Question 89: With the increase in rare earth costs, many units have decreased the rare earth oxide (REO) content or used rare earth substitutes in their FCC catalyst. What is your experience with these in terms of activity maintenance, delta coke, conversion, attrition, and yield selectivity's? How have operating conditions changed?
AVERY (Albemarle Corporation)
Rare earth stabilizes zeolite and increases hydrogen transfer. Reducing the rare earth on zeolite will decrease the catalyst activity at the same zeolite content and matrix activity. Most refiners who reduce rare earth have increased the amount of active component. This increase has resulted in higher zeolite content and more matrix activity. This shift can be confirmed by higher surface area and higher alumina on fresh catalyst.
The results vary. In general, gas oil operations and mild operating FCCUs have experienced little decrease in activity. Resid units have either maintained the original rare earth or zeolite or rare earth on zeolite ratio as these are operated at lower activity. There have been several papers published that outline the use of non-typical rare earths or other elements to stabilize the zeolite. As an example, phosphorus has been used for decades to stabilize ZSM (Zeolite Socony Mobil) additives. At least one catalyst supplier has recently published the use of phosphorus to stabilize FCC catalyst. These substitutes generally do not provide the same level of cost-effective stability as rare earth. If they had, it would have been in common use in FCCs long before now.
The effects of lower rare earth are widely known. They include higher LPG, lower gasoline, higher gasoline octane, lower activity, and lower delta coke. Even before the rare earth cost increased, Albemarle clients had the lowest rare earth in the industry. The slide shows a survey of all the North American e-cats, including when a refiner uses a SOx reduction additive that results in a slight increase in rare earth. If refiners are using a ZSM additive, it will make the rare earth go lower than the typical rare earth on the fresh catalyst.
Now look at some surveys of a couple of years of industry within North America and worldwide. You can see the highs in 2009 when it went from 6.7% down to 4.1% now. The average in North America has gone from 2.8% down to 2.1%. You could also see the comparisons for worldwide, Albemarle, and North America.
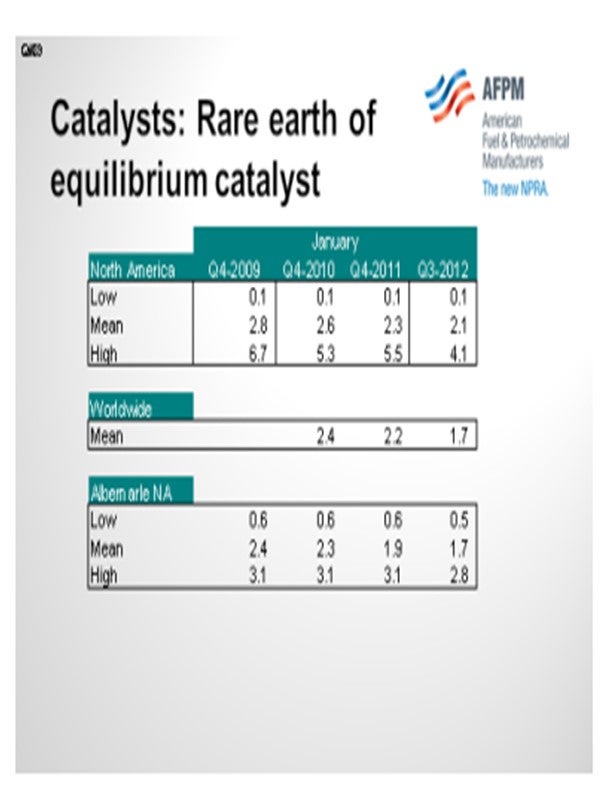
The next slide shows one catalyst system. For the matrix activity to be the same, all I did was go from 3% rare earth down to 1.5% rare earth; then with our models, I increased the zeolite until we got the same activity. I am just giving you an idea of how much more surface area or zeolite you will need in order to maintain the same activity. In this particular case, you have a catalyst going from 3% rare earth oxide to 1.5%. Due to the lesser stability of the lower rare earth, the zeolite surface area must go from 225 up to 270. With that, you will see more LPG, right? You will see lower gasoline and significantly more octane. Higher olefinicities will be present in the C3 and C4s.
