Question 86: In your experience, what are catalyst best practices to shift FCC yields rapidly between gasoline and diesel maximization and then back again? Many catalyst suppliers are recommending blended catalyst systems. Do you believe this catalyst/additive blending is the best approach?
Jeff Lewis (BASF)
Co-catalysts are a new product category providing the refiner with the flexibility to change the product slate of the FCC without changing the FCC catalyst. Changing between a maximum gasoline co-catalyst and a maximum LCO co-catalyst will allow the refiner to rapidly capture the most favorable economics at all times – maximizing FCC profitability. Co-catalysts are added to the base catalyst to rapidly change the core performance of the FCC. Due to their exceptional catalytic properties, co-catalysts drive this fundamental change in unit performance and displace at least the equivalent rate of the base catalyst. They can be added quickly to the unit making the unit performance respond to rapidly changing product values - in the shortest time – optimizing profitability far more quickly than can be achieved by reformulating the FCC catalyst.
Co-catalysts have similarities with both additives and catalysts but stand alone as a separate and new category of products. Catalysts provide the core catalytic performance of the FCC unit. Additives are added to the base catalyst to promote other process or product effects such as propylene maximization, sulfur reduction of gasoline, CO promotion, NOX and SOX reduction, etc. Co-catalysts are added to the base catalyst – at greater addition rates than typically used for additives – to change the FCC core performance.
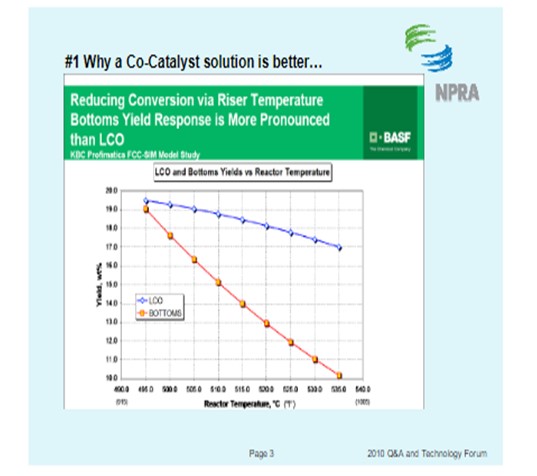
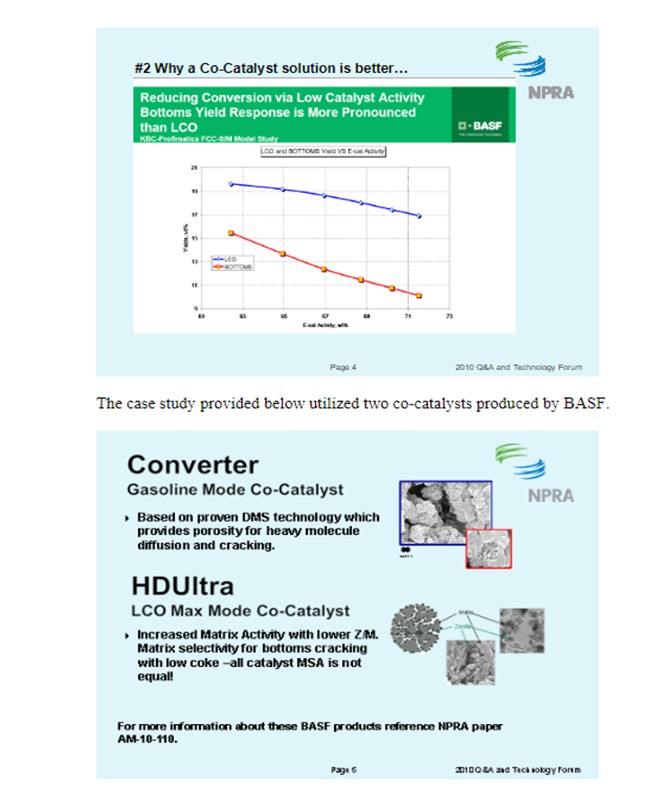
The Co-Catalyst approach is depicted below. On day 1, product economics favor diesel over gasoline by $0.45/gal. HDUltra co-catalyst is added to the unit and LCO production increases.
On day 60, the product economics have shifted to now favor Gasoline by $0.15/gal. At this time, Converter co-catalyst is added to the unit and Gasoline production increases. This type of operation continues as the volatile product pricing continues to shift between favoring diesel and gasoline.
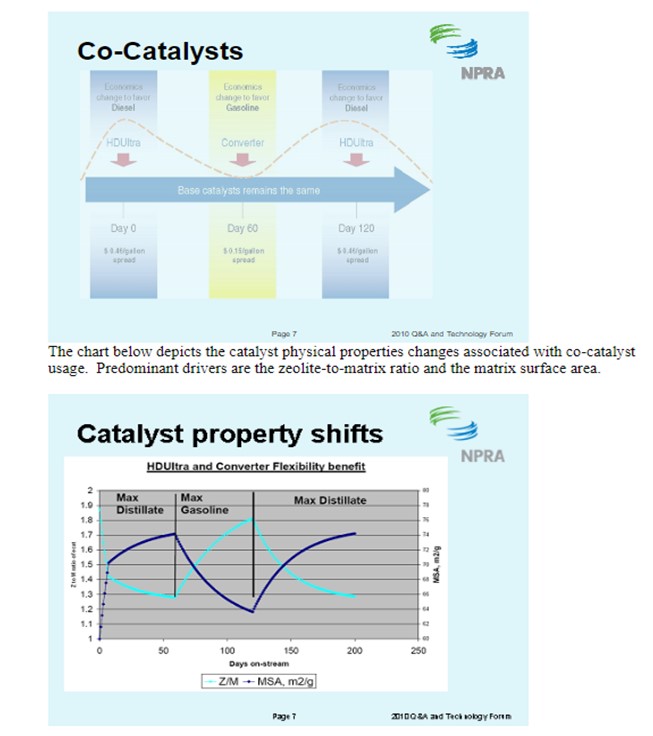
Typical post audit study results for a co-catalyst application. In this application, margin improvement was $0.23/Bbl feed. The combined additive usage cost $0.03/Bbl feed. The simplified value equation consists of spending 3 cents to make 20 cents.
