Question 82: What are typical and maximum targets for FCC unit main fractionator bottoms and wet gas scrubber water for weight percent solids? Also, what are typical for pounds per barrel (ppb) of catalyst losses to each and particle size distributions?
FOSHEE [Shell Global Solutions (U.S.)]
Typical total catalyst losses from both the reactor and regenerator side are somewhere around 0.05 to 0.1 pounds per barrel. A good assumption is that you have about a 50/50 split between your losses. From a maximum loss standpoint, you are looking at anywhere from 0.10 to 0.15 pounds per barrel for both the reactor and the regenerator.
On the reactor side for the slurry system: Slurry solids concentration can vary quite widely and be anywhere from 0.03 to 0.30 wt% under normal operation. Typically, your maximum solids concentration is somewhere around 0.5 wt% due to erosion concerns in the slurry loop piping. On the regenerator side, your wet gas scrubber solids concentration can vary depending on your water purge rate, but a typical maximum solids concentration in your water circulation is somewhere around 0.5 wt%, again due to erosion concerns.
Particle size distribution can depend on several factors including cyclone design and fresh catalyst particle size distribution. But in general, the average particle size of your losses is somewhere around 15 to 30 microns from the reactor, as well as from the regenerator, unless you have a third-stage separator and a fourth-stage separator. In that case, the average particle size for regenerator side losses will be less than 10 microns.
It is also important to have a baseline of the normal catalyst losses for your unit. This includes the solids concentration in your slurry and in your flue gas, as well as your solids’ average particle size and distribution. This baseline will help you troubleshoot catalyst loss issues later on down the line.
REYNOLDS (Phillips 66)
We generally use 0.5 wt% as an operating limit for both the slurry and the scrubber water, primarily for erosion concerns. As Todd mentioned, I would expect the losses – for both sides combined – to be less than 50 pounds per 1000 barrels, which I believe is the same as 0.05 per barrel. In the slurry fines, I would expect that the PSD profile to be bimodal and peak at 1 to 3 microns with the second peak at about 13 or 15 microns.
LARSEN [Marathon Petroleum Corporation (MPC)]
I published all of the Marathon data in the Answer Book that will be included in the final transcript. Our targets are similar to what Todd and Mark said. We do one test differently. We have often found that our laboratories do not particularly love doing ash tests. So, we will do a BS&W (base sediment and water) test on our slurry. If it is less than 1 or over 1%, then we will send it for ash analysis to verify what portion of that is actually catalyst. So that is one test we use to help the lab a little.
Our scrubber limit is 5,000 ppm TSS (total suspended solids). Our average particle sizes are in line with the other folks. I would say that across the board, our losses are 0.02 ppb of feed on the reactor side and maybe 0.07 ppb of feed on the regen side, when averaging out all of our eight FCC units.
LUIS BOUGRAT (UOP LLC, A Honeywell Company)
I agree with everyone’s comments. I just want to mention that units processing heavy feeds tend to have slightly higher additions because of the metals. So, you do see, maybe, a little closer to 0.1 pounds per barrel on the losses overall. With regard to particle size distribution, it is important not only to look at the average size but also to make sure that you have only one peak. Two peaks are usually a sign of something abnormal within the system, whether it corresponds to losses leading to a second peak or something present in the system, such as a bypass or leak.
CHRIS STEVES (Norton Engineering)
FCC wet scrubbers, available from several vendors, are designed to operate with slurry catalyst concentrations ranging from 0.25 to less than 5 wt% solids and normally operate at less than 0.5 wt%. Norton Engineering’s VSS units operate at greater than 1%, are designed to run at 5%, and can operate at greater than 20 wt% for short periods of time. The ability to operate an FCC scrubber with high slurry solids loading reduces makeup water requirements and the volume of purge water sent to the scrubber’s purge treatment unit. In some cases, the purge volumes may be low enough to allow direct purge water treatment in existing wastewater treatment facilities saving significant capital and operating costs. Reliable long-term operation at high slurry catalyst concentrations is made possible by proper materials selection for the slurry circuit. Critical components, such as the main circulation pumps and liquid atomization/spray nozzles, are manufactured from high quality, erosion-resistant materials by companies specializing in abrasive slurry equipment supply.
