Question 9: Describe your experience and application of advanced separation techniques, such as DWCs (dividing-wall columns), to reduce capital investment and operating expense.
KLEISS (Valero Energy Corporation)
At Valero, we actually have several dividing-wall column applications. We have four in aromatics recovery service and one in a sat(saturated)gas plant service. The towers in aromatic service have been in operation between three and six years, and the tower in the sat gas service has been in operation since early 2016. All towers are meeting their design expectations. The dividing -wall towers have several advantages relative to the traditional sequential column designs. The first advantage is a smaller plot area and a lowerequipment count, which results in a capital savings of about 20 to 30%. The second advantage is a reduction in energy use of about 20 to 30%. The towers we have in aromatics recovery service are about 12 to 15 feet in diameter and about 230 feet tangent to tangent.
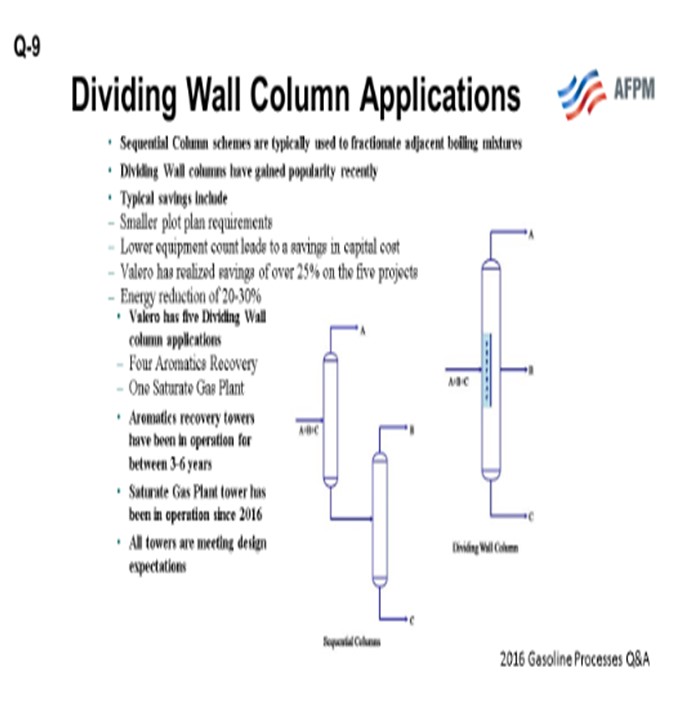
This slide shows a picture of one of the towers that is in aromatics recovery service. I noted on the bottom of the slide that there is an article published in the March 2011 NPR Annual Meeting papers that discusses the design and the contractor with whom Valero worked for the dividing-wall columns that were in the aromatic's recovery service.
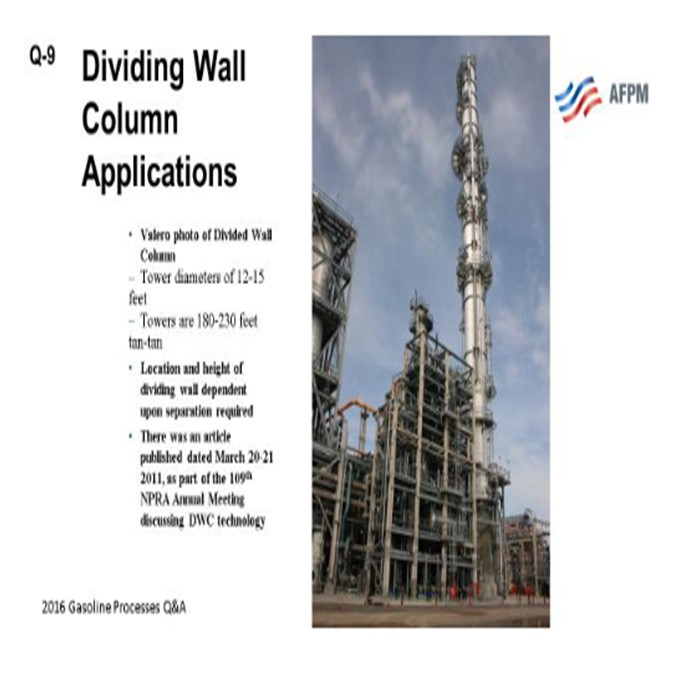
On the next slide, you can see a basic drawing of how the towers function. Instead of just having a light key and heavy key, you have individual light, middle, and heavy keys. One of the important process parameters is the feed temperature. It is critical in making sure that the light key goes up the tower and the heavy key goes down. The picture below is a graphic representation of how the towers basically work.
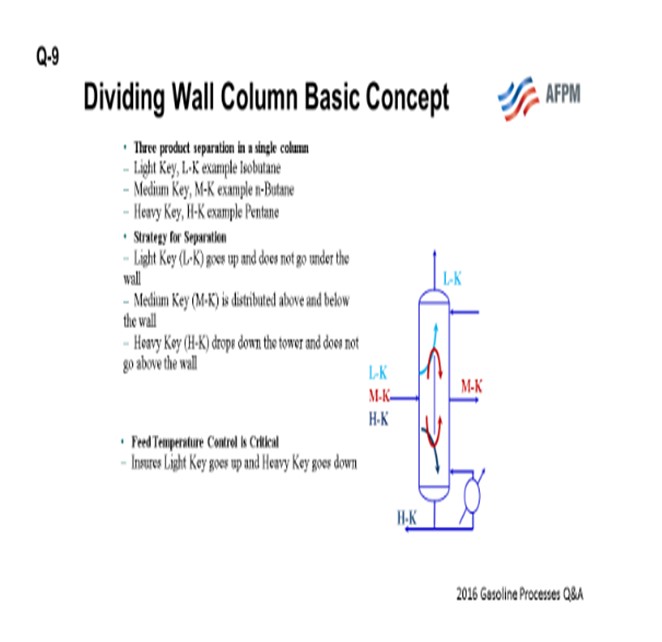
PHILOON (Honeywell UOP)
Honeywell UOP has been including dividing-wall columns (DWCs) in process unit designs, where they make sense, for a number of years with good success. We estimated and have seen significant reductions, as James was saying, in capital and operating costs on those columns. Most of the applications have been in benzene toluene fractionation in aromatics complexes or in linear alkyl benzene (LAB) detergent alky complexes. All of the columns with which we have been involved and which are operating have worked well, delivering the expected quality in each of the product streams with the predicted utility savings. The control systems have been able to deliver consistent products in generally robust operations. Recently, UOP completed the design of a dividing-wall column as a naphtha splitter in a naphtha complex. The overhead of the column is isopentane. The sidecut is a light naphtha (nC5and C6) that will be used as feed to a Penex™ isomerization unit, and the bottom is heavy naphtha that will be used as feed to a Platforming™ unit. This column is not yet in operation.