Question 79: For units that have experienced elevated losses leading to coarse inventory, what options exist to improve catalyst properties during turnaround? Describe your experience with purchasing external or classifying spent catalyst.
RUSSEFF (CVR Energy, Inc.)
First, I would ask an additional question: Did you fix the problem during your turnaround activities that led to your coarse inventory and loss of the smaller particles? There are a lot of different paths to follow. The easy answer is to discard and purchase e-cat (equilibrium catalyst) that is correct for your average particle size and minimum fluidization velocity, which we have done. We have also put in a little fresh e-cat just to compensate for the abuse that it gets from the torch oil and activity; so when we start up, we will be more optimized, in terms of our blend.
Another option is to reload with your own saved e-cat: e-cat plus your fines. We have saved e-cat. Right now, one our units in Coffeyville is actually in turnaround, and we are looking into reloading with our own e-cat there. With units that have higher EPSs (electrostatic precipitators), you will have to blend something in order to blend down your particle size. Whether it comes from your plant internally or from the e-cat vendor is up to you.
I have seen the blending done, and I have seen the results. Some folks have spiked the reload of their e-cat with ESP hopper fines. Just a quick reminder: During startup, you are in flux; and for units that have problems with retention, be on the lookout for the fines, which tend to be visible quickly. I tend to avoid situations like that where we have those unnecessary and awkward conversations over the phone, so I would definitely not try that myself.
Another option is to adjust the APS (average particle size) by reclassifying the e-cat. We will get into more of that later. And then also, just because it came up, in terms of experience, reclassifying fresh cat is also an option. I will get more into that later. I apologize for the link on this, but it is a complicated issue.
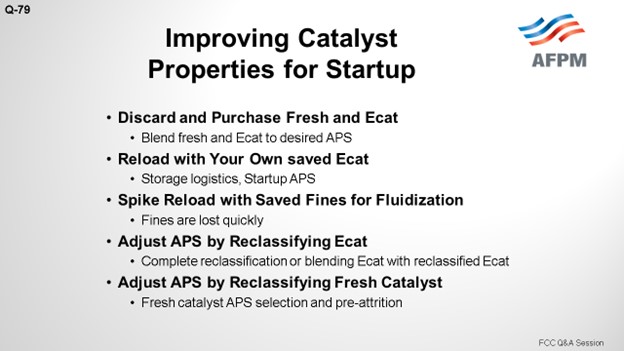
At CVR, we watch our historical data. You want to optimize your load as best as you can. So, in terms of watching the e-cat and fines analysis, for me, it is like cracking. I cannot not look at it when it comes in, but there is a lot more valuable information in there other than just particle size and distribution; and just because your unit shut down on your current e-cat and particle size does not mean that starting up on that material because the APS is too large. Obviously, you will hit the typical issue there of bridging off a dipleg because your velocity is below your minimum fluidization for startup.
The bottom line is that every FCC is different. Each licensor has different approaches to the operations around the unit. There are a number of very old units in services today. You end up with one brand of feed nozzles and another brand of regenerator in the reactor. So, consulting with the vendors or licensors is always good. In some units, I feel like we could start up on gravel and billiard balls, while other units are really sensitive to average particle size. So it is important to get the historical data and consult with the licensors, especially in the separation's technology, to make sure you are starting up on the right particle size and have the right distribution.
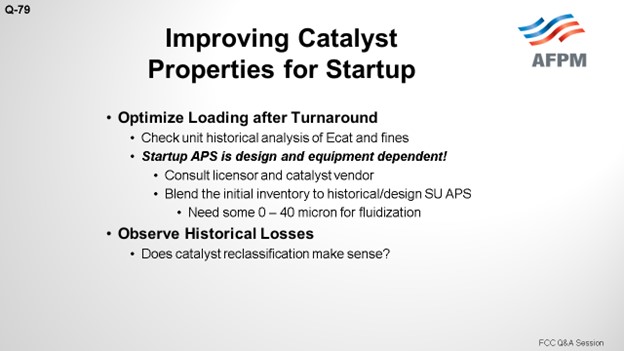
When, if ever, do you reclassify some of your loads? Some folks’ approach has been to observe that they lose all the zero-to-40 in their e-cat. So, they want to automatically just strip that out and say, “Oh, we do not need anything on startup.” Well, you still need some zero-to-40 for minimum fluidization velocity for your startup.
