Question 87: In your experience, how does catalyst activity affect the catalyst's coke selectivity and the FCCU's delta coke? How are the coke selectivity and delta coke related? Lastly, discuss how to determine the proper activity to maximize conversion.
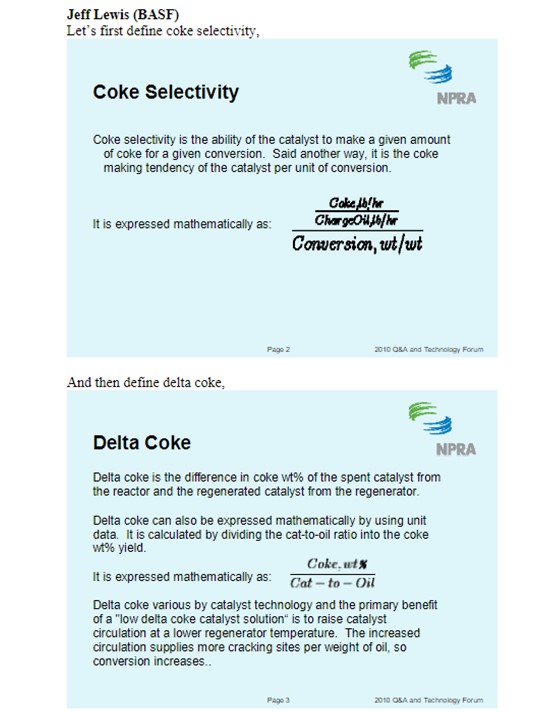
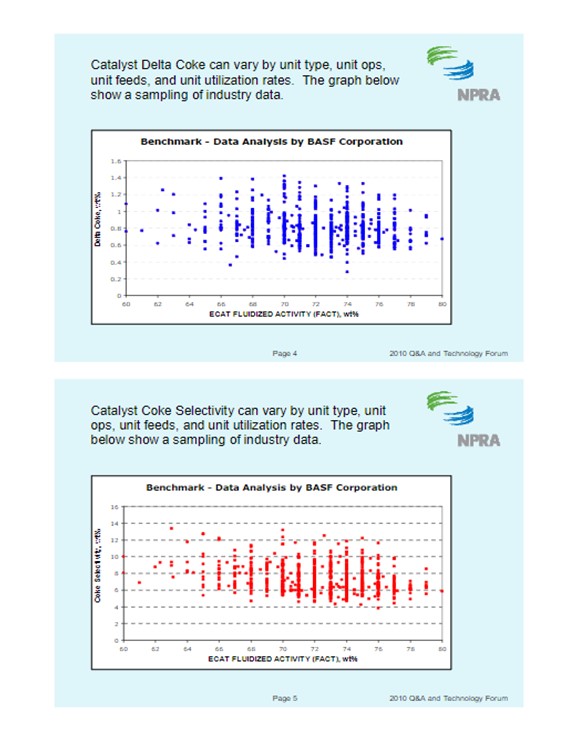
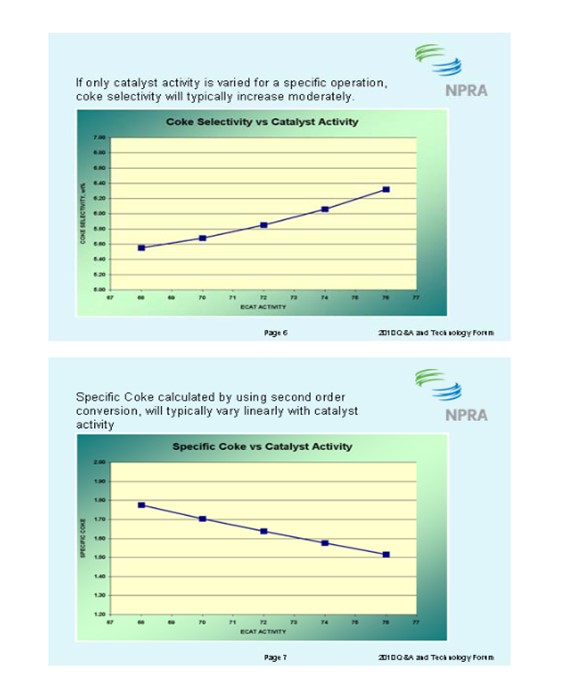
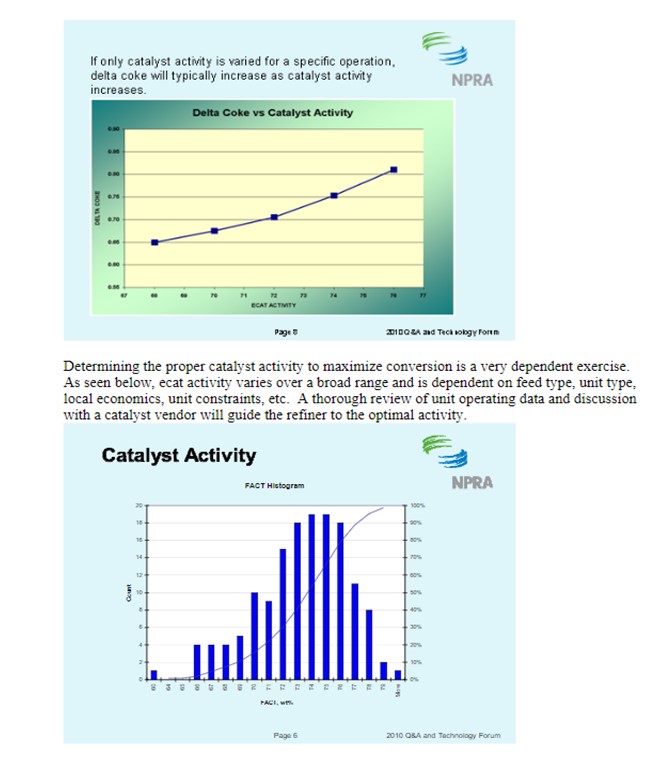
Rosan Schiller (Grace Davison)
When designing an FCC catalyst, one must consider coke selectivity, delta coke and total coke yield. Coke selectivity is the relative coke-making tendency of the catalyst, or in other words, a catalyst with good coke selectivity produces higher conversion per unit of coke make than the reference catalyst. Delta coke is, simply put, the difference between carbon on spent catalyst after stripping, and carbon on regenerated catalyst. Delta coke is expressed as a percentage of the catalyst. Generally, the delta coke is higher for catalysts with poor coke selectivity but is also higher for more active catalysts and with heavier feeds. Higher delta coke translates to higher regenerator temperatures.
Total coke yield is the delta coke times the catalyst-to-oil ratio. In other words, total coke yield is the amount of coke burned in the regenerator, expressed as a percentage of the feed rate. Burning this coke, total coke, is responsible for fulfilling all the heat requirements, including the heat of reaction, in the FCC process. Total coke cannot change unless there is a change in these heat requirements. Consequently, if these heat requirements are held constant, a change in delta coke will cause an opposing change in Cat/Oil ratio to maintain the total coke yield constant.
