Question 8: How do you improve cold flow properties in a hydrocracker?
LEICHTY (Chevron USA, Inc.)
I will discuss several considerations including crude and product PNA distribution, feed effects, distillation performance, catalyst selection, and operating parameters.
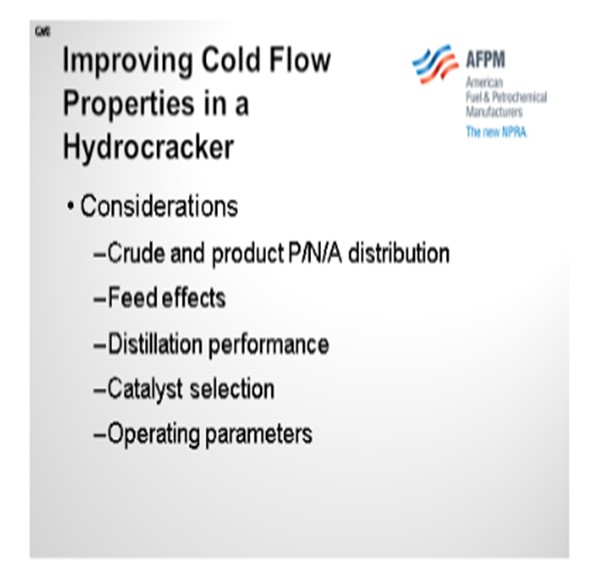
If you take a look at the molecular structure and properties of hydrocarbons in the C14 series, you will notice that the n-paraffins have the worst cold flow properties. Some of the multi-ring aromatics are also not good. So, when looking at crude purchases, waxy Far East crudes or some of the new shale-derived crudes will have worse cold flow properties because there are more paraffins in the feed. Moreover, any overlap in the feed (material that boils below the recycle cutpoint) will negatively impact cold flow properties since overlap material will contain more n-paraffins than the hydrocracked products. Finally, the proportion of product generated by the first stage versus second stage will also have an impact on cold flow properties. This is because the first-stage hydrocracker product tends to be 1:1 or 2:1 isoparaffin-to-normal paraffin ratio, whereas second-stage products can make 10:1 iso-to-normal paraffin ratio or better. Obviously, the more isomerization you get, the better your properties will be.
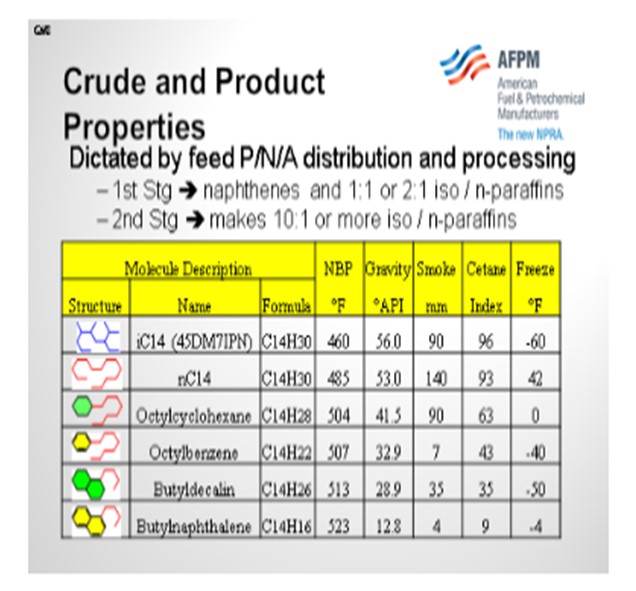
Now let’s consider feed overlap and ease of reaction. Light paraffins from straight run and coker feed, whether they boil below or above the recycle cutpoint, will tend to take a free ride through the first-stage reactor because they are the least reactive molecules and will negatively impact product cold properties. LCO feed overlap will impact the gravity, smoke, and cetane, but it may not impact the freeze or cloud, depending on the recycle cutpoint and the degree of saturation.
