
Turndown operational requirements need to be specified with any steam demand requirements. Forced circulation systems respond to load swings more rapidly as there is always flow through the tubes.
Vibration analysis/cold flow modeling/CFD modeling are topics to discuss with the various designs. Vertical tube designs will analysis the entrance flow distribution and tube support along the coil length. Horizontal tube designs with large (~4” NPS) tubes typically only require flow distribution analysis. Support is usually determined by API 560 requirements.
Refractory selection must be made considering the catalyst fines abrasiveness and the sootblowing frequency. Depending on the style of flue gas steam generator, there are a small variety of hard refractories that are used.
CHRIS STEVES (Norton Engineering)
A number of reliable technologies are currently being employed in flue gas steam generator service. They include: two drum vertical tube natural circulation boilers (water/steam on tube side), horizontal and vertical tube forced circulation boilers (water/steam tube side), and fire tube steam generators (flue gas on tube side). There is no one right answer for selection of a specific technology or equipment design for all applications as they all are demonstrated technologies available from reputable vendors. They all have pros and cons which must be weighed to determine the “best” (most economical) fit for a specific application. More often than not, constructability, space availability, and the cost of ancillary components and systems determine the optimum technology for a specific application.
Natural circulation WHBs are the simplest units, are easy to operate and have the lowest overall operating cost. They use the same manufacturing techniques and standards as fired-water tube boilers, so they tend to be highly reliable and are not normally spared. The only reason to spare this type of WHB would be to meet mandatory state/insurance inspection requirements if they require boiler component inspection on a more frequent cycle than planned FCC turnarounds.
Forced circulation boilers, typically horizontal tube units, in up-flow or down-flow flue gas configurations, are also highly reliable and rarely spared. This type of system uses external pumps to circulate water through the tubes of the steam generation bank instead of relying on natural circulation. The steam drum is normally separate from the tube bank and has many fewer connections than a natural circulation unit, making it less complex but also likely larger in diameter.
Circulation pumps are typically spared with one driven by a steam turbine and the other by an electric motor. Autostart is provided to prevent loss of flow to the WHB. The “rectangular duct” enclosure of forced circulation WHBs makes them easier to clean than natural circulation units and therefore less prone to external corrosion during FCC outages. Superheater and economizer coils can be included in rectangular duct systems at lower cost than non-rectangular duct designs.
The WHB types described above (flue gas cooling across a bank of tubes) all require soot blowers to maintain performance. Soot blower equipment, by itself, is not expensive, but soot blowers need significant infrastructure to operate – namely; steam and seal air – and require significant maintenance resources to maintain reliable operation and reliable WHB performance. Loss of effective soot blower operation results in higher flue gas discharge temperature. In the past, when FCC emissions control was not as prevalent as today, this increase in temperature was a purely energy conservation concern which did not adversely impact FCC operation. With current governmental focus on emissions reduction, specifically NOx emission reduction using SCR technology, it is now necessary to control the flue gas temperature at the outlet of the WHB, elevating soot blower maintenance from a routine, non-critical activity to a critical activity to maintain the FCC in operation.
Two types of steam generating flue gas coolers which do not require soot blowers for cleaning are commercially available. The first type places flue gas on the tube side and boils water on the shell side. These steam generators are fixed tube sheet designs and are installed in an inclined position with the flue gas flowing “downward” along the exchanger and steam exiting the upper portion of the shell. The inlet tube sheet is refractory lined, and the inlet of each tube is fitted with erosion-resistant, replaceable ferrules for erosion protection. The steam generation section is natural circulation, and units are not normally spared. Superheater and economizer coils cannot be integrated into this type of equipment. To include these features, separate duct coils and enclosures are required. High pressure steam (600 psig and higher) is normally generated in these units to avoid acid condensation on the inside of the tubes.
The second “cleaning-free” type of commercially available unit is a longitudinally finned vertical tube bundle with water/steam on the tube side and flue gas on the shell side flowing in “rectangular” passages formed of ¼ tubes and fins. Steam generation on the tube side of these units decreases the thickness of the shell versus a shell-side boiling design. Vertical hairpin steam generation coils require forced circulation of water to the steam generation coil. Longitudinal finned superheater and economizer coils are readily integrated into the system. Due to the complexity of the design, compared with an inclined “fire tube” design, this type of unit is normally supplied with an installed spare.
Both “cleaning-free” units require steam drums to be installed adjacent to the steam generator. Although permanent soot blower facilities are normally not needed for the “cleaning-free” type of steam generators, facilities for injection of cleaning material (such as walnut shells) should be provided.
The steam generator technology selection decision will be a project-specific one considering the level of steam to be generated, the available space for constructing the steam generator and ancillary equipment during FCC operation, the delivery time for equipment, the cost of flue gas ducting to the new SG(s), the cost of piping to and from the new SG(s) location, etc. A side-by-side assessment of the four SG alternatives is recommended to ensure you obtain the technology which fits your FCC.