I think it is important to talk a little about reclassification because it is a newer topic and not at the forefront of everyone’s mind. A reclassification operation is important to understand because it gives us another tool. The more we understand about that tool, the more we can use it to our advantage. Typical reclassification just uses air as motor fluid running through the unit. I know I am oversimplifying this process; but if you are going to run through a set of a series of cyclones, adjust the velocity for the rejection. That is, it in a nutshell. So, if you do a zero-to-20 reject, you will still get some zero-to-20 particles. So, nothing is perfect, but we should understand the product.
If you are going to do reclassification, especially with your fines and e-cat, then you can choose between many different options. However, it is important to plan it in advance. We are currently reloading with our e-cat at our Coffeyville refinery, and we have managed to plan that well in advance. We set back the catalyst we need. If your average particle size is high compared to your minimum fluidization velocity for startup, you will have to blend that with some smaller particles; not necessarily the zero-to-20, but maybe somewhere in the 40 to 60 range, depending on the condition of your e-cat. Again, each unit is different. You have to plan for this.
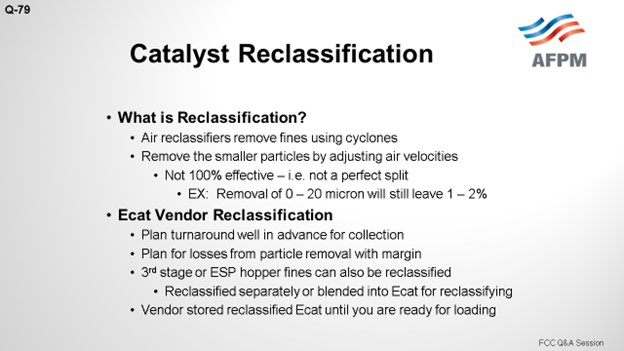
It can be as simple as reclassifying your third-stage or your ESP fines, but you also may need to do more, such as dumping your third stage and ESP fines into your bulk e-cat and sending it to your reclassifying vendor. Or you could set those aside and do them separately. There are quite a few different options available. What works best for you depends on which particles you actually need.
Again, a typical approach is collecting your third-stage or ESP fines and dumping that into your e-cat, running it through a re-classifier, and then rejecting the particles that are typically rejected by the unit. The ESP fines either come out in the flue gas or in your main column bottoms, such as a zero-to-20 cut on your combined e-cat fines plus your e-cat. That is one option; there are probably many more alternatives, depending on your needs.
We are looking at reclassification itself because some folks are starting to do that for a normal operation. The idea of removing the fines material and finest-generating material before it comes into the unit is a highly desired effect. Units struggle with loss problems. I think we have all done that at one time or another. Removing that material before it goes into the unit can also help units that have experienced high losses. It actually do damage to the downstream equipment, slurry pumps, slurry piping, and flue gas system and causes flue gas cooler erosion, expander erosion, and overloaded ESPs. There are a lot of great reasons to remove that high fines material from your catalyst.
Emissions can also be decreased, which was a highlight for us. Our interest in this option was sparked when we did our stack test. Reclassification did great, and we managed to do the testing without ammonia injection or pass on our ESP. We were close enough that in the future, or with different regulations, we may end up having to take some other actions, part of which may include reclassification.
Freshly manufactured catalyst has all the tips on it. Regardless of the vendor, you will always get some inconsistency. Some are better than others, and I will leave that to you guys to debate. So, all of this imperfection breakoff is the major source of fines.
Additionally, during some catalyst manufacturing processes, you get some agglomeration of the larger particles. The air reclassifier is essentially the same as our separation's technology inside our unit except that it is not being done in our unit, which makes it highly attractive. The reclassification cyclones knocked off these tips and made more uniform particle size, essentially pre-tripping the catalyst. The normal source of fines that would leave the FCC unit from your regenerator and your main column bottoms are essentially limited or reduced prior to being introduced to the unit.
The air reclassifier: Our vendor, with whom I have been discussing this for reclassification of our fresh catalyst, also said that the agglomerated particles have a tendency to break off and round off, so you will get a gradual reduction in fines and a more even-sized distribution. That all sounds attractive, but nothing comes free, especially for us. So the other caveat, in addition to the increased cost, is that you will lose some of your purchased catalyst to the fines generation as a result of reclassifying.
I do not know the actual losses. However, after talking about this problem with other people, I came up with some questions that could help us in the future. It would be nice to see the reclassifiers run a couple loads of fresh catalyst from the catalyst vendors side-by-side to determine the actual attrition and calculate the particle size distribution before and after each run. The results would be very interesting for those of us in the industry who could really use that information. Due to emissions and pump erosion, maybe the future is getting a pass through a reclassifier before it actually gets to us. I do not know the effects on it yet, but it is certainly something that could be investigated.
