Question 85: What are the advantages and disadvantages of catalyst mesoporosity [100 to 600 ǻngström (Å) diameter pores] in VGO (vacuum gas oil) operations?
KOEBEL (Grace Catalysts Technologies)
When talking about catalyst mesoporosity, we are referring to the matrix contribution, especially the 100 to 600 ǻngström pores found in the catalyst matrix activity. Catalyst matrix activity is really important, particularly in the Type I cracking depicted here, in the mix zone of the riser where the mix zone can be on the order of 1100°F. Even in VGO types of operations, you can have a significant portion of the total feed that may not vaporize at those conditions. Having effective diffusion is important for pre-cracking these types of feeds so that the zeolite can efficiently crack it further later on up the riser. Certainly, even in VGO operations, we think that avoiding diffusion limitations in the mix zone can be tremendously important.
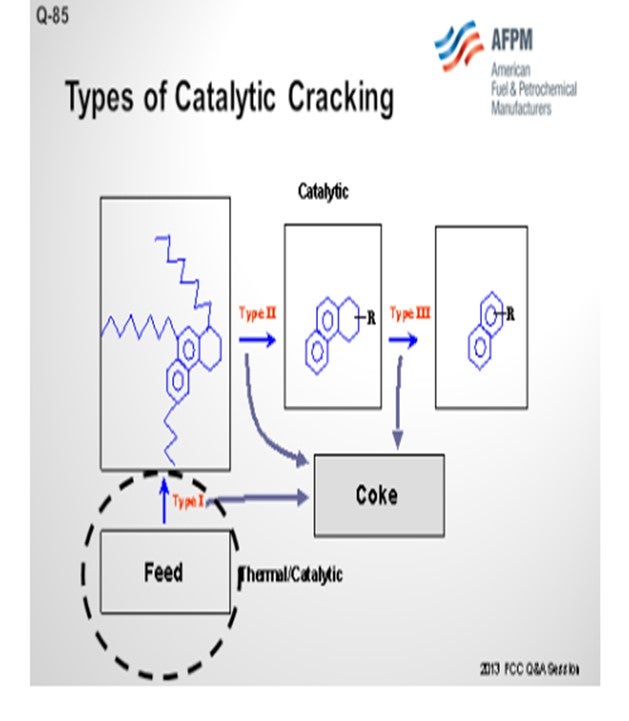
I queried the Grace database on FCC feed. Even in gas oil and VGO operations, the average was that about 10% of the feed boiled over at 1000°F; so clearly this is not just a resid phenomenon. This is a factor in FCC operation that Grace considers to be very important in even the VGO operations.
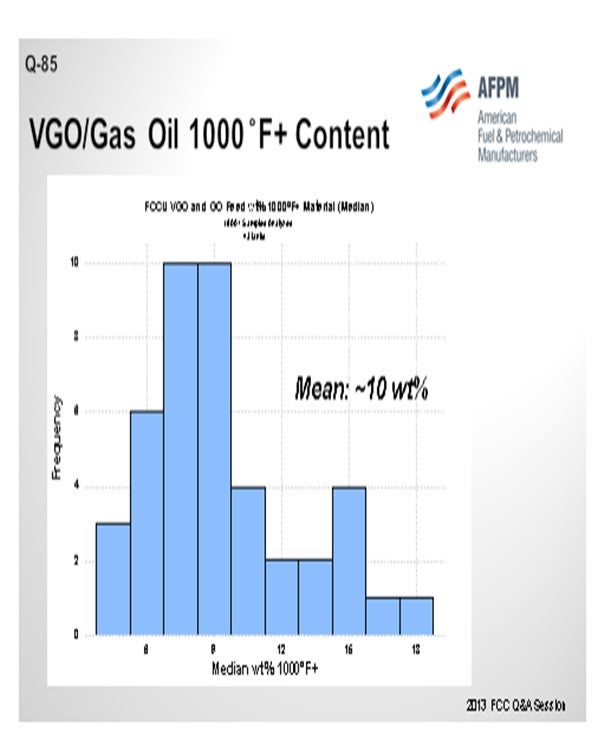
The next slide shows a commercial example of a refinery that was running on a catalyst and implemented 50% of Grace’s MIDAS® catalyst into the blend. MIDAS® is a catalyst for which Grace specifically maximizes the mesoporosity and matrix surface area in the mesopore range. You can see that over a wide range of conversion, the slurry yield was reduced by 2.0% absolute. This is a gas oil operation. Even though this would not be a feed you would consider to be heavy resid, clearly the matrix contribution to the efficiency of the cracking was obvious.