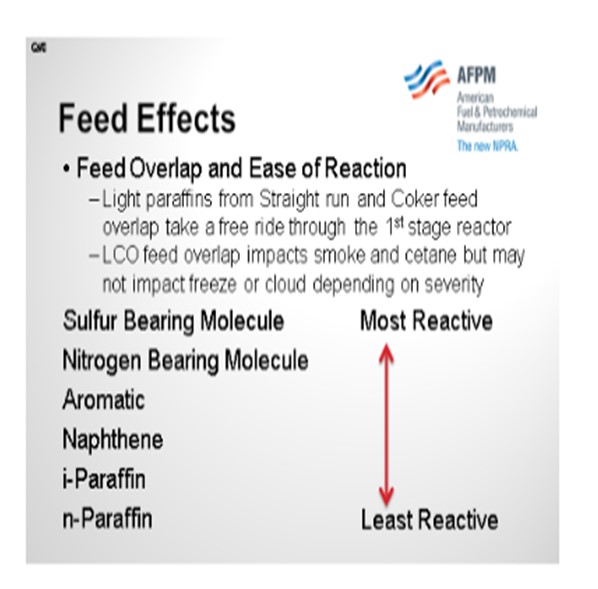
Distillation performance is probably one of the single biggest killers of cold flow properties. The cumulative distillation diagram below helps illustrate how the heavy tail of a distilled product can affect the cold properties. Cloud point and freeze point are defined by the temperature at which the first crystals of wax form in a hydrocarbon mixture as it is cooled. Sloppy distillation results in long tails which have material that will crystallize at a higher temperature. It is therefore important to have sharp distillation cuts by maximizing overhead reflux and minimizing pumparound in order to achieve high liquid-to-vapor ratio in the distillation tower. Note that it is also important to maximize reboiler duty in order to strip out the material boiling below the recycle cutpoint (the cutpoint between diesel and unconverted oil). The diagram shows approximately 5% yield that is boiling below the recycle cutpoint in the unconverted oil. With better stripping, much of this material could be recovered as on-spec diesel instead of cracked into less valuable products.
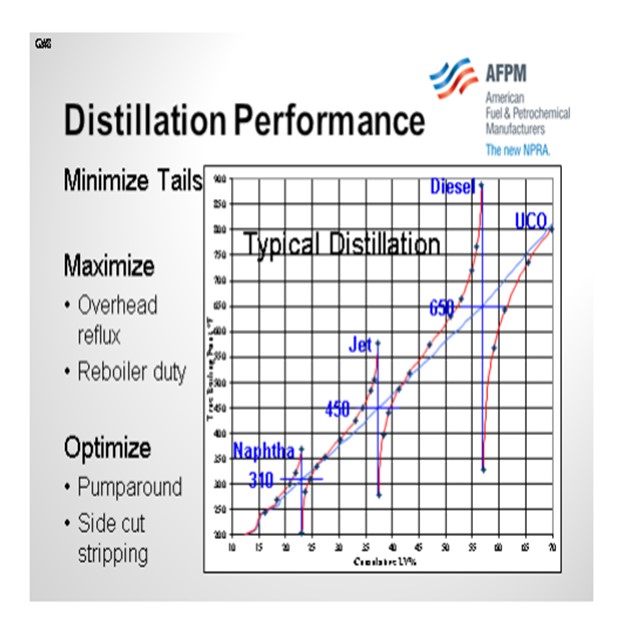
In your catalyst selection, if you have a single-stage hydrocracker, you want to design your catalyst system to isomerize paraffins to the highest degree possible. These types of hydrocracking catalysts tend to be a little less nitrogen-tolerant, so it is important to do good denitrification on the upper beds. The latest generation catalysts have higher start-of-run temperatures but have proven to be very stable over time. In the second-stage of a two-stage hydrocracker, there is not much room to improve cold properties since all of these molecules are synthetic in nature and have greater than 10:1 iso-to-normal ratio.