There are 4 contributions to total coke: feed carbon, contaminant, stripping and catalytic. The feed coke can be approximated by the Conradson carbon level. Stripping or cat-to-oil coke results from the carry-over of occluded hydrocarbons after stripping. Stripping and feed coke are non-catalytic. Contaminant coke results from the metals in the feed, primarily Nickel and Vanadium. Lastly, catalytic coke is the intrinsic coke making tendency of the catalyst and feed. While both contaminant and catalytic coke appear to be controlled via catalyst, they are also dependent on the Cat/Oil ratio, which always adjusts to maintain the exact amount of total coke yield required for heat balance.
Catalyst design has a direct bearing on the formation of variable components of total coke. The needs for in-unit activity (catalytic coke) must be balanced against the contributions to coke from feed carbon and contaminant metals. For a resid application, a catalyst with “good coke selectivity” would typically have moderate activity and exhibit superior stability to metals deactivation as well as the ability to crack and convert coke precursors into liquid product. In this case, the effect of contaminant metals is minimized, and the catalytic activity is balanced against the contribution from feed carbon. A heavily hydrotreated feed application, where there is minimal contribution to total coke from feed or metals, requires a higher catalyst activity to satisfy a given heat balance. If the catalyst is not active enough, torch oil or recycle must be utilized to achieve the equivalent targeted coke yield per unit of feed, often to the detriment of the overall operation. For these hydrotreated feeds, the recommended catalyst still must possess excellent coke selectivity (that is achieve high conversion for a given coke yield) but have enough activity (delta coke) to deliver the prescribed total coke for the application. At Grace Davison, we strive to deliver the most coke selective catalyst for each application, in order to maximize liquid yield and profitability.