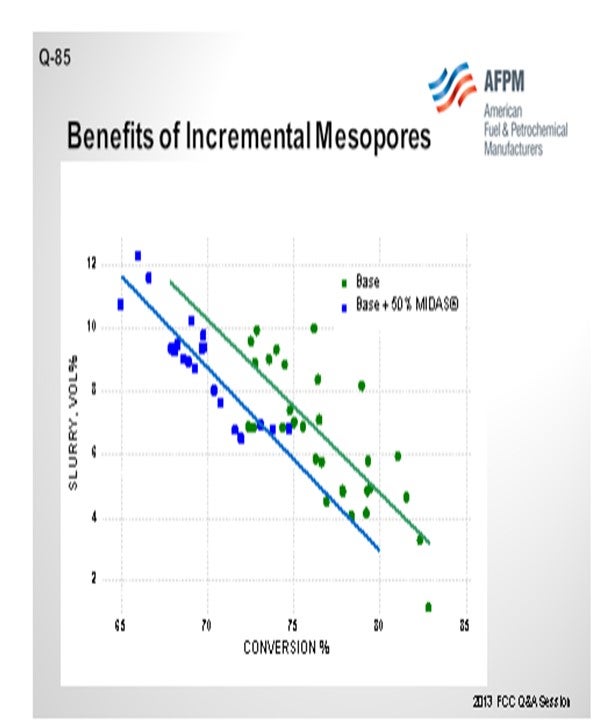
The question also asks about possible disadvantages of mesoporosity. I believe that it might be a disadvantage to have too much mesoporosity in the catalyst when there is a need for high zeolite activity, which is certainly very important, particularly in this Type II cracking where you are going to try and de-alkylate side chains off of naphthenic and aromatic cores. This cracking is very efficiently done by zeolite. If you have a catalyst system that is too biased towards matrix surface area (MSA), you may have a deficit in zeolite activity. So, you certainly want to make sure you have the proper Z/M (zeolite/matrix) ratio on all feeds.
JOE McLEAN (BASF Corporation)
We introduced a catalyst called NaphthaMax® back in about 2000. Really, the only difference between NaphthaMax® and its predecessor-type technologies was that there was a higher porosity version. It has been, by far, our best-selling gas oil catalyst line ever since. We are continuing to refine and introduce newer versions of it. Obviously, I agree with Grace, and certainly with Jeff, that it does make a difference, even in gas oil applications, because it has. We have added over 100 NaphthaMax® users over the past decade or so who could attest to that benefit.
It should not surprise you that we will differ in our opinion a little. I am talking about the zeolite versus the matrix; because with our DMS (dimethyl sulfide) technology, we can put in the mesoporosity. We actually use the external zeolite surface that now gets exposed and available in the larger pores as it functions the way that catalyst is manufactured. So even with the higher porous systems, we are able to get just as high of a zeolite content; and in fact, better zeolite efficiency and activity than what we have with less porous systems generated with the predecessor technologies that we had.
KEN BRUNO (Albemarle Corporation)
Indeed, we agree that mesoporosity is important; but when you talk about diffusion, it extends beyond mesoporosity. In addition to intra-particle diffusion, what is also critical is surface diffusion. To quantify that, Albemarle often talks about the Accessibility Index. Again, mesoporosity is important, but what is more important is the combination of surface and intra-particle diffusion as measured by the Accessibility Index.
PAUL DIDDAMS (Johnson Matthey INTERCAT, Inc.)
Just a quick comment: Do not forget that there are also concentrated additives which contain these kinds of mesoporous cracking sites.
JEFF KOEBEL (Grace Catalysts Technologies)
Effective bottoms cracking involves a three-step bottoms cracking mechanism which was discovered by Zhao1 (Figure 1). The first step is largely dependent on the catalyst matrix and porosity, and that is the effective pre-cracking of large molecules in the feed.2 Since the riser mix zone temperature can be on the order of 1050°F, feed components over 1000°F+ will not readily vaporize. Thus, these molecules need to pre-crack on the catalyst matrix before the catalyst zeolite can further crack them to desired products.
