Question 78: Under what conditions do gasoline sulfur reduction additives and catalysts reduce sulfur in gasoline, and by how much? What is the lowest gasoline sulfur level for which the gasoline sulfur reduction products are effective? At this gasoline sulfur level, please quantify the gasoline sulfur reduction and the amount of additive/catalyst required.
LARSEN [Marathon Petroleum Corporation (MPC)]
That is a very long breath of a question. [Laughter] I will summarize some of the Marathon’s findings on gasoline sulfur reduction additives. We have done a lot of testing in our pilot plant in the past. Some of that has already been presented. You can reference Jeff Sexton’s response to Question 46 of the FCC session of the 2009 AFPM Q&A Question if you want to see a little more data. But in general, we already mentioned our pretreat/post-treat scenarios and went over how gasoline sulfur reduction additives work. I will hit on the mechanism of how we believe they work, some of the variables that would impact their performance, and then some of our more recent testing and applicability at already low gasoline sulfur levels.

In terms of the mechanism, in our pilot plant testing, we have seen that recombinant reactions play a large role. So, no matter what feed sulfur species end up going into pilot plant, we get the same gasoline sulfur species coming out the back end, thereby emphasizing that the recombinant reactions in the riser play a large, dominating role in generating gasoline sulfur species. The additives we tested, for the most part, will crack the gasoline sulfur species into H2S. We charted a few of them on the slide. I believe there is other technology that will move the sulfur down into coke.

Several variables can cause an effect. Bart already mentioned vanadium as being one of them. There is a trend on the next slide showing one of our units with operation at low and high vanadium levels and the impact on the gasoline sulfur to feed sulfur ratio. You can see it is very significant. We have done testing with nitrogen and have also noticed big effects in the gasoline sulfur. In general, we have tried many types of gasoline sulfur reduction catalysts and found two that worked well for us. It is important to recognize the importance of balancing the ability of the GSR (gasoline sulfur reduction) to reduce sulfur without having any adverse yield impacts.

We have done economic modeling and confirmed the pilot plant testing with actual unit post-audits to find additives that work best for us, and we have then gone on to do some of our testing recently at already low gasoline sulfur levels.

On the next slide, I apologize for the scale being cut off on the left-hand side, but I believe it just goes from zero to 8 ppm. Those are all different sulfur speciation concentrations of the different molecules. You can see that the gasoline sulfur we are starting at is 20 ppm. This is full range gasoline sulfur concentration.
We have seen about the same reduction in gasoline sulfur that was previously seen when starting with higher levels of gasoline sulfur. So, it appears that the additives we have tested worked in about the same range, even when starting with less gasoline sulfur or reloads. I know the trend is a little busy. There are a couple of data points shown: a base case, a max desulfurized FCC feed case, and then a couple cases with additive that show the incremental reduction in gasoline sulfur.

DE GRAAF (Johnson Matthey Process Technologies)
Additives can help to reduce gasoline sulfur 20 to 35%, but they cannot perform miracles. Their performance depends on how much hydrogen transfer is already present in the system. There are various contributing factors to the success of this reduction.
I visited a refinery in China which had two different FCC units. They processed the same feed and used the same base catalyst. However, one was a unit that had a sort of fluid bed in the unit, and the other was more of a typical side-by-side FCC unit. At similar conversion level, the unit that had a sort of fluid bed in the riser had 35% less sulfur in gasoline due to the huge spent catalyst recycle caused by the fluid bed.
The base catalyst contributes to hydrogen transfer as well. You can optimize the amount of rare earth. The rarer earth you put in the catalyst, the higher the acid site density in the zeolite, which will result in more hydrogen transfer. A high alumina catalyst helps reduce sulfur; and like I mentioned before, high vanadium levels also help to reduce gasoline sulfur.
Another factor is how much hydrogen the feed brings in itself. If there is a lot of hydrogen transfer from the feeds, the performance of the gasoline sulfur additive will be affected. It will be more of an uphill battle than if there is a low amount of hydrogen transfer caused by the feed. Mercaptans, thiophenes, or hydrothiophenes are easier to remove than benzothiophenes. Typically, you would use about 10 to 20% of gasoline sulfur additive in on inventory, but we have seen that gasoline sulfur additives are effective over a very wide range of applications.
