Question 80: What are your Best Practices to address increased levels of conventional and “new” metals (V, Ni, Fe, Ca, Cu etc.) in the FCC that come from tight oil processing in the refinery?
DE GRAAF (Johnson Matthey Process Technologies)
In the preferred case, you do not have any of those metals entering the FCC units. So, if you can optimize your desalter operation, and if there are various additive fresh suppliers who can help you, then you will be able to mitigate and reduce the number of metals entering the FCC unit. Another approach could be feed pretreat. But since the tight oil is typically already very light, this is probably an option that very few people would use.
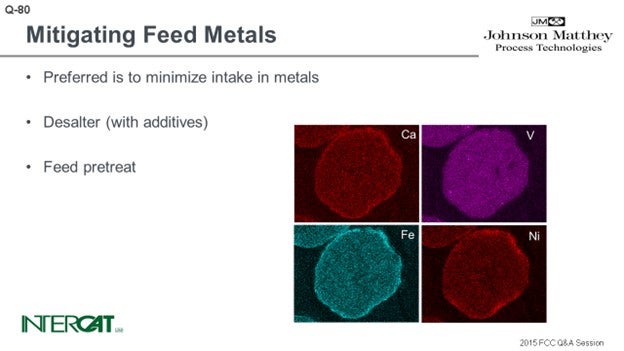
You have several ways to utilize your catalyst. If you want to reduce the overall metal effect, you can use a higher addition rate of fresh catalyst or add flushing catalyst on top of this. You will just have more particles over which the metals will be distributed. So on average, per particle, the actual metal level will be lower.
There are various options for making your base catalyst more metal resistant. For example, considering vanadium, if you want to make your catalyst more vanadium-resistant, then you can increase the amount of rare earth on your catalyst to make your zeolite more stable, or you can balance the activity by using more matrix. For nickel and copper, you can use high crystalline boehmite alumina because they can react with nickel and copper to form a nickel alumina spinel or copper alumina spinel. Those are more or less the conventional metals traps.
When it comes to iron and calcium, there are various options that catalyst suppliers can recommend. Since iron and calcium can form a eutectic and will close off the outer surface of the catalyst, the typical approach is to increase the amount of matrix and mesopores. Doing so will increase your diffusivity or accessibility. The term depends on your catalyst supplier, but it will help more feed to enter the catalyst.
Typically, catalyst suppliers also try to lower the amount of sodium off of your base catalyst. By reducing the amount of the zeolite and optimizing the amount of alumina, you will also postpone the point at which your catalyst will succumb to iron poisoning. For every catalyst, however, there is a point where iron and calcium concentrations will become too high. And at that point, you will either have to increase catalyst addition rate or use fresh catalyst.
Various refineries have also successfully used an external metal trap to mitigate iron effects. The benefit of that option is also that you retain your targeted yields from the base catalyst you have chosen. You will not have a fresh catalyst for this option because you will then be dependent on the quality of rare earth level and the presence of other additives off your fresh catalyst.
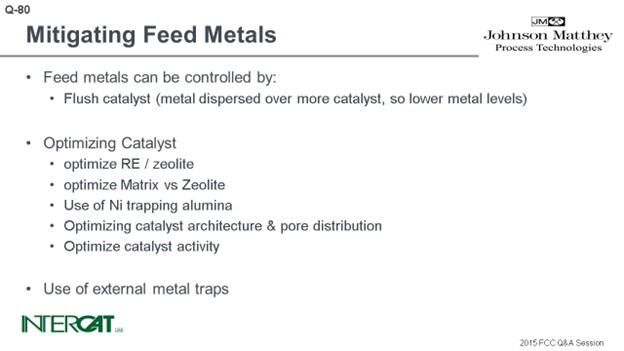
REYNOLDS (Phillips 66)
I completely disagree with everything Bart said. [Laughter] No, no! He gave a very complete answer. I will say that refiners should confirm that you are using the expertise of your catalyst and additives suppliers and your licensor. Bart’s response really covered the topic well.
