Question 8: What methods are you using to address alkylates’ sulfur contribution to the blend pool for Tier 3 compliance? Is your focus on feed pre-treatment or alkylate post-treatment?
DUBIN (Axens North America)
Thanks, Gordon. Our friends at STRATCO gave us some feedback of the survey they did back in 2014 of the sulfur content in the alkylate streams that were tested. It would be interesting to see how it compares with the results of the poll. Back in 2014, 90% of the alkylate streams had less than 10 ppm weight of sulfur in the finished alkylate and 60% of those had less than 5 ppm weight of sulfur. So, there were only 10% or so that had more than 10 ppm weight, which would be above spec for Tier 3. Most often, those high sulfur alkylate streams were due to issues with high sulfur in the makeup isobutane to the alkylation unit rather than sulfur from their LPG (liquefied petroleum gas) side of the FCC (fluid catalytic cracker) or coker. So, what we saw in the industry was that it was more expensive – on a sulfur barrel-per-dollar balance – to treat sulfur in the alkylate versus going after it in other streams such as FCC gasoline and LSR (light straight-run) naphtha.
SHARON (Valero)
I think this flanges up exactly as Geoff was saying. This stream is not something we have targeted in Valero for Tier 2 or 3 compliance. We have HF and sulfuric alkys; and throughout the circuit; we are at less than 10 ppm.
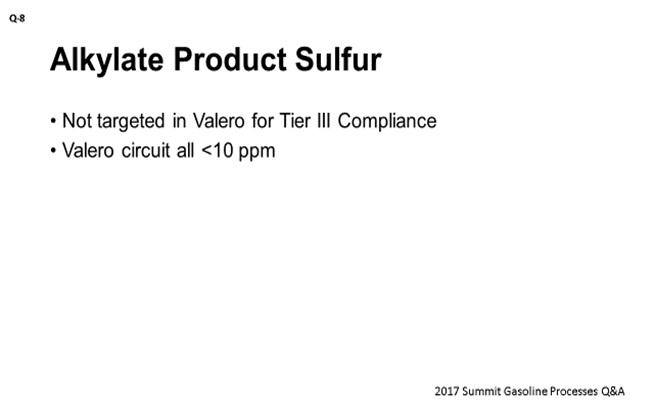
SABITOV (Phillips 66)
My answer is consistent with Kyle’s. The alkylate in the Phillips 66 refineries is a low-sulfur source to the gasoline pool. The sulfur level is well below 10 ppm. We rely on the alky feed pre-treatment as the way for sulfur management in the alkylate; that gives us the additional benefit of a lower acid consumption. Some tweaks to the alkylate sulfur might be possible, but these are fairly limited by increasing the spent acid rejection.
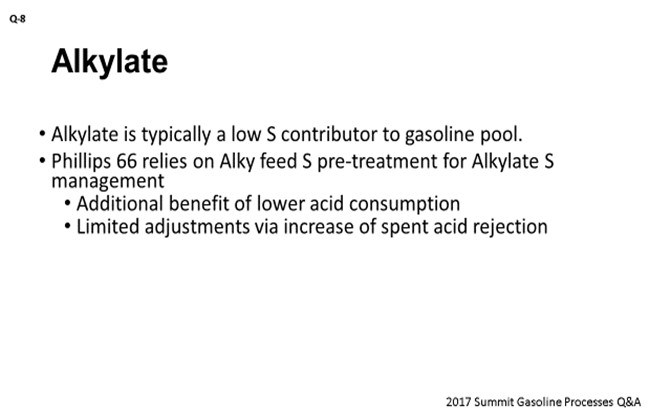
GEOFFREY DUBIN (Axens North America, Inc.)
For many, the alkylate’s sulfur contribution to the pool has not been the most economical sulfur to address when targeting Tier 3 compliance. STRATCO completed a survey of the sulfur content of alkylate streams in 2014; and that time, almost 90% of alkylate streams contained less than 10 ppmw of sulfur, with nearly 60% of those containing less than 5 ppmw of sulfur. Since that time, the overall distribution of alkylate product quality has not changed significantly.
