Question 88: Describe your approach to repair and improvement (i.e., materials, design, installation, and anchors) to areas that have seen repeated refractory failures.
FOSHEE [Shell Global Solutions (U.S.)]
In Shell’s experience, typical repeat refractory failures are caused by three different scenarios. First of all, it is due to improper repair and installation. Another scenario could be extreme refractory geometry. And then finally, it could just be due to a poor choice of refractory initially.
Speaking of the improper refractory repair, especially in a hot-wall refractory with the coking service, low alloy base metal requires a 300°F preheat along with removal of all sulfides on the metal surface. If you do not do this, you will get weak and brittle welds that will crack easily because of their low weld strength. And therefore, your anchors will break off and your refractory will fail due to the coke growth behind the refractory.
In extreme geometries, such as in the Y-piece or a bull nose, in cold-wall refractory, Shell usually uses what is called a monster tab, as shown on the slide, to anchor the system.
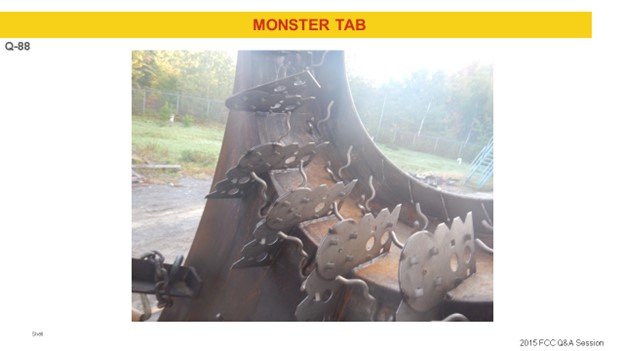
To prevent flow bypassing, as I mentioned previously, Shell uses what is called a vapor stop. You can see there that it is a ring of steel that goes around the vessel and protrudes into the refractory.
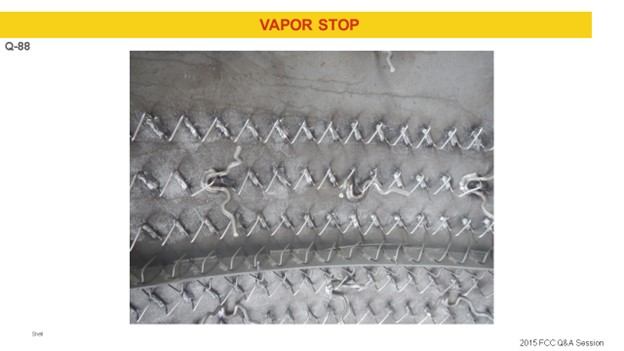
As far as poor refractory choice is concerned, in areas where you have severe erosion issues, you can obviously choose a more erosion-resistant refractory initially. Also, in areas where water sprays are a concern, it is important that you use a proper refractory, such as a fused silica thermal shock resistant refractory.
Regarding the repairs itself, a hot-wall repair requires complete removal of both the refractory and the hex metal in the affected area. Prior to reinstallation of the new refractory anchors, the metal surface must be prepared and cleaned, which means that it must be ground and power-brushed before welding onto the new anchors.
For large repairs, Shell typically uses curl anchors because using hex metal for a large repair is too time-consuming. For small repairs, Shell has had experience using speed hex. After the anchor is installed, you apply the new refractory. Here is a picture of some speed hex.
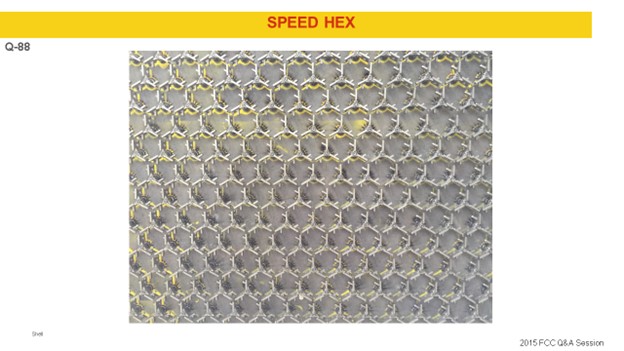
On cold-wall repairs, there is a similar repair method for both large and small repairs. Damaged refractory is removed back to the base metal (new cold-wall refractory is not put on top of the existing cold-wall refractory). For large repairs, the damaged refractory is cut back at a 90-degree angle to the metal surface. For small repairs, you can use an undercut, which will help lock in the refractory repair.
The metal surface for both large and small repairs must be cleaned and prepped, which includes grit blasting and grinding. If the metal or anchors are damaged, the old metal anchors must be completely removed and replaced. If there is a discontinuity in the repair area, which would be like a nozzle or something protruding the vessel, the refractory repair either has to completely surround the discontinuity or stop three anchors from the discontinuity. For both big and small repairs, three anchors need to be exposed for the repair to be successful. Once you have your anchors installed, the metal surface is wetted, and a new refractory is applied.