LARSEN [Marathon Petroleum Corporation (MPC)]
I somewhat hate to mention it; but sometimes, “The solution to pollution is dilution.” You just have to flood the catalyst in there. I have seen a few units that have been limited by how much catalyst they can physically withdraw from their unit and then cool down, store it in a hopper, and ship out. In that case, as we experienced at one of our refineries, we installed a catalyst cooler to help, but not for that specific reason. I am sure Bart, or anyone from his organization, would be more than happy to talk to you if you are interested in that type of equipment.
JUSTIN IRICK (GE Water & Process Technologies)
This could also be a chemical vendor question. I would like to provide a counterpoint on this question. Nickel can be treated with antimony. Up to a certain threshold, it can be economically beneficial. It is not always appropriate and depends on the individual unit and the ever-changing feed. In the case of vanadium, the threshold is even higher than for nickel. Vanadium can be mitigated with tin and is cost-beneficial under certain conditions.
In the case of calcium and iron, we go back to the desalter where the pH modification has been shown to lower those contaminants by between 50 to 75%, depending on several different variables. And lastly, sodium is sometimes feed related or can be managed by caustic adjustment. Reducing caustic feed can lower sodium.
SHUYANG PAN (BASF Corporation)
This panel gave very good answers. To build on that, the majority of our customers use processed tight oil to some extent. We do see that the concentration of nickel and vanadium is not as high compared to conventional residue, but iron and calcium can be very high for some customers. Obviously, one of the solutions is to have an iron-tolerant catalyst. One of the factors is pore architecture, as Bart referred to earlier. Among our customers is a unit who runs as high as a 1.2 wt% e-cat iron. So far, we have not seen any adverse effects that could be attributed to the catalyst. So certainly, the application of catalyst technology proven to possess better iron tolerance is one solution to combat the problem of iron poisoning.
RYAN NICKELL (Albemarle Corporation)
I just want to emphasize that, certainly, a catalyst specifically designed for tight oils is a strong and advantageous way to go. In the Answer Book, you can read about Albemarle’s T-grade catalysts. We have AMBER T, and UPGRADER T, and ACTION T which fit a variety of applications. Regardless of whether you are blending this tight oil with a lighter gas oil stream, or even a very, very heavy resid stream, these are very good catalysts at managing iron.
BILGE YILMAZ (BASF Corporation)
I just want to add one point with regard to the comment on switching to low zeolite-content catalyst for dealing with iron issues. I personally have seen cases with high zeolite-containing catalyst formulations that do well in high iron environments. I believe the main point regarding dealing with iron is that you must look beyond just the size of the pores. You must evaluate the pore architecture and the hierarchy of the pores. This is making the distinction between porosity at the particle surface where iron is found and the pore volume distribution, including the interior of particle. It matters how pores are structured and where they are located. The pore distribution at the surface becomes, in my opinion, the key in dealing with these situations. Zeolite is there to serve a purpose. So if you can preserve the same zeolite content, and if you can address the high iron with the right type of catalyst, I think that would be the better solution because you would not have to give up on catalytic activities that you need.
PAUL DIDDAMS (Johnson Matthey INTERCAT)
With regard to iron poisoning, you have to consider the added iron: delta iron between the iron of the e-cat and the iron of the fresh cat. You need to be aware that some fresh catalysts have much higher iron content than others. The fresh catalyst iron is embedded in the kaolin clay component and is harmless. It is the added (delta) iron you have to monitor, so take care not to just look at the total e-cat iron. Some refiners may have problems beginning at 0.7 wt% e-cat iron because their base catalyst has only 0.3 wt% iron. However, some refiners might have problem beginning at 1.2 wt% e-cat iron because their base catalyst already has 0.8 to 0.9 wt% baseline iron. In both cases, the added (delta) iron is 0.3 to 0.4 wt%; so monitor the delta iron.
Nik was talking about resolving iron issues via dilution by flushing through addition of large amounts of either fresh catalyst or flushing e-cat; and this, in turn, would be limited by the catalyst withdrawal rate. This is actually a very common limitation. E-cat withdrawal requires unloading a hot catalyst from the regenerator, and it just does not cool down quickly enough. There are catalyst withdrawal systems on the market that are able to cool the catalyst, thereby allowing the refiner to continuously and safely withdraw e-cat, which would be particularly applicable in this scenario.
ADAM KASLE (BP Products North America Inc.)
