Question 75: What are your Best Practices in design and operation to achieve positive isolation of slurry/HCO equipment?
DINKEL [Marathon Petroleum Corporation (MPC)]
The hazards of your slurry and HCO system include the fact that you get hot oil operating close to auto-ignition temperatures. If it is released, there is a risk of it lighting off, as well as the risk of exposure to personnel. The crux of the question is really around maintaining or confirming positive isolation so you can access the equipment and conduct maintenance activities.
Some Best Practices: If you had a clean sheet of paper, you would do double-block-and-bleed; however, most units do not have that configuration. That design would not have been installed years ago. It is very congested underneath the main fractionator and rather expensive to go in and retrofit the slurry circuit with additional valves. So, if you have the opportunity and are already making some piping modifications, you should minimize pipe lengths and get rid of dead legs in that system that would allow areas for solids to accumulate. You will also need to be cognizant that you have sufficient space in there to provide access for the Maintenance workers to come in, do their job, and have a good regress from the area.
You want to have flushing connections to valves, as well as piping. For valves, the connection should be right on the seat, in case you get solids buildup in the seat. You should also have connections that can be hooked up with LCO to try to clear plugging. We like to try to have the valve stems in the vertical position because they keep solids from potentially accumulating up around the bonnet area.
My last point is from an operational standpoint. If the valve is not holding, the field operators will cycle it open and closed to vary the velocity across the seat of the valve and try to sweep out any solids that will have accumulated.
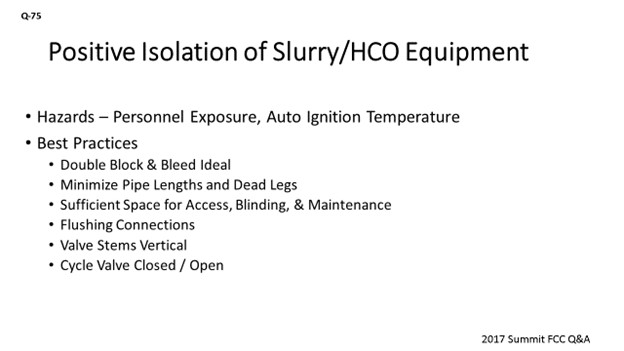
DARIN FOOTE (CHS Inc.)
The following are some important principles of design and operation that will help ensure positive isolation of heavy oil circuits in the FCCU main fractionator system.
Principles of Design
-
Proper Line Sizing: Maintaining an operating velocity of 4 to 10 fps is important for circuits on the discharge side of pumps. On the suction side of pumps, a velocity of 3 to 5 fps is desired. Keeping the velocity elevated will help prevent slurry deposits in valve seats.
-
Double Isolation: Where geometries allow, consider double block and bleed connections and make provisions for blinding.
-
Minimize Dead Legs: Locate the isolation valves for pumps as close to the continuously flowing line as practicable, preferably fitting makeup if stress allows. Also avoid geometries that are prone to catalyst settling out.
-
Flush Connections: Make provisions for flush connections on the bottom of the line – on both sides of equipment that is routinely isolated – within the block valves. Ensure that these connections can be cleaned with a straight bleeder cleaner.
-
Valve Selection:
-
Gate valves are the most robust and common in this service. 5Cr-0.5 Mo with API Trim #8 with the stem mounted in the horizontal where possible. There is no complex mechanism, and you can beat on the seat and stem to get them to seal.
-
Flush-Ported Gate Valves: Some have used these with mixed success.
-
Triple-Offset High-Performance Butterfly Valves: We have one of these in service as an emergency isolation valve from the main column to the slurry pumps. We have never had to use it, nor have we made a complete run with it yet. On our next shutdown, we plan to test this valve.
-
Wedge Plug Valves: These have a proven track record in slurry and coker service. The design ensures that the seat remains clear. Some designs, however, require steam purge; so, be cautious if using them in pump suction applications. These valves usually must be sent off for repair since most sites do not have the expertise to work on them. If the timing mechanism is not set properly, the valve will not seat.
Principles of Operation:
-
Exercise the valve as you close it. Open and close against the seat multiple times as you are isolating equipment. This action allows the seat to be exposed to higher velocities just before closing off. In cases of pump suction and discharge where this is not possible, utilize pump seal flush and/or other flush connections to generate flow across the seat.
-
Monitor isolation while steaming. There have been incidents in our industry where initial isolation was thought to be complete. After steaming the circuit, the catalyst in the seat of the valve breaks free and causes a loss of containment.
-
Monitor steaming operations and watch for signs of valve leakage.
-
Ensure that hoses used are rated for process temperature and that the location where condensate is routed has been evaluated for the potential of process leaking back into the system.
ALEX MALLER (TechnipFMC Process Technology)
Technip’s practice is to specify gate valves with flushing connections at the base of the seat. To ensure positive isolation, the flushing connection can be used to remove any sediments that may be impact the contact of the gate with the seat. Another option is to orient the valve stem off of vertical in order to move the final seating location away from the low point, therefore reducing the chances of sediment to accumulate there. This type of valve orientation is only possible given that space is available. Most importantly, these valves should be overhauled during every turnaround to ensure their long-term reliability.
BRYAN DINKEL [Marathon Petroleum Corporation (MPC)]
Positive isolation of slurry and heavy cycle oil (HCO) equipment is important in order to prepare equipment for maintenance activities or to isolate hydrocarbon source in the event of loss of containment. Risks include fire and personnel exposure to hot process materials. Across a typical slurry pumparound circuit, operating temperatures will range from as high as about 690°F at the tower bottoms down to about 550°F return temperature. Apart from hydrocarbon flammability, slurry has the added potential to operate near the auto-ignition temperature (AIT); the pumps are at highest risk due to the slurry being at its hottest temperature directly off the tower. The AIT of slurry is approximately 750°F and of HCO is approximately 500°F. Slurry contains a mixture of catalyst fines and coke, which both lead to a higher risk of an obstruction that could inhibit isolation and verification steps.
The ideal installation includes double-block-and-bleeds with sufficient straight runs of piping for access, blinding, and maintenance while also working to minimize the distance between the tower bottoms and pumps. Minimize the presence of dead legs within the circuit that provide a location for solids to settle out. Block valves should have the stems in the vertical position – or as close to vertical as possible – to minimize the risk of catalyst collecting in the valve bonnet. In reality, most units were not originally designed with a double-blocks valve configuration and will have single-block valves. The cost of a retrofit is not trivial, particularly when there are options available to clear the seat of a valve of deposits. Flushing oil connections to the valve allows for the direct addition of flushing oil to the valve seat. The cycling of the valve opened and closed to dislodge any deposits that settled in the seat of the valve is also an effective Operations trick. For verification of positive isolation, bleeders are used; or in scenarios when bleeders are not available, bleeder blinds can be installed.