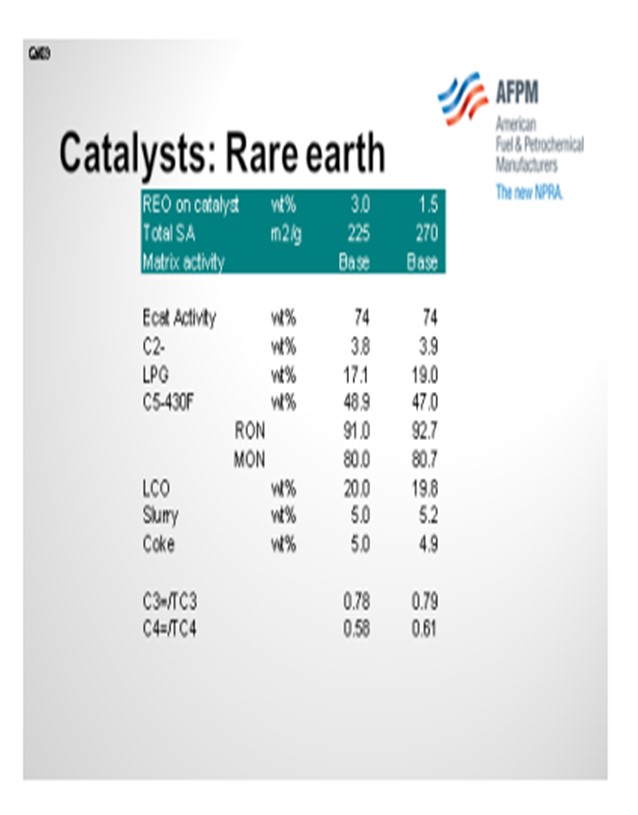
BROOKS (BP Refining)
With the increase in rare earth cost, BP went through a series of reductions and rare earth on catalyst changes at a number of our sites. We did a bit of modeling work, and we decided not to drop the rare earth on every site we reviewed. Our models and the catalyst pricing with the surcharges at that time were used to evaluate our path forward. Our projected economics did determine an optimum point for each of our sites to get an idea of the appropriate rare earth on zeolite level within the balance of the manufacturing limits from the vendor.
For the sites on which we did make changes, we typically attempted to maintain rare earth on zeolite as much as possible to prevent the shift you should see in gasoline, LPG, and olefinicity and also to prevent the activity drop you would expect. We increased our zeolite surface areas on the sites where that was an option.
We have not yet had an opportunity to evaluate all of our changes. We have completed a lot of these reformulations. A base review of the operating data showed what we expected. In the units where we dropped rare earth on zeolite, we saw an increase in olefinicity and more LPG. Most of the time, we were able to balance that yield shift by backing out some of the ZSM-5 additive in use; so it was not really a problem for most of our units.
Many of our units that made adjustments to rare earth also dropped it in steps, especially if they were making very large changes in rare earth, so that made the yield pattern shifts a little less obvious. We saw what we expected in these step changes: an increase in catalyst addition rates for most of the units that made a significant drop in rare earth. We did not see a huge shift in the stability of the catalysts, especially in our hydrotreated units.
We do have one unit that runs some resid. In a situation like that, particularly with high metals, there is some nasty feed coming in with their resid stream. They saw what they thought was a drop in stability that required the addition of a lot more catalyst to maintain activity. They have come up on rare earth since the market prices have gone back down, but that is the only unit on which we went back up in rare earth levels because of the stability of the catalyst.
We have not seen any noticeable attrition shifts with the drop in rare earth. Also, we did a trial of a few of the rare earth-free catalysts blends. One of our sites actually adjusted the blend throughout the trial and would step more and more of the rare earth-free catalyst into the blend. They were able to step it up to 50% of their blend and did not feel as if they saw any difference in coke or bottoms makes. Again, that has not been fully evaluated, but they were happy with their yield patterns.
SCHOEPE (Phillips 66)
Phillips 66 actually reacted aggressively as rare earth prices increased. On average, the rare earth content was decreased by about 0.7%. In most cases, we tried to compensate for the decrease in the rare earth with an increase in activity. Overall, if we used e-cat activity as a benchmark, we really did not see a big decrease. One unit had a little bit higher activity; another one had lower activity. We did, however, see the effect that Cliff described. We saw a decrease in gasoline selectivity, which, in one unit, was great because they had additional capacity in the alkylation unit. Another unit struggled with increased LPG yield because they were wet gas compressor limited.