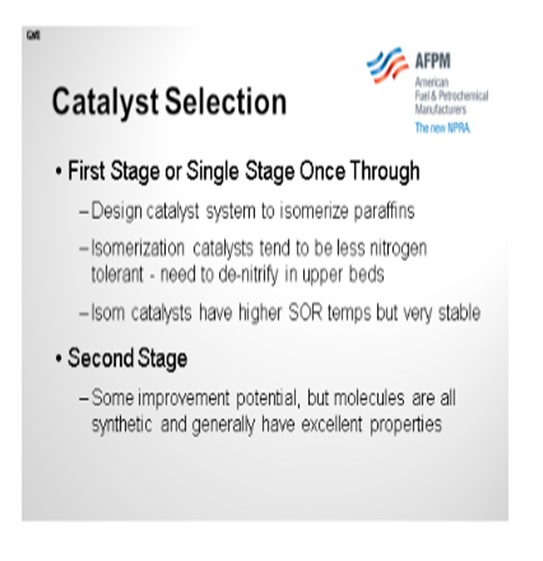
On this slide is a diagram showing how if you move from a conventional first-stage hydrocracking catalyst up to a newer generation that has a higher selectivity, you may require a little higher temperature in order to get the pour and cloud point reduction. The good news is that these newer generation catalysts are very stable, so you will not see a high degree of fouling over time.
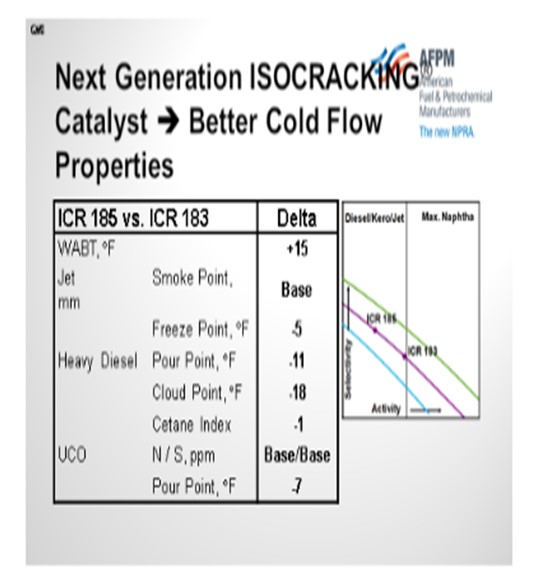
In the two-stage hydrocracker, it is important to optimize first-stage conversion. The first-stage products see a less acidic environment because of the presence of ammonia and higher temperatures. These conditions tend to favor n-paraffin production. Knowing this, it would be tempting to shift the first-stage conversion to the second stage by loading less hydrocracking catalyst in the first stage. However, in doing so, the per-pass conversion in the second stage could get so high that over-cracking will cause a reduction in distillate yield. Maximizing distillate with the desired cold flow properties therefore requires an optimization between first- and second-stage hydrocracker conversions. In any scenario, it is desirable to maximize hydrogen partial pressure and/or minimize space velocity in order to saturate diaromatics, promote cracking and isomerization, and achieve high distillate yield with good cold properties.
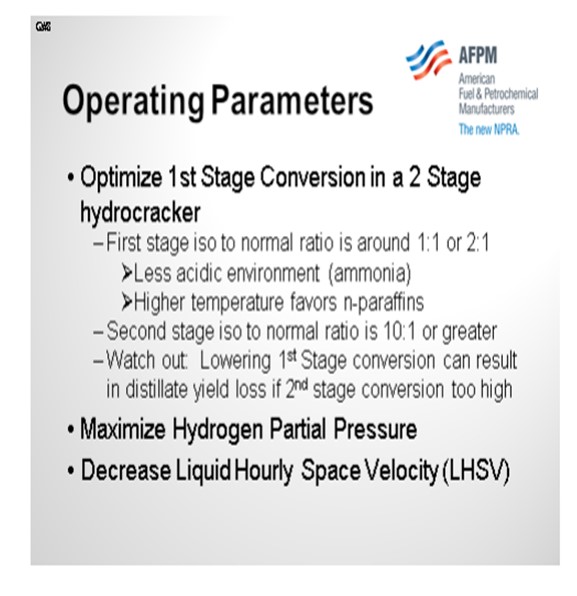
CARLSON (Criterion Catalysts & Technologies)
In addition to those considerations just presented, we look at middle distillate flow improvers and wax anti-settling agents. They can be effective, of course, in controlling pour point and CFPP (cold flow plugging properties), but they do not tend to help us much on cloud point. Neither of them adds to our operating cost. So, if we want to achieve significant cold flow improvement, we really need to know how to get rid of these long linear paraffins in the reactors.