I want to add onto what Paul said, because he said the beginning of what I wanted to say. You need to look at the delta iron, but I think that it is really important to remember that it is critical to look at the source of the iron in the unit. So saying this unit with this weight percent of iron did well or that unit did not do well does not really give you enough information. In fact, you really need to consider things like if it is organic or inorganic iron, the condition of the catalyst pore architecture, the riser residence time, and the time it will take to diffuse the hydrocarbon into the catalyst. I think this is a really complicated issue that cannot be simplified into, “This weight percent iron on e-cat has a given result every time.” It depends on the unit, the feed, the source of the iron, and the catalyst. So, you really need to think about all those aspects rather than just saying that there will be a problem at a particular weight percent.
ANN BENOIT (Grace Catalysts Technologies)
The first consideration should be removal or minimization of the contaminant metals upstream of the FCC. Since removing or limiting these contaminants may not be an option, other methods must be considered to address their negative impacts.
It is recommended to evaluate the FCC catalyst and ensure it is properly designed to handle the metals of concern in the unit. Catalysts can be formulated to incorporate Ni (nickel) and V (vanadium) traps, which reduce the negative impacts from the metals. Grace employs an integral rare earth oxide-based vanadium trap in the catalyst to reduce the deactivation caused by vanadium poisoning12. With regard to nickel, Grace utilizes a matrix alumina to trap the nickel to reduce the harmful effects. In this system, nickel that deposits on the catalyst undergoes a solid-state chemical reaction that diminishes nickel’s dehydrogenation activity13.
To address iron (Fe) and calcium (Ca), it is crucial to have an FCC catalyst that is designed to resist the negative impacts of the metals. High alumina catalyst, especially catalyst with alumina-based binders and matrices such as Grace’s MIDAS® and ACHIEVE® catalyst families, are best suited to process iron- and calcium-containing feeds because they are more resistant to the formation of low melting-point phases that destroy the surface pore structure. It is recommended to monitor bottoms cracking, e-cat ABD (apparent bulk density), and catalyst diffusivity for evidence of iron and calcium poisoning. A loss of bottoms cracking, unusually high slurry API, loss of conversion, a drop in e-cat ABD, and poor catalyst diffusion are all indicators that the unit may be experiencing iron and calcium poisoning. The loss of bottoms cracking is due to feed molecules being blocked from entering the particle and being cracked at an active site of the catalyst. The e-cat ABD drops due to the formation of nodules on the catalyst surface, which prevent the e-cat from packing as densely. SEM (scanning electron microscope) pictures of the catalyst can be taken to confirm the nodule formation on the surface of the catalyst. Fe (iron) and Ca (calcium) poison will cause the catalyst to be diffusion-limited due to pore closure, leading to a loss in bottoms conversion. Grace has developed a proprietary laboratory test method that can confirm adequate or inadequate diffusion into and out of the pore of a sample of FCC e-cat14 for use in FCC troubleshooting activities. If the unit is indeed experiencing negative impacts due to Fe and Ca, flushing the metals with higher catalyst additions and switching to a more resistant catalyst will be necessary for the unit to return to normal operations.
Other contaminants, such as alkali metals and alkaline earth metals, may be present in unconventional feedstock. These contaminants can cause a loss of unit conversion. One example is magnesium (Mg). While not a concern at low levels of less than 0.5 wt%, at higher levels, Mg has a tendency to react with silica from the zeolite to form forsterite (Mg2SiO4), which will decrease zeolite stability and adversely affect unit conversion. Note that MgO present on e-cat can be due to the presence of SOx-reducing additives and not feed contaminations15. E-cat properties and unit yields need to be closely monitored for negative impacts from these contaminants. If these contaminants start to impact the catalyst activity and unit yields, flushing the unit with higher catalyst additions could be required to return to normal operations.
In summary, the first strategy should be to evaluate removing or limiting the amount of contaminant metals that are in the FCC feed. This can be done by putting guidelines in place which set a maximum limit on the amount of contaminants being processed at the FCC. Also, when the economic analyses on these different feedstocks are being conducted, ensure they are being properly evaluated for the impact they will have on the FCC. It is suggested to close the loop on predicted yields and operating expense with actual yields and operating expense. Next, it is recommended to evaluate the catalyst and make certain that it is designed properly to handle the contaminant metals. Depending on the amount of contaminant metals levels and if the unit starts to experience negative impacts due to high contaminants, a flushing strategy may be required to get the unit back to normal operations. If purchased e-cat is being considered in the flushing strategy, it is important to evaluate and choose the right purchased e-cat that meets unit objectives. If needed, the refiner and his technical service catalyst representative can discuss how to best evaluate different catalyst options.