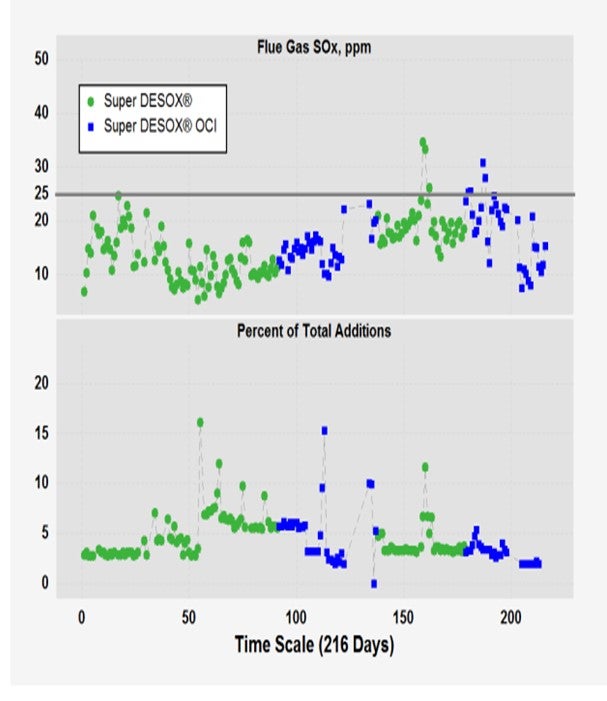
Grace’s FCC feed database contains many examples of units processing VGO and GO that still have a significant portion of the total feed to the unit with a boiling point above 1000°F. In fact, the average 1000°F+ in VGO and GO FCC feed is approximately 10% across our database (Figure 2). Thus, pre-cracking is a real consideration, even in a non-resid operation.
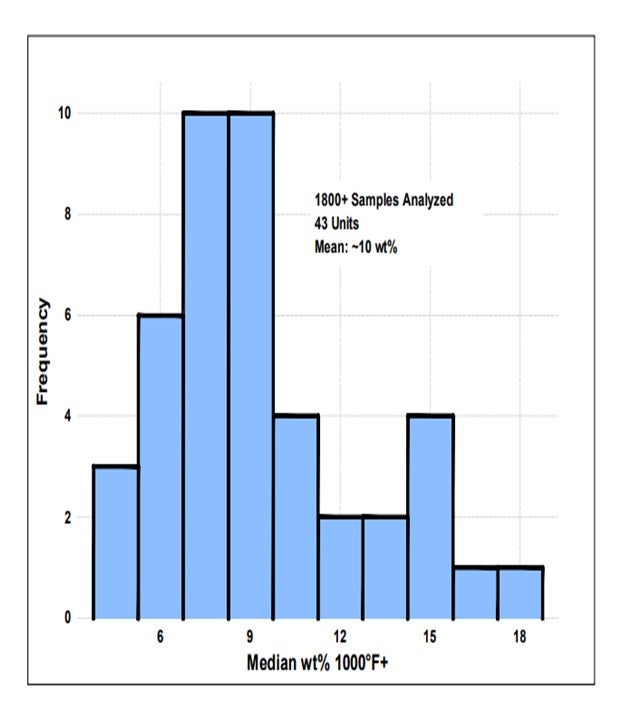
The pore volume of an FCC e-cat (equilibrium catalyst) sample is typically analyzed and reported by each vendor. However, the size distribution of the pores is also a critical component of the effectiveness of the catalyst porosity. Liquid phase diffusion, like one can find in the mix zone of the riser, is typically 2 to 3 orders of magnitude slower than gas phase diffusion, especially if the pores are small (less than 100 Å).4 High mesoporosity in the 100 Å to 600 Å range mentioned in the question is critical for achieving effective pre-cracking of heavy molecules without diffusion limitations. Excess small pores less than 100Å will lead to high coke and gas make, while an abundance of large pores greater than 1000 Å will have ineffective bottoms cracking and perhaps poor attrition characteristics.