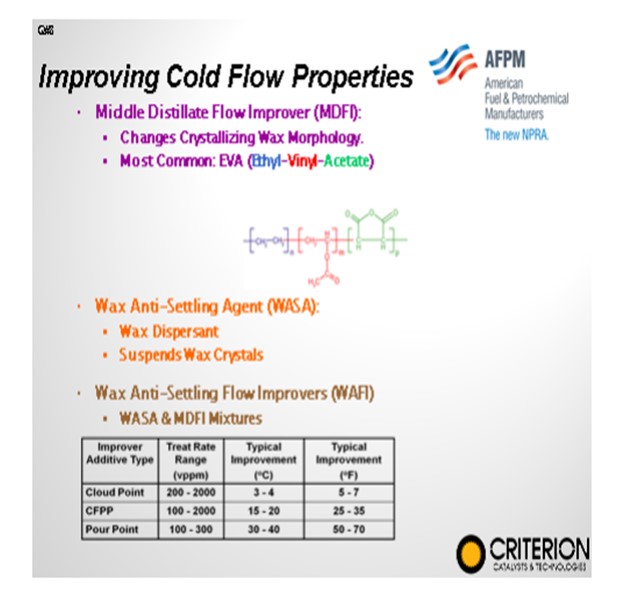
To achieve a considerable improvement in cloud point, there is a need to remove the components causing the high cloud point. As discussed, reducing the feed final boiling point can reduce these components, but it can result in yield losses that may be economically unfavorable. A better approach is to install catalysts that can modify or remove the linear paraffins within the feedstock (dewax) while achieving the desired product selectivity.
Two types of reactions are used for the removal of linear paraffins: selective paraffin hydrocracking and paraffin isomerization. Cracking decreases both the melting and the boiling point, while isomerization mostly affects the melting point, leaving the boiling point largely intact. Cracking creates two smaller fragments from the original linear chain paraffin molecule that have substantially lower melting points. However, the boiling point will also shift downward, potentially moving the molecules out of the target boiling range and reducing the total diesel yield. This yield shift can occur when using conventional zeolites in hydrocracking operations.
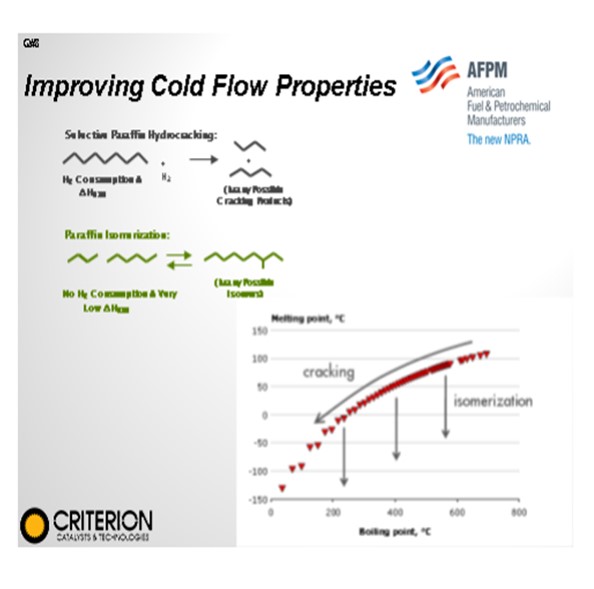
I
somerization, as you heard, would be a preferred mechanism because it both improves the cold flow properties by lowering the melting point and it leaves the final molecule in the distillate boiling range. However, selective isomerization is difficult to do in hydrocracking applications. Selective isomerization is typically much more favorable in a clean second-stage reactor with platinum or palladium-type catalysts.