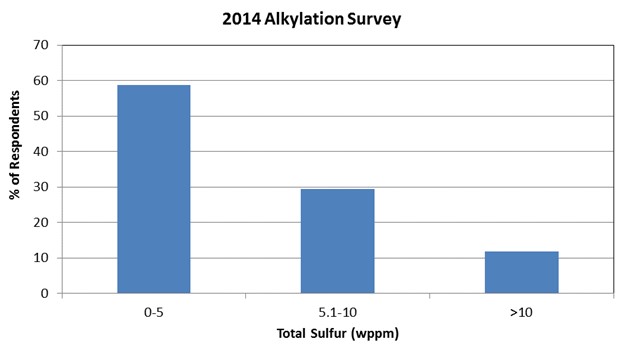
Reprinted with the permission of DuPont Clean Technologies
Typically, when refiners are facing high sulfur in the alkylate, it has less to do with sulfur in the olefinic LPGs, rather, it is often caused by makeup isobutane with high sulfur – through poor end point control, as an example – that is sent directly to the deisobutanizer and on to the product. Another key source of sulfur in the alkylate is due to issues in the effluent treatment systems that allow sulfur into the alkylate product.
Often, the sulfur in the alkylate is more expensive, on a dollar-per-pound-sulfur-removed basis, to remove then the cost of removing sulfur in other gasoline pool streams such as cat gasoline and/or light straight-run naphthas.
RICHARD TODD (Norton Engineering Consultants, Inc.)
Sulfur in alkylate is normally very low; but with the extremely low sulfur requirements of Tier 3 gasoline its impact may be more widely felt than previously. Sulfur can be the result of improperly treated feedstocks, and normally the best route for handling this type of sulfur is to improve the operation of the alkylation pretreatment facilities to reduce sulfur. Removing sulfur from the feed will not only improve alkylate sulfur, but it will also improve overall alkylation unit operation and reduce acid consumption.
In some sulfuric acid alkylation units, sulfur may result from sub-optimal operating conditions in the reactor and/or effluent treating section. An evaluation of the reactor and effluent treating section may identify opportunities for improvements that will not only reduce alkylate sulfur, but also decrease acid consumption and increase alkylate octane.
STEPHEN WILLIAMS (CB&I)
CB&I has successfully licensed an advanced version of sulfuric acid alkylation technology, called CDAlky®, to thirteen clients to date. CDAlky technology does not focus on feed pretreatment or product post-treatment, but rather on effectively eliminating the root cause of why sulfur is present in the alkylate product; namely, sulfate formation and acid carryover.
CDAlky’s design philosophy not only reduces alkylate sulfur levels to less than 5 ppm, it mitigates corrosion and fouling issues. First, the amount of acid leaving the reactor is limited by the reactor’s novel design, which has the added benefit of increasing acid utilization while operating at low temperatures. Second, the acid droplet size is controlled by using an optimized proprietary packing system rather than a rotating impeller. This packing system permits a rapid and efficient separation of the acid-hydrocarbon phases, which eliminates acid carryover completely. Because of greater separation efficiency, post-treatment of the reactor effluent is not required. Third, the unit operates in an acid-to-olefin regime, which minimizes the formation of stable, hydrocarbon soluble sulfates.
This strategy ensures that the reactor effluent is dry, which greatly reduces corrosion rates and associated maintenance costs and safety risks. It also provides for an alkylate product that has an extremely low sulfur content, clearly an advantage in a Tier 3 world. Most importantly, these advantages have been fully and consistently demonstrated at units that have been in commercial operation over the past four years.
SHANE PRESLEY (DuPont Clean Technologies)
The total sulfur of the alkylate product from a sulfuric acid alkylation unit is typically not a function of the concentration of sulfur in the feed since most sulfur species are highly soluble in sulfuric acid and will go into the acid phase in the reaction zone. DuPont has experience with at least one customer who had up to 1,000 ppm total sulfur in the olefin feed, yet the product sulfur was still very low. One exception is when feed streams enter directly into the fractionation section without passing through the reaction section. This is a common practice when there is a low-purity isobutane stream being fed directly to the deisobutanizer (DIB) tower to separate out isobutane from diluents such as normal butane.