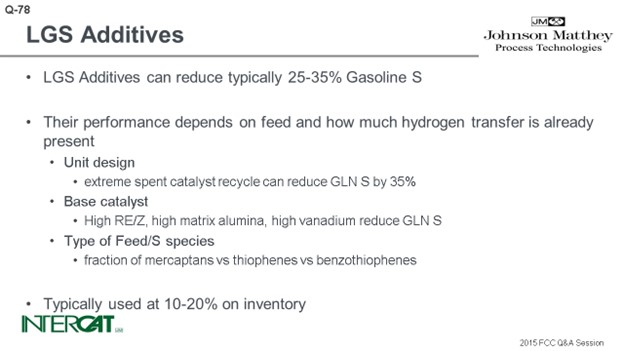
MELISSA CLOUGH (BASF Corporation)
I will just add a couple more comments. Both Nik and Bart did a good job talking about a number of key aspects, including speciation. It is important to understand how or what kind of game plan you need, in terms of gasoline sulfur reduction additives. So, the usage of the additive, like Bart said, is about 10 to 20%. Another point to consider is preblending, so we can avoid diluting the base catalyst.
And then, Nik did mention part of that question that asks: When you already have low sulfur in the gasoline, what kind of reduction is still possible when using these additives? We just saw some testing results from Nik.
I want to add another story from the refinery experience side. Some of our customers in Japan are running very low sulfur feeds and treating gasoline sulfur reduction additives and are still seeing around 20% reduction. So even at already low gasoline sulfur, further reduction is still possible.
COLIN BAILLIE (Grace Catalysts Technologies)
Grace’s gasoline sulfur reduction (GSR®) additives are effective under a wide range of operating conditions in the FCC unit. There have been numerous case studies and references supporting the robust performance of GSR® technologies in which 20 to 40% gasoline sulfur reduction has been observed for a wide range of:
• Feed types,
• Feed sulfur levels, and/or
• Gasoline sulfur levels.
Grace’s GSR® technologies are particularly effective for removing mercaptans, sulfides, tetrahydrothiophenes, and thiophenes in gasoline. Benzothiophenes are harder to remove, while dibenzothiophenes generally remain unaffected under FCC operating conditions. Therefore, a key factor in determining the actual level of gasoline sulfur reduction is the identification of the sulfur species present in the gasoline. Figure 1 shows gasoline sulfur species distributions for various non-hydrotreated feeds (U1-U3) and hydrotreated feedstocks (H1-H3). All of the gasoline streams contain the same types of sulfur species, although their distribution varies. Grace’s GSR® technologies would result in gasoline sulfur reduction for all of these streams, though higher reductions would be observed for those containing a lower proportion of benzothiophenes, highlighting the suitability of GSR® technology for various feed types.
Feed sulfur type plays a bigger role than feed sulfur content in the level of gasoline sulfur reduction observed. Multi-ring aromatic thiophenes in the feedstock will not contribute to sulfur species in the FCC gasoline, so they have little impact on subsequent GSR® performance. In contrast, alkylbenzothiophenes in the feedstock undergo dealkylation resulting in benzothiophenes in the gasoline. These are harder to remove than the thiophenes, sulfides, and mercaptans that result from the alkylthiophenes and cyclic sulfides in the feed. Therefore, although Grace’s GSR® technologies will provide gasoline sulfur reduction for all feedstocks, those with a higher proportion of alkylthiophenes compared to alkylbenzothiophenes will see a greater gasoline sulfur reduction.
Removing thiophenes is a key part of gasoline sulfur reduction, the reaction pathway of which is shown in Figure 2. The FCC catalyst component catalyzes the hydrogen-transfer (HT) reactions between thiophenes and tetrahydrothiophenes (THT). GSR® technology works by increasing the cracking of THT into hydrocarbons and hydrogen sulfide.
