Question 86: With more refiners upgrading to packing in the reactor stripper, what has been your experience with reliability? When do you consider removing packing for inspection during turnaround? How much of the packing does one spare?
REYNOLDS (Phillips 66)
At Phillips 66, we have three refineries that have packed strippers. Two of those have not yet run through a full turnaround cycle, so I cannot really comment on their reliability yet. The first refinery to put in the grid packing within P66 did so in 2003. It has gone through two turnaround cycles since then. It has an external stripper and is fairly small in size. In each turnaround, we have pulled out all eight layers of the packing.
In the first run from 2003 to 2007, we ended up replacing the bottom two layers just due to general thinning. There was about a 60% metal loss. There was one caveat to this run: The steam distributor underneath the packing failed during the run; so, most of the time, we ran with poor steam distribution. The adjacent layers moving up from the bottom of the bed had 20 to 30% loss as well, but we deemed them okay and reused them.
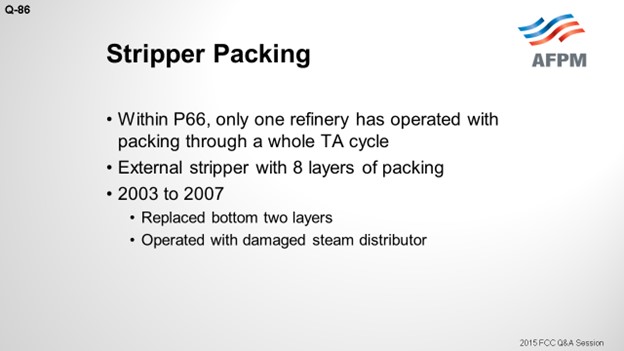
In the next run, from 2007 to 2012, we ended up replacing the bottom six layers. Some of that damage was on two of the layers that had not been replaced on the previous run. We could have reused the two top layers that were replaced; but since we already had them out of the vessel and had new packing sitting right there, we replaced the lower six of eight layers, as well as the support grid underneath the packing. It was knife-edged and had some thinning. Going forward, we plan to keep four layers on hand just for turnarounds.
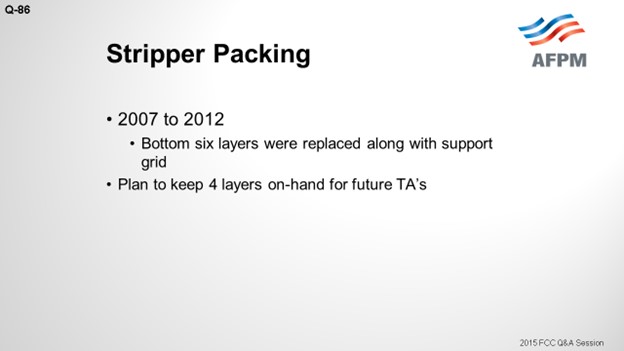
I have included some pictures. The first one is from the first run in 2007. You can see that there are some knife edges and it is worn out. What I like about this picture is that it is from April. The white stuff is not a catalyst. This is snow. [Laughter] You can guess which part of the country this refinery is in.
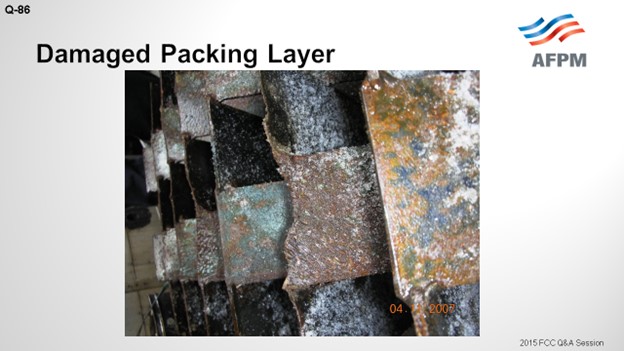
On the next slide, you can see another picture of that damage. There are erosion patterns in this wear. You can that see it is just worn down.