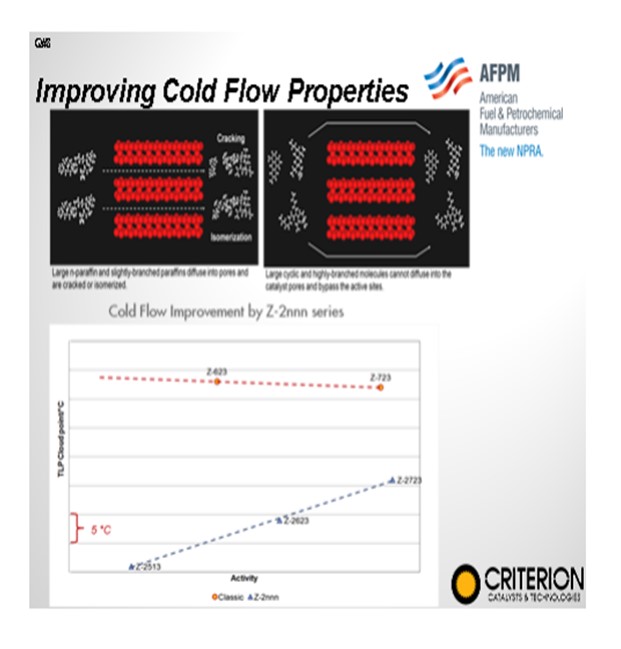
Effective dewaxing requires a proper differentiation between the linear paraffinic molecules (wax) and the rest of the feed molecules in order to achieve a high selectivity and minimize distillate yield loss. In hydrocracking, this is achieved by employing a shape-selective zeolite to preferentially convert the large linear paraffins. Criterion/Zeolyst has a portfolio of shape-selective cracking catalysts, its Z-2000 series, that selectively crack large linear paraffins resulting in an improvement in the product cloud point all along the activity/selectivity scale. These catalysts provide a boost in middle distillate yield versus conventional wide-pore zeolite catalysts due to the fact that the converted material has the tendency to reside in the distillate boiling range.
In mild hydrocracking operations, catalytic dewaxing can be employed on the backend of the upgrading process once all other properties have been already achieved. Criterion has a number of distillate feed applications where a catalyst, such as an SDD-800, can be loaded in the last bed of the reactor to assist in improving cloud point and, again, minimize distillate losses.
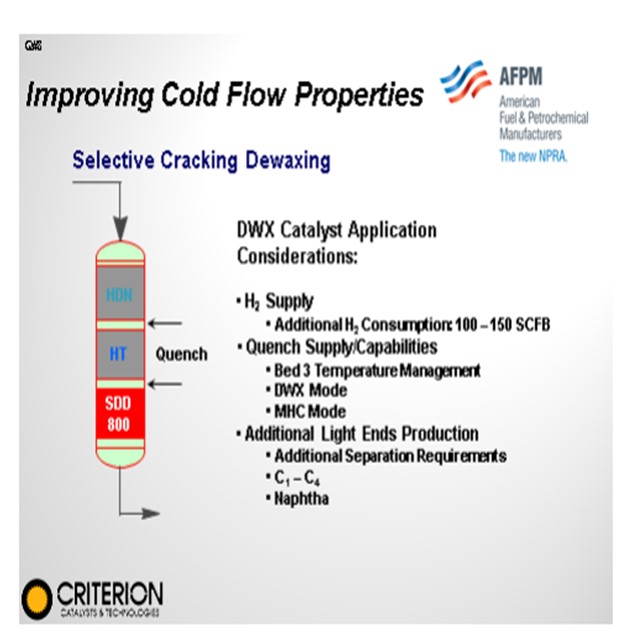
KEVIN CARLSON and WARD KOESTER (Criterion Catalysts & Technologies)
In the last decade, improving the cold flow properties of various feedstocks in a selective and cost-efficient way has gained increasing importance. In addition to providing a product in the specified cold flow property range, refineries apply cold flow improvement processes to avoid using cold flow additives, to reduce their kerosene blending requirements, to upgrade heavier feedstocks with higher cloud and/or pour points, and to create room in the blending pool for heavier feeds. The growing interest in cold flow improvement technologies stems from the increasingly stringent engine specifications, the processing of more paraffinic crudes, and the desire to sell the products at markets with demanding cold flow properties specifications.
There are several routes to improve the cold flow properties of distillates from a hydrocracker. Dilution by the addition of kerosene and/or cold flow improvers to the diesel pool have been the most widely applied routes. These methods are effective for pour point and cold filter plugging point (CFPP), but these have little effect on cloud point.