BART DE GRAAF (Johnson Matthey Process Technologies)
The most preferred option for minimizing the effects of increased levels of conventional “new” metals in the FCC, which come from tight oil processing it, is to minimize the intake of metals. Optimization of the desalter is key. Various suppliers offer services and additives to optimize the desalter operation. Feed pretreat is another effective way of limiting metals in feed to the FCCU.
Feed metals in the FCCU can be controlled by using various strategies. Addition of flush catalyst helps, as metal will then be dispersed over more catalyst, effectively lowering metal levels (dilution). Another option is to optimize the base catalyst. Higher rare earth on zeolite helps protect the base catalyst and increases its activity (at the expense of octane). Matrix is less susceptible than zeolite towards many metals; therefore, optimization of matrix versus zeolite activity is key. Nickel-trapping aluminas can help mitigate Ni [and some Cu (copper)] activity. These metals are all “conventional” metals, so catalytic solutions are straight-forward.
“New” metals, such as iron and calcium, are more detrimental as they can induce iron poisoning of the base catalyst. The standard response to this situation is to optimize the catalyst architecture and pore distribution. All catalyst vendors offer technologies that will provide higher mesoporosity of the catalyst. This modification will increase diffusivity/accessibility (term dependent on catalyst supplier), which is typically translated into optimizing the matrix content of the base catalyst. A separate effect is that when the alumina content of the base catalyst is increased with lower zeolite content, sodium on the base catalyst is reduced as well. Higher mesoporosity can offset the moment when the base catalyst succumbs from iron poisoning; but in the end, every catalyst has a threshold and its performance will decrease when this threshold is exceeded. Calcium enhances the effects of iron. In case of iron (or combined with calcium) poisoning, frequently flushing out the catalyst is an effective option. Various refiners have successfully used external metal traps as well. A benefit of this option is that it conserves the base catalyst selectivities, contrary to the use of flush catalyst.
NIKOLAS LARSEN [Marathon Petroleum Company (MPC)]
For some units, the ability to add catalyst in an FCC system (to flush metals, etc.) can be limited by the amount of catalyst that can be withdrawn from the system. Logistics, spent catalyst cooling, etc. can be factors here.
At one MPC FCC, we worked with Johnson Matthey INTERCAT to install a catalyst withdrawal skid to continuously withdraw and cool catalyst. Although the purpose of this skid was to aid in maintaining reactor catalyst level in this specific unit configuration, it will also aid in units that are cooling constrained, in terms of spent catalyst withdrawal. The INTERCATJM Catalyst Withdrawal System is skid-mounted and uses load cells to calculate catalyst withdrawal rates, which, in our case, is cascaded to reactor level. It continually withdraws catalyst and utilizes three pipe-in-pipe heat exchangers and an air blower to cool the catalyst before sending it to the spent cat hopper. The system has been successfully tested up to near 20 tpd (ton per day) withdrawal rates.
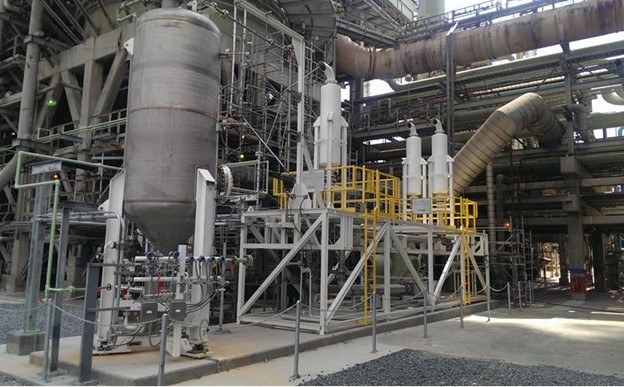
SAM LORDO (Nalco Champion)
The best place to manage at least calcium, sodium and iron are in the desalter, either the crude unit or FCCU pretreatment. Nalco Champion has two approaches, acidic and non-acidic, depending on the metal to be removed. Below is one example of a non-acidic iron removal program.