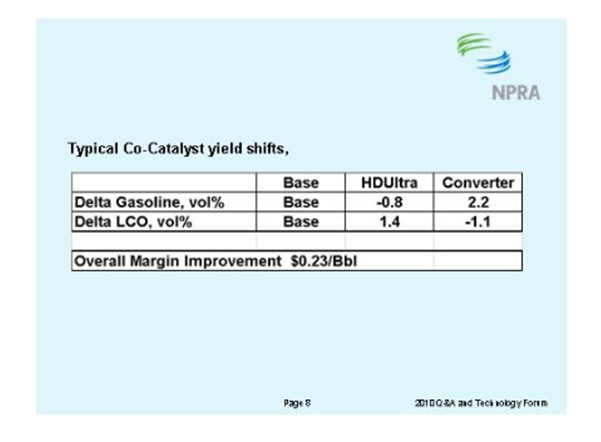
Rosann Schiller (Grace Davison)
In these challenging times, refiners more than ever need flexibility. Grace Davison delivers the flexibility most refiners need with the GENESIS® catalyst system. GENESIS catalysts provide a means to maximize yield potential through the optimization of discrete cracking catalyst functionality [1].
GENESIS systemsoffer refiners' formulation flexibility and the ability to realize the desired yield shifts quickly in order to capture dynamic economic opportunities. GENESIS is one of Grace Davison’s most successful catalysts, with 20% of the world’s FCC capacity having utilized the technology.
For new applications, Grace’s experienced technical service carefully formulates the GENESIS catalyst to achieve the stated goals of the refiner. Often, several scenarios (e.g., max gasoline or max LCO) are prepared and presented to illustrate the flexibility and the power of GENESIS to change product slate. As product supply/demand balance shifts, GENESIS catalyst in the unit can be reformulated to maximize profitability and capture short term economic opportunities. To speed implementation, formulation adjustment often takes place in the fresh hopper, minimizing the delay often associated with a catalyst change out.
GENESIS has also provided the flexibility to maximize profitability based on current supply/demand economics. Since introduction to the unit, the refiner in Table 1 has reformulated GENESIS twice; first to maximize LCO and again to return to a gasoline operation. In the max LCO operation, the percentage of MIDAS was increased in the blend to maximize bottoms cracking and reduce Z/M. GENESIS 2, formulated for max LCO, delivered an additional 3.5 lv% yield for a net increase of 5 lv% LCO and 2.2 lv% reduction in slurry relative to the competitive base catalyst [Table 1]. When economics became favorable for gasoline, the refiner returned to the original formulation. Overall, these yield shifts were worth between $0.45 and $1.00/bbl, depending on the operating mode and the refining margins at the time.
For both catalyst reformulations, the blend ratio of MIDAS and IMPACT was adjusted to achieve the desired yield shift. Grace was able to reduce turnover time by working with the refiner to readjust the formulation within the fresh catalyst hopper.
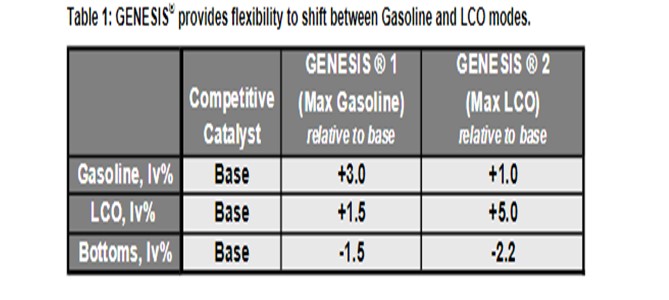
GENESIS FCC catalyst offers customers the ultimate in formulation flexibility and the option to realize those changes quickly. A decision to reformulate within a GENESIS catalyst system typically happens 80% quicker than with a traditional catalyst because simply changing the blend ratio presents a lower risk option than a new catalyst or even a new additive. Catalyst Z/M ratio can be optimized to match the specific unit feedstock and operating constraints. In addition to optimizing the blend ratio, the activity levels of the individual components are carefully selected to match the operating mode and feed types. This formulation flexibility can deliver a significant selectivity change, allowing a refiner to accommodate a seasonal operation, manage a swing feedstock or even a hydrotreater outage, and most importantly, GENESIS catalyst systems allow refiners to capture short term economic opportunities.
References
1.Schiller, R., et al, “The GENESIS Catalyst System,” Catalagram® 102, Fall 2007.