Question 77: When relying primarily on FCC feed pretreating to meet FCC gasoline sulfur specifications (current or future Tier 3), how do you manage feed pretreater outages?
LARSEN [Marathon Petroleum Corporation (MPC)]
Marathon relies on feed pretreating for three of our FCCs, which will all continue post-Tier 3 regulation implementation. Looking at the difference between Tier 2 and Tier 3, we see that when the annual average ppm in gasoline goes down from 30 to 10, the maximum per gallon, I believe, does not change from 80. So technically, you would not have to change how you currently handle your cat feed hydrotreater outages, but I think I would put some numbers to it. If you run 10 ppm and take a four-week FCC feed pretreater outage, you will have to run about 4 ppm for the rest of the year to make up for it, which is challenging.
I pooled our refineries and gathered our experience. On the slide, you can see what we plan to do. In a few of our cases, we have invested in some additional reactor volume to be able to have minimal impact on the FCC. In general, painting in a rather broad stroke, undercutting and gasoline sulfur reduction additives are not generally part of our normal operation strategy to comply with Tier 3. All of our refineries will be able to make 10 ppm gasoline to generate credits, which is also an option.
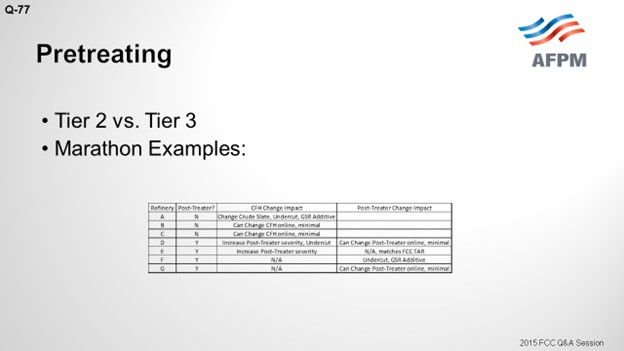
REYNOLDS (Phillips 66)
I currently live in this situation right now. We totally rely on pretreating to meet our FCC gasoline sulfur. We try to have several days’ worth of minimum FCC rate in tankage. In case there is a little upset with the gasoline hydrotreater, we could keep the FCC running. If there is a major outage, we have to manage our tankage. That is really our only option. We are in an isolated area, so we cannot export gasoil. Lastly, we are very aggressive. If there is an issue with that gasoline hydrotreater, we will cut the rate in the FCC quickly just to try to stay ahead of it and give us all the time we can to keep running.
RAMA RAO MARRI (CB&I Lummus Technology)
I have one comment. Normally, more and more FCCs are operating with the feed preheater. So, we recommend considering that over 10% of the feed coming from the feed hydrotreater will go to the tank for handling emergency situations under Tier 3. Without the feed preheater, it is difficult to maintain the gasoline sulfur requirements. Instead, having 10% of the feed go to the tank and stored for a couple of days would help you ease out of the situation and still maintain the refinery gasoline sulfur limits.
COLIN BAILLIE (Grace Catalysts Technologies)
Refiners have created operating flexibility during hydrotreater outages by utilizing Grace’s clean fuels GSR® additive technology as a part of their short-term operating strategy. Proper management of FCC feed hydrotreater outages becomes increasingly important as more and more refiners rely on hydrotreating to meet their per-gallon gasoline sulfur limits. Running at higher severity increases the frequency of turnarounds. Conventional methods of ensuring that the gasoline pool stays below the sulfur limit during the hydrotreater turnaround are purchasing low sulfur feed or reducing FCC throughput. Either approach can significantly reduce refinery profitability. An alternative is to use one of Grace’s gasoline sulfur reducing technologies during the outage to provide operational flexibility while maintaining sulfur compliance and profitability.
One such example of a refiner who used Grace’s GSR® 5 sulfur reduction additive during a feed hydrotreater outage is shown in Figure 1. The refiner was able to process higher than typical feed sulfur and maintain gasoline pool sulfur compliance. Use of GSR® 5 began two months prior to the 45-day feed hydrotreater outage. During that time, feed sulfur increased by as much as 35%. The three periods represented are typical operation (Base Period), GSR® 5 before and during the outage where gasoline sulfur reduction ranged from 20 to 25%, and finally GSR® 5 following the outage. The customer estimated that use of GSR® 5 netted $1.7 million of savings during the hydrotreater outage. The results were so encouraging that the customer elected to continue using GSR® technology, switching to a SuRCA® catalyst and operating with post-outage feed sulfur 10 to 15% higher than the typical operation. This change to their operation grew annual profits by approximately $8 million.11
Figure 1: GSR® 5 delivered 25% gasoline sulfur reduction during a feed HT outage
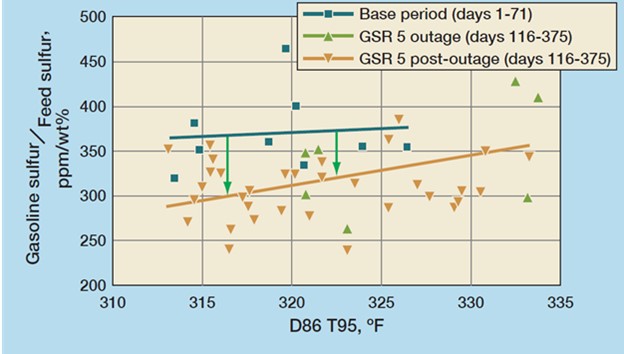
Grace’s clean fuels technologies include D-PriSM® and GSR® 5 FCC additives, as well as SuRCA® FCC catalysts, which are the result of almost two decades of innovation. Grace’s clean fuels technologies have been used in more than 100 FCC applications worldwide delivering 20 to 40% sulfur reduction in FCC naphtha in both full- and partial-burn operations. The D-PriSM® and GSR® additive technologies are used at a 10 to 25% loading in inventory, whereas the catalytic solutions are a customized 100% drop-in replacement for your base catalyst. Grace’s clean fuels technologies allow for a truly customized solution for the management of feed pretreater outages, or the compliance of environmental regulation.
NIKOLAS LARSEN [Marathon Petroleum Company (MPC)]
The maximum per-gallon sulfur specification of 80 ppm does not change with Tier 3, but the annual average drops from 30 to 10 ppm. Since the per-gallon cap does not change, in theory, Tier 3 does not change how FCC feed hydrotreater (CFH) outages are handled. However, Tier 3 will require operation at less than 10 ppm sulfur to meet the annual average target if the CFH is down. For example, if you ran at the 80 ppm gasoline sulfur limit for a four-week CFH outage, you would need to average 4.2 ppm the rest of the year to meet the 10 ppm pool average. All MPC refineries plan to achieve less than 10 ppm gasoline pool sulfur during normal operation and will generate credits which will be used to offset CFH and gasoline post-treater outages.
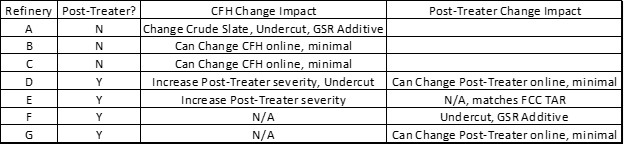