PIMENTEL (CITGO Petroleum Corporation)
During that rare earth crisis, we had a sharp reduction in rare earth concentration from 4.5% to less than 1% in our catalyst. We found no issues with attrition or catalyst losses in any of our units. We did reformulate the catalyst to increase matrix surface area. That reformulation was done in anticipation of the lower delta coke resulting from that catalyst formulation. The LPG increment was very small: in our experience, less than 1%. The catalyst activity reduction experience changed from unit to unit. In some of our units, we stayed at the same catalyst addition rate to achieve the same activity; while in other units, we had to increase up to 20% of our addition rate.
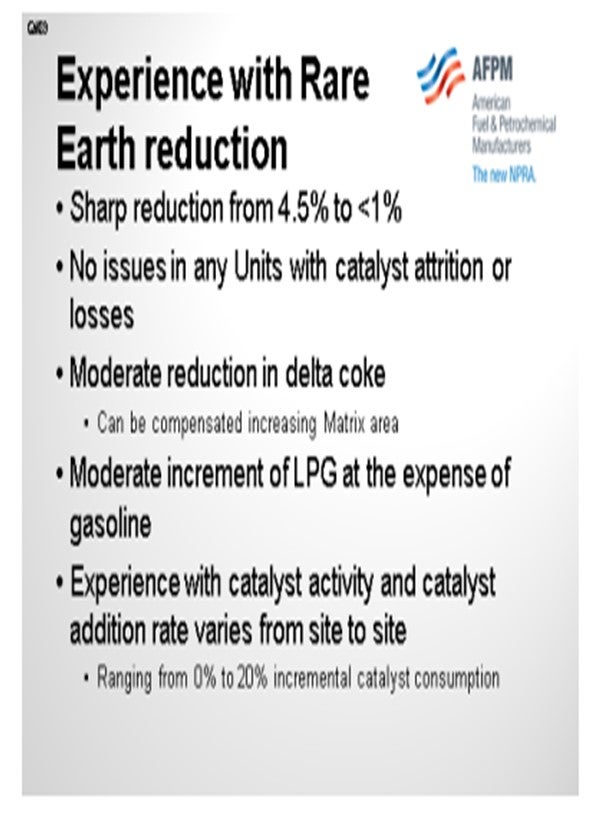
JOSEPH McLEAN (BASF Catalysts LLC)
This past August at the 2012 Cat Cracker symposium in Houston, there was a session during which the three U.S. vendors all participated. Those presentations will all be on the AFPM website; so rather than rehash what was discussed, I will just direct you to the details within those transcripts. I also want to point out that as the rare earth prices have gone down, the quantity of rare earth being used by the customers has increased]. Our average shipping content for the past two quarters has bottomed down the first quarter of this year. The content is not quite back to where it was two years ago, but this quarter shows that it is heading in that direction.
AVERY (Albemarle Corporation)
Rare earth (RE) stabilizes the zeolite and increases hydrogen transfer. Reducing the RE on zeolite will decrease the catalyst activity at the same zeolite content and same matrix activity. Most refiners who reduce RE have increased the amount of active component. This has resulted in higher zeolite content and more matrix activity. This shift can be confirmed by higher surface area and higher alumina on fresh catalyst. The results vary. In general, gas oil operations or mild operating FCCUs have seen little decrease in activity. Resid units have either maintained the original RE on zeolite or operated at lower activity. There have been many published papers outlining the use of non-typical REs and other elements for zeolite stabilization. As an example, phosphorus has been used for decades to stabilize ZSM-5 additives. At least one catalyst supplier has recently published the use of phosphorus to stabilize FCC catalyst. These substitutes generally do not provide the same level of cost-effective stability as rare earth; if they had, they would have been in common use in FCC catalyst long before now. The effects of lower RE are widely known. They include higher LPG, lower gasoline, higher gasoline octane, lower activity and lower delta coke. Even before the RE costs increased, Albemarle clients had the lowest RE in the industry. North American averages are listed below.
BROOKS (BP Refining)
BP decreased rare earth levels on a number of units due to the high rare earth cost environment last year. If possible, we targeted reduced rare earth (RE) levels with increased zeolite (Z) surface area to the offset the reduction in catalyst stability and minimize the impact on catalyst additions/activity. Although we targeted minimal shifts here, our unit reformulations typically resulted in some drop in RE/Z which was expected to cause increases in LPG yield, a decrease in gasoline yield, and an increase in LPG and gasoline olefinicity. However, in some cases we were able to adjust the ZSM-5 usage rates to manage the selectivity shifts that come with a change in RE/Z ratio.
