Question 9: What experience do refiners have regarding fired heater stainless steel tubes OD/external polythionic acid attacks due to sulfur in fuel gas such as the ones in hydroprocessing units? What criteria are refiners using to decide when to neutralize the external side of the tubes with soda ash during turnarounds?
Vern Mallett (UOP)
UOP’s recommended neutralization procedures follow the recommendations found in NACE RP0170-2004 1.6. It states:
“The need for protection of the external surfaces of austenitic stainless steel and other austenitic alloy heater tubes should be considered when sulfur-containing fuels have been used for heater firing. In many applications, however, combustion conditions do not form the iron sulfide film that is a key to polythionic acid formation. Consequently, many users do not require protection of the external surfaces of austenitic stainless steel heater tubes. It is only when poor combustion practices lead to reducing conditions that it is possible to generate sulfide scales versus oxide scales externally on heater tubes.”
If it has been determined that sulfide scale is present, then the heater tubes can best be protected by maintaining a balanced set of small fires (or pilots, as applicable) in the heater box at all times, even when there is no process circulation.
UOP conducted a survey of several refiners’ neutralization practices in 2009 and found that the majority of refiners did not take any steps to protect the OD of heater tubes when the heater was shutdown. Out of the refiners that do take steps to protect the OD of heater tubes during shutdown, they are divided between running pilot burners and neutralizing with a soda ash solution.
Of the total 13 total responses, 7 conducted no neutralization of the heater tubes, 1 left pilots on in the heater, 3 conducted soda ash solution neutralization, and 2 left pilots on but conducted soda ash neutralization if entering the heater
Dan Webb (Western Refining)
Austenitic stainless steel (300 series) heater tubes should always be protected against if the fuel contains any appreciable about of sulfur compounds. These metal sulfides form polythionic acids (H2SxO6) when exposed to a wet oxygen environment. We recommend that the refinery Inspection department be consulted prior to shut down when 300 series stainless steel is involved.
Austenitic SS become sensitized to polythionic acid attack after long term service at high temperatures 700° to 1300°F. Sensitization describes steel that has formed chromium carbides along the grain boundaries, producing adjacent chromium-depleted regions that are not as resistant to many corrosion mechanisms. Even stabilized SS may become eventually become sensitized to polythionic acid attack although the time required is greater.
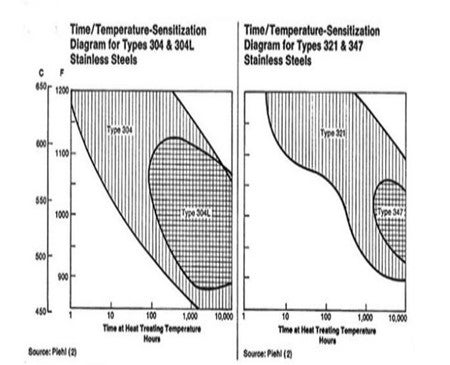
Standard practices for avoiding Polythionic acid SCC are fully described in NACE Standard RPO170. But, in general, the best protection is to maintain a dry air free environment during shutdown. If this is not possible the SS should be neutralized with soda ash solution prior to exposure to air. Austenitic SS that will not be opened should be sealed in a nitrogen-ammonia atmosphere.
Example Neutralizing Procedure:
· 5000 ppm anhydrous ammonia should be injected with the nitrogen if the equipment is cooled to within 130°F
· Inert atmosphere should be maintained by using valves, blinds or rigid plastic covers and duct tape.
· 2% soda ash solution (Na2CO3) should be sprayed over 300 series SS, leaving the soda ash residue to remain on the tubes during the exposure to air. 0.5% sodium nitrate solution to minimize chloride stress corrosion cracking if chloride concentration in over 60 ppmw.
· 1.5% soda ash solution (Na2CO3) should be sprayed over the tubes unless the tubes are kept above 300°F. If tube temperatures will be < 150°C for 4-6 hours, soda ash washing is not necessary
Michael Chuba (Sunoco)
Within the Sunoco system for those heaters using stainless steel tubes we do not generally neutralize the external surfaces of heater tubes during temporary shutdowns or turnarounds. The main reason for this is that the conditions in the fireboxes do not favor formation of sulfide scale on the metal surface. This is one of the critical factors for concern over polythionic acid stress corrosion cracking or PASCC.
Since our hydrotreaters are gas fired, sulfur contents are generally low. In addition, we generally operate with at least 3% excess O2. This results in an oxidizing versus reducing environment. In this environment any iron sulfide scale that may form is quickly converted to an iron oxide, with the sulfur being returned to the flue gas and exiting the firebox as SOx. Thus, for reactor charge heaters in the Sunoco system there is little potential for sulfide scale on the tube surfaces to present a PASCC concern; consequently, passivation of tube ODs during unit outages is typically not necessary. We have not experienced any PASCC failures due to tube OD corrosion.
For heaters that operate in a reducing atmosphere (zero excess O2), where a stable iron sulfide scale may form on the tube surfaces, passivation should be consider. Another case where passivation may be required is where the type of fuel burned in the heater (such as heavy fuel oil) may create heavy ash deposits on tube surface. Localized reducing environments at the tube surfaces (under the deposit layer) can restrict the oxidation of the iron sulfide scale during operation making it susceptible to PASCC.
There are other factors that would need to be considered to determine if soda ash passivation of the tube surfaces is needed. The first factor is the tube metallurgy, and whether the heater tubes are a “stabilized” grade of austenitic stainless (such as grades 321 or 347). For these stabilized metallurgy grades the metal operating temperature must be above 850F for at least 1000 hours before the materials would be “sensitized” and susceptible to PASCC. For heaters that have these materials and operate at reduced metal temperatures the soda ash passivation would not be needed even if sulfide scale were present on the tube ODs.
For heaters that operate with metal temperatures above 850F, or the tube materials are from non-stabilized grades (such as grades 304 or 316) then PASCC potential is a concern if the conditions for sulfide scale formation are also present. The final factor to consider in this case is whether moisture will be present inside the fire box during a unit outage. The sources of water can be dew point condensation, rain leakage into the fire box, or any water-washing activities inside the heater. The best method to avoid PASCC is to keep the tubes dry during outages (using dry air purges, N2 purges, space heaters to stay above dew point, etc.). If dry conditions cannot be assured then a sodium carbonate solution should be used to wash (to remove as much ash as possible) and rinse the tube ODs – with the neutralizing residue re-applied whenever it is washed away.