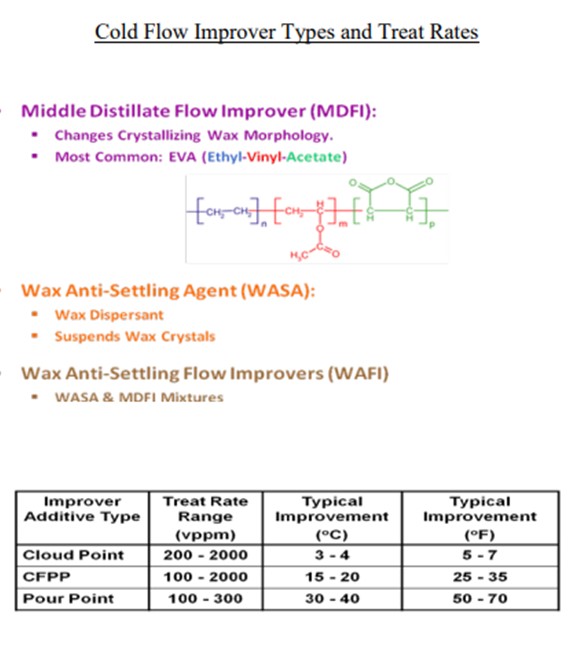
Cloud point measurement is aimed at registering the first appearance of solid particles and the additives/diluents used for improving the flow will not prevent the crystallization; rather, they delay it by modifying the shape of the crystals or by impeding their growth. Therefore, to achieve a considerable improvement in cloud point, there is a need to remove the components that cause the high cloud point. Reducing the feed final boiling point can achieve this with limited effect, but this results in relatively large yield losses that may be economically unfavorable. A better approach is to install catalysts that can modify or remove the linear paraffins within the feedstock (dewax) while achieving the desired product selectivity.
Two types of reactions are used for the removal of linear paraffins during catalytic dewaxing to improve the cold flow properties of the diesel: cracking and isomerization (selective paraffin hydrocracking and paraffin isomerization).
Cracking decreases both the melting and the boiling point, while isomerization mostly affects the melting point leaving the boiling point largely intact. Cracking creates two smaller fragments from the original linear chain paraffin molecule. These fragments have substantially lower melting point than the starting molecule and the cold flow properties, especially the cloud point, will drastically improve. However, the boiling point will also shift downward, potentially moving the molecules out of the target boiling range of the feedstock, reducing the total diesel yield. This is what can occur when using conventional zeolites in hydrocracking.
Isomerization is the preferred mechanism for converting linear paraffins because isomerized products have the same molecular weight as their parent starting molecules thus preserving yield. However, you cannot do selective isomerization under hydrocracking conditions with base metal catalysts. Selective isomerization is much more favorable in a clean second-stage environment (i.e., with very little to no H2S, NH3, unconverted organic nitrogen and sulfur-containing molecules) with employment of noble metals such as Pt (platinum) or Pd (palladium).
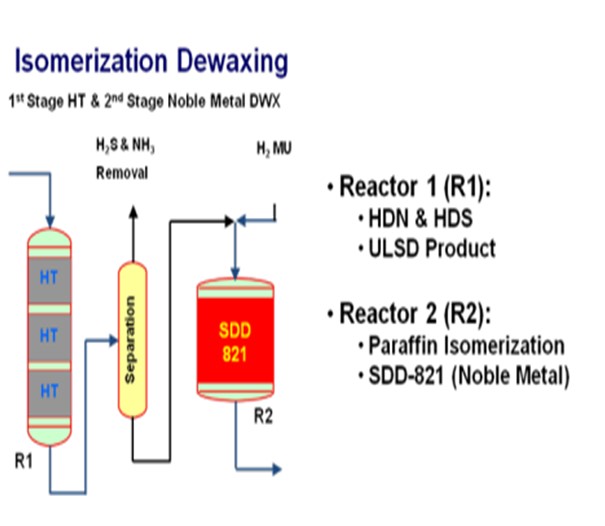
Effective dewaxing requires a proper differentiation between the linear paraffinic molecules (wax) and the rest of the feed molecules in order to achieve a high selectivity and to minimize distillate yield loss.