In our analysis to determine the most profitable RE level for each unit, we used our FCC process model to optimize the unit operating conditions against each sites’ commercial pricing projections and unit constraints for various RE levels in the catalyst. This allowed us to consider the impact of the predicted yield shifts and catalyst addition rates in conjunction with the shifting catalyst prices (including RE surcharges) to identify the conditions that would result in the highest unit margin. In some cases, the model work resulted in reduced e-cat MAT for operating cost reductions which was then balanced by increased riser temperatures to maintain conversion. For these cases, a shift in delta coke was predicted. However, in cases where the e-cat MAT and other operating conditions were maintained, the delta coke was projected to remain unchanged as long as the metals levels on e-cat did not shift significantly. This could also be said about conversion; i.e., lower optimized MAT would yield lower conversion, but constant MAT and operating conditions would result in no change. Our FCC process model was used to select an optimized RE level based on each sites’ commercial pricing projections, unit constraints, yield shift projections, shifts in catalyst addition rates, and catalyst prices (including RE surcharges). Because there was some uncertainty around the expected catalyst addition rate and yield shifts, many of our units that were making a large shift down in RE levels did it sequentially by stepping their RE levels down to the optimum suggested in the modeling studies.
We have not yet had an opportunity to complete full evaluations on these RE shifts so cannot be sure of the absolute yield and catalyst addition shifts observed. However, unit yields appear to have made the expected step changes in LPG and gasoline yields and olefinicity. Addition rates have gone up slightly as expected. Catalyst stability seems good in the majority of our units. One unit which periodically runs high levels of metals on e-cat due to feed contaminants noted a drop in catalyst stability at heavy metals loading and has since increased RE levels slightly to handle swings in feed quality better. We have not seen any changes in attrition with the lower RE catalysts. We have one site that has trialed a RE-free catalyst as part of a blend with another RE catalyst. Their trial showed no significant shifts in coke or bottoms yield at blend levels of up to 50% RE-free catalyst. We have another site who has implemented a catalyst blend which includes and RE-free portion of the formulation. This was a recent change and has not yet been evaluated for actual yield and addition rate shifts. However, they have not noticed any significant issues with operation on this catalyst via regular unit monitoring methods.
SCHOEPE (Phillips 66)
As rare earth prices increased, the average rare earth content on Phillips 66 units was decreased by 0.7 wt% to about 2.0 wt%. In most cases we compensated for the lower rare earth content by increasing zeolite content to maintain target equilibrium activity. Although one unit saw an increase in equilibrium catalyst activity and one saw a decrease, most of our units maintained constant equilibrium catalyst activity, despite the reduction in rare earth content. In general, this reformulation caused the gasoline selectivity to decrease slightly at the same conversion, with the expected increase in LPG selectivity. This change might have caused problems for units with wet gas compressor constraints.
PIMENTEL (CITGO Petroleum Corporation)
In one unit, we lowered rare earth on one FCC from 2.8 wt% to 1.35 wt% and made a modest formulation change. Catalyst additions had to be increased by 20% to 25% to maintain the same e-cat activity. Even with a significant reduction in stripping steam, delta coke dropped by 0.05 wt% to 0.07 wt%. LPG yield increased by approximately 1 LV%. Conversion was unchanged. We did not have any attrition or opacity issues. In another unit, we reduced rare earth from 4.5% to less than 1% and increased matrix area to compensate for the expected lower delta coke. We experienced a moderate increment in C2- and LPG production (~5%) at the expense of gasoline. We did not experience incremental catalyst attrition or loss of activity at constant catalyst addition rate.
ROSANN SCHILLER (Grace Catalysts Technologies)
Rare earth plays a key role in FCC catalyst and has been traditionally used in stabilizing zeolite which preserves catalyst activity and modifies selectivity. Rare earth has also been successfully utilized as a contaminant metals trap, reducing deactivation caused by vanadium.1 There are several different avenues one could take to lower rare earth on catalyst with wide ranging impacts on FCCU yields and selectivity's. The following avenues will be discussed:
1. Lowering rare earth on zeolite,
2. Lowering rare earth and using a rare earth substitute, and
3. Lowering rare earth used for metals traps
Simply lowering rare earth on zeolite with no other changes made to the catalyst system will typically reduce catalyst activity at similar catalyst additions. Conversely, higher catalyst additions will be required to maintain similar catalyst activity. If activity/conversion is maintained, catalysts with lower rare earth will typically be more LPG selective than gasoline selective. The graph below showing this relationship was presented at the 2012 Cat Cracking seminar. The data are pilot plant yields from merely reducing rare earth on an FCC catalyst with constant zeolite and matrix input.
