Question 84: What operating conditions and monitoring equipment have you been practicing avoiding sulfidation corrosion problems in main fractionator bottoms circuits? What guidelines have you established? How does sulfur type contribute to these guidelines?
RUSSEFF (CVR Energy, Inc.)
Currently, we do not have the operators monitor or alter operating conditions for sulfidation and corrosion in the main column bottoms. We took a more traditional approach. We did a good process study throughout both FCC units with the total sulfur because that is what is represented on the McConomy curves, not the sulfur speciation. We also noticed that we were having some naphthenic acid attack in other areas of the refinery, so we also tested for that, just to keep our nose clean since we were doing the Process Study anyway. We discovered that our naphthenic acid in our feed circuit was much lower than 0.5 wt% of sulfur, so we were in good shape.
We did take the traditional approach to metallurgy 9 chrome, some L-grade stainless steel 316 and 317. Additionally, we increased the pipe wall thickness to allow for a larger corrosion allowance and then revamped our inspection practices. As far as operations, monitoring, and altering the operating conditions in the unit, the economics completely favor metaling up and moving on.
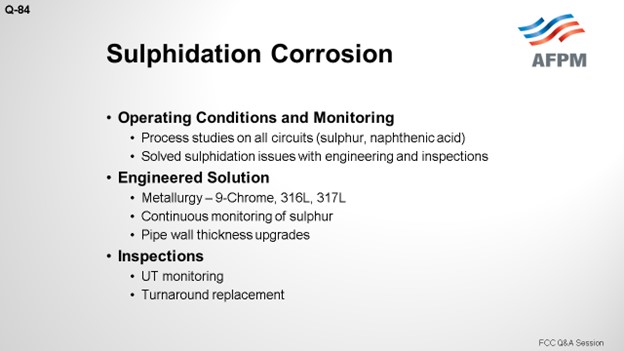
FOSHEE [Shell Global Solutions (U.S.)]
That was a very good response, Rich. Just to add Shell’s perspective, of course, high temperature sulfidation occurs in sour services. Shell has found that H2S and light mercaptans are the active sulfur species in this occurrence. Bottoms temperatures above 530°F tend to cause cracking, which can create vapor pockets with high sulfur concentrations and accelerate the corrosion mechanism. In addition, localized erosion can occur due to solids being present in the slurry. Higher erosion will cause an increase in your corrosion rate.
Carbon steel piping with low silica content is especially vulnerable to high temperature sulfidation. The Chemical Safety Board has defined low silica content as anything less than
0.1 wt% in carbon steel. But alloys, such as 5 chrome and 9 chrome, can be susceptible to high temperature sulfidation as well, just to a lesser extent than carbon steel.
One of the safeguards that Shell implements is to change carbon steel piping to an alloy piping when that section of pipe is due to be replaced. Shell also does positive material identification on new piping to verify metallurgy. And then, frequent, non-obstructive testing and inspection is essential, especially in carbon steel piping, to catch any areas with corrosion concerns.
LARSEN [Marathon Petroleum Corporation (MPC)]
Like these guys, Marathon considers three different buckets of sulfidation: in liquid streams, H2S vapor streams only, and then streams with erosion/corrosion as well. So in general, I think we look at a conservative value for sulfur rather than trying to speciate the specific sulfur species to trigger further assessment. As an example, for piping that is carbon steel up to 5 chrome, anything over 450°F will trigger further assessment/inspection. And then for 5 chrome and higher, it is a sliding scale with temperature and sulfur.
The H2S vapor systems where we have seen higher than predicted corrosion, I think, are carbon steel through 9 chrome. Anything above 500°F will trigger further assessment on those. And then, we rely on our catalyst monitoring, like we mentioned during the last discussion, and looking at the particle size distributions and loss rates to make sure we do not have erosion/corrosion phenomena in the sulfidation streams of that nature, such as slurry.
ADRIAN SKIPPER (Phillips 66)
Since Todd from Shell was the only one who mentioned H2S and light mercaptan concerns, I would like to know if you have specific levels where you get concerned or, like the McConomy curves, you use different sulfur levels Or, do you just go on a baseline and then look for changes upward? How do you approach that?
FOSHEE [Shell Global Solutions (U.S.)]
I do not have any Shell information on specific sulfur levels that I can share at this time.
LARSEN [Marathon Petroleum Corporation (MPC)]
In Marathon, I think we use API 939. I am looking at my notes. This will be in the Answer Book. We use 939-C B-13 curves for corrosion rate estimates for equivalent H2S content.
NIKOLAS LARSEN [Marathon Petroleum Company (MPC)]
There are two forms of sulfidation corrosion found within the FCCU and the gas condenser. Sulfidation is typically a general form of corrosion, though hotter (greater than 550°F) carbon steel can be corroded locally due to flow induced damage and other mechanisms.
Sulfidation in Liquid Streams: The hot portions of the FCCU upstream of the riser, the main fractionator pumparound, and bottoms systems are subject to sulfidation from organic sulfur and residual H2S constituents in the streams. Above 450°F, the S species can corrode carbon steel at rates that can be estimated by the Modified McConomy curves. The S content of the particular stream (feed, pumparound, bottoms, etc.) should be used in these evaluations and can be obtained via sampling or modeling. Cracked stock S content in the main fractionator is difficult to predict and typically must be measured to determine corrosivity. It should be noted that S content alone may not be solely indicative of corrosivity as different feeds may have different kinds of S that contribute to corrosion. In general, MPC utilizes total S at conservative levels in lieu of knowing S types to trigger further assessment. We target CS (carbon steel) up to 5 Cr equipment for increased inspection at temperatures greater than 450°F at any sulfur level. For 5 Cr components, we use a sliding scale to trigger increased inspection, as operating temperature increases the sulfur level decreases to initiate further assessment.
H2S Vapor Sulfidation: There can be sections in the FCCU and gas con that operate in all vapor conditions with operating temperatures greater than 500°F that may corrode at higher rates than those predicted by the Modified McConomy curves. Without the benefit of a liquid protecting the surface, the direct sulfidation by the light S species or H2S in the vapor can cause higher than expected sulfidic corrosion. Examples include:
-
The reactor vapor space internals such as CS cyclones, particularly if operating above 950°F,
-
The upper vapor section and vapor return piping of sidestream strippers with reboiled stripping, and
-
The shell-side reboiler vapor space of the stripper and debutanizer towers.
Estimates of equivalent H2S content and use of API 939C B13 curves can be used for corrosion rate estimates. MPC targets CS through 9 Cr equipment operating at temperatures higher than 500°F for increased assessment where H2S vapor sulfidation could be present.
It is interesting to note that the hot vapor transported from the reactor to the main fractionator, though operating higher than 900°F, has typically not been subject to high rates of sulfidic corrosion despite a significant H2S content. Typically, this piping is constructed of 1¼ to 5 Cr for high temperature strength purposes, but it appears that the amount of coking in the line protects it from high rates of sulfidic corrosion.
Sulfidation Erosion/Corrosion: Catalyst fines are entrained with reactor vapor and end up in the main fractionator bottoms stream. If the solids levels reach high levels due to problems with reactor cyclone performance, this can contribute to erosion of the sulfide scales protecting the piping and pumps of this circuit and lead to accelerating local erosion/corrosion. Regular monitoring of the solids in the fractionator bottoms is typically undertaken to monitor. Increased slurry solids levels will trigger additional assessment in these circuits, as well as any slurry circuit components that are CS and operating above a 0.5% sulfur level.