Figure 2: Thiophene Reduction Reaction Pathway
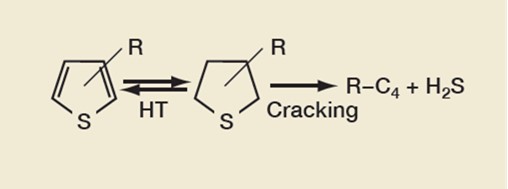
Any conditions that promote HT reactions are likely to be favorable for gasoline sulfur reduction. These include reduced riser temperature and increased pressure, as well as a catalyst with an optimized unit cell size, though this play less of a part than feed sulfur species. This is highlighted by the current users of Grace’s GSR® technologies that are achieving high levels of gasoline sulfur reduction operating under the following various conditions:
-
Riser Temperature: 965°F to 995°F
-
Feed Preheat Temperature: 430°F to 625°F
-
Cat-to-oil: 6 to 10 weight catalyst to weight of oil
-
E-cat Unit Cell Size: 24.27 to 24.32 Å
When considering the lowest gasoline sulfur levels for which GSR® products are effective, there are many interesting case studies from Japanese refiners who are producing gasoline with less than 10 ppm sulfur. In addition, many of these refiners operate their feed pretreater unit very severely, resulting in low FCC feed and gasoline sulfur levels. One such refinery had average gasoline sulfur levels of 13 ppm prior to the use of GSR® technology. After switching to Grace's SuRCA® catalyst technology, the refinery managed to achieve upwards of 30% reduction to control gasoline sulfur levels to below 9 ppm. SuRCA® is a tailored catalytic solution for gasoline sulfur reduction and is used as 100% drop-in replacement of the previous base catalyst, with no increase in catalyst addition rates required.
BART DE GRAAF (Johnson Matthey Process Technologies)
When additives are used in FCC to reduce gasoline sulfur, they typically reduce the sulfur content by 20 to 35%. Performance of gasoline sulfur additives depends on many variables: feed, unit design, and operation and catalyst composition. They are typically used at levels of 10 to 20% in inventory.
The type of sulfur species in feed and gasoline is important. Additives are more successful when the fraction of aromatic sulfur species in feed is lower. Sulfur from mercaptans, thiophenes, and hydrothiophenes is easier to reduce than that of benzothiophenes. Therefore, the gasoline cutpoint is an important parameter when determining the overall effect of gasoline additives. Because of the distribution of sulfur species over gasoline boiling range, additives are more successful at lower gasoline cutpoints.
Unit design can affect gasoline sulfur as well. Experiments have shown that in cases of extreme spent catalyst recycle (approaching bed cracking), gasoline sulfur can be reduced up to 35%.
Catalyst design can help mitigate gasoline sulfur. Hydrogen transfer helps reduce gasoline sulfur; therefore, catalysts containing high rare earth USY show lower gasoline sulfur. Separately, boehmite matrix has some tendency to reduce gasoline sulfur, too. Vanadium has some sulfur-reducing tendencies as well. If the catalyst contains high rare earth stabilized zeolite and high matrix content and is high in vanadium, gasoline sulfur additives will typically be less effective than for high zeolite catalyst with low rare earth stabilization and low matrix content. Some refiners have tried e-cat from resid operations as a sulfur reduction additive, as this e-cat typically contains all of the above. Sulfur in gasoline is reduced by using this e-cat; however, at the expense of other yields such as coke and dry gas. In the design of sulfur reduction additives, the functionality of sulfur reduction is optimized, whereas potential side effects are substantially reduced or eliminated.
NIKOLAS LARSEN [Marathon Petroleum Company (MPC)]
In a post-Tier 3 environment, MPC will have three units that will rely on cat feed hydrotreating (CFH) and four units with post-treaters (Prime-G) to meet gasoline sulfur targets. GSR additives have been used on four units with CFHs during catalyst change outages. GSR products from all vendors have been evaluated in our pilot plant. We have conducted commercial trials with three vendors and have extensive experience with two vendors. MPC has presented significant data in previous AFPM meetings (see Question 46 from 2009 AFPM Q&A) but will summarize here since it has been several years.