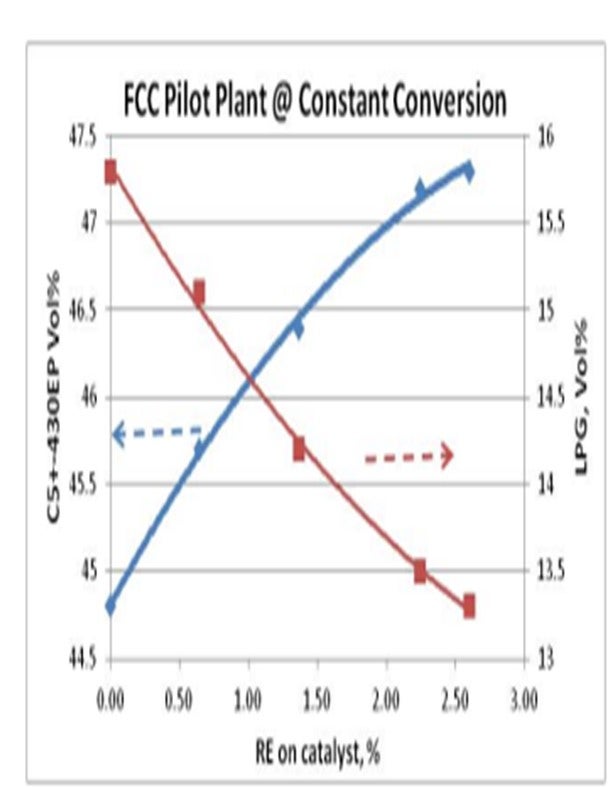
For further information on the function rare earth plays in FCC catalyst and yield selectivity's, please refer to the Grace Davison paper, “Role of the Rare Earth Elements in Fluid Catalytic Cracking.”4 One thing to note is that removing rare earth from FCC catalyst typically provides relief in catalyst expenses but is not necessarily an economical solution as most FCC operations cannot accommodate lower activity and/or product value.5
One alternative to lower rare earth while maximizing FCCU profitability is to use alternate materials and processing to stabilize the zeolite. Grace has recently added the REpLaCeR® family to its catalyst portfolio. REpLaCeR® is a collection of low and zero rare earth catalysts which have been applied in a wide range of FCC applications. 6 REMEDY™ catalyst, one of the REpLaCeR® family of catalysts with zero rare earth content, has been proven to have similar unit conversion at similar catalyst additions, similar slurry/coke selectivity, similar e-cat activity, and higher gasoline selectivity when compared to a moderate rare earth containing catalyst. In one refinery example, the catalyst was reformulated from a traditional 1.5 wt% rare earth catalyst, GENESIS®GSR®, to REMEDY™2 GSR®.7 As shown in Figures 2 and 3, the catalyst additions on a pound per barrel of feed basis were maintained with REMEDY™2 GSR® while maintaining similar conversion. Figure 4 shows both catalysts have similar coke selectivity.8 Also, REMEDY™2 GSR® proved to be more gasoline selective when compared to GENESIS®GSR® which is shown in Figure 5.9 It is also worth noting that the lower rare earth catalyst reformulation in this example did not negatively impact catalyst retention.