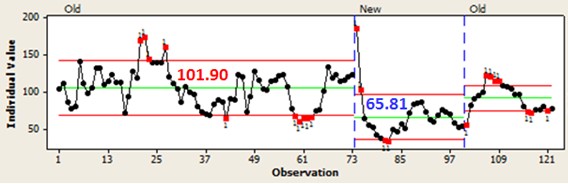
SHAUN SPIRO (XOS)
Metals found in tight oils greatly impact the performance of the FCC, as well as costs associated with replacing and protecting catalyst. Iron and calcium levels are generally high in tight oils, while nickel and vanadium concentrations can vary. The contaminants lead to increased coke and hydrogen formation with decreased gasoline production. The easiest method to control metal deactivation is to supplement with fresh catalyst, although this can be very expensive. Manufacturers have created catalysts to better handle specific metals (and combinations of metals) that are associated with tight oils. Metal trapping additives can be used to reduce the impact of metals (specifically V and Ni) and protect catalyst. Critical to improving performance is to accurately and quickly measure the metal concentrations in the FCC feed. Many of our customers utilize the XOS Maxine benchtop analyzer to measure critical metals in the FCC process. All the metal concentrations are given in a single 10-minute test as opposed to waiting hours for ICP (inductively coupled plasma) testing, which can be vital in determining unit performance or troubleshooting. The easy test and rapid results can free up laboratory resources for other analysis.
RALPH WAGNER (Dorf Ketal)
We understand that there is a concern of FCC catalyst deactivation due to the presence of metals in tight oil feedstock resulting in substantial cost on fresh catalyst. Key metals that are present in the FCCU feed are calcium, sodium, iron, magnesium, nickel, and vanadium. Calcium, sodium, and magnesium content can be reduced by optimizing the crude desalter and, in the case of resid feed, incorporating the desalter upstream of the FCCU.
The standard desalting process does not remove oil soluble compounds such as calcium naphthenate, iron naphthenate, and other metals present in organic form. Water insoluble compounds such as iron oxide, iron sulfide, and silica also present processing challenges.
Metal removal additives are available to enhance metal removal in the desalter. Selection of the best additive is a function of water chemistry, metals present, wastewater limitations, and downstream process configuration. Most options are acidic, but there are also non-acid options.
RYAN NICKELL (Albemarle Corporation)
Several steps should be taken to ensure optimal profitability and stability from an FCC unit receiving tight oil fractions. The metal contaminants in tight oils can vary significantly, not only from one shale play to another but also within a given play over time. A full analytical analysis of the feed will allow the catalyst provider to make optimal technology and formulation decisions. Some tight oils are very high in Na (sodium); therefore, optimal operation of available desalter capacity is advised. The most important step is, perhaps, selection of a catalyst specifically designed for tight oil feeds. Albemarle offers AMBER™ T, UPGRADER™ T, and ACTION™ T which are demonstrating tangible benefits for refiners.16,17 Though tight oils are very light (high API, low CCR), they are often mixed with heavier feeds to better fit refinery design. UPGRADER™ T fits these heavy feed applications while AMBER T is the choice for lighter feeds. When the paraffinic nature of tight oil affects the FCC naphtha octane, ACTION is the preferred catalyst family proven in over 10 FCC units within North America. ACTION™ T contains ADZT-100, a proprietary zeolite technology that promotes octane enhancement and butylene production. A key feature of all three aforementioned catalyst families is their use of Albemarle’s matrix technologies which provide high resistance to the “new” metals in question, as well as conventional ones. Fe and Ca from tight oils are particularly detrimental since they interact synergistically to form an impenetrable skin on the catalyst surface. This phenomenon effectively deactivates all interior acid sites that help facilitate the cracking reactions. Albemarle’s tight oil catalysts have exceptional surface and pore accessibility; thus, they resist iron and calcium better than competing technologies. Finally, the light FCC feed resulting from tight oils can lead a refiner to be short on delta coke and low on regenerator temperature. In this case, the Best Practice will further depend on the individual FCC unit design and constraints. Albemarle may recommend an adjustment to the activity, nickel-tolerant matrix, or use of antimony. These considerations are optimally addressed with an Albemarle representative.