Question 81: How do CO (carbon monoxide) and NOx (nitrogen oxide) emissions change when you operate at low regenerator temperatures? What can be done to mitigate any increases?
BULL (Valero Energy Corporation)
I will initially address this question from a CO standpoint and then discuss the NOx. CO emissions typically increase if the regenerator falls below a certain temperature threshold. That temperature threshold will vary based on your regenerator configuration and definitely on the type of air distribution. In general, well-mixed regenerators with longer residence times can be run at significantly lower temperatures before CO emissions increase, compared to a poorly mixed regenerator with lower residence time.
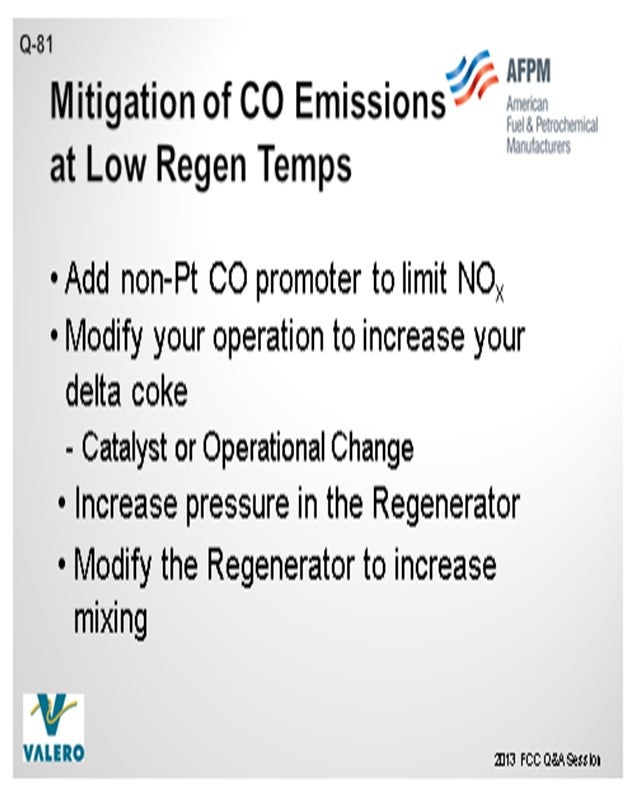
In the absence of a CO combustion promoter, large variations in the CO2 (carbon dioxide)-to-CO ratios are observed. At the catalyst surface, it is believed that that CO2-to-CO ratio is an intrinsic function of the temperature at the burning site. However, the CO exiting the burning site may be further oxidized to CO2 at a rate dependent on the temperature, amount of CO and O2, water partial pressure, and active metals on the catalyst.
To mitigate CO emissions at low regenerator temperature, we add a non-platinum CO promoter to limit the NOx. Other solutions include increasing 1) your delta coke, 2) the pressure in the regenerator, or 3) the mixing by modifying the regenerator. The amount of NOx emitted from the regenerator is highly dependent upon several variables such as operation regenerator style, excess O2, promoter concentration co-distribution, feed nitrogen, and dense bed temperatures. So, there are many variables that determine the overall NOx equation. NOx formation chemistry inside the regenerator is difficult to pin down. Studies have shown that about half of the feed nitrogen becomes coke on the catalyst, but only a small portion of that actually becomes NOx. It is also believed that NOx emissions are limited by the reaction of CO plus NO (nitric oxide) to form N2 (nitrogen gas) and CO2. Thus, when you have platinum CO promoters added to the unit, CO is converted to CO2 so quickly that there is less CO available for that reaction to occur.
We do have an experience of the regenerator being in true countercurrent flow. With platinum promoter in the unit, it is able to run NOx levels that are very low; but, I will say that is a rarity. In our system, if there is normally a platinum promoter, then you will see elevated NOx levels. In partial-burn operation, there is always CO available to react with the NOx; so emissions are lower. Good coke and air distribution is important to ensure that the concentration of CO, O2, and NOx are evenly distributed throughout the regenerator. The results have been better and more efficient control of the burn zone so that oxygen is used more efficiently and the regenerator can be operated at lower levels of excess oxygen to completely burn the coke to CO2. Generally, you do not need to use platinum promoter. Finally, uniform residence time distribution minimizes the duration that spent catalyst remains the regenerator.