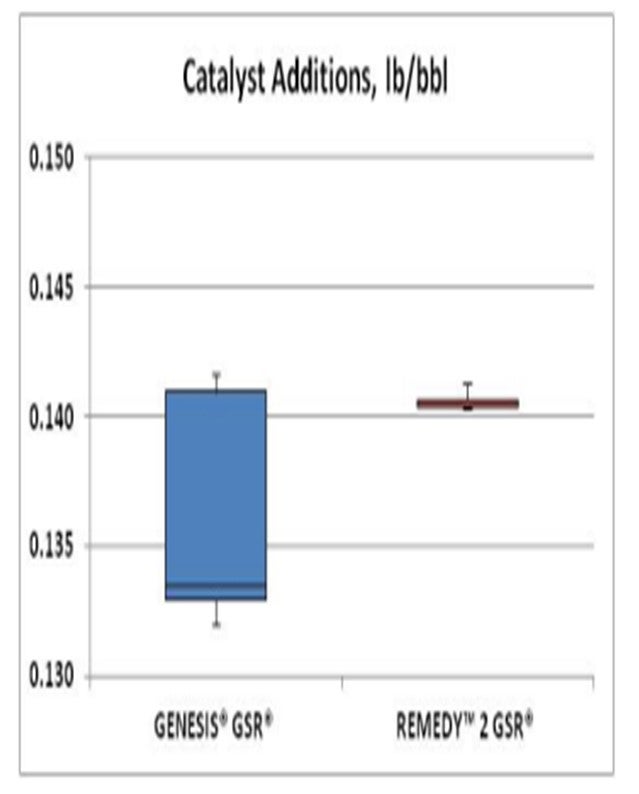
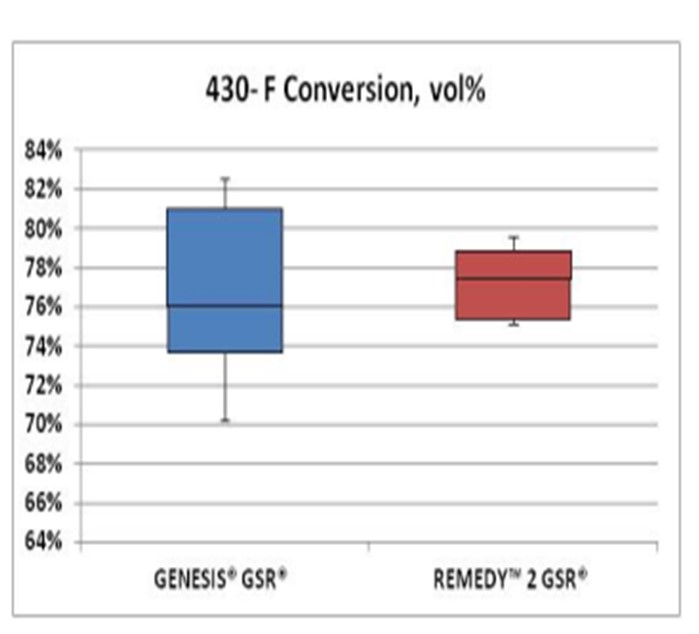
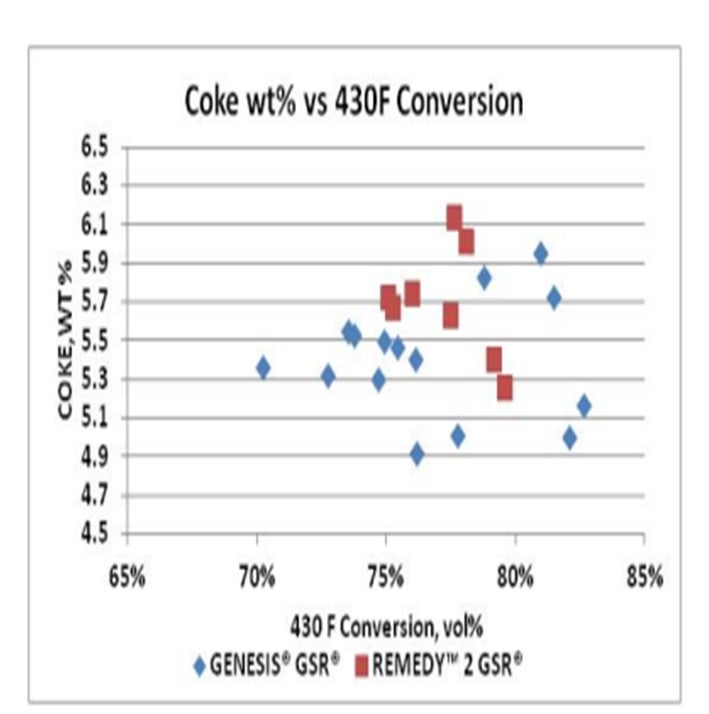
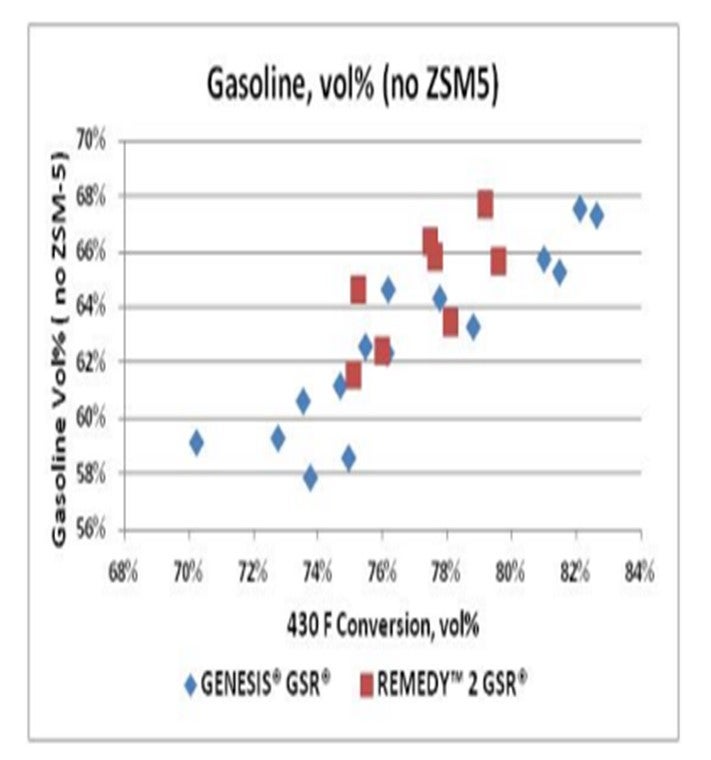
With regard to rare earth being utilized as a metals trap, Grace has been successful reducing rare earth by 40% without sacrificing activity or selectivity with the re-optimization of our IMPACT® technology, ResidUltra™14. Commercial experience proves that unit performance is nearly interchangeable.15 In lab testing ResidUltra™ and IMPACT® samples were deactivated with metals levels of 3,000 ppm V and 2,000 ppm Ni and tested side by side in the ACE unit over a residual feedstock.16 