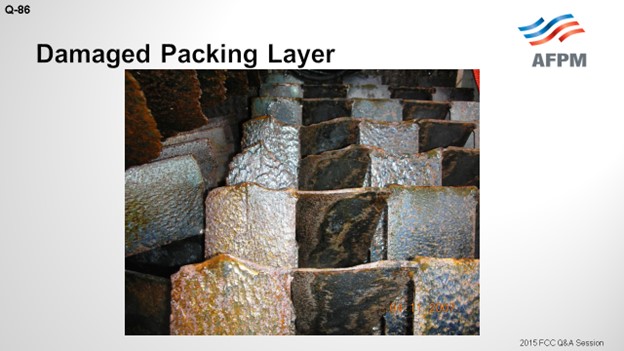
I will say that going into both of these turnarounds, there are no indications of any pour stripping. The stripper runs great. We do not have any plans to make modifications. P66 recommends that you keep the flux rate under 600 pounds per hour per square foot (pph/ft2) of cross-sectional area. We run about 1100 pph/ft2, so we are quite a bit above the guidelines.
The last slide shows the steam ring. It was C-shaped. It failed in two locations. I believe there were bad welds, as dissimilar welds have failed. So, we put a pipe grid-type distributor in there, and it has done fine since then.
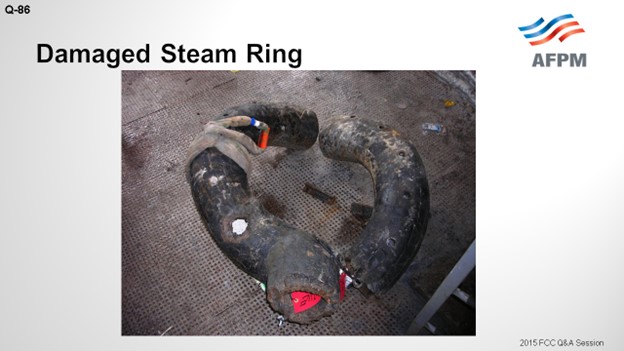
LARSEN [Marathon Petroleum Corporation (MPC)]
In Marathon, we only have one unit with the packed reactor stripper. This stripper was installed in 2010, so we have not been through a turnaround cycle on this unit yet. We have not seen any problems with stripping in it. We are not really planning to pull the packing out of this stripper. We are planning to inspect it from the top and from the bottom. The external IR surveys we do around the stripper do not indicate any refractory problems. So that is our plan.
RAMA RAO MARRI (CB&I Lummus Technology)
Mark, I just have one question for you. The layer is from the top of the first one. Which is the portion of the layer?
REYNOLDS (Phillips 66)
Just the lower one. The one that is damaged is at the bottom. The damage has been worst at the bottom and progressively better going up.
RAMA RAO MARRI (CB&I Lummus Technology)
So, there could be a situation where the starter packing could be damaged from the top also. If the catalyst level is not at the level at the top of the grid, then there could be some impingement of the catalyst coming at high velocity from the cyclone dipleg, which could also impinge and possibly damage the top. So, it is essential to keep the catalyst bed level such that all the grids are immersed in the bed and the packing catalyst is covered.
NIKOLAS LARSEN [Marathon Petroleum Company (MPC)]
MPC only has one FCC with a packed reactor stripper. This unit is in its first cycle following installation; and so far, reliability has been good. We are not planning to remove packing for inspection; we will inspect from the top and bottom. External IR surveys have not indicated any internal refractory problems.
JOSH TREISNER (Monroe Energy, LLC)
We installed packing in our reactor stripper in 2006. So far, the only issue we have seen was in 2012. When we went into the reactor, we had refractory and coke debris from various areas of the reactor that had fallen onto the top of the packing and partially clogged and blocked a portion of the packing. We had already made the decision to remove all of the packing to evaluate whether there was any erosion with the new configuration (there was not), but we would have needed to remove at least the top two layers for cleaning anyway due to the debris.