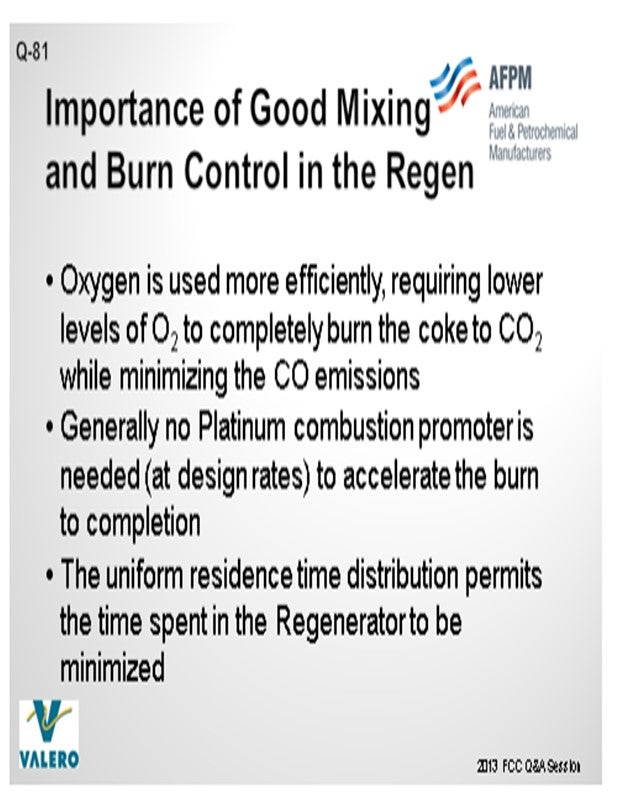
Due to the interaction between CO, NOx, and the FCC regenerator, I recommend that you actually conduct testing to determine the tipping point where you start going up in CO emissions because there are benefits from lowering the oxygen at that time. Running O2 in excess slightly above that tipping point provides a good NOx baseline of your minimum level on the unit. If that level is still too high, then you have other options which include LoTOx™, WGS+™, CONOx™, and SCR (selective catalytic reduction). We have all of these applications across our system. We have very little experience with NOx reduction additives.
GIM (Technip Stone & Webster)
The low regen temperature used to be beneficial. However, with the advent of tight oil and light feed stock, actually too much of a good thing is now bad. So let us first consider what causes some of these low regen temperature phenomena.
The first cause is a result of better feed stock qualities, such as lower Conradson carbon, lower nitrogen, and metals. Second, lower operating severities, such as lower reactor outlet temperature and lower catalyst activity, will reduce regenerator temperatures. The third cause is catalyst regeneration, including full- versus partial-burn, CO promoters (platinum-based or non-platinum-based), and supplemental oxygen that has been turned off.
Jeff described many of these aspects, but I thought it would be worthwhile to summarize all of the factors into three main categories. One is, obviously, the combustion kinetics. Second is the hardware of the actual generator design; and third, to a certain aspect, are the feed contaminants such as feed nitrogen. In terms of combustion kinetics, a lot of these items have been discussed multiple times in past panels, so I will just go over the basics and summarize them. The lower regenerator temperature increases the CO but decreases the NOx or NO2; the promoter lowers the CO. But in terms of the distinction between a platinum and non-platinum base, the promoters can be either increased NO2 or NO2 neutral. The higher O2 concentration lowers the CO and increases the NOx. Again, these are some of the factors that you can use to counteract the formation of CO and NO2.
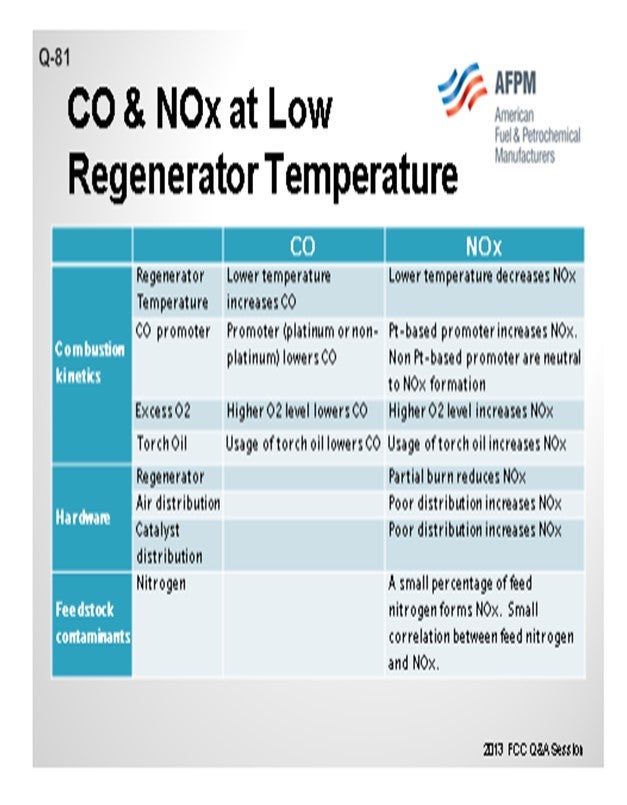
BART de GRAAF (Johnson Matthey INTERCAT, Inc.)