MPC’s pilot plant has been utilized to help understand the chemistry surrounding gasoline sulfur and additives. A few important findings resulted from our pilot plant studies:
-
Recombinant reactions of H2S and olefins in the riser play a predominant role.
-
Sulfur species in feed and gasoline are different.
-
FCC feed sulfur compounds have different conversion reactivities. Basic nitrogen lowers the conversion.
-
This effect is apparent from FCC feed studies with nitrogen spiked components
-
Identification of where sulfur goes when removed from FCC gasoline is vital.
The majority of GSR products we have evaluated crack up feed sulfur into the different species in the product sulfur. The chart below shows the distribution with different GSR products. The majority of the gasoline sulfur goes to H2S. However, there are other technologies that can do the opposite where you can move the sulfur into coke sulfur.
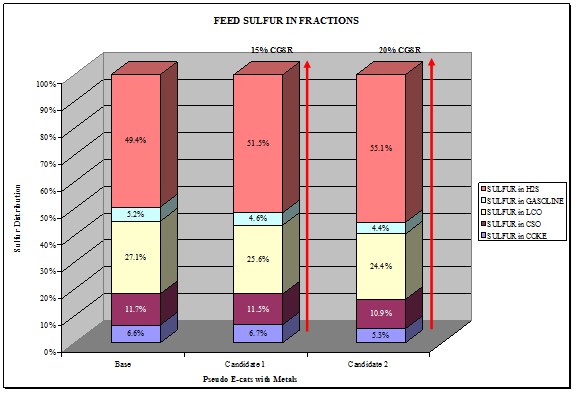
Vanadium on e-cat is an important variable affecting gasoline sulfur. The data shows the two base operations which represent a typical range of e-cat vanadium. The data points represent three GSR products from two vendors. Performance has resulted in a 20 to 25% reduction in gasoline sulfur. This unit has used a GSR additive for 10 years.
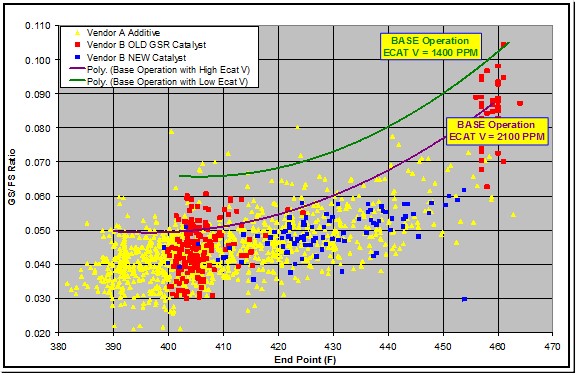
In addition, we evaluated the impact of different feeds and combinations of vendor additives in the pilot plant. An additive and catalyst system were evaluated separately and then combined. Both were based upon different technologies, and the hope was that they would be additive. This theorem was evaluated with four different feeds. The rankings will vary depending upon the feed type. However, we did not find a synergy combining vendor products.
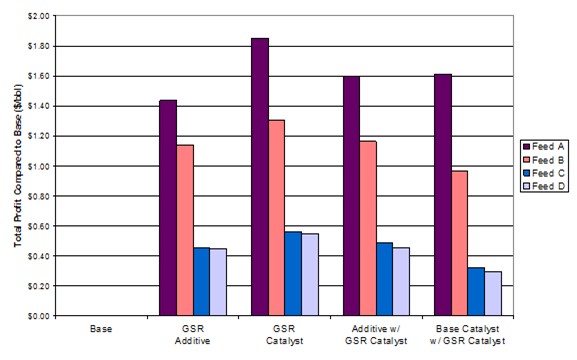
It is important to understand all aspects of GSR additives. Some candidates demonstrate great GSR reduction but also have a coke selectivity penalty. MPC has had success with a compromise between GSR and yields and bases decisions upon overall economics. For the case below, the pilot plant predicted a 17% reduction with a 20% reduction seen commercially. A post-audit of the yields confirmed the pilot plant prediction.