In hydrocracking, this can be achieved by employing a shape selective zeolite as the active acidic component to preferentially convert large linear paraffins. Criterion/Zeolyst has a Z-2000 series of shape selective cracking catalysts that selectively crack large linear paraffins resulting in an improvement in the product cloud point all along the activity/selectivity scale. These catalysts provide a boost in middle distillate yield versus conventional wide-pore zeolite catalysts due to the fact that the converted material has the tendency to remain in the distillate boiling range.
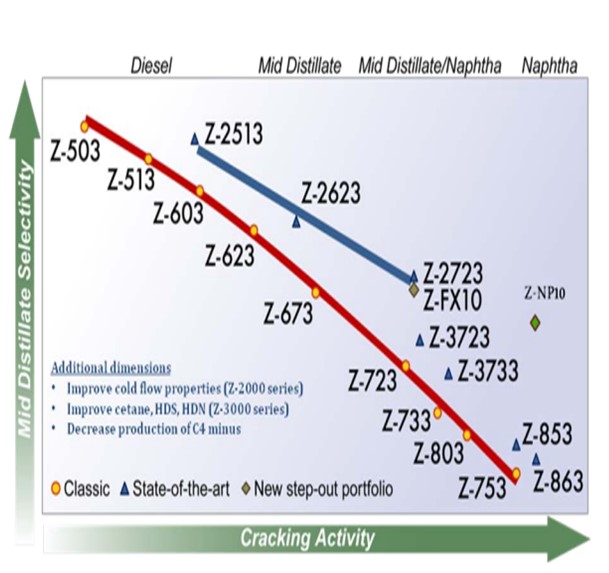
In mild hydrocracking applications, catalytic dewaxing can be employed at the back end of the upgrading process, where all other properties of the product (i.e., sulfur, nitrogen, aromatic content and cetane index) have already achieved the required target levels. Criterion has a number of distillate feed applications where a dewaxing catalyst, such as Criterion’s SDD-800, is loaded in the last bed of a single stage mild hydrocracker to improve cloud point while minimizing distillate yield loss.
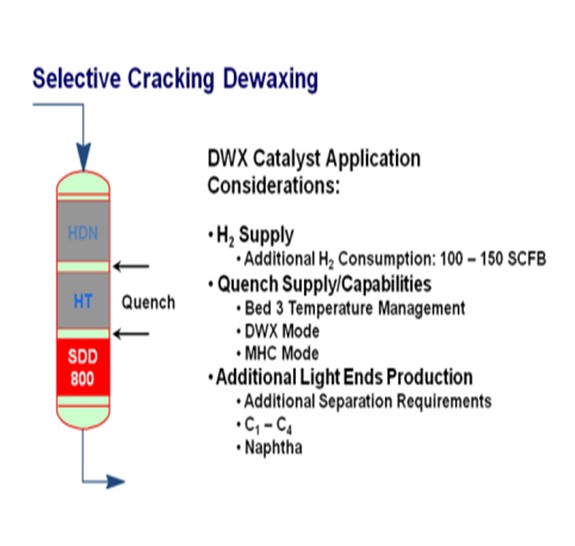
BODOLUS (CVR Energy)
Start with catalyst vendors for recent developments in their products and capabilities. Cold flow properties are a very complicated function of catalytic selectivity. Our refineries adjust cold flow properties seasonally at the crude unit via distillation specifications and monitoring run-down tank samples. No daily or seasonal adjustments are made to the hydrotreaters/hydrocrackers for cold flow parameters. Once the catalyst selection is made, the hydrotreating and fractionation is done to accommodate distillation, flash and sulfur targets. A point worth mentioning in our system is the rationalization of the economic interactions between competitive distillate products in the finished product pool. The desire to produce high margin seasonal products (#1 kero) or solvents (mineral spirits) often impact or overly constrain the diesel cold flow properties adjustments made at the crude units.
SUBHASH SINGHAL (Kuwait National Petroleum Company)
The easiest way to achieve better cloud point/CFPP could be to adjust fractionator operations to drop some heavy kerosene to diesel inside the column (within flashpoint specs limits).