Even with all the feed passing through the reaction section, there is typically a small amount of sulfur present in the alkylate product. The graph below shows the results from the 2014 Alkylation Survey conducted by DuPont. Customers responded to a series of questions related to sulfuric acid alkylation units. As can be seen in this chart, nearly 60% of the reporting alkylation units have a sulfur content of less than or equal to 5 ppm, and nearly 90% of those who responded had less than or equal to 10 ppm sulfur in the alkylate. For those units that reported higher alkylate sulfur concentrations, the reason for this elevated number is likely due to sulfur-containing feeds being routed directly to the fractionation section.
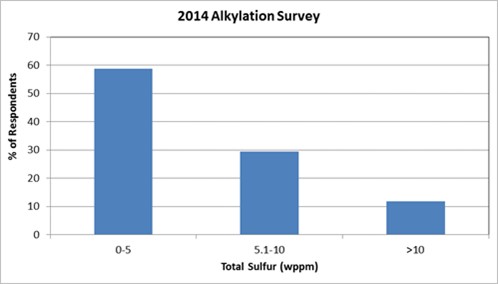
The graph below shows the alkylate sulfur content from a 2017 performance test of a grassroots STRATCO® alkylation unit. During this performance test, the sulfur content of the alkylate averaged 1.5 ppm and never exceeded 2.0 ppm.
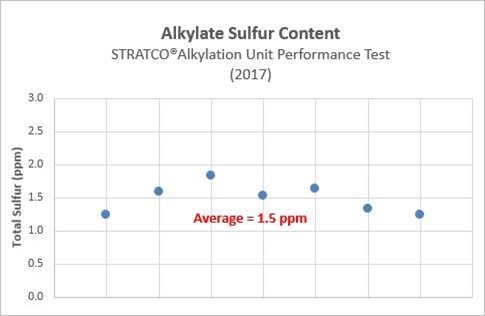
DuPont has recently unveiled the Dry Alumina Adsorption technology for removal of acidic species from the feed stream to the fractionation section. Within units where this technology has been installed, consistently low sulfur concentrations (less than 2 ppm) have been observed. For existing alkylation units that suffer from unusually high sulfur in the alkylate, an evaluation is recommended to understand the source of this sulfur. Installation of the Dry Alumina Adsorption technology may also be an option to further reduce sulfur, as well as corrosion and fouling, in the fractionation section.
RICHARD TODD (Norton Engineering Consultants, Inc.)
Sulfur in alkylate is normally very low; but with the extremely low sulfur requirements of Tier 3 gasoline its impact may be more widely felt than previously. Sulfur can be the result of improperly treated feedstocks, and normally the best route for handling this type of sulfur is to improve the operation of the alkylation pretreatment facilities to reduce sulfur. Removing sulfur from the feed will not only improve alkylate sulfur, but it will also improve overall alkylation unit operation and reduce acid consumption.
In some sulfuric acid alkylation units, sulfur may result from poor reactor or effluent treating operations. An evaluation of the reactor and effluent treating section may identify opportunities for improvements that will not only reduce alkylate sulfur, but also decrease acid consumption and increase alkylate octane.
KURT DETRICK (Honeywell UOP)
We are not aware of any refiner doing post-treatment of alkylate for sulfur reduction.
Feed pretreatment typically consists of extractive caustic designs. Proper operation of the H2S (hydrogen sulfide) removal units (typically amine-based) upstream of these extractive caustic units is essential for good mercaptan removal.
During normal HF alky operation, up to about 25% of the sulfur in the feed can end up in the alkylate. The use of “internal” acid regeneration, upsets, or poor operation of the acid regeneration column can cause up to 100% of the sulfur in the feed to wind up in the alkylate.