All of the speakers mentioned that the low temperature does affect the CO oxidation and the formation of NOx. The nitrogen kinetics in the regenerator are not affected by the lower temperature. Nitrogen in coke can be converted into nitrogen in NOx, hydrocyanide, and ammonia. As was suggested, non-platinum combustion promoter can be used to steer the oxidation reactions from HCN and NH3 towards N2 instead of NOx. Partial-burn operation is one example where you can see that the CO concentration does affect high NOx. But at the same time, in a partial-burn operation, after the CO boiler, you frequently see a higher NOx level than you would have in a full-burn operation because of the high temperature oxidation in CO boiler.
KEN BRUNO (Albemarle Corporation)
I want to point out that Albemarle has a detailed answer in the Answer Book. But in summary, Albemarle’s non-platinum promoter, ElimiNOx™, provides high CO promotion, excellent afterburn, and minimal impact on NOx emissions.
ROBERT “BOB” LUDOLPH [Shell Global Solutions (US) Inc.]
If you are an oxygen enrichment operator or considering oxygen enrichment, this is your opportunity to raise your bed temperature at the same coke burning rate and shift the CO and NOx distribution within the bed. In turn, the control of NOx and CO emissions could improve.
MICHAEL WARDINSKY (Phillips 66)
We have done a lot of modeling around NOx and CO emissions for additive use. We have seen NOx emissions decrease with higher regen temperatures in almost all of the modeling cases. From our experience, we also know that the non-platinum promoters can increase NOx emission, although not as severely as a platinum-based promoter. We have moved partial-burn units from deep partial-burn to full-burn and observed the NOx emissions decrease substantially. I think it was from the gentleman from INTERCAT who mentioned that in partial-burn, you are releasing ammonia and HCN (hydrogen cyanide) off the regenerator in greater quantities than during full-burn operations. However, these reduced nitrogen species are combusted across the CO boiler to NOx, so your partial-burn units always appear to emit higher NOx emissions than operating in full-burn, even after accounting for thermal NOx generated in the CO boiler.
JEFFREY BULL (Valero Energy Corporation)
CO emissions will increase if the regenerator falls below a certain temperature threshold. That temperature threshold varies based on the regenerator configuration and the type of air distribution. In general, well mixed regenerators with longer residence times can be run at significantly lower temperatures before CO emissions increase compared to a poorly mixed regenerator with lower residence times. In the absence of a CO combustor promoter, large variations in CO2/CO ratios are observed. At the catalyst surface, it is believed that the ratio of CO2/CO is an intrinsic function of the temperature at the burning site (“Arthur's ratio”). However, the CO exiting the burning site may be further oxidized to CO2 at a rate dependent on temperature; CO, O2, and H2O partial pressures; active metals on the catalyst; carbon/oxygen distributions within the fluidized bed; and even the catalyst presence.
To mitigate CO emissions at low regenerator temperatures you can:
• Add non-Pt (platinum) CO promoter to limit NOx,
• Modify your operation to increase your delta coke (catalyst or operational changes),
• Increase pressure in the regenerator, and/or
• Modify the regenerator to increase mixing.
The amount of NOx emitted from the regenerator is highly dependent upon several variables such as mode of operation, regenerator style, excess O2, promoter concentration, coke distribution, feed N2, and dense bed temperature. Studies have shown that about half of the feed N2 goes to coke on catalyst, but only a small portion of the N2 in coke goes to NOx. It is believed that the NOx emission is limited by the reaction of CO + NO to form N2 and CO2. Thus, when Pt CO promoter is added to a unit, CO is converted to CO2 so quickly that there is less CO available to react with the NOx; so NOx emissions increase. We do have experience with a regenerator that is in true countercurrent flow, and the operator is able to run at low NOx levels with platinum promoter in the unit. In a partial-burn operation, there is always CO available to react with the NOx formed; so, emissions are lower. Good coke and air distribution are important so that concentrations of CO, O2, and NOx are evenly distributed throughout the regenerator.
The results of the better, more efficient control of the burn zone in a regenerator are that:
• Oxygen is used more efficiently so that lower levels of excess oxygen are required to completely burn the coke to CO2 while minimizing CO emissions.
• Generally, no Pt combustion promoter is needed (at design rates) to accelerate the burn to completion.
