Question 89: For an equipment revamp/replacement, what are the factors you consider when choosing between hot-wall and cold-wall refractory design, including advantages and disadvantages of each?
REYNOLDS (Phillips 66)
At Phillips 66, we predominantly rely on cold-wall equipment. Our approach is typically to use cold wall, unless we cannot use it for reasons I will discuss. There are situations where you are not able to use cold-walls, where the larger physical size of the cold-wall equipment cannot fit in the space allowed or if the additional weight requires too much structural steel modifications to fit it in.
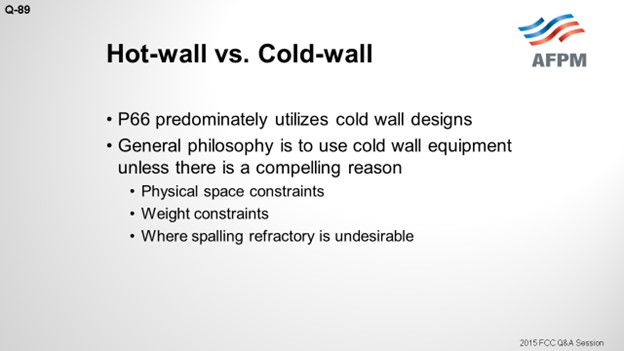
Another circumstance where you may not want to use hot wall is upstream of the power recovery equipment where spalling off refractory is not good. So an option that I have heard described as a “warm-wall” is basically to have a cold-wall design in which you put a stainless-steel skin on the inside to minimize refractory spalling.
One of the issues with the hot wall is that the hotter temperatures force you into higher metallurgy of all the equipment. For carbon steel going from 650 to 1000°F, allowed stresses will go down by a factor of seven. The additional cost of that higher metallurgy will usually balance out with the refractory. We found that cost to be fairly comparable. Also, cold-wall metallurgy will not suffer from or be as susceptible to creep and sulfidation as will hot-wall metallurgy.
You need to keep future repairs in mind. The refractory repairs will require a dryout. But when you work on a hot wall, that hot work will often require expensive and time-consuming post-weld heat-treating. Also, the higher metallurgy may push you into a hexavalent chrome concern, so the workers performing the hot work will be in fresh air. If you are inside the equipment, everyone else in that vessel may have to be in the fresh air as well, which will slow down the work.
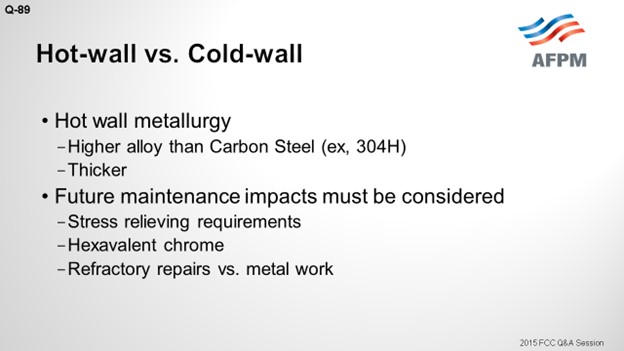
I included this comparison of slide valves, but it is applicable for fixed equipment as well. I have touched on most of these bullet points. We have had better reliability with cold wall slide valves. The slide says that for cold-wall designs, exterior insulation is not required; but it actually is typically not allowed.
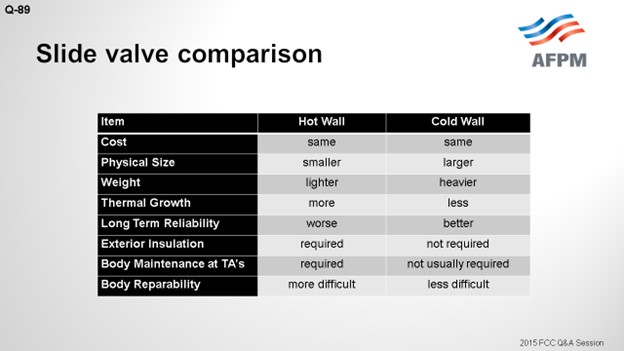
FOSHEE [Shell Global Solutions (U.S.)]
Shell has experience with both cold-wall and hot-wall refractory designs for reactors and stripper vessels, but regenerator vessels are always cold-wall refractory designs. Depending on the reactor and stripper vessel, refractory type and standpipes, liftpots, and external portions of the riser can be either cold-wall or hot-wall designs. However, having said that, our current Shell standard is to use cold-wall design for all grassroots FCC projects for the design of all vessels, standpipes, liftpots, and external portions of the riser.
For a revamp FCC project, sections of the unit that are hot-wall are typically replaced with a hot-wall design unless the foundations and steel are improved to handle the additional weight of the cold-wall design. I will add here that for cold-wall refractory, one of our Best Practices is to stencil along the surface of the metal the words: “This is a cold-wall refractory. Do not insulate.”
Cold-wall refractory has several advantages over hot-wall refractory. First of all, you are able to use less expensive carbon steel for the vessel shell versus a more expensive alloy. In cold water refractory design, you do not have temporary embrittlement issues in the steel, whereas in hot-wall design, you can run into these problems. Also, external insulation is not only not required; it is absolutely not put on cold-wall refractory. Hot-wall refractory designs do need external insulation.
There are a few drawbacks to cold-wall designs. First of all, hot-wall refractory can be easier to repair, and it is faster to cure than cold-wall refractory. Secondly, hot-wall refractory is much lighter than cold-wall refractory. And thirdly, as I have mentioned before, putting insulation on the outside of cold-wall refractory design will cause problems with the vessel metallurgy that will eventually lead to metal failure, whereas hot-wall designs do not have this issue.