There are many variables affecting the total amount of catalyst lost in the reactor and regenerator including: catalyst type; primary, secondary and tertiary separation systems design and operation; the design, operation and condition of the regenerator air grid; the type of regenerator (dilute phase, dense phase, high efficiency, etc.); the design, operation and condition of the riser termination device, etc. Each operating, design, and condition variable contributes something to the amount of catalyst abrasion occurring in a particular FCC and the effectiveness of catalyst recovery in the reactor and regenerator, as well as in downstream flue gas cleaning equipment. That being said, Norton Engineering has gathered a significant amount of data on FCC regenerator catalyst emissions over the years. While we do not share the specifics of this data with the public, we can provide some general estimates for losses from FCC regenerators:
Regen Type / Flue Gas Clean-up Equipment
|
Flue Gas Solids Loading mg/Nm3
|
Weighted Average Particle Size micron
|
Full-burn, Primary, Secondary, and Tertiary |
150 – 300 |
~2.0
|
Full-burn, Primary, and Secondary |
300 – 600 |
~2.5
|
Partial-burn, Primary, Secondary, and Tertiary |
100 – 250 |
~2.0
|
Partial-burn, Primary, and Secondary |
200 – 500 |
~2.5
|
NIKOLAS LARSEN [Marathon Petroleum Company (MPC)]
For slurry, MPC tests for BS&W with a high limit of 1%. Results exceeding this specification are tested for ash to determine actual catalyst content. Units where slurry is sold for use in the carbon black market often utilize a settling agent to help meet solids specifications. For units where slurry is routed to an ebullated bed unit, we have filtration in place. For scrubber purge, MPC uses a mix of cone samples and TSS testing. Our limit on TSS is 5000 ppm. Below are catalyst loss and APS summaries for MPC’s FCC units
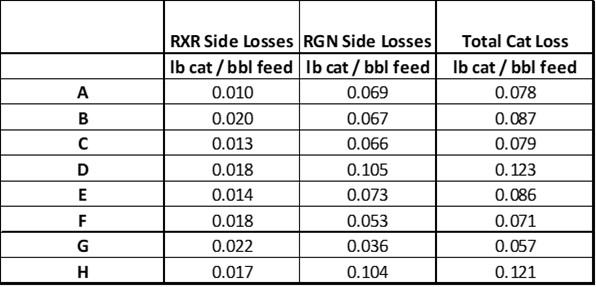
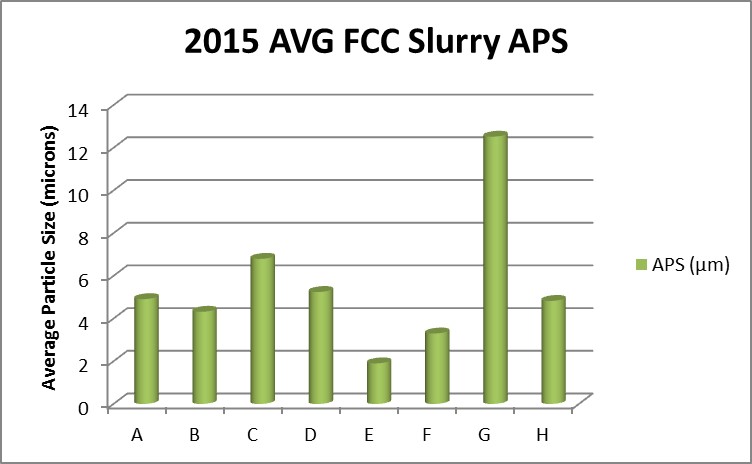
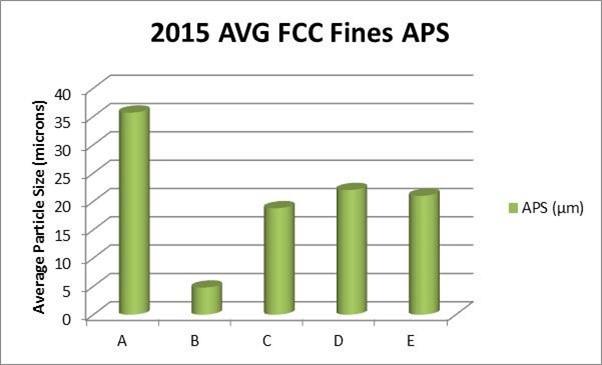
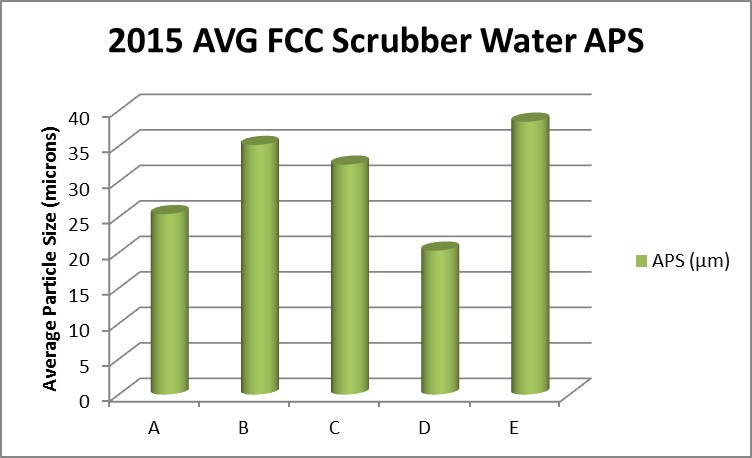