The constant conversion data is summarized in Table 1. In this scenario, relative to IMPACT®, ResidUltra™ has similar catalytic activity, the same hydrogen selectivity, slightly better coke selectivity, similar gasoline, similar LCO, and similar bottoms yield.17 ResidUltra™ yields slightly higher-octane number and LPG olefins.
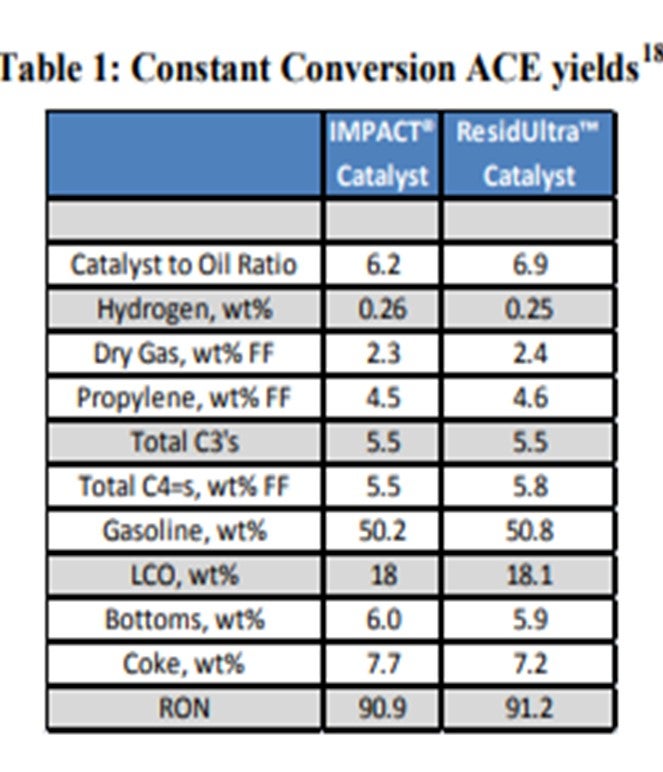
In summary, the means by which a catalyst supplier might lower rare earth may have no impact or a substantial impact on catalyst activity and FCCU yields and selectivities. Your unit objectives and constraints will dictate which catalyst reformulation best fits your FCCU.