Question 8: Where is salt (NH4Cl or (NH4)2S) fouling most likely to occur? What are common practices for monitoring and mitigating?
ABIGAIL SLATER (HollyFrontier)
Salting typically occurs in the reactor effluent exchangers (shell and tube and fin fans), recycle and net gas compressors, and product stabilizer overhead system (top trays, overhead condenser, etc.). Common monitoring practices on exchangers and fin fans can be tracking exchanger duty, temperature, and delta pressure, all of which indicate increasing fouling. For compressors, the discharge flow, efficiency, and delta head (corrected for gas molecular weight) can all be indicators of compressor fouling. For stabilizer towers, tower delta pressure and similar overhead exchanger monitoring can indicate fouling.
Common practices to mitigate the fouling are to reduce the source of the foulant, which includes reducing nitrogen in the feed and chloride in the products using technologies like chloride guard beds. For compressors, continuous naphtha washes can be effective at managing fouling. For towers and exchangers, online and offline water washes can remove salt formations. In Naphtha HydroTreaters, online water washes can also be effective in removing salt fouling with no major impacts to the unit. In Naphtha Reformers, online washes can also be effective but must be done in parts of the unit where the water will not contact the catalyst (downstream of reactors and recycle compressor). If no online mitigation is possible, the unit will periodically need to be shut down to clean the affected equipment.
THOMAS PORRITT (Chevron U.S.A.)
We find that salt deposits form in the compressors, the reactor effluent fin fans, the stabilizer column overhead fin fans, and the stabilizer top trays (see figure Q8 – 1). Process temperature is the largest factor in where the deposits are most likely. There are two approaches the user can take to monitor and mitigate salt deposition. One is proactive the other is reactive.
The user can prevent salt deposition by choosing to operate their process above the sublimation temperature of the salt being monitored. For exchangers or coolers, the user can also monitor the fouling rate. For compressors, the user can track compressor efficiency. Once fouling rate or efficiency have declined to unacceptable levels the user can mitigate with one of the methods described below.
If the user cannot practically monitor the indicators above, there are some additional reactive monitoring they can employ. For heat exchangers or coolers, the user can monitor the approach temperature and the differential pressure. For compressors, the user can monitor vibrations. For distillation columns, the user can monitor differential pressure and flooding in the top of the column. These indicators are less effective as they only manifest once salt deposits have begun to impact the process.
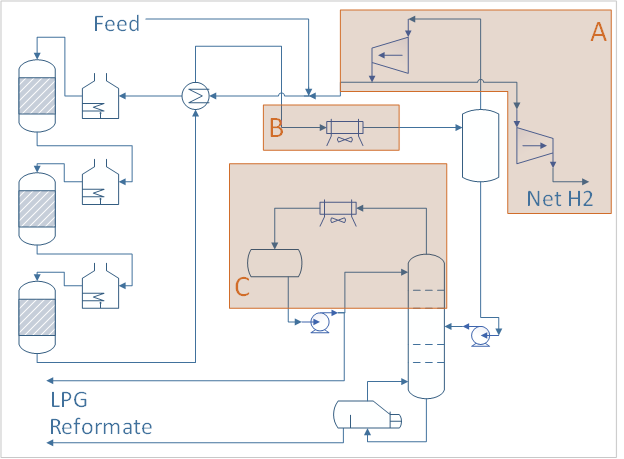
Figure Q8 - 1 Common Areas for Salt Deposition
The user has some preventative and reactive options to mitigate the effects of salt deposits in the process. The best option is to control species that form the salts. Most users limit nitrogen in the feed because it addresses both the ammonium chloride and the ammonium bisulfide salts. For compressors, the user can supply a film on the rotors in the form of a coating or a continuous naphtha wash to prevent salts from gaining a foot hold. For reactor effluent coolers or distillation overhead coolers a continuous water wash can remove the salts before they build up. For distillation columns a chloride scavenger has been proposed by some vendors.
For existing units and equipment where continuous washes or coatings are not an option, the user will need to periodically shut down for a water wash to remove the salts when they build up.