Question 8: What is the industry experience with de-isobutanizer (DIB) feed pre-heatexchanger or reboiler fouling? What are the typical causes of the fouling? How do you mitigate this problem? Comment on both HF and sulfuric technologies.
BULLEN (UOP LLC, A Honeywell Company)
I am going to talk about HF alkylation units only. The feed pre-heaters for the isostripper or main fractionator have experienced corrosion and fouling. There are several possible causes. One is getting the metallurgy, which is typically carbon steel, too hot. If you go over 160°F in the presence of HF, it gets very corrosive; so, you can lose metal that way. How does that happen? Often it will be caused by the hot side being too hot, which leads to the metal tubes becoming too hot. For instance, if you use the bottoms alkylate for heating up the feed, you can get the skin temperatures on the tubes hot enough to accelerate corrosion. So, we recommend that you actually heat-exchange the isostripper bottoms prior to using it as a pre-heater. If you continue to have issues with corrosion, upgrading to Monel™ or 70/30 copper-nickel (Cu-Ni) is a way to address the issue, though our standards have not changed for this exchanger. It is still carbon steel.
Another possibility for corrosion would be if you are getting excessive carryover from an acid settler and more than just the normal low level. One cannot heat up the feed to dissolve that extra acid into the feed, given the temperatures involved. Again, if the problem cannot be fixed with settler modifications, some refiners have upgraded the tubes again to Monel™ and 70/30 Cu-Ni.
Also, fouling can occur due to scale carryover from the acid settler. When that happens, the particles can settle out and accumulate in the feed pre-heater. We recommend that you actually have the feed go into the exchanger in a downward direction to help flush out the scale particles, so they do not settle out.
Finally, in the isostripper reboiler aspect of corrosion, we typically do not see an issue in HF alkylation units. We are aware of only one unit that had issues. You can read about that in the Answer Book response if you like.
MELDRUM (Phillips 66)
Patrick covered the issues with the HF technology, so I will address my comments to the sulfuric technology. Therein, the primary reasons for DIB fouling from the sulfuric alkylation units are poor net effluent treatment, caustic carryover, foaming, or Butamer stabilizer operations. Poor reactor effluent treatment, either through operations or by design, can allow neutral ester carryover, which would then decompose upon heating in the DIB pre-heat exchanger or in the DIB reboiler. The decomposition of these neutral esters will form SO2 (sulfur dioxide); and when they migrate up the tower, they will create a low pH in the tower overhead leading to corrosion and thus some fouling from the deep products of corrosion. It can occur not only throughout the tower, but also in the pre-heat exchange.
The reboiler can also foul with tar-type deposits as the byproducts of the decomposition of these neutral esters. Good reactor effluent treatment requires effective mixing in both the caustic and alkali wash sections, as well as the waterwash. Also, to have sufficient temperature in the treatment section, at least 120°F is recommended for a butylene feed system. If significant amounts of propylene are being fed, that temperature should also be increased.
Caustic carryover can contribute to salt fouling in the DIB tower. It is generally controlled with good level management in the treatment section and by having a waterwash section after the caustic or alkali wash. High caustic hydrocarbon interface level makes it easier for this carryover to occur, so the management at that level should be given some attention. Foaming carryover from the treater can also occur. It can be caused by aromatics, such as benzene in the alkylate feed, or from ethylene in the feed. It is reported that as little as 50 ppm of benzene in the alkylation feed can cause some net effluent treatment foaming.
Finally, the Butamer stabilizer operations should be operated as such to reject the chlorides overhead from being treated in the off-gas caustic scrubber. If not operated properly, the chlorides can leave the bottom of the stabilizer with the butane that then enters the DIB tower and contributes to corrosion in the DIB system.
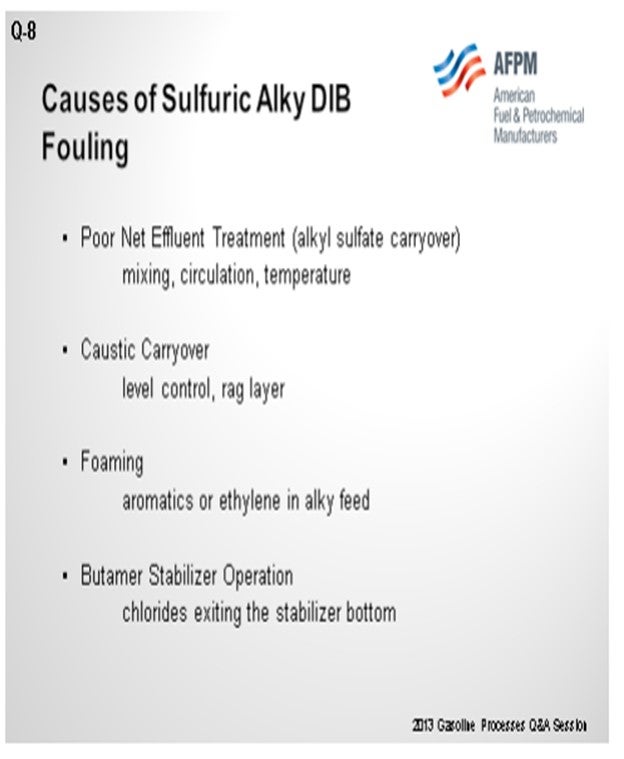
ERIC LEETON (UOP LLC, A Honeywell Company)
I want to build on the statement that Craig mentioned about the rag layer. In our settlers and HF alkylation processes, we often look at an acid and hydrocarbon interface. We tend to forget about that emulsion layer. Different feed contaminants change the characteristics of that layer; so, while your apparent acid level may be good, if that emulsion or rag layer expands, you could have unexpected carryover at that perceived acid level. So, watch out for feed contaminants that show up periodically with changes in FCC operations, purchased feedstocks, or the rise of butane in the HF alkylation process.