• The uniform residence time distribution permits the time spent in the regenerator to be minimized.
Due to the interaction between CO and NOx in an FCC regenerator, testing should be conducted for your individual regenerator to determine the “tipping point” where a reduction in excess O2 causes CO emissions to increase dramatically. Running at an excess O2 slightly higher than the “tipping point” provides a baseline NOx that you can expect for your unit. If this level is too high, then you will either need to modify your regenerator for better mixing or use an alternate method of NOx reduction like LoTOx™, WGS+™, CONOx™, or an SCR. We have four LoTOx™ applications, one WGS+, one CONOx™, and one SCR in our system. In some cases, a catalyst additive can reduce NOx, but we have limited experience with this application.
STEVE GIM (Technip Stone & Webster)
Why lower regenerator temperatures? Let us first examine some of the factors leading to lower regenerator temperatures: first, better feedstock qualities (such as lower Conradson carbon), lower nitrogen, and metals. Second, lower operating severities, such as lower reactor outlet temperature and lower catalyst activity, will lower regenerator temperatures. Third, catalyst regeneration, including full versus partial-burn, CO promoters (platinum-based or non-platinum-based), and supplemental oxygen turned off are additional options.
Factors Directly Affecting CO and NOx: Many of these directly affect the formation of both CO and NOx in the regenerator. Some of these factors influence the formation of these two species in opposite direction. I have summarized these factors into three categories and their directional changes of the CO and NOx. Many of these items are obvious and have been extensively discussed in the past panels, but I thought it would be a good summary.
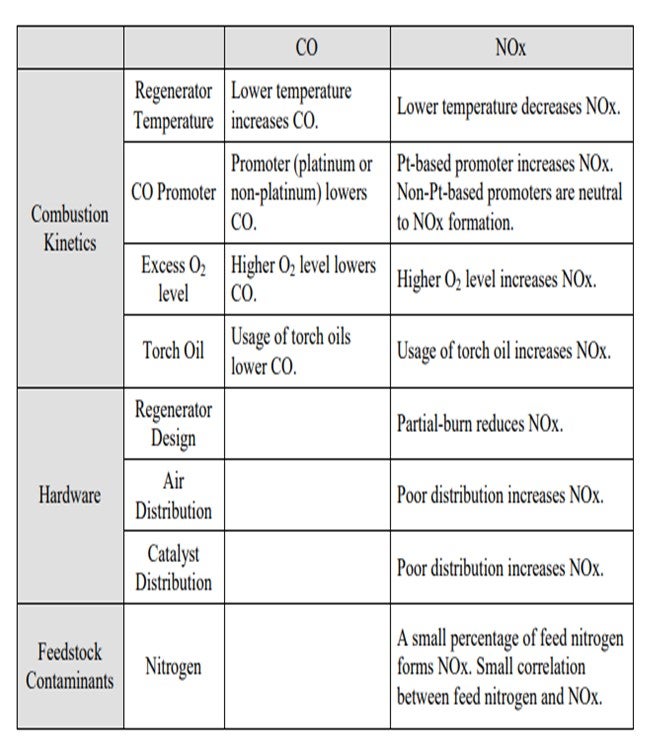
Interactions Between CO and NOx: Reductant-like CO converts NOx to elemental nitrogen in the presence of O2. Lower regenerator temperature can be the direct result of higher CO to CO2 ratio in partial-burn units, which in turn will lower the NOx.
CHRIS STEVES (Norton Engineering)
The impact of low regenerator temperature on CO and NOx emissions can be very unit-specific, depending especially on regenerator design and the distribution of air and coke in the regenerator. In full-burn units, operation at low regenerator temperature will generally result in higher CO emissions and lower NOx emissions. The use of CO promoter can help in reducing CO formation, but use of platinum-based promoters is well documented as increasing NOx emissions. Non-Pt-based promoters are widely used today to allow for control of CO (and afterburning associated with CO) while limiting NOx emissions.
RYAN NICKELL (Albemarle Corporation)
Though not directly stated, this question is most applicable to FCC units concerned with after-burn. Lowering the regenerator temperature can indeed lead to an increase in CO and NO to N2 and CO2. A platinum-based combustion promoter can be used to reduce CO emissions with excellent success. However, NO will increase as intermediates, such as HCN and NH3 (ammonia), are also oxidized by platinum. As a result, many refiners prefer a non-Pt-based promoter such as Albemarle’s ElimiNOx™. This additive provides high CO promotion activity but acts less on the aforementioned intermediates containing nitrogen. ElimiNOx™ provides excellent after-burn control and minimal impact on NOx emissions.