Question 82: Immediately after startup of the FCCU, we experienced a hot spot in the regenerator dome and flue gas system. Do you know of any "on the run" acceptable mitigations? Should steam and/or water sprays be applied to the impacted area? Are there reliable analytical techniques to determine if and when the unit should be shutdown for repairs?
Steve Shimoda (SHAW)
Hot Spots are an unfortunate but common problem in cold walled FCC converter vessels and transfer lines. Hot Spots which are not treated can lead to several undesirable effects to the steel envelope. Most refiners typically mitigate these effects by applying steam to the localized hot area. However, in more pervasive and/or problematic areas, a water mist or blanket are also used to allow refiners to safely reduce the effects of higher heat to the steel and make it to their next scheduled shutdown where a planned permanent engineered repair can be applied. Safety needs to be considered when using steam or water based on the environmental conditions and how it may impact site conditions. For example, use of a water mist will have different consequences in a gulf coast summer versus a Canadian winter.
The life cycle of the steel is affected by the hot spots as a function of time and temperature. Generally, CS life cycle is 100,000 hours at 850 °F (455 °C). However, as the temperature increases life cycle is reduced; meaning for example, CS life cycle is 1,000 hours at 1072 °F (578 °C), as shown in graph below. Refiners apply steam / water to reduce temperatures and extend life cycle. As the Licensor, we concur with this type of short-term solution to problematic areas; provided the areas are continuously monitored by regular thermal scanning effected area and kept cool. Also, Shaw recommends ultrasonic testing (UT) suspect areas for loss of skin thickness. A long-term solution is required.
Ken Fewel of Shaw presented results of a hot spot study at the 2010 Cat Cracker Seminar. He demonstrated the use of Finite Element Analysis (FEA) to evaluate the potential danger of the stresses put on the system as a result of a hot spot. In comparing the results of FEA to actual field measurements, it was determined that the calculated movement was accurate. One could then compare the calculated stresses to a risk chart to determine if the unit should be shut downfor repairs or could operate with temperature mitigation until a scheduled shutdown.
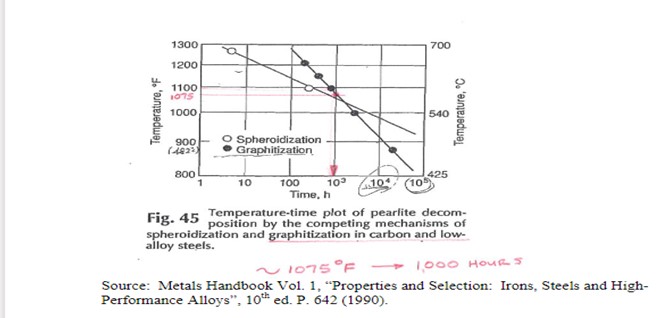
Emerson Domingo (Sunoco)
If the shell temperature exceeds 650F, the hot spot can be mitigated using a variety of external cooling methods:
•If the hot spot is small and temperatures not too extreme, air lances can be an effective way to keep the shell below 650F.
•If the temperature continues to exceed 650F with air lances or the hot spot is too large (such that the needed volume of air is not practical), then steam lances or steam rings can be the next option. Steam has the advantage of providing a larger volume of cooling media but has the disadvantage of producing more noise and a “steam cloud” around the hot spot making personnel access and ongoing surveillance more difficult.
•If steam cooling is not effective at cooling the metal below 650F (which can be the case for very large hot spots or very hot process temperature) or if the noise and other problems with using large volumes of steam cannot be tolerated, then other alternatives are considered. An array of small steam nozzles used in conjunction with fine water spray mist can be a very effective cooling method. This “steam/water mist system” can be sized and shaped to cover the irregular area of the hot spot and expanded as needed if the size or shape grows over time. This method is very effective cooling with much less steam use and much less noise and temperature extremes in the area of the hot spot. The disadvantage of this method is the time it takes to fabricate the assembly (with high man hours and labor cost) and also the steam/vapor plume that is created due to the vaporizing water spray on the hot spot. Visual surveillance of the hot spot can be difficult with this cooling method. However, since the water mist sprays produce minimal excess water to drip off of the equipment this method does minimize the housekeeping and other issues associated with water deluge cooling (discussed next).
•If the “steam/water mist system” is not effective, or the steam plume cannot be tolerated, then water deluge cooling is used as the next option. Water deluge is extremely effective at controlling metal temperature and also produces a minimal steam plume (due to large amounts of excess water that is used). The disadvantage of this method is the potential for thermal fatigue and potential housekeeping problems that may be created. Once the water is turned on, it should be left flowing constantly such that all of the affected surfaces are continually wetted. Having insufficient deluge will lead to surfaces being alternately wet and then dry – which will result in localized metal temperature thermal cycling and eventual thermal fatigue cracking and failure of the metal.
•As a last resort (if none of the above cooling methods are effective or the disadvantages cannot be tolerated) an engineered “enclosure box” over the hot spot and either pump the box with insulating refractory or inject cooling steam inside of the box. Once the box is installed there is no way to monitor the base metal temperature and it is likely the material will run excessively hot and need replacement during the next unit outage. Also, if the hot spot grows larger and expands outside of the box then there are complexities associated with installing adjacent “box extensions” or other means to manage the problem.
Determining when the unit must be shut down for repairs depends upon the effectiveness of the external cooling along with ongoing surveillance and monitoring of the equipment. This process includes:
•Periodic infrared thermal scans or contact thermocouple measurements to verify the metal temperature is below 650F and the hot spot is not growing beyond the limits of the external cooling system. These scans may be performed daily at first, but once steady operation is verified the frequency can be reduced to weekly or monthly, depending upon the situation. Frequent unit operator visual surveillance (multiple times per shift) is also an important part of the monitoring to observe for changes to the situation. As long as the metal temperatures are maintained below 650F then metallurgical degradation (or metal creep, stress overload, etc.) is minimized.
•In addition to monitoring temperature there are periodic thickness measurements that are taken – to monitor for internal erosion or corrosion (metal oxidation) in the area where the internal refractory has failed. This can be accomplished using high-temperature ultrasonic thickness transducers, although high temperature thickness measurements can have a wide range of error (+/- 10%). An alternative is to use a small water hose to temporarily cool the locations where the measurements will be taken. This provides much more accurate thickness data for trending purposes. Thickness measurements are initially taken on a daily basis, but once a stable trend is established these can be reduced to weekly, monthly, or quarterly depending upon the situation.
•Based upon the monitoring data, fitness-for service assessments per the API-579 methodology can be performed. In some situations, this has included Finite Element Analysis (FEA) modeling to determine potential structural collapse and pressure boundary breach due to high temperature and/or localized metal thinning to determine the need to shut down and determine repair timing.