PUI-NANG LIN (Flint Hills Resources, LP)
I agree with the comment from Eric Leeton on the importance of the emulsion layer in the acid settler. We found out that we have excessive fouling on our DIB pre-heat exchanger on an HF alkylation unit. This fouling occurred at the inlet tube sheet of the exchanger even though our exchanger flow path is a downward flow, as Patrick suggested. We learned that the main criteria is to be sure that the pipe scales I the exchanger inlet piping are cleaned thoroughly during the turnaround. Those loose scales can really cause a lot of problems.
PATRICK BULLEN (UOP LLC, A Honeywell Company)
Corrosion and fouling of isostripper or main fractionator feed pre-heaters has been experienced in some HF alkylation units. The tubes in these pre-heaters are typically carbon steel, and there are often two exchangers in series that use different sources of heat.
One possible cause for corrosion of the tubes is high tube skin temperature. The corrosion rate increases sharply when the carbon steel temperature exceeds about 160°F in the presence of HF. If the hot-side fluid temperature is too high, the skin temperature can be high enough to cause high corrosion rates. Low pressure steam is generally a good choice for the hot-side fluid. Alkylate directly from the bottom of the isostripper column is typically not a good choice. If alkylate is used to heat the isostripper feed, it is best to reduce the alkylate temperature below about 300°F by routing it through another exchanger first (such as an auxiliary reboiler in the depropanizer or upper part of the isostripper). In cases where high tube skin temperature cannot be avoided, the tube metallurgy can be upgraded to 70/30 Cu-Ni Monel™.
Another possible cause of corrosion is excessive acid carryover from the acid settler upstream of the pre-heater. There is always a small amount of free acid carryover from the settler in the form of tiny droplets that are simply too small to settle out inside the settler. This small amount of acid will readily dissolve into the hydrocarbon phase as soon as the temperature increases just a few degrees. If the acid carryover is excessive, the hydrocarbon temperature may have to increase by 20°F or 30°F to fully dissolve the acid. The corrosion rate of carbon steel is much higher when it is in contact with a separate liquid phase of acid (commonly called “free” acid) than when the acid is fully dissolved in the hydrocarbon at the same temperature. The extra time and higher temperature required for free acid to dissolve can result in significant corrosion of carbon steel. This problem can be avoided by proper design of the settler and operation of the unit so that the hydrocarbon flow rate through the settler is not excessive. In cases where acid carryover has been an ongoing problem, some refiners have upgraded the tubes to 70/30 Cu-Ni or Monel™.
A possible cause of fouling of the pre-heater is accumulation of scale that settles out of the flowing hydrocarbon. Scale particles can be carried over from the settler into the isostripper feed. These scale particles can settle out and accumulate in the pre-heater exchangers. This accumulation can be minimized by making sure that all acid-containing streams (which generally contain some small amount of scale) flow through the exchanger in a downward direction (even if the stream is being heated). This may reduce the theoretical efficiency of the clean exchanger a bit, but it also reduces the accumulation of scale inside the exchanger during the run that will result in better overall performance of the exchanger.
The isostripper or main fractionator reboiler in an HF alkylation unit is typically a fired heater; and in UOP’s experience, coking in the tubes of this heater is rare. UOP is aware of only one unit that experienced accumulation of coke-like particulates in the column bottoms circuit. This was due to low reboiler pass flows that resulted in well over 80% vaporization in the tubes. Normal design is 50% vaporization.
PAUL FEARNSIDE (Nalco Champion Energy Services)
On sulfuric units, one of the main constituents of reboiler fouling is corrosion byproducts that are formed higher up in the DIB column and migrate downward. Corrosion can be attributed to acid carryover or neutral ester degradation. A corrosion control program including neutralizers and/or filmers has proven effective in reducing reboiler fouling from this mechanism