Grace’s MIDAS® catalyst family is specifically designed to provide higher matrix surface area (MSA) with an optimal pore size distribution that provides excellent mesoporosity. Grace has many commercial examples of GO and VGO operations that have benefited from the inclusion of some portion of MIDAS® in the fresh catalyst mix. This commercial example shows that inclusion of MIDAS® into a catalyst system for a VGO application improved bottoms conversion by 2% absolute (Figure 3).
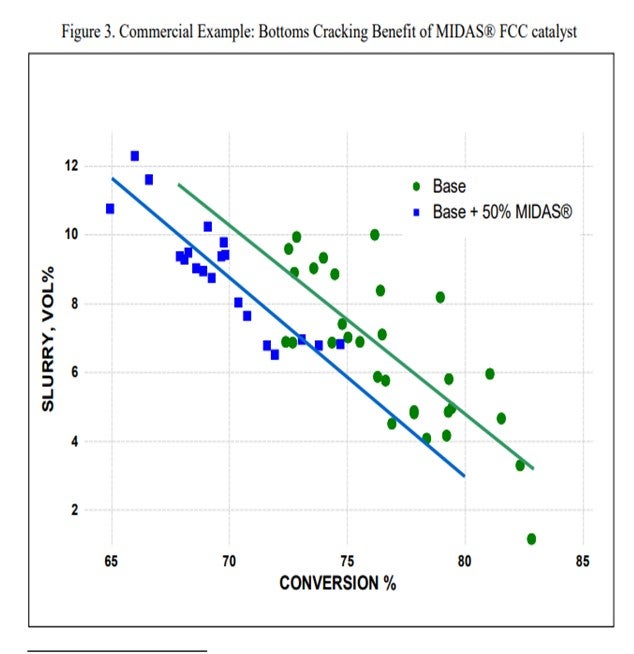
The question also asks about possible disadvantages of mesoporosity. As was mentioned previously, there are multiple steps to effective bottoms cracking. Another step in the conversion of bottoms is dealkylation of side chains from aromatic and naphthenic cores (Figure 1). This is a step that is most efficiently catalyzed by zeolite activity. If a catalyst formulation is too heavily biased towards MSA in an effort to achieve high porosity, it is possible that the formulation may not have adequate ZSA to efficiently drive this type of bottoms conversion. The proper balance between matrix and zeolite is heavily dependent on feed properties and unit yield objectives. Optimization of matrix porosity and zeolite activity is critical to achieve the most effective bottoms cracking, even in light feed applications.
CAREL POUWELS (Albemarle Corporation)
Mesoporosity is typically considered an important feature for enhanced bottoms conversion. This is not only valid for resid applications, but also holds for VGO operations. The effect, however, depends on many aspects, such as the type of VGO, severity of operation, and the base catalyst in use: the more crackable material present in the slurry fraction, the more potential impact by additional mesoporosity. This is particularly valid when the additional mesoporosity is applied within the same catalyst technology. Changing catalyst technology with additional mesoporosity will not necessarily yield the desired effect as the activity, and selectivity of the mesopores between the catalyst technologies can be different. Another aspect that plays a role is catalyst accessibility, which is often confused with catalyst porosity. Poorly designed catalysts can measure high mesoporosity but are not effective as constricted pore openings act as bottlenecks and result in a low accessibility. Thus, it is key to design a catalyst with high mesoporosity and high accessibility.
While mesoporosity (and accessibility) plays an important role in bottoms conversion, it also contributes to the preservation of important primary cracking products such as olefins in the gasoline range. These are important components for high gasoline RON (research octane number) and also precursors for the production of propylene.
Another potential benefit of catalysts with reduced mass transfer limitations in VGO applications becomes evident in units with advanced riser termination devices (RTDs) and short contact times. Under these circumstances, reactants can travel faster to the active sites, and products can egress from the pores before the catalyst is separated from the hydrocarbons in the RTDs, resulting in higher conversion and reduced rate of secondary reactions (everything else constant, compared to a catalyst with inferior pore architecture).
Albemarle offers a wide suite of products for different VGO applications with a varying range in mesoporosity and accessibility, such as AMBER™ for lowest slurry, GO-ULTRA™ for maximum gasoline, ACTION® for superior gasoline octane and alky-feed, and AFX™ for record high propylene.