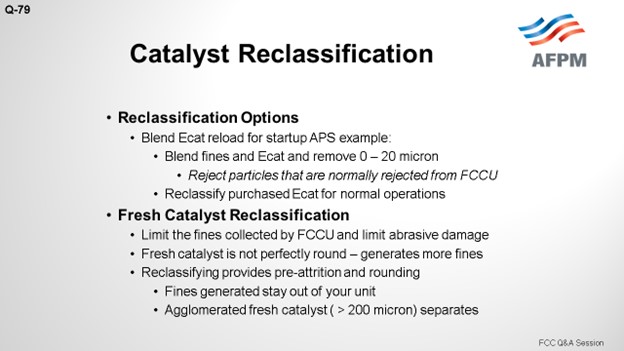
FOSHEE [Shell Global Solutions (U.S.)]
That was a fairly complete answer. I will just add that Shell has experience with operating units for an extended period with elevated catalyst losses when the unit is close to turnaround: six to nine months away. When catalyst losses increase, the number of fines in the circulating catalyst decreases more than the other fractions, which reduces the ability of the catalyst to stay fluidized. During these times, Shell used a combined approach of additives, purchased e-cat with high fines content, or a fluidization aid in conjunction with the modification of the fresh catalyst for its particle size distribution (increasing the fines content of the fresh catalyst). This particular approach helped maintain fluidization before the turnaround and keep acceptable fines content, even during restart. After a startup, Shell has stopped the use of additives but has kept the high fines content fresh catalyst addition for several months in order to ensure that proper e-cat fines are maintained.
One of our FCC units has used another approach. This particular unit has a third-stage separator with a fourth-stage separator and hopper. The unit will periodically send the fines from the fourth-stage separator hopper back to the e-cat hopper, which results in alternating layers of e-cat and fourth-stage separator fines. At turnaround, when they are ready to put their e-cat back in the unit, they hire a third-party contractor to come and take the contents of their e-cat hopper and reclassify it to a specified particle size distribution; in particular, remove the zero-to-20 material.
REBECCA KUO (BASF Corporation)
Another option for units experiencing elevated losses is to use an additive that contains a high percentage of 20- to 40-micron material, such as EZ-Flow. Cyclones are typically designed to retain particles larger than 20 microns, so reintroduced microfines (0- to 20-micron material) from the ESP will just go back out the stack, and the coarse inventory would still remain an issue. Depending on how much additive is charged into the unit, the unit could see a 2 to 4 lb/ft3 (pound per cubic foot) drop in density in the standpipe and a 1- to 2-number increase in the Umb/Umf (minimum bubbling velocity to minimum fluidization velocity) ratio. Additionally, using an additive is a flexible option because once the elevated losses have decreased, the refinery can simply stop using the additive and move back to normal operation.
RYAN NICKELL (Albemarle Corporation)
I want to comment on the use of the fluidization additives. It is particularly advantageous to utilize an additive that has active cracking components in it. If you do that, you can certainly utilize aggressive injections to keep the unit up and running without dilution effects. Albemarle offers the SMOOTHFLOW™ product, which is described in the Answer Book.
ADAM KASLE (BP Products North America Inc.)
I have had experience with a couple of units that have had loss problems during operation which resulted in a loss of fines and an increase in average particle size. These units eventually shut down for one reason or another. When they tried to restart, we saw significant catalyst losses because of the poor particle-size distribution. I agree with what other people have said about using these additives, which you can probably get from any of the vendors. These additives provide a good option for quickly increasing the 20-to-40-micron particle content of the inventory to regain the fluidization properties, which are very important to keep the cyclones – and especially the secondary cyclone diplegs – fluidized during startup. If you are just buying e-cat from someone or buying fines, specifically, you will need to either consider classifying the catalyst or looking closely at the source. You certainly do not want to add a lot of zero-to-20-micron fines to the unit.
I worked with one unit that added an e-cat that someone had combined with ESP fines before selling it. The e-cat had a high zero to 40 fines content, which the refinery thought would be good, but most of this was less than 20 microns. The microfines in the purchased e-cat could not be retained by the reactor cyclones, so this material ended up in the bottom of the main fractionator and almost immediately plugged the slurry filter.
WARREN LETZSCH (Technip USA)
We get fixed on how much 0-to-40 micron catalyst is in the inventory. You need 10% to run the unit well. And as Bob Flanders used to say, “Purgatory was trying to run a Model IV with less than 10% fines in it.” What I would suggest is certainly nothing smaller than 20 microns. But frankly, if you did add 20- to maybe 60-micron catalyst, you would reduce the average particle size and find that your average particle size. The very larger particles – those over 100 microns – that are building up in the inventory will really start causing fluidization problems.