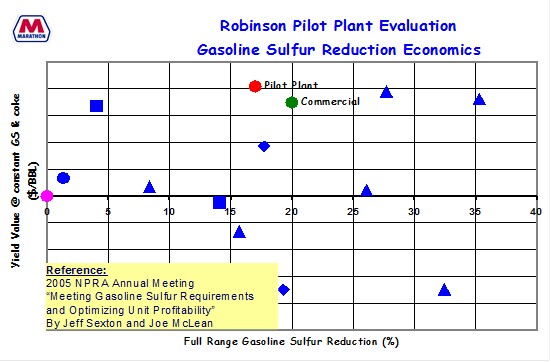
MPC has demonstrated that a 20% gasoline sulfur reduction is possible on multiple units with different applications feeds. We have evaluated various vendor products and seen that some have worked; some have not. We found two products that we have used successfully commercially.
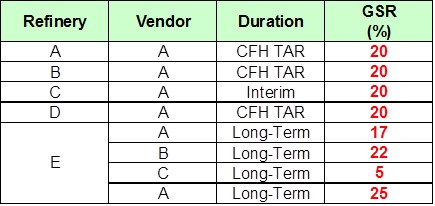
Given the lack of intensive research into GSR technology and a lack of trials on units with low feed sulfurs, MPC investigated the impact of GSR additives on already low sulfur gasoline. The study utilized additives at 30 wt% since the initial driver was to see if we could get a measurable response at very low base gasoline sulfur levels. As you can see, this study demonstrated more than 25% sulfur removal at this low-range base sulfur with two different additives. A challenge in studying such small levels of gasoline sulfur is measurement of the different sulfur species, many of which are less than 1 ppm.
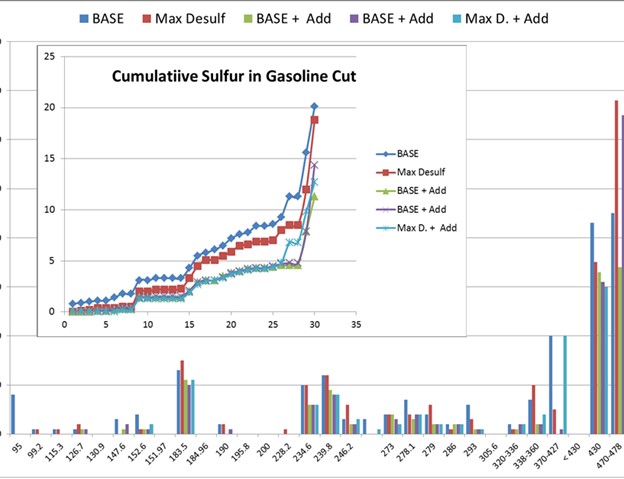
MELISSA CLOUGH (BASF Corporation)
Gasoline sulfur reduction additives are a convenient method used to get gasoline sulfur levels closer to or meeting Tier 3 standards. This is an important consideration since 90% of the naphtha sulfur typically comes from FCC naphtha. The amount of removable sulfur depends on whether or not the FCC feed is hydrotreated. With hydrotreated feed, the sulfur in the gasoline cut is typically lower, but the sulfur that remains is more difficult to remove (aromatic sulfur). On the other hand, non-hydrotreated feed contains more sulfur, but that sulfur is easier to remove. Typically, saturates, mercaptans, thiophenes, and alkylthiophenes see good or reasonable conversion to H2S or coke with the use of an additive. Benzothiophenes, although present in lower quantities than other species, have much lower conversion rates and are harder to remove. Sulfur removal from benzothiophene of 15% or less is common with an additive. Overall, when looking at the entire sulfur species in FCC naphtha, an average of about 20 to 40% reduction across the entire boiling point range can be achieved with gasoline sulfur reduction additives. Typical loading is about 15 to 25% of the base catalyst. Additives can be synergistically combined with the base catalyst formulation to minimize activity loss via dilution effects.