Once removed, we did not see any noticeable erosion on the packing itself; but in anticipation of possible issues, we had ordered one layer of spare packing prior to the outage. I will caution that the price per layer was twice as high when just ordering one or two layers compared to ordering a complete replacement (eight layers for us) and lead time for even just one layer was in the range of 12 weeks. I would also caution that even though our packing was very robust, some sections still got deformed during handling, although not badly enough to need to be replaced. For our next outage (if we did not already need to remove the packing for another reason), we would have suggested having one layer on hand and simply inspecting from the top and bottom and determining whether cleaning or replacement was needed from there.
The following pictures are of the as-found condition and the packing, and some pictures of it once it had been removed and then cleaned.
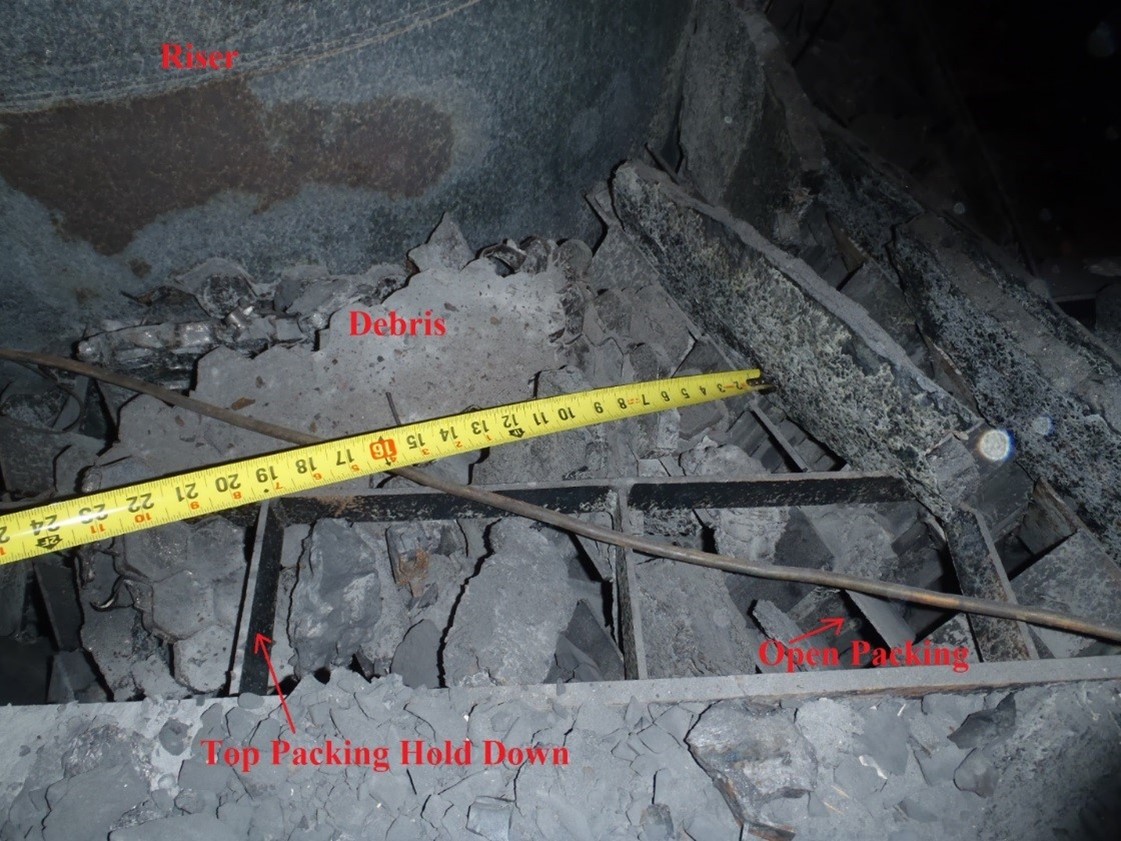
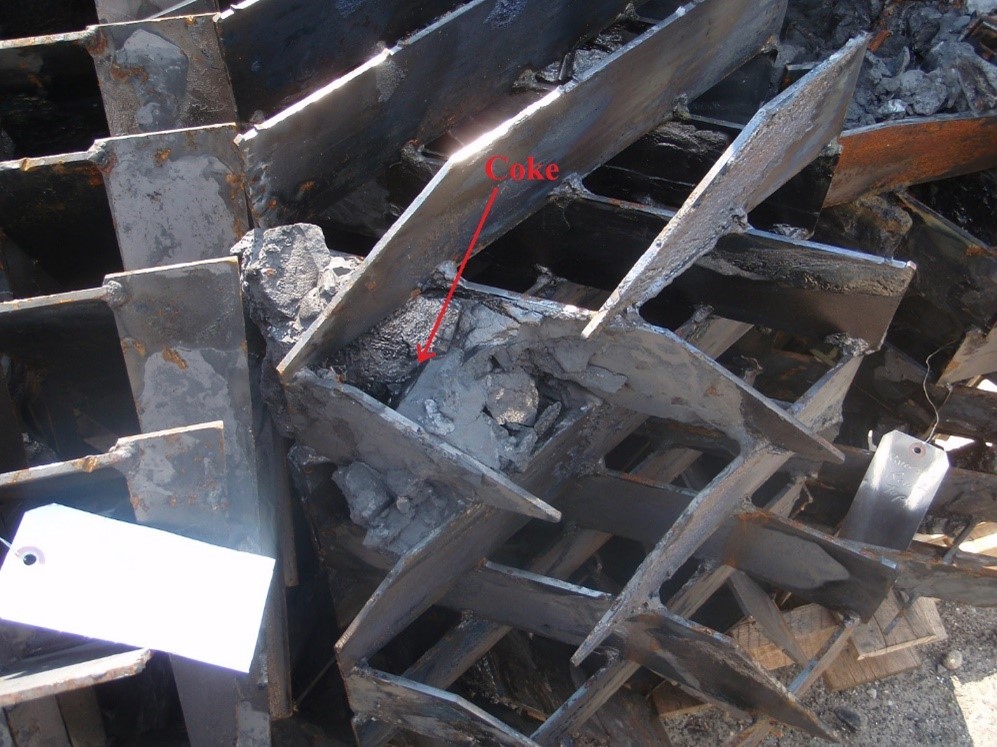
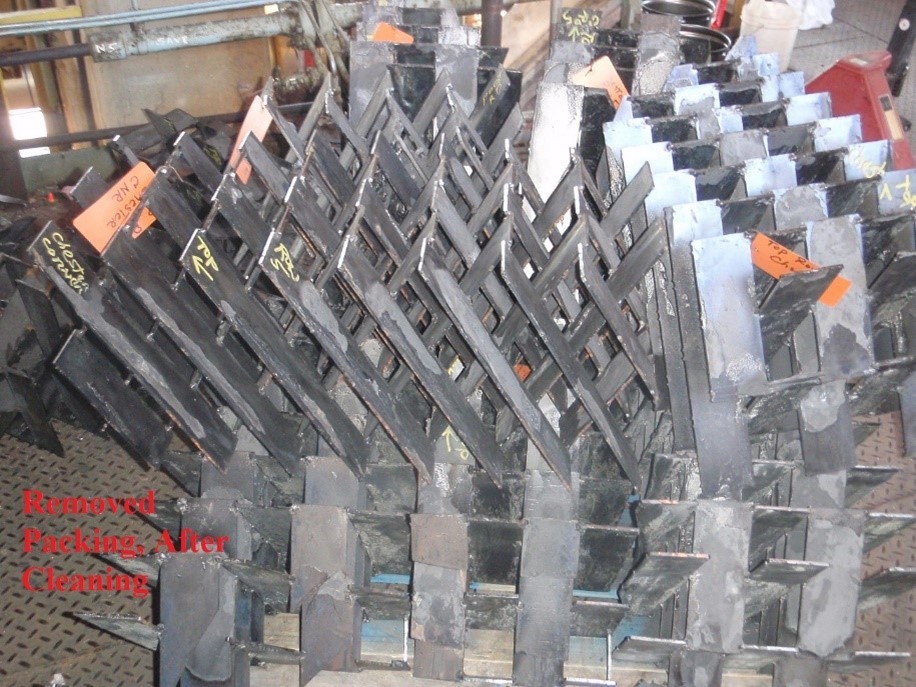