The advantage of taking out the 0-to-20 micron material is that you are likely to retain a lot more of this lighter or smaller catalyst that you were putting in. In my ideal world, I live in a place where you would have an FCC unit so tight that the average particle size would be 55 or 60 microns, which would circulate very well, and the bubbles would be smaller in the stripper and regenerator.
FOSHEE [Shell Global Solutions (U.S.)]
That was a fairly complete answer. I will just add that Shell has experience with operating units for an extended period with elevated catalyst losses when the unit is close to turnaround: six to nine months away. When catalyst losses increase, the number of fines in the circulating catalyst decreases more than the other fractions, which reduces the ability of the catalyst to stay fluidized. During these times, Shell used a combined approach of additives, purchased e-cat with high fines content, or a fluidization aid in conjunction with the modification of the fresh catalyst for its particle size distribution (increasing the fines content of the fresh catalyst). This particular approach helped maintain fluidization before the turnaround and keep acceptable fines content, even during restart. After a startup, Shell has stopped the use of additives but has kept the high fines content fresh catalyst addition for several months in order to ensure that proper e-cat fines are maintained.
One of our FCC units has used another approach. This particular unit has a third-stage separator with a fourth-stage separator and hopper. The unit will periodically send the fines from the fourth-stage separator hopper back to the e-cat hopper, which results in alternating layers of e-cat and fourth-stage separator fines. At turnaround, when they are ready to put their e-cat back in the unit, they hire a third-party contractor to come and take the contents of their e-cat hopper and reclassify it to a specified particle size distribution; in particular, remove the zero-to-20 material.
REBECCA KUO (BASF Corporation)
Another option for units experiencing elevated losses is to use an additive that contains a high percentage of 20- to 40-micron material, such as EZ-Flow. Cyclones are typically designed to retain particles larger than 20 microns, so reintroduced microfines (0- to 20-micron material) from the ESP will just go back out the stack, and the coarse inventory would still remain an issue. Depending on how much additive is charged into the unit, the unit could see a 2 to 4 lb/ft3 (pound per cubic foot) drop in density in the standpipe and a 1- to 2-number increase in the Umb/Umf (minimum bubbling velocity to minimum fluidization velocity) ratio. Additionally, using an additive is a flexible option because once the elevated losses have decreased, the refinery can simply stop using the additive and move back to normal operation.
RYAN NICKELL (Albemarle Corporation)
I want to comment on the use of the fluidization additives. It is particularly advantageous to utilize an additive that has active cracking components in it. If you do that, you can certainly utilize aggressive injections to keep the unit up and running without dilution effects. Albemarle offers the SMOOTHFLOW™ product, which is described in the Answer Book.
ADAM KASLE (BP Products North America Inc.)
I have had experience with a couple of units that have had loss problems during operation which resulted in a loss of fines and an increase in average particle size. These units eventually shut down for one reason or another. When they tried to restart, we saw significant catalyst losses because of the poor particle-size distribution. I agree with what other people have said about using these additives, which you can probably get from any of the vendors. These additives provide a good option for quickly increasing the 20 to 40 micron particle content of the inventory to regain the fluidization properties, which are very important to keep the cyclones – and especially the secondary cyclone diplegs – fluidized during startup. If you are just buying e-cat from someone or buying fines, specifically, you will need to either consider classifying the catalyst or looking closely at the source. You certainly do not want to add a lot of zero to 20 micron fines to the unit.
I worked with one unit that added an e-cat that someone had combined with ESP fines before selling it. The e-cat had a high zero to 40 fines content, which the refinery thought would be good, but most of this was less than 20 microns. The microfines in the purchased e-cat could not be retained by the reactor cyclones, so this material ended up in the bottom of the main fractionator and almost immediately plugged the slurry filter.
WARREN LETZSCH (Technip USA)
We get fixed on how much 0-to-40 micron catalyst is in the inventory. You need 10% to run the unit well. And as Bob Flanders used to say, “Purgatory was trying to run a Model IV with less than 10% fines in it.” What I would suggest is certainly nothing smaller than 20 microns. But frankly, if you did add 20- to maybe 60-micron catalyst, you would reduce the average particle size and find that your average particle size. The very larger particles – those over 100 microns – that are building up in the inventory will really start causing fluidization problems.
The advantage of taking out the 0-to-20 micron material is that you are likely to retain a lot more of this lighter or smaller catalyst that you were putting in. In my ideal world, I live in a place where you would have an FCC unit so tight that the average particle size would be 55 or 60 microns, which would circulate very well, and the bubbles would be smaller in the stripper and regenerator.